バッチ系化学プラントの設備構成をレイアウトと関連付けて解説します。
この考え方を展開させていくと、プラント建設や工場運営という広い見方に展開です。
基本的に反応器単位で反応を考えるので、設備の構成も反応器単位(ユニット)で考えます。
この記事を読むと、ユニットを基準にプラントが構成されている例が理解できます。
特に機械系エンジニアで企画を目指す人は必須の知識でしょう。
プラント平面
バッチ系化学プラントのレイアウトとユニットを紹介します。
プラントを上から眺めると、一般には以下のような形状をしています。
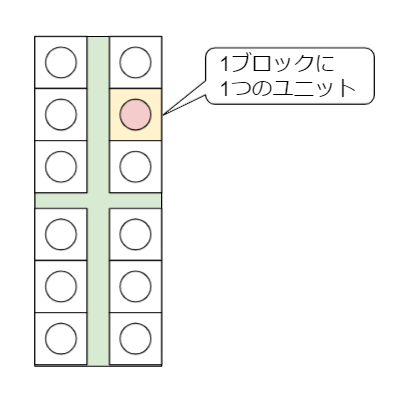
こういう形状のプラントの特徴を言語化してみましょう。
- 縦長の形状
- 中央に通路がある
- 通路を挟むように設備ユニットを配置
- 1つの設備ユニットの四方を柱で支えるブロック構造
平面的にこういう単純な形をしているものが、上階に伸びていってプラントが形作られます。
プラント建設段階でブロック内のユニットはほぼ決まっています。
ブロックの8~9割に設備を設置します。
ちょっとだけ予備のブロックがあるというという感じです。
予備のブロックを大きくすればするほど、プラントサイズが大きくなってプラントコストに響きます。
プロジェクト段階でよく考えましょう。
1つのブロックは縦横5~6mが限界です。
これ以上長くしようとすると大梁の大きさがとても巨大になります。
フルスペックユニット
1ブロック内のユニットの構成例を紹介します。
フルスペックのユニットから紹介します。
これ以上複雑になるケースはないというくらいのフルスペックです。
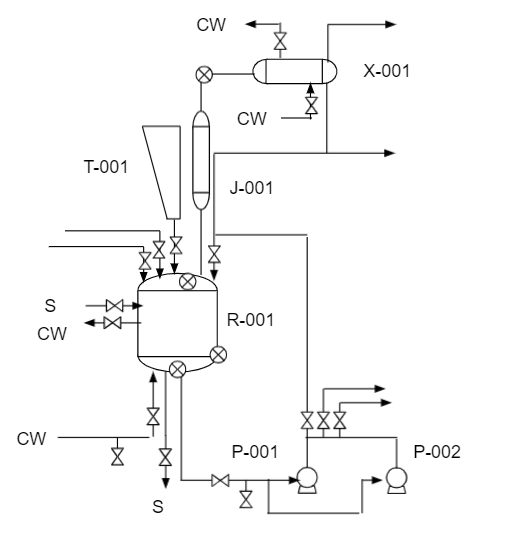
複雑ですよね・・・。
落ち着いて分解してみると、構成する設備が見えてきます。
これらの設備同士をつなぎ合わせるプロセス配管や熱交換をするためのユーティリティ配管が付属します。
ポンプが2個ありますが連続プラント的な冗長化目的とは限りません。
ライン材質(ステンレス系・耐酸系)で用途を分けたり、スラリーの有無などで用途を分けたり、分液をしやすくするためなどの思想があります。
1種のマルチ対応のポンプが存在しない以上、使い分けをせざるを得ません。
粉体貯留ホッパーは近年増加傾向にあります。
原料が液体ではなくて粉体であるケースが増えているからです。この辺は時代の流れ。
このフルスペックユニットを最初から設定して建設できていれば、後の追加工事は発生しないはず。
それができないのはイニシャルコストを重視するから。
ミニマムスペック
フルスペックは配管が複雑で非常に分かりにくいです。
上の例でも複雑なのに実際のP&IDにはもっと細かい情報がいっぱい載っています。
逆に今から紹介するミニマムスペックはあっさりしています。
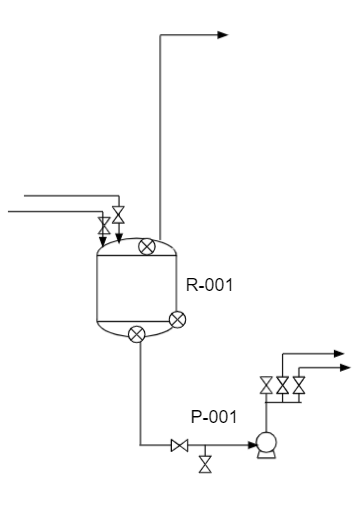
構成設備が単純ですよね。
- 反応器
- ポンプ
これだけです。
入社したてのエンジニアは、まずはこれくらいからスタートするのが分かりやすいでしょう。
実務ではいきなり実機の複雑なP&IDと格闘することになり、混乱しがちです。
最初は、単純な要素に分割して基本を理解するようにしたいですね。
装置数が単純なら構成する配管も単純です。
- 反応槽に入る液の配管
- 反応槽から出るガスの配管
- 反応槽から出る液の配管
基本はこれだけ。この数が多いかどうかの違いだけです。
フルスペックとミニマムスペックの中間
実際の設備はこのフルスペックとミニマムスペックの中間のケースが多いです。
すなわち、
- 蒸留がしたいけど充填塔がない
- 粉体を投入するホッパーやタンクのノズル口径がない
- スラリーを送りたいけどポンプが適さない
こんなパターンが多いです。
ミニマムスペックで設備を構成するといっても、反応器には余分ノズルを付けておきます。
それで後に機能を追加しようとするわけですが・・・
充填塔なりホッパーなり大口径が必要となり、ノズルが足りないということがままあります。
ポンプは反応器底にいくつか並べておきます。
ブロック的思考ではポンプは2~3台置けるでしょう。
ポンプの数を増やせば増やすほど、配管が複雑になります。
スラリー系を送ろうとして曲がりくねった配管で詰まったということも、結構起こしがちです。
ミニマムスペックで作ったユニットに対して、後で機能を追加させていってフルスペックに近づけていこうとするがゆえに、化学プラントでは改造工事が頻繁に発生します。
フルスペックに到達するまでの工事費用トータルを考えると、いきなりフルスペックにする方が安いのは言うまでもないでしょう。
投資判断の問題です。
プラント階数
プラントの階数は4つの階くらいに分けるのが良いでしょう。
4階 | 熱交換器 |
3階 | 塔 |
2階 | 反応器 |
1階 | ポンプ |
こんな発想で組みます。
塔や原料仕込みが全くないプラントなら3階とコンパクトにすることは可能です。
逆に拡張性を増やすためにあえて5階以上に上げているプラント思想もあり得ます。
こんな風にプロセスフローを見ながら各階にどんな設備を置くのか、という視点で階数を決めていきます。
材質
ユニットとそのスペックを考えるとき、材質は1つのキーワードとなります。
バッチで多いグラスライニングとステンレスの2択が考えられます。
ユニット的な思考でこの2つの材質の違いを見てみましょう。
ガラス | ステンレス | |
耐酸性 | 高い | 低い |
費用 | 安い | 高い |
温度 | 弱い | 強い |
衝撃 | 弱い | 強い |
静電気 | 弱い | 強い |
反応器は耐食性と安さを重視してグラスライニングにすることが多いでしょう。
例えステンレス系でも持つラインであっても、汎用性を考えてグラスライニングにするというケースです。
ラインはステンレスなので、中途半端な形になります。
ここも最初から設備も配管もグラスライニングにしておく方が無難という考え方もできます。
近年はグラスライニングは調達性に問題があるので、あえて言うとフッ素樹脂ライニングの方が良いかもしれませんね。
フッ素樹脂も調達性の問題はありますけど・・・。
参考
最後に
バッチ系化学プラントのユニットとプラント構成の考え方を紹介しました。
反応器・塔・熱交換器・ポンプのフルスペックユニットを1つのブロックに納めるように配置します。
ブロックの数を広げていくだけで増築ができるという思想です。
ミニマムスペックとフルスペックに対する投資判断と、設備・ラインの材質に対する投資が会社によって分かれるところでしょう。
化学プラントの設計・保全・運転などの悩みや疑問・質問などご自由にコメント欄に投稿してください。(コメント欄はこの記事の最下部です。)
*いただいたコメント全て拝見し、真剣に回答させていただきます。
コメント