化学プラントのオーナーエンジニアリングにおいて、「標準ユニット化」という考え方が近年注目されています。
これは、プラントの構成要素をあらかじめ標準化されたユニットで設計・組み立てるという思想であり、従来の設備設計・配管設計とは一線を画すものです。
とくに技術革新が進みにくい化学プラントの設計現場においては、配管設計の効率化、設計期間の短縮、予備品管理の容易さなど、多くのメリットをもたらします。
本記事では、現場のオーナーエンジニアの視点から、標準ユニット化の基本思想とその具体的なメリット、導入に際してのポイントを解説します。
化学プラントのオーナーエンジニアリングは配管が主役
私は、化学プラントのオーナーエンジニアリングは配管が主役だと考えています。
そもそも化学プラントのオーナーエンジニアって具体的になにをするものでしょうか?
自社現場の設備を設計すると広い表現だと分かりにくいですが、例えば以下のように分割してみましょう。
項目 | 担当 |
撹拌槽 | 設備メーカー |
ポンプ | 設備メーカー |
熱交換器 | 設備メーカー |
配管 | ユーザー |
化学プラントでは多くの設備をそれを繋ぎ合わせる配管があります。
設備は設備メーカーに作ってもらいます。
その設備を現場で接続するためには、配管設計という幅広い検討事項が課題となります。
こここそがオーナーエンジニアの価値。
極端に言うと設備の大きさは、おおよそ分かればOK。
それを現場にセットして、現場が操作できる配管構成をくみ上げることができるのか。
これは現場を知るエンジニアにしかできませんよね。
だからこそオーナーエンジニアの最大の勝負所。
配管が最も大事と判断するためにも、関連要素の重要度を判断しておきましょう。
設備の大幅な改善は期待できない
オーナーエンジニアリングを設備設計と配管設計の2つに分ける場合、設備設計が大事!と考える人は多いでしょう。
私はそうは思っていません。
ここが一部のオーナーエンジニアが否定される部分。
だって「エンジニア→設計→設備設計」って容易に関連付きますので。
「エンジニア→設計→配管設計」という思考に至るには、設備設計が大して大事ではないという点に気が付く必要があります。
設備設計が大して大事ではないのは、以下の理由から。
設備の大幅な改善は期待できない
残念ながら、設備の技術革新は望めないでしょう。
例えば、10m2の熱交換器が同じ交換熱量で1m2に縮小することなんてできるでしょうか?
その結果として、設備寸法を1/3程度まで削減することができるでしょうか?
これくらい劇的な変化がない限り、設備サイズはだいたい予想ができます。
配管設計としては「設備→配管」の準に組んでいくことが普通ですが、設備寸法が分からないから配管を全く組むことはできないと思考停止をするエンジニアが非常に多いです。
そんなことはありません。
設備のおおよその仕様(プロセス・ユーティリティの仕様)が決まっていれば、接続すべき配管のスペックは決まっていきます。
設備メーカーの図面が無いと、具体的にどこに接続するかという1ピース配管の接続が分からないだけです。
それならば設備仕様が決まっていなくても、P&IDさえあれば配管設計は進めることができます。
この発想が進めば設備設計が最も大事か?という疑問が出てくるでしょう。
「類似設備の取扱経験が多い」という前提が付きますが、現在の自社工場で完全に新規取扱の設備なんてほぼほぼ無くなっている以上、この前提はかなりの確率で成立するでしょう。
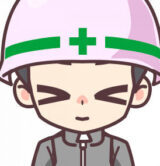
似た設備がすでに実績であるなら、詳細設計ってほとんど不要です
建屋の構成が不均一
設備に比べて建屋は変更が極めて難しいものです。
設備は老朽化すれば単純更新をしよう、その際に配管レイアウトも合理化しよう、という思想にいたります。
でも建屋は一度建てると壊したり増やしたりといった改造がほぼできません。
そのため、個々のプラントに特性が出て同じプラントが2つと存在しえない環境を生みます。
全く同じ時期に2系列のプラントを建てたとしても、系列1は新剤を導入して設備改造を行い、系列2は改造をしないまま。
この瞬間に設備構成は変わっていきます。
系列2では簡単に導入できた設備が、系列1では難しい。
個々に配管設計をしていかざるを得なくなってしまう。
プラントのライフサイクルという要素が設計に関連します。
プラントは生き物ですね!
標準ユニットとプラント建設思想
設備の技術的革新がこれ以上望めず建屋が不均一だという設計環境に対して、ユニット設備という発想があります。
ユニット設備
バッチ系化学プラントでは真空ポンプユニットが良い例。
封液循環タイプの水封式真空ポンプなら、エゼクター・コンデンサー・真空ポンプ・セパレーター・封液熱交などがユニットとして組まれます。
メーカーはこのユニット設備で組むのが非常に得意です。
本当に最小限のサイズでくみ上げます。
ユーザーが同じ設備で、個々の設備を組み合わせるともっと大きなスペースを取ってしまいます。
作業性を考慮してしまうから。
ユニット設備にするとサイズを小さくできるがゆえに、色々なプラントに対して汎用的に使える可能性があります。
広いスペースが必要な設備だと、特定の狭いプラントには導入できなかったりしますよね。
小さいは化学プラントでは正義。
ユニット設備は「自動化をすると居た目を見る」というのが定説です。
ポンプの起動・スチームの入切・封液の注入という点だけをユーザーが自社で自動化すれば簡単に運転できる真空ポンプは、まさにユニット化に適したもの。
自動化を進めれば進めるほどシーケンス作成が複雑になるので、メーカーに依頼するとブラックボックス化されて後で困ります。
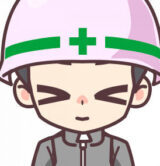
ユニット設備って良く分からないですね
プラント建設思想
ユニット設備という概念を応用すれば、そのプラントに対して標準設備構成を考えることができるでしょう。
バッチ系化学プラントで標準設備構成というとこんな感じでしょう。
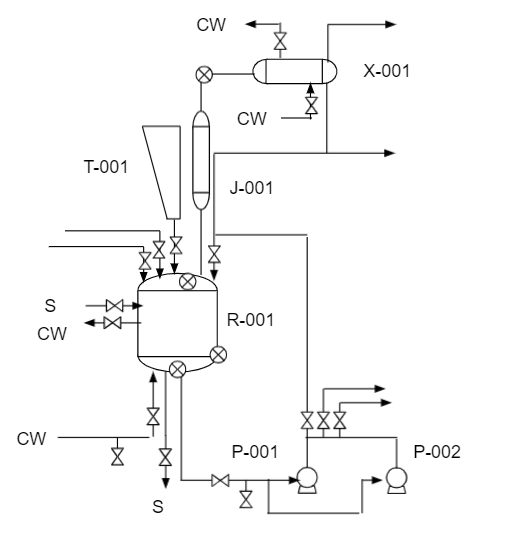
反応槽・ポンプ・塔・熱交換器を1セットにするという考えです。
これがプラントの1ブロック内に縦方向に組み上げていくという発想です。
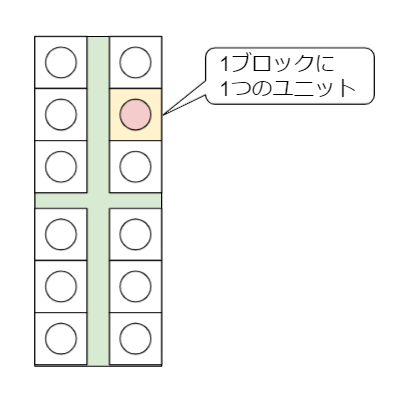
これこそ完全な縦割りですね(笑)
この考え方が綺麗に忠実に実施できれば、配管設計はほぼゼロにすることが可能でしょう。
それが現実的ではないのはプラント建設思想が工場内で統一化されていないから。
個々のプロジェクトに最低限対応していって建設思想を反映させていないと、どんどん道を外していきます。
建設思想に忠実なエンジニアはプロジェクト担当者から見ると、頭が固いと批判されそうですが・・・。
標準ユニットのメリット
ここまで解説したユニット化について、メリットを整理しましょう。
設計期間の短縮
ユニット化の最大のメリットは設計期間の短縮です。
ピースを単純に当てはめればいいだけ。
1つ1つを繋ぎ合わせるために神経を使う必要性が少なくなります。
ジグソーパズルのピース数を少なくすることと同じ発想ですからね。
工事期間の短縮
ユニット化が進むと工事期間を短縮できます。
同じものを10個作るのと10個の別々のものを作るのとでは、どちらが簡単かはいうまでもありませんよね。
こう書くと当たり前ですが、気が付かないくらい追い込まれるのがエンジニアです。
予備品を持てる
ユニット化が進めば、そのユニットを一式予備品として持つという発想が可能です。
どのプラントでも同じ装置・同じ配管ならそれを一式予備として持っておくだけで、
異常があったときにはすぐに交換という高度な判断ができます。
ユニット化が進んでいない場合、反応槽が壊れたらその時に他に使える反応槽を探したり、ポンプなら予備品を探したり・・・
と緊急対応で様々なリソースを調査していかざるを得ません。
頻度が少ないならまだ許せますが、振り回される業務が多い職場はそれだけでブラック職場となる可能性を秘めています。
電気・土建は標準ユニットの発想が進んでいる
このユニット化の発想は機械や計装だと斬新に感じるでしょう。
ところが電気や土建だと結構当たり前の発想です。
電気盤や建屋の構造なんてほぼぼ共通化されています。
ユニット化が進んでいるからこそ設計の価値が相対的に低いのが、電気や土建。
少子高齢化や人員削減の流れに従うように、機械や計装もこの方針に移行せざるを得ないでしょう。
参考
最後に
化学プラントのオーナーエンジニアリングにおいて、標準ユニット化は設計の効率化と現場運用の安定性を両立する有力な手段です。
特に配管設計の簡素化やメンテナンス性の向上、工事期間の短縮といった効果は、人的リソースが限られる今後のプラント設計において大きな武器となるでしょう。
電気や土建の分野で既に当たり前となったユニット設計を、機械・計装にも広げていくことが、これからの化学プラント設計の本流になるはずです。
化学プラントの設計・保全・運転などの悩みや疑問・質問などご自由にコメント欄に投稿してください。(コメント欄はこの記事の最下部です。)
*いただいたコメント全て拝見し、真剣に回答させていただきます。
コメント