バッチ系化学プラントの機械エンジニアが最も力を発揮できる部分であり、最も悩める機械がスラリーポンプ。
さまざまなトラブルを起こす機械で、どう選んだらいいか悩む人は多いです。
基本的な考え方は渦巻ポンプと同じ。
スラリーの特徴と渦巻ポンプの選択肢を複合的に考えて、最適な案を選ぶことが大事です。
これができれば一人前のエンジニアですね。
スラリーポンプを使う理由
まずはスラリーポンプを使う理由をまとめましょう。
水力輸送は移送しやすい
粉体を輸送することを考えた時、水力と空力の2つが思いつきます。
バッチ系化学プラントで水力を使うのは詰まりを防止したいから。
密度差が大きい方が粉体が沈降しやすいので溜まって詰まりやすい、という考えです。
空力輸送(気流輸送)だと空気と粉体という1000倍程度の密度差が発生しますが、水力輸送だと液体と粉体という数倍あるかないかのわずかな密度差しか発生しません。
特に、液体が水である場合、有機物である粉体は浮くことが多いため、閉塞しにくくなります。
液体に有機溶媒を使う場合でも、空気に比べればはるかに沈みにくいです。
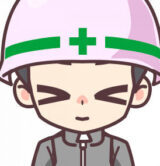
気体・液体・固体の基本的な性質はしっかり理解しておきましょう
静電気対策が取れる
水力輸送では静電気対策が取りやすいです。
水力輸送で静電気対策が取りやすいのは
- 流速を1m/s程度まで落とすことが可能
- 導電性の液体を使える場合がある
という2点が理由でしょう。
特に流速を落とせる点が魅力的です。
空気輸送では、移送速度は10m/s以上とせざるを得ません。
速度が遅いと沈降します。
流速が速いと静電気は溜まりやすいので、空気輸送は避けたいですね。粉じん爆発も起こしやすいし。
動力が低い
水力輸送は動力費が少ないのがポイント。
ポンプ1台あればOKですね。
空力輸送では、エアーコンプレッサーや圧縮窒素を使わないといけないので、動力費が高いです。
スラリーポンプの注意点
スラリーポンプを選ぶ場合、一般的に考えるべき注意点があります。
液体を分離しないといけない
粉体をスラリー化して送る以上、スラリーから粉体を分離する工程が必要となります。
一般には、ろ過・乾燥・充填の工程です。
スラリーポンプに直結した問題ではありませんが、前後工程の設計が必要という意味では影響度は非常に大きいです。
結晶破砕
水力輸送ではポンプでスラリーに力を加えます。
羽根車で粉に力を加えるため、粉が破砕される恐れは非常に高い。
これが良いか悪いかは製品の特性によります。
空力輸送では破砕は起きにくいため、結晶破砕は水力輸送のデメリットとしておさえておくべきでしょう。
ポンプが損傷する
水力輸送では粉が破砕されるのだから、ポンプも破砕される可能性があります。
粉体が歯磨き粉と同じ研磨剤の役目をして、ポンプが削れていきます。
ポンプが破砕されるため、定期的なメンテナンスが欠かせません。
単なる液体送液ポンプよりも重要度を上げるのが普通。
空力輸送ではコンプレッサーのメンテナンスだけなので、損傷可能性はあまり高くありません。
コンプレッサーは世間一般に使用される機会で使用条件もほぼ同一ですが、スラリー送液の場合はスラリーの特性により異なります。
そのためスラリーポンプの故障確率は、他の設備よりも読みにくいですね。
スラリーポンプの候補
スラリーポンプの候補となりえるポンプを紹介しましょう。
渦巻ポンプ
スラリーポンプと言えば渦巻ポンプが一般的です。
渦巻ポンプの多彩なバリエーションがメリットとして効いてきます。
竪型
竪型の渦巻ポンプはスラリーポンプの最有力候補。
渦巻ポンプのデメリットであるメカニカルシールの故障を緩和させてくれますから。
悩んだらまずは竪型を考えると良いでしょう。
横型
竪型が嫌だったり、ちょっと冒険したかったり、そんな場合には横型も選択肢になります。
- オープンインペラもしくはセミオープンインペラ
- ダブルメカニカルシール
- メカニカルシールやシャフトは摩耗に対する硬度を上げる
これらを守るだけで、使える横型の渦巻ポンプもスラリーポンプとして使える場合が多いです。
スラリー専用のインペラやケーシングを特殊開発したポンプも世の中には出回っています。こう言ったポンプは往々にしてメンテナンス性を犠牲にする傾向にあるので、工場の運転指針を考えながら選定することになるでしょう。自社ではメンテナンスできず、メーカー工場に返却するために予備機を保有するというパターンになりがちです。
メカニカルシールの選定
スラリーポンプに渦巻ポンプを使う場合は、メカニカルシールもちゃんと選定したいです。
- ダブルメカの方がミスが少ない
- シングルメカにするなら外部注水のインサイド型
この辺の思想がちゃんとしたいところ。
ダブルメカの方が無難に見えるのは、漏れが目に見えないから。
中間冷却液からプロセス液に漏れたり、プロセス液が中間冷却液に漏れる可能性もありますが、気が付きにくいです。
ダブルメカは本来は、本体側の圧力が高くて大気圧との圧力差がある場合のシール性向上のために使いますが、
目くらまし的な効果もあるのは確かでしょう。
シングルメカは漏れた時に目立ちます。
竪型のポンプならシングルメカでもある程度は使えるので、わざわざダブルメカを選ぶことはあまりないでしょう。
漏れが許容できない場合は、ダブルメカも駄目という展開になります。
ダブルメカニカルシールは中間液の選定に気を使います。水が無難と思いきや、水が許容されない系も存在します。有機溶媒などの共液を使う場合には共液の循環冷却システムを構築しておくべきでしょう。
シールレスポンプ
渦巻ポンプと肩を並べるシールレスポンプ。
シールレスポンプも横型と竪型の2つが候補となりえます。
竪型の需要は残念ながら徐々に減っています。
というのも特徴が渦巻ポンプの竪型と似ているから。
シールレスにこだわる必要が無く、渦巻で良いでしょ?という展開になります。
メカニカルシールがあって、液が漏れてくる可能性があるわけですからね・・・。
横型の場合でも数wt%程度のスラリーなら送れるので、場所を選んで横型のシールレスポンプを使うことは十分に考えられますよ。
シールレスポンプをスラリー用に使う場合、実は冷却液がプロセスに混入する仕組みを使っていることが多いです。シールレスと言いつつ実はシールレスではないという意味で、スラリー目的でシールレスポンプの意味はあまりないと、個人的には考えています。
ポンプの起動停止
スラリーポンプを考えるときに、ポンプの起動停止の問題が必ず発生します。
- 人が現場に行かないといけない
- 液を送り終わったら、洗浄しないといけない
この辺はバッチ系化学プラントの課題の1つです。
作業員が徐々に少なくなっている現在、自動化を進めていかないと生産が立ち行かなくなっていきます。
自動化を進める各社は配管設備と合わせて自前でユニットを組んでいますが、これが結構面倒。
できることならポンプメーカーがユニットを開発して欲しいと思っています。
でも、ポンプメーカーも体力が無かったり需要が低いという理由で、開発しないようです。
DXって何なんでしょう。
参考
最後に
化学プラントで使うスラリーポンプの考え方を解説しました。
スラリーポンプのような水力輸送は空気輸送に比べてメリットが高いですが、工程の追加などデメリットもあります。
竪型の渦巻ポンプでシングルメカを選ぶと失敗する確率は低いですが、横型の渦巻ポンプやシールレスポンプも候補となりえます。
化学プラントの設計・保全・運転などの悩みや疑問・質問などご自由にコメント欄に投稿してください。(コメント欄はこの記事の最下部です。)
*いただいたコメント全て拝見し、真剣に回答させていただきます。
コメント