化学プラントで使われるポンプや撹拌機などの回転機械には、「漏れ」を防ぐための重要な部品、メカニカルシールが取り付けられています。
でも「構造が複雑でよくわからない…」「種類が多くて選び方に迷う…」という声も多いはず。
いろいろな種類があって理解しにくいですが、現場では問題となりやすいです。
この知識があるだけでも、対応策を提案することが可能となり、現場からは信頼感を得られますよ。
本記事では、初心者の方にもわかりやすいように、メカニカルシールの基本構造や主要部品、選定に関わるポイントなどを図解とともに丁寧に解説していきます。
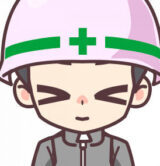
メカニカルシールは化学プラントの数少ない「メカ」的な機械です
メカニカルシール(mechanical seal)の構造
メカニカルシールはさまざまな型式が開発されています。
- 回転環
- 固定環
- 2次シール
- スプリング
- 金属ピン
多くの型式がありますが、ここに上げた基本5点は共通しています。
型式について第1世代・第2世代・・・なんて言い方をして表現をしますし、メカニカルシールという名前を相まって、機械的なイメージが強い部品です。
摺動面の材質
メカニカルシールの摺動面の材質は、SiCとカーボンの2種類がメジャーです。
摺動面とは回転環と固定環の向きあう面を指します。
ここでプロセス物体である液体や気体を外部に漏らさないようにシールします。
摺動面の材質には、色々な要求事項があります。
機械的性質、自己潤滑性、耐摩耗性、熱伝導性、耐熱性、線膨張係数、耐食性・・・
これらすべての性質を満足する材質は世の中にはなく、メリットデメリットがある候補材質も色々あります。
カーボン、超硬合金、アルミナ、SiC・・・
この中でもSiCとカーボンだけを知っていれば、バッチ系化学プラントでは十分です。
SiC
SiCはシリコンカーバイドというセラミックスです。
熱伝導度が高く硬度が高く耐食性が高いです。
熱伝導度が高いと摺動面で発生する発熱を外部に逃がすことが可能です。
硬度が高いと摺動部で発生する摩擦に強いです。
耐食性が高いことは、化学プラントでは非常に重要です。
総合的な能力に優れるので、摺動面の材質の基本として使います。
カーボン
カーボンは炭素を焼結して作成したものです。
熱を伝えやすく多孔質で非常に柔らかく腐食もしにくいです。
SiCと比べると柔らかいというのが特徴
摺動面の組み合わせ
摺動面の組み合わせを見ていきましょう。
- SiC/カーボン
- SiC/SiC
この2パターンが一般的です。
この使い分けは「硬さ」。
SiC/カーボンは硬さの差がある程度はっきり出ていて、カーボンを削りながら使うというイメージです。
SiC/SiCなら同じSiCだから硬さも同じと思いきや、SiCでも硬さの差をつけています。
硬さの差が少ないため削れにくいのが特徴。
SiC/SiCはスラリーなどに向いています。
摺動面にスラリーが噛みこんでしまうと、運転を続けるうちに摺動面が削れていきます。
スラリーポンプ向けのメカニカルシールではSiC/SiCとしておくと良いでしょう。
この削れを緩和するためにはできるだけ硬いものにしたいという発想で、SiC/SiCを使います。
SiC/カーボンが一般的
インサイド型・アウトサイド型
固定環と回転環の一の組み合わせでインサイド型・アウトサイド型という2種類があります。
インサイド型
インサイド型は以下のようなイメージです。
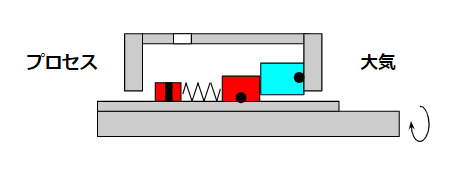
イン・サイドというのは回転環がイン側、つまりプロセス液内に入っている構造です。
インサイド型の方が一般的に使用します。
理由はシンプルで、摺動面から漏れても被害が拡大しにくいという点にあります。
これは遠心力で液体が回転軸から離れる方向に移動するから。
アウトサイド型を見た方が速いでしょう。
インサイド型が一般的
アウトサイド型
アウトサイド型は以下のようなイメージです。
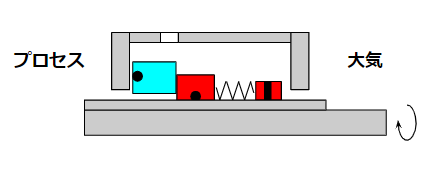
アウト・サイドというのは回転環がアウト側、つまりプロセス液外に入っている構造です。
アウトサイド型で摺動面から漏れがあった場合、漏れの方向と遠心力の方向が一致します。
遠心力を受けた液体が積極的に漏れる方向に動きます。
これは安全とは真逆の方向。
なるべく使いたくありません。
アウトサイドを選ぶ理由はスプリングの材質の問題。
高耐食性が求められる渦巻ポンプに対するメカニカルシールでは、材質の耐食性が課題になります。
ここでスプリングは最も注意が必要。
回転機器で大きな力を受けるスプリングは常温・静機器としての耐食性以外にも、力を受けたり温度が上がった状態での耐食性を考えないといけません。
不安になります。
それならスプリングがプロセスに接触しないように、アウトサイド型にした方が無難だろうという発想です。
回転型・静止型
回転型・静止型はスプリングがどこに付いているかの違いです。
下図を見てください。左が回転型、右が静止型です。

回転型はスプリングが回転環側に、静止型はスプリングが固定環側に付いています。
回転型の方がシンプルな発想です。
メカニカルシールでは回転運動で発生した振動の影響を受けずにシール面を維持するために、スプリングなどを使います。
スプリングは振動の発生するまさにその場所に置きたいもの。
ところが静止型の方がメリットが大きいです。
- 高速回転に強い
- スラリーに強い
回転型のように回転軸にスプリングが付いている構造だと、高速回転時にスプリング自身が変形します。
これは振動の吸収を妨げる方向です。
静止型だとスプリングは遠心力の影響を受けないので、その分だけ安定します。
静止型だとスプリングをプロセス外に出すことも可能です。
スプリングがプロセス液に接触しないとスラリー液などの嚙みこみの可能性がなく、スプリングの故障が起きにくくなります。
静止型が一般的
バランス型・アンバランス型
メカニカルシールにはバランス型・アンバランス型があります。
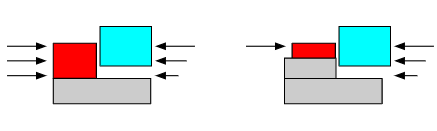
左側がアンバランス型・右側がバランス型です。
バランス型・アンバランス型は回転環が受ける圧力のバランスのことを言います。
アンバランス型だとプロセス液の圧力を吸収しにくい(バランスが悪い)状態となります。
これはシール面が振動して安定性を失う方向なので漏れの可能性が高くなります。
回転環が受ける圧力はプロセス液とシール面の2つ。
シングルメカの場合はプロセス液と大気圧が回転環に作用します。
当然ながらプロセス液の方が高圧なので、高圧部の受圧面積が高い方がバランスは悪くなります。
バランス型ではシール側(大気圧側)の受圧面積を大きくしてバランスを無理やり取ろうとしたものです。
アンバランス型の方が基本で、バッチ系化学プラントではアンバランス型で十分です。
特別な事情としてバランス型を選ぶ場合に考えないといけないことがあります。
- 高圧運転をする
- シャフトの段差を付ける
バランス型を選ぶのはプロセス液側の圧力が高い場合に限定されます。
バッチ系化学プラントではアンバランス型で対応できる程度の低圧での運転をします。
バランス型を選ぶ場合はシャフトに段差を付けないといけません。
これはシャフトの折損の可能性をあげたり、メカニカルシールボックスを大きくしたりと、ポンプにとって好ましくない要素を生みます。
そうまでしてでも高圧運転が避けられないからバランス型にするという思想ですね。
アンバランスが一般的
シングルスプリング・マルチスプリング
メカニカルシールのスプリングは、シングルスプリングとマルチスプリングの2種類があります。
- シングルスプリング 1個のスプリング
- マルチスプリング 複数個のスプリング
これだけの違いですが、いろいろな差があります。
シングルスプリングはスラリーに強く、マルチスプリングは高速回転に向きます。
シングルスプリングは1個のスプリングしかないので、サイズが大きいです。
スプリングの中の隙間が大きくスラリーが入っても溜まりにくいです。
マルチスプリングはスプリングの数が多く、サイズが小さいため詰まりやすい特徴があります。
スラリーに対してはマルチスプリングは避けた方が無難です。
一方、マルチスプリングはスプリングの数が多いので高速回転の振動を吸収しやすい特徴があります。
例えば3個のスプリングで摺動面を押すと、非常にバランスがとりやすくなります。3点指示ですね。
2次シール
2次シールとは1次シールではない部分のシールです。
1次シールとはメカニカルシールの摺動面そのものですね。
2次シールとは以下のような場所のシールのことを言います。
- 固定環とメカニカルシールボックス
- 回転勘とシャフト
一般的なシール材であるOリング・Vリング・ベローズなどを使います。
Oリング
Oリングがついたメカニカルシールは下図のようなものです。
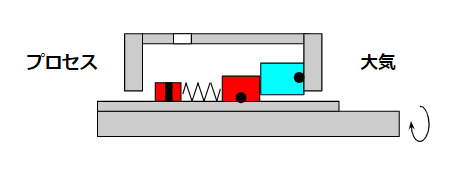
回転環とスリーブ間のシールにOリングを使っています。
化学プラントでOリングのシールはあまり使いません。
高耐食性のOリングが高いからです。
一般的なFKMで対応できない薬液だと、高価なFEPやFFKMが必要となります。
Vリング
Oリングの代わりにVリングを使うことがあります。
Vリングは動的シール専門です。パッキンの1種。
PTFEのVリングというとあまりいい印象はありませんが、正常に機能します。
Vリングなので複数枚を重ねて寿命を持たせる思想です。
ベローズ
OリングやVリングの代わりにベローズを使う場合があります。
ベローズは部品点数を削減できるメリットがあります。
スプリングと2次シールの両方を兼ねることができます。
でも注意点はあります。
- 腐食性の高い液には使えない
- スラリー液には不向き
スプリングの問題でアウトサイド型を選ぶときと同じ問題です。
スプリングの代わりにベローズを使うから当然と言えば当然。
ヒステリシス
2次シールではヒステリシスが話題になります。
ヒステリシスとはここでは往復運動の往と復で条件が違うということを意味します。
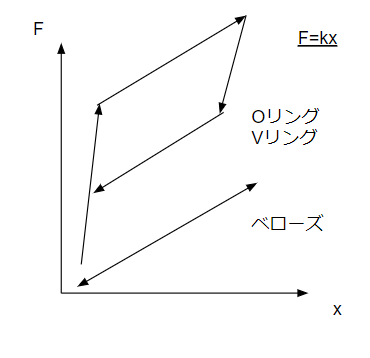
これはスプリングのたわみ量Xとスプリングの力Fの関係を示しています。
高校物理のフックの法則F=kxに従えば直線関係になるはずですが、上の図では直線関係になっていません。
これは2次シールがスプリングの動きを阻害しているから。
OリングやVパッキンはその形状が問題で、伸びるときと縮むときで抵抗力が変わります。
一方でベローズは伸びるときも縮むときも差があまりありません。
腐食性の無い清浄な液でOリング・Vリング・ベローズの寿命を比較したら、ベローズが最も寿命が長くなりそうですよね。
ヒステリシスが小さく、スプリングに掛かる力の変動が最も小さく安定するからです。
回転環の固定方法
回転環の固定方法もいくつかのパターンがあります。
ピン
機械の知識があれば真っ先に思いつく方法です。
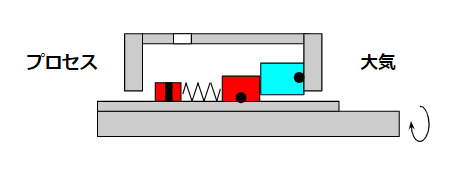
メカニカルシールを軸・ケーシングそれぞれにピンを打って接続します。
これで回転環は回転軸と連動して動き、固定環は回転環に引きずられることなくケーシングに固定されます。
極めて原始的な方法。
シンプルで確実。
普通はこのピン固定を使います。
スプリング・ベローズ
スプリングやベローズ自身に回り止めの機能を持たせようという物です。
回転環にピンを付けずに、スプリングやベローズで固定しています。
スプリングやベローズで固定するためピンが不要で部品点数が少なくなるメリットがあります。
でもスプリングやベローズにはそれなりの強度が必要となります。
ゴム
ピンのような金属部品を使わずに、ゴムで何とかしようという発想です。
化学プラントではあまり使いません。
ゴム自身の劣化・耐食性・摩擦強度などいろいろな問題があるからです。
固定環の取付方法
固定環の取付方法もいくつかの種類があります。
クランプ型
クランプ型は下図のようなタイプです。
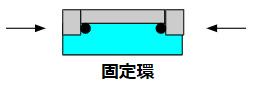
この方法は固定環を確実に固定する方法です。
だからこそ、ケーシングや軸が傾いていると、固定環もそのまま傾いてしまいます。
ポンプ製作時の精度出し・据付時の芯出しが重要と言えます。
プレスフィット
プレスフィットタイプは下図のようなタイプです。
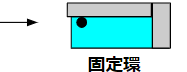
固定環が受ける圧力をケーシングが完全に受けてくれます。
Oリングやガスケットタイプで紹介したように、固定環が受ける圧力の一部分だけをケーシングが受けるわけでは無く、全面で受けてくれます。
そのため、プレスフィットタイプは高圧用に使います。
フロート
フロートタイプは下図のようなタイプです。
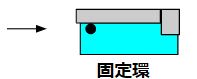
プレスフィット型に比べてバランスが悪く、クランプ型のように挟み込んでいません。
浮いているように見えるからこそフロートと呼ばれるのでしょう。
フロートであるからこそ回転運動による振動に追従しやすい性質があります。
シャフト保護
メカニカルシールでは実務的にはシャフトの保護を考えないといけません。
スリーブ
メカニカルシールは回転環をシャフトと固定します。
ここで回転勘とシャフトは摩擦を起こし、シャフトは削れていきます。
メカニカルシールに寿命が来て交換するときにシャフトも寿命が来た、となればダメージが結構大きいです。
インペラなど様々な部品を外してまた付けるというような大幅な修理が必要となります。
これを防ぐためにシャフトにスリーブを付けます。
シャフトとスリーブが分割できるようになっていて、スリーブとメカニカルシールが接触します。
運転時にはスリーブだけが消耗します。
メカニカルシールを交換するときはスリーブだけを交換すれば良いという発想です。
回転機械では一般に使う方法ですね。
バランス型でシャフトに段差を付けた場合は、スリーブもちょっと考えないといけませんね。
ベローズ
スリーブと同じような発想でベローズを使う発想があります。
金属ベローズやゴムベローズでシャフトを保護するという発想ですね。
使いどころが限定されています。
ダブルメカニカルシール(mechanical seal)
メカニカルシールは1つだけを使うシングルメカニカルシールと2個並べて使うダブルメカニカルシールがあります。
ダブルメカニカルシールには以下の特徴があります。
- 高圧のプロセス液に使う
- プロセス液の直性漏えいを防ぐ
ダブルメカニカルシールには2個のメカニカルシールの間に緩衝液を入れることができます。
フラッシングプランとも大きく関係します。
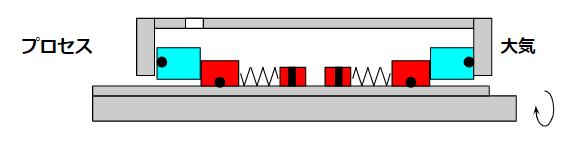
背面型
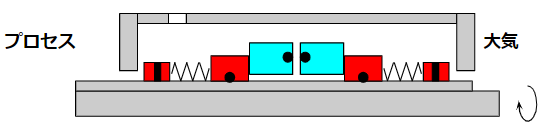
正面
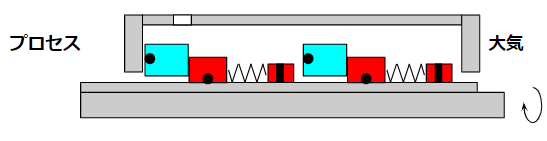
タンデム
背面型は2個のシール面が反対を向いていて、タンデム型は同じ向きを向いています。
背面型はアウトサイド型・インサイド型の組み合わせ、タンデム型はインサイド型・インサイド型の組み合わせです。
組み合わせ | プロセス側 | 大気側 | 緩衝液 |
背面 | アウトサイド | インサイド | 高圧 |
タンデム | インサイド | インサイド | 低圧 |
背面型やタンデム型は緩衝液の圧力と関係があります。
インサイド・アウトサイドでも話題になった、漏れに対しての対応で決まります。
背面型では緩衝液はプロセス液よりも高圧にする方が好ましいです。
これは背面型のシールがアウトサイド型になっているから。
プロセス液を外部に漏らしたくないというニーズが強い時に使います。
アウトサイド型でシールが壊れた時はプロセス液が遠心力で緩衝液側に漏れようとしますが、緩衝液で抑え込むという考え方です。
プロセス液側への緩衝液の混入もケアしないといけない場合は、背面型を選ぶかどうかは微妙なところ。
この場合は正面型(背面型の逆)やタンデム型などを選ぶか、そもそもダブルメカニカルシール自体を無くす発想にしないといけません。
タンデム型は高圧で使用するメカニカルシールの作動を安定化させる役割があります。
まさに緩衝液として機能します。
バランス・アンバランス型の議論であった摺動面への圧力バランスを適正に保つために、高圧のプロセス液に対して一定の圧の緩衝液で押し付け合うという考えです。
正面型は大気側はアンバランス型になるので、緩衝液が外に漏れる方向であまり使いません。
PV値
メカニカルシールにはPV値という思想があります。
圧力P×回転速度Vで決まる数値で、この値をもとにメカニカルシールの型式を選ぶという考えですP
PV値と適用できるメカニカルシールの範囲を下図に示します。
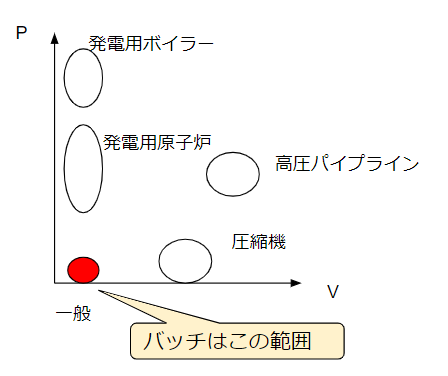
いろいろな種類があります。
バッチ系化学プラントの中でも大型の回転機械として37kW渦巻ポンプや22kW撹拌翼がありますが、この表では左下の隅っこ・・・
これならメカニカルシールの種類にこだわりを持たなくても良いですよね。
関連記事
メカニカルシールや渦巻ポンプに関してさらに知りたい方は、以下の記事をご覧ください。
最後に
メカニカルシールは化学プラントにおける回転機器の信頼性と安全性を左右する重要部品です。
本記事を通して、構造や材料、タイプの違いなどを理解することで、トラブルの予防や適切な選定に役立てていただければと思います。
化学プラントの設計・保全・運転などの悩みや疑問・質問などご自由にコメント欄に投稿してください。(コメント欄はこの記事の最下部です。)
*いただいたコメント全て拝見し、真剣に回答させていただきます。
コメント
ダブルメカシールで大気側の漏れが発生してます。気密時では漏れが有りません。プロセス液の粘度が温度により変化するのですが、メカシールの漏れには影響が有りますか。ちなみにフラッシング液はプロセスをクーラーで冷却して循環してます
お世話になっております。
粘度が高い方がシール性が高いので、摺動熱で温かくなったプロセス液が影響を与える可能性はゼロではありません。
温度と粘度の依存性によります。
しかし、普通の有機溶媒程度だと問題になるとは考えにくいです。
プロセス液も緩衝液(フラッシング液)も同じ溶媒ということなので、プロセス中の溶質側(有機物や固形分)の影響よりも、
漏れに影響を与える可能性として先に考えるのは圧力です。これは大丈夫でしょうか?
プロセス圧、緩衝室、大気それぞれの圧力差があれば、漏れる要因になります。
気密試験で問題なくても、運転時の圧力変動(例えばプロセス側がバッチ操作で締切運転になるとか、
緩衝液側の溶媒が他の溶媒とラインやポンプを共有しているかなど)の影響も問題ありませんか?