化学プラントでは、さまざまな工程で空気やガスを移動させるために送風装置が欠かせません。代表的な送風装置には「ファン」と「ブロワー」がありますが、それぞれの特徴や使い分けを理解することは、効率的で安全な運転にとても重要です。
この記事では、化学プラントでよく使われるファンとブロワーの種類や特徴を初心者向けに解説し、選定時のポイントも紹介します。
送風機はファンとブロアーと表現の違いがありますが、バッチ系化学プラントではファン・ブロアーが多いです。これらの装置は化学プラントではとても重要です。
送風機/ファン/ブロアー(fan/blower)用途
ファンやブロアーや排ガス吸引に使います。
局所除害や集中除害として運転時は絶え間なく動かし続ける、工場の心臓部の設備です。
送風機/ファン/ブロアー(fan/blower)の設計仕様
ファン・ブロアーの設計仕様をまとめました。
型式
ファンとブロアーの違いは、静圧の違いです。
静圧が10kPa未満をファン・10kPa以上をブロアーと呼ぶことが多いです。
弱い送風機をファン・強い送風機をブロアーというイメージでもいいでしょう。
静圧が高いことが重要ですので、遠心型を使うことが多いです。
遠心型は小容量・大静圧、軸流型は大容量・小静圧ですね。
羽根形状
ファン・ブロアーの羽根形状は教科書的には以下の3種類があります。
多翼・ラジアル・後ろ向き
形状のイメージは以下のとおり。
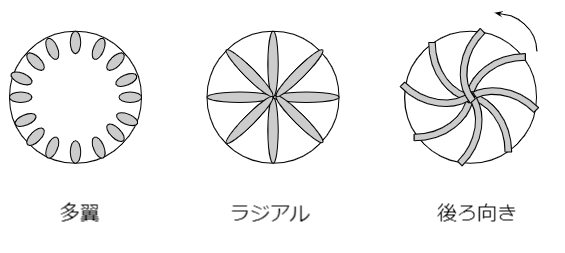
ファンが多翼で、ブロアーがラジアルや後ろ向きというパターンが多いですよね。
教科書的には形状の種類と特徴が箇条書きしてあるだけで終わりというパターンが多く、暗記に頼る人もいるでしょう。
これってエンジニア的には辛い発想です。覚えることばかりでしんどいです。
そうではない原理的な部分をちょっと深掘りして、暗記に頼らない理解をしたいと思います。
多翼
多翼形状の特徴は以下のとおりです。
- 風圧が低い。0.1~2kPa
- 小型軽量
- 効率が低い
多翼形状の特徴は、「小さな羽根を数多く重ね合わせた」という点にあります。
1枚1枚の羽根が小さいので強度が弱く、高い風圧を出すことはできません。
物理的には、羽根車は羽根径が大きいほど、角運動量の伝達量が大きく、高い風圧を生みますからね。
1枚1枚の羽根を小さくすると、羽根車全体を小さくすることが可能です。
小型軽量であることを重視したタイプが多翼型という位置づけになります。
多翼・ラジアル・後ろ向きの3種の中でも一番弱いのが多翼です。
ファンとブロアーが風圧(静圧)のクラスで決まることから、風圧が低いファンが多翼型とリンクしやすいですよね。
「羽根の大きさが小さい」という点から角運動量というワードで風圧に繋げられると、理解しやすいと思います。
ラジアル
ラジアル形状の特徴は以下のとおりです。
- 風圧はやや高い。0.5~5kPa
- 強度が高い
- 構造がシンプル
ラジアル形状は多翼形状の真逆ですね。
1枚の羽根を大きくすることで、高い風圧を生み出します。
ブロアーにラジアル型が多いのもこの辺が理由の1つ。
化学プラントでは後ろ向きよりもラジアルの方がメンテ的には好まれます。
というのは形状がシンプルで清掃しやすいから。
除害装置のガス吸引に使用するブロアーは、塩やダストや中間層などの異物が羽根車に付着します。
これがブロアーの性能劣化に繋がります。
清掃しようとすると、温水の掛け洗いをするのが一般的。
それでも取れなければ、人力で書き落とします。
ラジアル型は形状がシンプルだから工具が届きやすくて清掃しやすいですね。
とはいえ、効率を最大化していないため、ランニングコストが上がります。
これは工場としては好ましくありません。
メンテをする人はラジアル型の方が好みですが、コストの問題でラジアル型は採用されない悲しい運命にありがちです。
後ろ向き
後ろ向き形状の特徴は以下のとおりです。
- 風圧が高い。2~8kPa
- 効率が高い
後ろ向きはラジアル型の効率を最大化する方向で発展させたものと考えればいいでしょう。
羽根車の回転方向と空気が遠心方向に押されることを考えて、空気抵抗を減らすために羽根をカーブさせています。
カーブの度合いは回転数や風圧などの性能に直結します。
本当の最適解は流体力学のシミュレーションをして決めることになりますが、そこまでしなくてもある程度の効率化は図れます。
渦巻ポンプの羽根車もこの発想で作っていますよね。
最近の渦巻ポンプはそれこそシミュレーションで形状を決めていますが^^
軸封
ファン・ブロアーの軸封は主に2種類あります。
グランド
ファン・ブロアーの軸封はグランドシールが基本でしょう。
グランドシールはファン・ブロアーとしては最高級クラスのシール性を持っています。
危険なガスを扱う化学プラントではグランドシールの方が好ましいです。
ラビリンス
グランドシール以外の方法としてラビリンスシールがあります。
これはメカニカルシールより隙間が大きいシールと考えて良いでしょう。
ケーシングとシャフトの間に微笑の隙間を設けて、空気が漏れこむようにしています。
隙間が小さくて圧力損失が大きいので、少量の空気しか漏れこみません。
グランドシールのようにグランドパッキンを交換する手間がない分、メンテナンスが楽です。
使い分け
グランドシールは局所除害系、ラビリンスシールは集中除害系に使います。
局所除害系は特に厳しいガスを処理する場所なので、なるべく密閉化させるためにグランドシールが良いでしょう。
集中除害塔ではあらゆるガスを吸わせるために、空気が吸い込むこともあります。密閉化がそこまで求められません。
軸受
軸受はプランマーブロックとピローブロックという軸受箱を使います。
プランマーブロック
プランマーブロックの最大の特徴はメンテナンス性が良いことです。
プランマーブロックは2つ割の構造をしています。
2つ割だと、ベアリングの交換が非常にしやすいです。
2つ割でない場合、ベアリングを交換するためには、モーターや羽根車を取り外さないといけません。
これには設備洗浄や設備停止に大きな時間が掛かります。
ベアリングを交換するというとき、特に運転時に交換する場合は、速やかに交換したいもの。
メンテナンス時間をできるだけ短縮させたいと思うのは、運転面でも保全面でも共通の想い。
2つ割はメカニカルシールでも同じ発想で、好まれます。
ピローブロック
ピローブロックはプランマーブロックとは違って、2つ割ではありません。
2つ割ではないために、ブロックのサイズは小さくできます。
使い分け
特に指定がない限り汎用的なピローブロックを使いましょう。
点検口
ケーシングには点検口を付けると良いでしょう。
ファンを動かしている間に、塩などの固形分がインペラに付着します。
温水や苛性水で洗えば洗浄できますが、そのための口を設けると良いでしょう。
ドレン口
オートドレンが可能なような仕組みを作ると良いでしょう。
ガスを吸わせている時にミストが同伴されることが多いです。
特に誘引方式ならほぼ確実にミストが同伴されます。
仮に塔にデミスタを付けていたとしても、です。
ドレン口にバルブを設けておき逆Uシールを組むことで、オートドレンが可能です。
通風方式
ファン・ブロアーの通風方式は一般に3パターンあります。
誘引・押込み・平衡
この辺りは、教科書に載っているレベルです。
今回は、実際に化学プラントに対してどの方式を採用しているかを解説します。
いったん工場ができてしまうと、新たに増やすことがあまりないのがファン・ブロアー。
設計思想を知らないまま10年くらい過ぎ去ってしまいがちです。
誘引方式
まずは誘引方式から説明します。
化学プラントではファン・ブロアーは除害装置への排ガスの供給用によく使用します。
化学反応で発生した排ガスは適切に処理しないと、環境破壊や人体に影響を与えますからね。
除害装置としてスプレー塔を使うのが一般的。
他の装置もありますが、液体のスプレーで大半は処理可能です。
ということで、どこの化学プラントにもスプレー塔とファン・ブロアーは集中除害装置のセットとして1基は設置されているでしょう。
化学プラントでは特に「誘引」方式が普通です。
誘引方式は以下のようなイメージです。
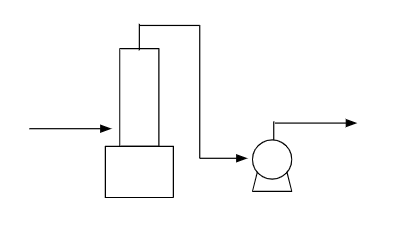
誘引方式はスプレー塔の出口にファン・ブロアーを設置した方式です。
スプレー塔基準で見れば分かりやすいですね。
スプレー塔にガスを吸わせる構成です。
誘引方式を化学プラントで使う理由は以下のとおりです。
- スプレー塔の中を負圧にして、仮に漏れても大気に拡散させたくない
- 腐食性のあるガスでファン・ブロアーにダメージを与えたくない
環境への配慮がやはり大事ですよね。
ファンで吸わせるということは、一般にはスプレー塔は大気圧より低い状態になります。
この前提として、「反応装置の排ガス発生部分が常圧」という条件が付きますが。
バッチ系化学プラントだとこれは基本的に満足する条件です。
どうでもいいことかもしれませんが、機電系エンジニアは設備目線で考える癖が強いので、上の1と2の順番を逆に考える傾向が強いです。
設備そのものに目を向けるのも大事ですけど、それだけだと視点が狭くなりがちです。
環境という別の目線でも見れるようになりたいですね^^
押込み方式
押込み方式は誘引方式の逆です。
下のようなイメージです。
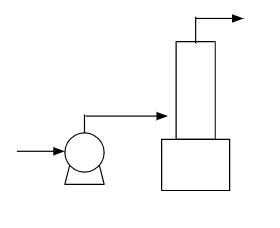
誘引方式とはスプレー塔とファン・ブロアーの位置関係が逆ですね。
スプレー塔に向かって排ガスを押込む形になります。
化学プラントであまり見ることは無いと、個人的には思っていましたが使うケースはいくつかあります。
- スプレー塔への空気の漏れこみが少なく、省エネ
- ミストがないドライガスを対象にして、ファン・ブロアーを傷めない
一般的にはこのように言われていますが、個人的には疑問です。
まず、1の空気の漏れこみですが、ファン・ブロアーの静圧(10kPa以下)で気にするレベルではありません。
バッチ系化学プラントでは、吸込みガス量が安定せずに、空気を余分に吸わせながら運転するのが普通です。
反応装置で吸引するガス量が生産品目でも変動がありつつ、時間に対しても変動があるからですね。
初めから空気の漏れこみを許容しているので、スプレー塔で多少空気が入ってきても気にしないから、押込みのメリットが少なく感じます。
2のミストが無いドライガスですが、これもほぼ非現実的。
個々の反応装置にミストセパレータを付けないと成立しない話です。
フレームアレスタだけでは難しいですよね。
平衡方式
平衡方式とは誘引方式と押込み方式を足し合わせたものです。
下のようなイメージです。
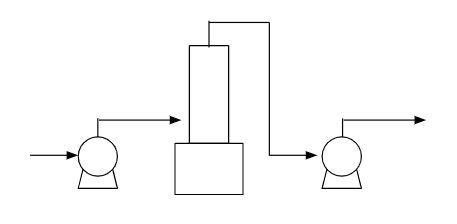
このイメージだと、押込みファンと誘引ファンのバランスが取れていないといけませんよね。
押込みファンが強すぎても誘引ファンが強すぎても、スプレー塔内で圧力損失を持ちすぎます。
これはスプレー塔での気液接触効果を減少する方向に動きます。
バッチ系化学プラントでは、このイメージのような使い方はほとんどしません。
除害装置が複数系列ある場合に、結果的に平衡方式になっているというパターンくらいです。
除害装置をスプレー塔とファン・ブロアーのセットで1系列として考える場合、
工場に1系列の除害装置だけという場合だけでなく、2系列・3系列を使うことがあります。
これは除害装置で処理したいガスの性状が違うから。
酸性ガスとアルカリ性ガスではスプレー液が違います。
それぞれに専用の除害装置を使って、直列に接続すると自然と平衡方式になります。
その場合でも、1基のスプレー塔に対して専用の誘引ファンと押込みファンが1基ずつ綺麗に配置するケースはほとんどありません。
- 一部のガスは系列1→系列2と処理を進め
- 残りのガスは系列1は通らず、いきなり系列2に進む
こんなケースが多いからです。
平衡方式で問題となる「誘引ファンと押込みファンのバランスの問題」は、バッチ系化学プラントでは気にしなくて大丈夫、ということですね。
参考
最後に
化学プラントの送風装置であるファンとブロワーは、目的や使用条件に応じて使い分けることが重要です。正しい理解と選定により、設備の効率化や安全運転に繋がります。
初心者でも本記事を参考に、送風装置の基本をしっかり押さえてください。
化学プラントの設計・保全・運転などの悩みや疑問・質問などご自由にコメント欄に投稿してください。(コメント欄はこの記事の最下部です。)
*いただいたコメント全て拝見し、真剣に回答させていただきます。
コメント