化学プラントにおける機械設備では、ベアリング(軸受)は見えにくいながらも極めて重要な存在です。ベアリングの不調は設備停止や事故の原因となり、保全においても重要な管理対象の一つです。しかし、軸受の種類や選定理由、構造などについて、現場のエンジニア全員が深く理解しているとは限りません。
この記事では、化学プラントの保全担当や機電系エンジニアが最低限おさえておきたい軸受の基本知識を、転がり軸受とすべり軸受の違いを軸に、分かりやすく整理していきます。
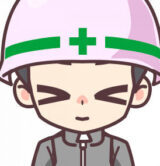
転がり軸受だけは最初におさえておきましょう
機械設備の2大軸受の特徴
軸受はすべり軸受と転がり軸受があります。もうちょっと詳しく言うと、軸受は以下の体系が分かりやすいでしょう。
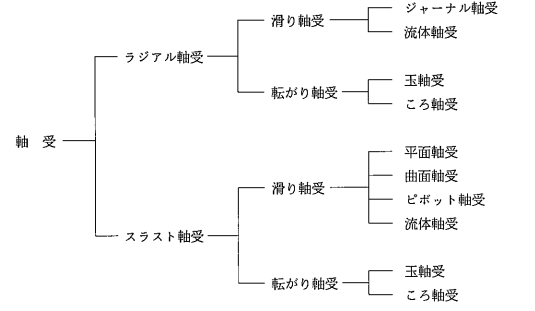
化学プラントの機械エンジニアは軸受を細かく知っておく必要はありません。何となく知っているだけで十分です。軸受のメーカーでは細かい情報が載っていますが、そこまでは必要ありません。
例えば、参考となる外部サイトは色々あります。
今回は、化学プラントの機械エンジニアが知っておくべき範囲に絞って、軸受の解説をします。
すべり軸受と転がり軸受の比較
軸受というと、すべり軸受と転がり軸受の2つの区分が大事です。比較を下に示します。
項目 | すべり軸受 | 転がり軸受 |
大きさ | 大きい | 小さい |
構造 | かんたん | 複雑 |
互換性 | ある | ない |
荷重 | ラジアルのみ | ラジアル・スラスト両方可 |
摩擦 | 大きい | 小さい |
耐衝撃 | 大きい | 小さい |
高速回転 | 有利 | 不利 |
低速回転 | 不利 | 有利 |
潤滑剤 | 液体 | グリース |
かなり簡潔にまとめました。化学プラントの機械エンジニアが抑えておきたい項目に絞って解説します。
高速回転
高速回転はすべり軸受の方が有利です。転がり軸受だと、回転数が高いほど潤滑油が飛散しやすくなり、転動体や保持器に潤滑油が掛かりにくくなります。
転がり軸受の方が構造が複雑ですからね。潤滑油が掛かっていない軸受は直ぐに壊れます。この点で高速回転には転がり軸受は不利です。
化学プラントの場合、高速回転と言っても3600rpmが最高クラスなので、転がり軸受で普通に対応できています。
低速回転
高速回転に対して低速回転は、転がり軸受の方が有利です。低速回転だと、すべり軸受は潤滑油膜を作ることが難しくなります。構造が複雑な転がり軸受の方が、潤滑油膜を作りやすいです。
互換性
化学プラントでは互換性は非常に大事です。
- 壊れたらすぐに交換
- SDMの準備のために納期が早い方が良い
大量のポンプや減速機などを一斉にメンテナンスする化学プラントのSDMでは、互換性がある軸受の方が好まれます。規格が統一化されているからですね。
この1点だけでも化学プラントでは転がり軸受を重宝する理由になります。
転がり軸受・ベアリングの構造
一般にベアリングと呼ぶ場合は転がり軸受のことを言います。そもそも化学プラントではすべり軸受はほぼ使いませんからね。同じように、スラスト軸受もほとんど使いません。
バッチ系化学プラントでは「ラジアル軸受の転がり軸受」がベアリングとほぼ同義です。
内輪・外輪・転動体
転がり軸受は以下のような構造をしています。
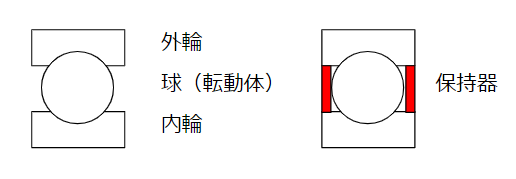
内輪・外輪・転動体で構成されています。球を固定するための保持器も付いています。これではちょっとイメージがつかめないですよね。回転軸に転がり軸受を付けたイメージを見てみましょう。
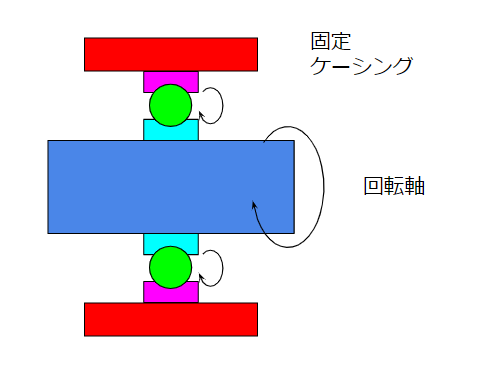
青色の回転軸と水色の内輪は固定されます。焼はめなどを利用することが多いです。赤色の固定ケーシングと紫色の外輪も固定されます。内輪と外輪が回転部と固定部にそれぞれ固定されて、その間に球である転動体が接触しています。
この球が転がることで、回転部と固定部の摩擦を極小化しています。摩擦には静摩擦・動摩擦・転がり摩擦と三種類合って、転がり摩擦がもっとも小さい摩擦です。
転動体は「球」と「ころ」
転動体は何の断りもなく「球」の形状を指していますが、分類上は「ころ」もあります。「球」をボールベアリング、「ころ」をローラーベアリングと使い分けます。「ころ」は「球」とは違って、いろいろな形状が考えられます。
円筒ころ・棒状ころ・針状ころ・円錐ころ・球面ころ
化学プラントの機械装置ではボールベアリングがほとんどです。
転動体の寿命
ベアリングの寿命は転動体の寿命そのものです。動機器の寿命は動くことによる部品の寿命。そう考えると、化学プラントで寿命を考えないといけない・メンテナンス上大事な部品がベアリング
汎用的なベアリングを調達するため、意識することは少ないですが、ベアリングの寿命を一度は考えてみましょう。ベアリングの寿命は速度と荷重でほぼ決まります。
- 速度は回転数
- 荷重は圧力
これで決まります。考え方としては、転動体が内輪や外輪と接触する強さ = 寿命
もっと簡単に言うと「どれだけ強く衝突したか」ということです。バッチ系化学プラントの場合、圧力はほどんとありません。影響が出るのは速度である回転数側。ポンプなら2Pモーターか4Pモーターかで倍半分変わります。
60Hz地域で2Pモーターなら3600rpm、4Pモーターなら1800rpmですね。
反応器の撹拌軸などで減速機を挟むと、撹拌軸での回転速度は100rpm程度まで下がります。回転数が遅い方が寿命は当然長くなります。
シールド型
シールド型とは転がり軸受であるベアリングにグリースを封入したものです。グリースが封入されたベアリングは、追加のグリース補給が無く運転が可能です。
グリースが外部に漏れず、外部からゴミや水が入ってこないため、安定運転が可能です。
それが運転管理・保全管理において大きなメリットがあります。いちいち何百~何千個もあるベアリングの潤滑油管理をするのは、労力が大きいですからね。
グリースは異物に弱いです。特に水が混入すると、質が劣化します。
粘度を持たせて液体というより固体に違い状態で維持しているグリースに、水が含まれるとその性質が劣化します。液体化してグリースが外部に漏れたり、油と水が分離して変性したり・・・色々な悪影響が考えられます。
そのため、ベアリングにとってはオイル潤滑の方が好ましいです。オイルなら多少水が入っても何とかなるでしょう。
とはいえ、グリースよりは良いというだけであり、水が混入することはそもそも厳禁。オイルの湯面管理をしないといけないことも、デメリットの一つです。オイルを管理するための油面計は非常に見難いですからね。だからこそ、ノーメンテのシールド型が好まれます。
シールド型は無難に使えます
オイルシールが問題
ポンプのベアリングの寿命は、金属部品の劣化そのものよりもオイルシールとその使い方にあります。オイルシールの寿命はベアリングより短いです。
屋外使用のポンプなどでは雨が大量に降ることがあり、オイルシール部から雨が混入してくるリスクが多いです。この辺の対応が、最大の課題。
すべり軸受の特徴
すべり軸受は、軸と軸受の間にオイルが入っていて、オイルの薄い膜が軸と軸受を遮断する構造とです。その特徴を紹介しましょう。
軸受寸法が小さい
すべり軸受では、薄い油膜分だけの隙間があれば良いので、小型で製作可能です。転がり軸受は、転動体がある分だけ大型になります。
バッチ系化学プラントでは、転動体はあまり大きくないので、軸受寸法が大きい転がり軸受はデメリットになりません。
上手くいけばノーメンテ
転がり軸受のような、機械的な接触部が無いため、すべり軸受は摩耗部が無いと言われています。したがって、「上手くいけばノーメンテ」と言われます。
ところが、化学プラントではそれが難しい。化学プラントでは、過酷な周囲環境で運転することが多いです。すべり軸受では軸受周りにオイルが常に充満している環境や、周囲環境の影響を受けにくい場面で使います。
バッチ系化学プラントでは設備の起動停止が多いです。すべり軸受では、停止している時に軸と軸受が接触する可能性があります。その状態で起動すると、軸と軸受が一瞬ですがダメージを受ける恐れがあります。
起動停止が多いほどそのリスクは高い。
連続的に動かす設備ならすべり軸受は有効ですが、バッチ系化学プラントでは連続運転をしないためにデメリットとして働きます。
ガス・雨・水などの影響を受けやすい
化学プラントでは腐食性のあるガスが発生します。ここに雨や水が降ってきたら、腐食性のある液体が生成されます。これが設備に付着すると腐食します。
一般的な設備よりも腐食が進みやすい空間が化学プラント。ここですべり軸受を使おうとしても、軸受部に腐食性液体が侵入し軸受のオイルを変性させたり、漏えいさせたりします。その意味でもすべり軸受は、化学プラントでは設備の安定運転に弱いです。
荷重方向
軸受の勉強をしている荷重方向が話題になります。ラジアル荷重とアキシャル荷重です。化学プラントの機電系エンジニアならあまり詳しくは知らなくても良いでしょう。
ラジアル荷重
ラジアル荷重とは半径方向・r方向の荷重のことです。ポンプや撹拌軸のような回転機械では遠心力による回転方向が必ず発生します。
軸は自重により「たわみ」、製作誤差によっても「たわみ」ます。そういう真円柱でない軸を高速回転させると遠心力がでます。この軸のブレを吸収するためにも軸受は大活躍。
回転機の軸受にはラジアル荷重を受ける特性が求められます。横型のポンプを停止させている時には軸受にはラジアル荷重が掛かっていると考えます。
アキシャル荷重
アキシャル荷重とは軸方向の荷重です。ラジアル荷重とは垂直方向の荷重です。
実はアキシャル荷重はポンプで顕著に発生します。これはポンプの羽根車前後で圧力が急激に変わるから。垂直方向に移動している機器でないのに、垂直方向であるアキシャル荷重を受ける格好になります。機械的・物理的にはちょっと面白いですね。
撹拌槽などが停止している時は軸受にはアキシャル荷重が掛かっていると考えます。
ベアリングの特性
ベアリングに求められる特性のうち代表的なものを紹介しましょう。
速度特性
ベアリングの速度特性ではdn値が有名です。
dn値
物は使えば使うほど劣化していくのは当然です。これを軸受について適用しましょう。転がり軸受の寿命は、転がり軸受にどれだけダメージが与えられるかで決まると考えます。
軸受に与えるダメージを評価するには何が適切でしょうか?物理現象を議論するとき、特に力学を議論するときは、位置・速度・加速度に着目します。運動方程式そのものの基本原則に立ち返ります。
軸受に掛かる力は、軸の回転時の摩擦力です。摩擦は速度に比例すると考えるのが普通。
軸受には速度に比例した力を受け、速度が速いほどダメージを受ける。
回転体における速度は、どう表記するでしょうか?
半径×回転速度ですね。
これを軸受の世界ではdn値と表現します。dは軸受内径・nは回転速度です。それぞれの軸受について、長期安全運転が可能な最大回転数をdn値で表現するようです。ですが、dn値で軸受を議論したことは私はありません。メーカーにお任せです。
4Pモーター
軸の回転速度はモーターの仕様で決まります。60Hz地区ではモーターの極数が4の時は1800rpm、2の時は3600rpmです。
$$ f=\frac{60×周波数}{曲数/2} $$
横型の渦巻ポンプなど汎用的なモーターには4Pモーターを使用します。これが2Pモーターであれば、回転速度が2倍になります。dn値が2倍になるので、2Pモーターは4Pモーターより軸受の寿命が1/2と考えても良いでしょう。
摩擦特性
転がり軸受が受けるダメージは摩擦です。摩擦は摩擦係数×速度で効いてきますね。高校の物理の世界です。摩擦係数を下げるためには、軸受の精度で決まるといって良いです。精度が悪いと本当にすぐに駄目になります。
ベアリングの精度が悪いと、摩擦力が過剰に加わり軸受がすぐに破壊されます。
振動騒音特性
軸受にダメージが出ると振動騒音が出やすくなります。これがメンテナンス時の主要指標の一つになります。転がり軸受はすべり軸受よりも振動騒音が起こりやすいです。
転がり軸受は、軸受の内輪と外輪の間に有限個の転動体があり、有限個の接点で接触しているだけです。
すべり軸受は、油膜で軸と固定部が接触しているため、転がり軸受よりも軸を支える接触面積が大きくなります。
接触面積が大きいほど、軸は安定して固定されるとともに、固定部が受ける応力が分散されるため、軸が受けるダメージが分散されます。
参考
最後に
化学プラントにおけるベアリング(軸受)は、目立たないながらも設備安定運転の鍵を握る重要部品です。
- 転がり軸受が化学プラントでは主流
- 回転数と荷重が寿命を左右
- シールド型やオイルシールの状態も定期的に確認
「どの軸受が使われているか」「どんなトラブルが起きやすいか」を保全担当として理解しておくことで、トラブル予防や早期対応が可能になります。
化学プラントの設計・保全・運転などの悩みや疑問・質問などご自由にコメント欄に投稿してください。(コメント欄はこの記事の最下部です。)
*いただいたコメント全て拝見し、真剣に回答させていただきます。
コメント