化学プラントの設備の設備が故障したときの応急補修について解説します。
設備はいつか壊れます。
使用環境が厳しい化学プロセスでは寿命も非常に早いもの。
寿命を予測しながら設備を使って良き、適切なタイミングで交換していくことで、安全安定操業をします。
応急補修をするということはこの寿命が読めていなかったということ。
応急補修が起きた時は考える時間が短く、即断しないといけません。
故障モードに対してどんな選択肢があるかを簡単にまとめました。
会社での保全体制によって多少変化する部分はありますが、基本は同じだと思います。
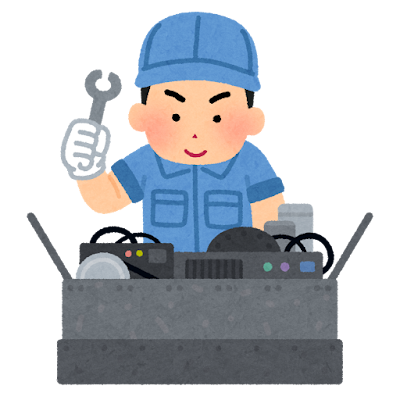
応急補修の目的
まずは応急補修の目的について考えてみましょう。
生産量の確保のためというのは分かりやすいですが、保全マンという視点で見ると他にも目的があります。
- 化学プラントの生産に対する考え方を学べる
- 化学プラントの保全としてできることを考えられる
大手企業だと日常補修レベルは施工会社に一任できる環境にあります。
ここに甘えてしまうとトラブル自体が少なくなっている現在では、保全として学ぶことは少なくなります。
化学プラントの生産に対する考え方なんて理解する気にもならないでしょう。この辺は保全だけでなく設計も同じですが・・・。
応急補修は最悪時の対応であって、これを防ぐために設備保全エンジニアが居ます。
応急補修を経験しながら、こんなことを二度と起こさないためには・・・と考えるきっかけになります。
純粋に応急補修って振り回されっぱなしで大変ですからね。
予備部品の持ち方・設備の型式や種類・設備の配置・・・
プラント設計思想に反映させるべき重要な要素だらけです。
摩耗した・折れた
設備が摩耗したり折れたりした場合の応急補修について解説します。
当たり前の話ですが、物が動けば摩耗します。
機械設備では摩耗により所定の強度を保てなくなると、最悪は損傷・破壊に至ります。
これが運転中に起こった場合に応急補修をしようとしても現実的に良い方法はありません。
- 溶接
- 溶射
- 焼きはめ・冷やしはめ
いすれも化学プラントの現場で応急補修するには無理があります。
火を使わないといけないから。
工場から作業場など安全な場所に一度移動させてから、修理します。
これだけで数日間は掛かるので応急補修としては時間が掛かりすぎます。
さらにどの方法も応急補修であって、設備に不連続部分を付けてしまう以上は早急な更新が必要です。
いつまた壊れるだろう・・・と不安になりながら日々を過ごさないといけません。
気にしすぎることなく、壊れたらその時になって考えるか!という度胸が付けばいいですが、
これが行き過ぎるとすべてをBM扱いにして、保全の意義が薄くなってしまう嫌いがあります。
亀裂が入った
亀裂が入った場合の応急補修について解説します。
これだけです。他に方法はありません。
溶接といっても、亀裂を直接埋めようとする補修と当て板を付けて溶接する補修の2つに分かれます。
とはいえ、やっていることはどちらも同じ溶接。
現場で火を使うかどうかという点で、摩耗や折れと同じ発想になります。
変形した
設備が変形した場合の応急補修について解説します。
- 不可能
設備が変形するとは、誰が見ても明らかな異常な状態です。
設計・運転のどちらに原因があるかは別として設備が異常な状態であることは間違いありません。
この状態で強引に動かそうとすると、すぐに壊れて大惨事になる可能性もあります。
機械的な力で強引に変形を戻すという方法や、火で炙るなど温度変化を強引につけて変形を戻すという方法もありますが、
上手くいけば御の字、ダメでもともと。という扱いで考えるべきでしょう。
あと1日だけで良いからなんとか耐えてほしい、などの状況でなければ変形に対する応急補修は考えない方が良いでしょう。
このあと1日だけ・・・ということが数年に1回は起こりえるのが怖いところです(笑)
ゆるみが起きた
設備にゆるみが起きた時の応急補修はいろいろあります。
- 増し締め
- ボルト取替
- 溶接で固定
- 治具で固定
ゆるみはボルトで繋がる部分で発生するので、ボルトを増し締めすれば基本的にはOKです。
ボルトが腐食してそうであれば取替をしましょう。
そういうメンテナンスのためにボルトの材質を犠牲にした設計をします。
ボルトでの固定を諦めて溶接や治具を使うという方法も考えられなくはありませんが、基本的に実施しません。
設備の取替やメンテンナンスを犠牲にするからです。
取替時の洗浄もできなくなり廃棄コストがあがります。
動機器のゆるみが起きる場合は、バランス調整や振動吸収を考えても良いかも知れません。
そもそも動バランスが崩れていたり、防振ゴムやバネが弱かったりして振動が大きくなって、ボルトが緩むことがあるからです。
動バランス調整の場合は専門のバランス調整器が必要だから、応急補修の範疇を越えていますね。
液が漏れた・腐食した
液が漏れてきたという時の応急補修について解説します。
- 溶接
- 当て板
- 樹脂で塗る
ここで上げた発想は応急補修の基本です。
どんな補修もこの3つに集約されるといって良いでしょう。
溶接は火を使うという意味で応急補修では極力使いません。
選択肢から真っ先に除外されます。
当て板は応急補修の基本。
配管では金属の板を当ててゴムなどでシールしてバンドで止めます。
設備内でもこれと同じ発想。タンタルやPTFEなど材質が高級になっているだけで発想は同じです。
樹脂で塗る方法も応急補修の基本。
ユーティリティ関係では液を止めずに補修する方法も開発されて行っています。
設備に対しても樹脂で塗り固める方法は一般に行われます。
ただし、当て板も樹脂も新品同様の状態に戻すわけでは無いので、使い方が変わらない以上は近いうちに寿命が来ます。
配管がつまった
配管が詰まったときの応急補修について解説します。
- 窒素ブロー
- 薬液洗浄
- 分解洗浄
この3つくらいでしょう。
運転継続のためにも早期復旧が基本の応急補修。
設備を分解するという最悪の手段に出ないために、インラインで処理できる窒素ブローが基本です。
何回もブローをして詰まりが取れればOKです。
それでもダメなら薬液洗浄。
水やスチーム以外にもプロセス液など有機溶媒を使う場合もあります。
プロセスによってまちまち。
インラインでの薬液洗浄も駄目なら分解洗浄です。
分解してブラシなどで物理的につまりを取ったり、別の配管と交換したりします。
詰まりが起きた時というのは配管設計よりもプロセス由来の方が大きいので、プロセス改善に期待せざるを得ないかも知れません。
それでも配管の形状が複雑であることは意外と多く、単純かも考えたいですね。
グラスライニングが壊れた
バッチ系化学プラントの特有な設備としてグラスライニングが壊れた場合の応急補修を紹介しましょう。
- 樹脂で塗る
- 当て板
このどちらかです。
樹脂は天板ノズルやマンホールのガラス面などに限定されます。
樹脂での補修は気相部に限定します。液相部では樹脂が絶えないケースが多いです。
ノズルのガスケットから液が漏れてガラス面が壊れたというケースが多いからこそ、樹脂による補修のニーズは高いです。
樹脂で塗る場合は補修業者は結構ありますので、応急処置として大活躍します。
当て板はタンタルという高級金属でガラス面を覆う方法です。
タンタルとガラスをPTFEでシールします。
気相部だけでなく液相部でも使える方法です。
この補修はあくまで補修。補修後の寿命は新品より短いです。
タンタル自体は耐食性がありますがPTFEの耐食性が問題だからです。
タンタルによる補修は施工メーカーにしかできないので、メーカーのメンテナンスマンに急遽お願いすることになります。
メンテナンスマン不足の現状では、対応してもらうのに時間が掛かってきています。
当て板補修に至らないようにするために定期診断が大事ですね。
FRPが壊れた
グラスライニングと同じでFRPも応急補修を解説しましょう。
- 樹脂で塗る
これだけです。
FRPが樹脂でできている以上は補修は樹脂で塗るしかありません。
グラスライニング設備の補修材としての樹脂と比べて、補修業者も少なく施工メーカーのメンテナンスマンも少ないので、補修には時間が掛かります。
グラスライニングと同じく定期診断を行って、応急補修が起きないようにしたいですね。
応急補修後のフォロー
応急補修は起きると他の業務を後回しにして、大至急対応します。
完了したときには達成感が満載。
だからこそ、その後のフォローを忘れてしまいがち。
その結果、また同じ応急補修を行う可能性もあります。
- 応急補修後の定期診断
- 設備故障の原因解析や対策
- 応急補修後の設備更新の計画
この辺をちゃんと考えるのが設備保全エンジニアです。
応急補修は単なる作業でしかありません。
エンジニアたるものその後の対策に自らの存在価値を置きましょう。
参考
最後に
バッチ系化学プラントの設備が故障したときの応急補修について解説しました。
基本は溶接・当て板・樹脂の3つ。溶接は難しいので当て板か樹脂。
摩耗・折損・亀裂・変形・ゆるみ・漏洩・閉塞に分けて解説しています。
バッチ系ならではのガラスやFRPにも触れていますが、基本は同じですよ。
化学プラントの設計・保全・運転などの悩みや疑問・質問などご自由にコメント欄に投稿してください。(コメント欄はこの記事の最下部です。)
*いただいたコメント全て拝見し、真剣に回答させていただきます。
コメント