ポンプ周りの配管設計(Piping design)の例を紹介します。
化学プラントではどこでも使うポンプですが、ポンプ周りの配管設計は意外と悩みがあります。
その理由は空間スペース。
単純に空地から建設したときにはスペースがいっぱいあって、基本に忠実な設計が可能です。
建設が終わってから増改築していくと、必ずと言っていいほどポンプの増設があり、その瞬間に配管設計の難易度がグッと上がってしまいます。
基本から応用まで幅広く使えるように、ポンプ周りの設計についてまとめました。
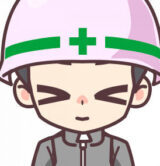
配管設計は機械エンジニアのこだわるべき部分です。
ポンプ周りの配管部品類
ポンプ周りで付けておきたい配管部品類を以下に示します。
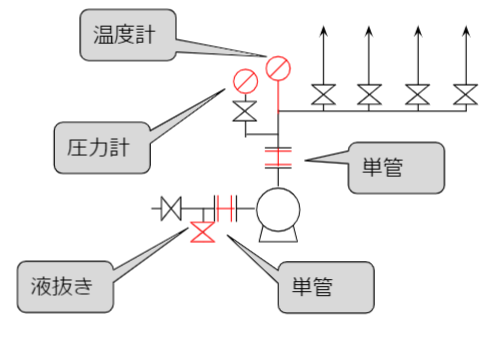
それぞれの要素の目的について解説します。
圧力計
圧力計はポンプの運転状況を示す典型的な計器です。
現地式の圧力計で十分です。
DCSに取り込む圧力伝送器を使うことはありません。
プロセスなら隔膜式圧力計を使うことが普通。
ポンプを据え付けて運転開始した状態で、ポンプの圧力計の指示値の範囲を圧力計に着色しておいて、
その範囲内で運転をしているかどうかを監視することで、ポンプの日常的な監視ができます。
性能曲線と合わせて能力検証に使うことも不可能でありませんが、難しいでしょう。
圧力計はポンプ出口から枝を取るように出すのが良いでしょう。
ポンプのベントライン(エアー抜き)も枝から施工できます。
ヘッダー上に圧力計を取るパターンも考えられますが、ヘッダーは配管のスペースのために取っておく方が良いです。
温度計
温度計はポンプで送る流体の温度を測定するためのものです。
これはかなり特殊な例です。
温度計は付けないケースの方が一般的。
ポンプを締切状態で運転したときにポンプの動力が流体に熱としてそのまま加わってしまうと、流体の種類によっては火災爆発を起こすものがあります。
化学プラントならではの怖い性質。
温度上昇を早期に発見するために温度計を設置する場合があります。
この場合は、温度計の設定値に対してポンプのインターロックを掛けるように仕組みを作ります。
温度計がちゃんと液温を測定できる位置が良いです。
ポンプ出口のヘッダーとの接続T管が理想的。
難しい場合は、圧力計と同じように出口から枝を取ります。あまりしたくはありませんけど。
液抜き
ポンプの吸込み口には液抜きを必ずといっていいほど設けます。
タンクがポンプへ押し込む形をイメージしていますが、吸込み形でも同じです。
液抜きバルブのすぐ1次側には遮断バルブを付けます。
これはポンプメンテナンスのためというのが1点。
ライン洗浄時の液抜き用に使用するのがもう1点。
液抜き量を最小化するために、ポンプ吸込み口のすぐ近くにバルブを設置するのがマナーです(笑)
ポンプ出口にも液抜きを付ける場合はあります。
これはポンプを逆回転させたくない場合や、ポンプ出口の液を早く抜きたい場合に使います。
ポンプ出口の液抜きはエアー取り込み口としても使用できます。
圧力計の枝の部分に抜きバルブを付けると良いですね。
単管
ポンプの出口も入口も単管を付けることを心がけてください。
これはポンプメンテンナンスが最大の理由。
配管フランジの切り離し個数を最小化するため。
吸込み口は遮断バルブがその機能を持ちますが、出口はヘッダーバルブまでノーフランジの場合があります。
この場合は、出口のヘッダーバルブ分すべてのフランジを切り離さないと、ポンプのケーシングを分解できない場合があります。
それならポンプ出口とヘッダーの間に単管を挟むと良いでしょう。
振動吸収用のフレキシブル継手を設けた場合は、単管代わりに使えます。
配管改造をした直ぐ後にそのラインを使う場合は、配管工事の汚れを取るためにテンポラリーストレーナーを設置します。
テンポラリーストレーナーを付けるためには、単管に付けると都合がいいです。
ポンプ本体のフランジを分解するのは単純そうに見えて、気を使います。
変にフランジの締め付けをすると、ポンプが歪んで使えなくなる場合があるからです。
影響の少ない配管部分を切り離したり繋ぎなおすのは抵抗感が少ないですね。
この単管、基本のはずですが、意外とできていないことが多いですよ。
吐出ライン
ポンプの吐出ラインの配管設計の考え方を説明します。
ここは純粋な圧力損失計算の世界。
ポンプ流量と圧力損失から配管口径を決めます。
標準流速を使えば計算はかなりの部分が省略できるでしょう。
圧力損失を最小化するためにヘッダーの向きや並びなど考えられる要素もありますが、スラリーなどの特殊な場合を除いてあまり重視されません。
配管レイアウトを多少変えても圧力損失があまり変わらないからですね。
吸込ライン
ポンプ吸込ラインの配管設計の考え方を説明します。
吸込ラインの口径は吐出ラインより1サイズ上げます。
これは圧力損失計算を省略するためですね。
昔のプラントでは吸込ラインと吐出ラインが同サイズというケースをよく見ます。
増改築が無く同じ製品を使い続けている場合は問題でもありませんが、新製品が入るとちょっと考えないといけません。
最近の製品では、スラリー性が高かったり・粘度が高かったり・結晶が析出しやすかたりと厄介な性質の液が増えています。
ギリギリのプロセス設計をせざるを得ないのでしょう。
そう簡単に新しい反応経路なんて作れませんからね。
この場合、キャビテーション・NPSHの問題が沸き上がります。
その場合、吸込ラインを1サイズ上げておけば基本的には問題になりません。
循環ライン
まずは循環ラインの考え方を紹介します。
循環ラインはP&ID上は下のような形状をしています。
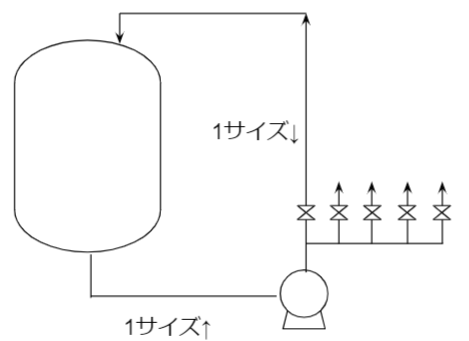
ここで抑えておくべきポイントは以下の3つ
- 循環ラインはポンプヘッダーの一番「手前」に置く
- ポンプサクションラインの口径はポンプヘッダーより1サイズ上げる
- 循環ラインはポンプヘッダーより1サイズ下げる
建設したばかりの時はこの考え方で統一されていても、改造を繰り返していくと結構無茶苦茶になりますよ^^
ヘッダーの一番手前
循環ラインはヘッダーの一番手前に置きます。
これは循環ラインがポンプヘッダーに絶対に必要な要素だからですね。
ポンプで送る先は増改築を繰り返していくうちに変わっていきますが、
循環ラインは1度付けると基本的に変更ありません。
この思想で、循環ラインはポンプの位置が決まったら自動的に決まる一番「手前」に配置します。
前提として、ポンプはタンクに固有のモノという発想があるのですが、これが覆されるケースが増えているからです。
タンクA | ポンプA |
タンクB | ポンプB |
こんな感じでタンクとポンプが固定化されるべきですが、増改築を繰り返して、別の製品が導入されたときにはこんな使い方をする場合があります。
タンクA | (使わない) |
タンクB | ポンプA |
ある製品ではタンクAそのものを使わず、タンクBは使うけどポンプBでは不適切なのでポンプAを使うというケースです。
流量・揚程などの能力や材質などによっては、こんなケースは十分にありえます。
ポンプAの立場に立つと循環ラインはタンクAに対するもので固定と思っていたら、タンクBに対して循環をするケースも出てくるということです
増改築を繰り返すほど思想が維持できなくなっていきます。
1サイズ下げる
循環ラインの口径は1サイズ下げるのが基本です。
これも圧力損失の問題。
送り先の配管口径と同じサイズで組んでいると、制御が難しくなります。
循環させながら一定量を送るという場合に、圧力損失の少ない循環ラインに流れ過ぎるという問題ですね。
送り先の流量計の調整弁と循環ラインのバルブの開度調整だけでは、十分に制御ができないというケースは日常的に起こりえます。
それなら最初から1サイズ下げておいた方がいいだろう、という考え方です。
循環させながら送るのか・循環なしで1パスで送るのか、という思想に依って簡単に変わってしまいます。
ヘッダー
ヘッダーの配列も一定の考慮が必要です。
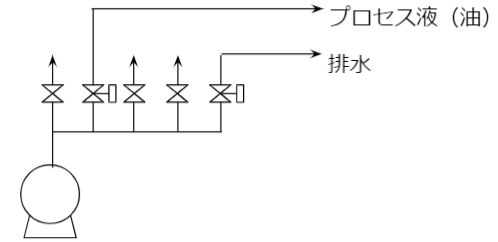
同じポンプで送り先を変えて、タンクの分液をする場合がバッチ系化学プラントでは典型例です。
プロセス液である油層はヘッダーの中間に、排水である水層はヘッダーの末端に置きます。
これは分液後の洗浄性というよりは設備洗浄の洗浄性を考慮しています。
分液では水層→油層の順にヘッダーを液が通過します。
油層を送った後に送る洗浄液は油層と同じ溶媒であることが普通です。
この場合、ヘッダーのどの位置に油層送りと水層送りがあっても意識することはないでしょう。
一方で設備洗浄時は、最終的に水で洗浄をすることが普通です。
洗浄廃水はプロセスで発生した排水と同じルートで書類することが普通です。
ヘッダーの末端まで洗えるように、水をヘッダーの末端に持ってくると都合が良いです。
ヘッダーの向きと作業性
ヘッダーの向きと作業性について解説します。
工場レイアウトに関連する部分であり、思想が分かれやすいですよ。
現場作業性重視
現場作業を重視した基本形です。
バッチ系化学プラントではこれが多いでしょう。
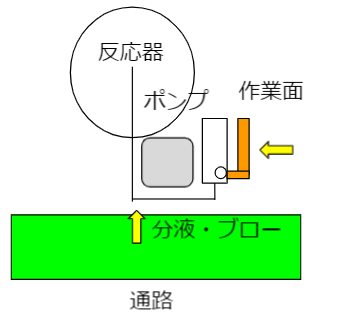
通路から中に入った部分に反応器があり、反応器の底からポンプに向かって配管が接続されます。
ポンプの吸込みノズルが通路側に配置されているケースを現場作業重視型と呼ぶことにします。
- 吸込み配管が遠回りになる
- ポンプ吸込み口の点検はしやすくなる
- 分液やブロー操作は楽になる
- デッドスペースができる
これらの特徴があります。
吸込み配管が遠回りになるのは、下のモーターメンテ重視ケースを見る方が速いです。
ポンプ吸込み口の点検が楽になるのは、通路側から配管取外し作業ができるから。
液抜き作業などもしやすくなりますね。
バッチ系化学プラントではポンプ周りの手動操作がいくつかあって、分液や窒素ブローなどは現場で作業をします。
カメラや導電率計で判定したり、自動弁を付けてシーケンスでブローをしても、現場で監視する作業自体は残っています。
このケースではデッドスペースができやすいデメリットがあります。
上の図では、サクション配管とポンプの間のグレー部分です。
ここには新たな設備や配管を付ける余地がほとんどありません。もったいないです。
モーターメンテ重視
モーターメンテ重視ケースは、現場作業重視ケースとはポンプの位置が逆になっています。
モーターが通路側に出ています。
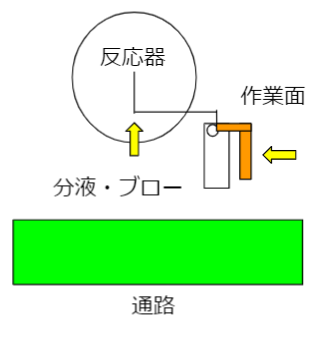
このケースはサクション配管が最短化されていることが分かるでしょう。
モーターが通路側にあるので、モーターの定期点検にも向いています。
一方で分液やブロー作業をするためには、通路から一歩先に入らないといけないデメリットがあります。
連続プラントは一般にこのケースです。
最近では、バッチプラントでもこのケースがトータルでメリットがあると判断している方向ですね
屋外タンクなど連続的な部分では、バッチプラントでもこのタイプを積極的に採用しています。
並列設置
2台のポンプを並列設置するケースを考えましょう。
バッチ系化学プラントではこのケースが増えています。
2台のポンプでヘッダーを共有する場合が多いです。
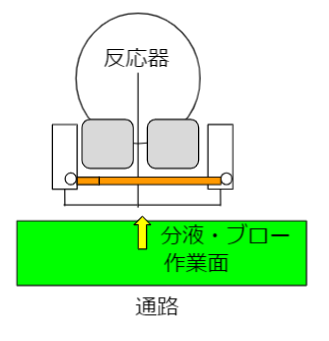
ヘッダーを共有する場合、その配置はかなりの制約を受けます。
ポンプ1基だけの場合は、ヘッダーの向きをある程度変えることができて、
- 通路側から操作する
- 通路から中に入って操作する
という2パターンから選べます。
2台のポンプでヘッダーを共有する場合はそんな選択肢はなくて、2台のポンプを最短で繋げることが普通です。
通路から作業するパターンしか基本的にはありえまん。
この場合、デッドスペースが必ずできます。
現場作業重視型でもモーターメンテ重視型でもデッドスペースはかなりの限界があります。
自動弁
自動弁の追加はバッチ系化学プラントでは日常的に起こりえます。
送り先が増えたからとりあえず自動弁も増やす
こんな見積をしてP&IDもとりあえず書いてしまいます。
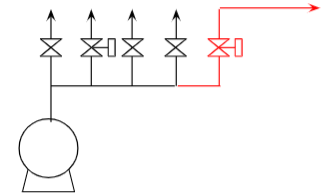
配管と自動弁を追加している絵です。あまり違和感はないでしょう。
ですが、自動弁を足すために弁本体・ソフト改造含めたコストは高くなります。
こんな時はちょっと考えてみましょう。
下のような逃げ道を見つけられる場合があります。
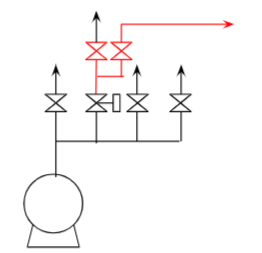
そのヘッダーの中に、特定の製品では使わないラインに自動弁があって、そこから枝を取れば対応できるというケースです。
これはヘッダーの形状を複雑にしていきます。
ヘッダーの隣り合う配管の間隔を一定に保つ同一方向にヘッダーを伸ばしていく、という基本思想を変えることになります。
自動弁のメンテナンス性も悪くしていく方向です。
それらの犠牲を払ってでも、イニシャルコストを下げる方を優先するというケースで採用されがちです。
P&IDを書く段階で気が付けるようになりたいですね。
逆止弁
ポンプでは逆止弁の問題がしばしば問題になります。
単独ライン
吐出ラインのポンプ直近に逆止弁を付けると、逆止弁の構造上どうしても液がたまってしまいます。
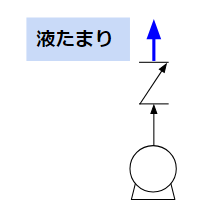
そもそも逆止弁をポンプ出口に設ける目的は、ポンプの逆回転の防止です。
ポンプを止めた時にポンプより高い位置にある液は自重落下してきます。
ポンプを送る方向と逆方向の回転をすることでポンプを破損させる可能性があります。
- ねじ込みのインペラがシャフトから外れる
- モーターに逆電流が流れる
最近では対策を取ったポンプが多いので、あまり問題になることはないでしょう。
逆止弁を付けることで逆に問題が起きる可能性があります。
逆止弁の上側は液が溜まり下側はガスが溜まった結果、ポンプの液満たしができない場合があります。

ガスが溜まっている状態で液をポンプ内に入れようとしても、ポンプ内に液は入ってきません。
ガス部が多少圧縮するだけで終わり。
ポンプのインペラに液体が満ちていない状態で、起動しようとしてもポンプは動きません。
逆止弁を付けた場合はガス抜きの方法を考えないといけません。
捨てバルブ
シンプルに思いつく方法です。
捨てバルブを置きます。
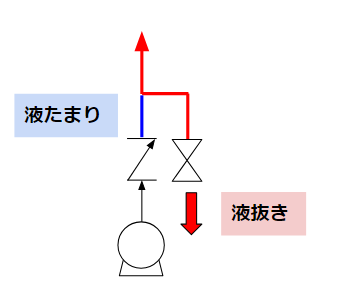
液たまりの量が逆止弁の内部と配管のT管部分のみの少量にすることができます。
普通はこれでOK
ポンプ室内にガスが溜まっていても、ポンプを少し回せばOKです。
逆止弁の上側の液量が少ないために、逆止弁を押しのけてガスが上部に流れていくことを期待します。
バイパス
バイパスも捨てバルブとほとんど変わりません。
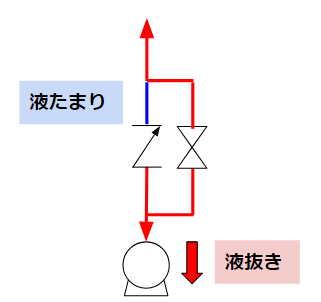
捨てバルブの場合は、一回一回盲フランジを開けてバケツ等で液抜きをしないといけません。
バイパスの場合はバケツを準備せずにバルブをちょっと開けたり閉めたりするだけで解決します。
逆止弁を付ける目的はポンプの逆回転を過度に起こさないようにすればいいのであって、逆回転をゼロにするという意味ではありません。
バルブをちょっとでも開けてガスが抜ければ何とか起動できるでしょう。
オリフィス
バイパスは毎回開けるのが面倒だから、オリフィス等で微妙に抜け道を作ろうという発想です。
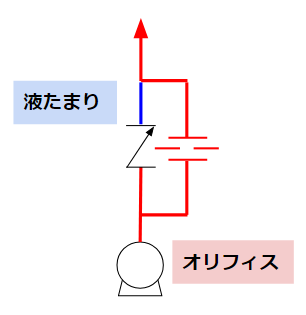
バッチ系ではこのケースはあまり見ません。
連続的に運転しているわけではないので、ポンプが停止している状態はバッチ運転では必ずあります。
ここで、オリフィスを付けているだけだと別の系から液が逆流してくる可能性があります。
窒素ブロー
逆止弁上部の液を窒素ブローで送ってしまうという発想があります。
窒素ブローを使うと、捨てバルブやバイパスの意味はあまりありません。
自動化もしやすいので窒素ブローは割とおススメです。
集合ライン
逆止弁の問題は単独配管だけでなく集合配管でも起きます。厄介ですね。
複数のポンプ出口が1つの集合管に合流するケースを考えましょう。
ここでポンプ直近に逆止弁が付いているとします。
単純に2つのラインを接合すると下記のようなイメージになります。
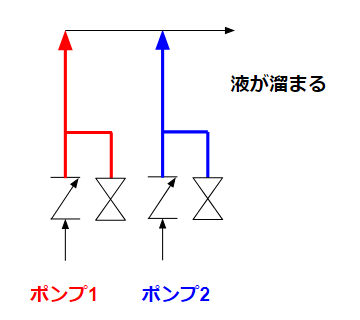
ポンプ出口の逆止弁が相対的に低い位置にあって集合管が高い位置にあると、各ラインの逆止弁出口には液が溜まります。
液抜き・ガス抜きが大変で窒素ブローが必要でしょう。
配管を少し上げる
配管ラインを少し改造して以下のようにします。
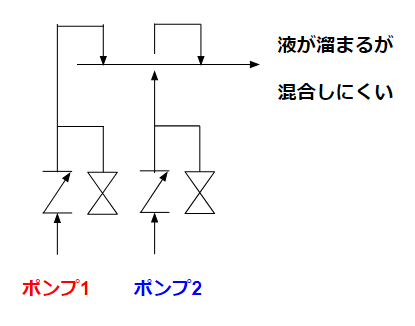
2つのラインからの液が逆止弁に溜まりにくくなります。問題が解決したように錯覚するでしょう。
しかし、実際には液が溜まります。
というのも集合ラインの枝管がそのライン中の一番高い場所にあるとは限らないからです。
たいていは、集合ラインからタンクまでの配管のどこか(タンク手前)が一番高くなるでしょう。
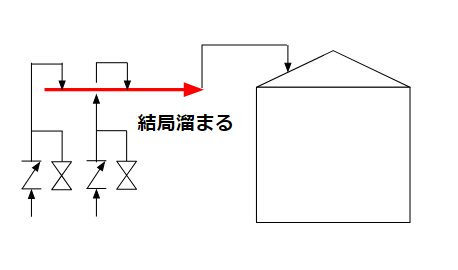
そうするとこの方式では、逆止弁からの漏れこみのリスクを若干下げるだけの効果しか期待できなくなります。
逆止弁を高い位置に
現実的な解として逆止弁を高い位置に付けることが多いです。
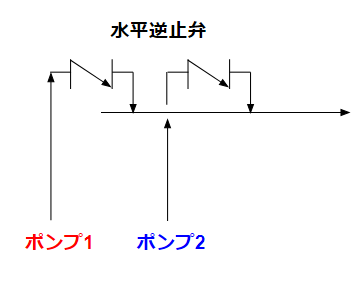
この結果、以下のような効果が期待できます。
- 集合管からの液が逆止弁に漏れこむ確率は低い
- ポンプ出口の立ち上がり部にガスが溜まっても、ポンプは液体で満たされる確率が高い
- 液体が自重落下で引き落とされても、ポンプが逆回転する量は少ない
逆止弁が高い位置にあってメンテナンスしにくいという問題は残りますが、運転面での課題はかなりクリアできます。
参考
配管設計は化学プラントの機械系エンジニアにとってとても重要な知識です。
特にポンプ周りは失敗しやすいので、ポンプに関する勉強も欠かせません。
関連記事
関連する配管設計の考え方をさらに知りたい方は、以下の記事をご覧ください。
配管設計全体としてはヤンさんの【失敗しない配管設計法】プラント配管設計がわからない?その勉強法と基本を解説!が参考になります。
最後に
バッチ系化学プラントのポンプ周りの配管設計について解説しました。
圧力計・ガス抜き・液抜き・単管などの組み合わせが必要です。
吸込・吐出・循環に分けて配管設計の考え方を示し、やっかいな逆止弁の問題にも触れています。
化学プラントの設計・保全・運転などの悩みや疑問・質問などご自由にコメント欄に投稿してください。(コメント欄はこの記事の最下部です。)
*いただいたコメント全て拝見し、真剣に回答させていただきます。
コメント
セントリーヒューガルポンプについて質問です。
吐出側にバルブまたはコックを必ず設置して流量を絞る必要があると教えられたのですが、インバーター制御をするなら必要ないんじゃないかなと疑問を持ち始め、ネットを彷徨っているうちにこちらのホームページをみつけました。
ほかのネットも調べてみましたが、バルブをつける必要があるなど書いてる情報が無く気になっています。
もしこの本に書いているなどありましたら教えて頂きたいです。
よろしくお願いいたします。
流量調整という意味ではインバータを付ければバルブは無くても運転可能な場合はあります。
インバータの設定による運転能力の変化と、バルブの開度調整による運転能力の変化は、別のパターンですので、
インバータだけで設定できるのであればバルブによる調整は要らないでしょう。
ただし、インバータの場合は渦巻ポンプだとそんなに広い範囲で調整はできませんので、バルブがあった方が現実的には調整しやすいです。
ポンプの出口にバルブを付ける目的は、起動時に液でポンプを満たすことと、停止時にポンプの逆回転をさせないことでしょう。