プレート式熱交換器について解説します。
化学プラントに限らず幅広い用途で使われます。
熱計算の基本を学べる設備で、多管式熱交換器よりも先にマスターしたい設備です。
プレート式熱交換器の原理と特徴
プレート式熱交換器の原理は、プレートを挟んだ2流体の熱交換です。
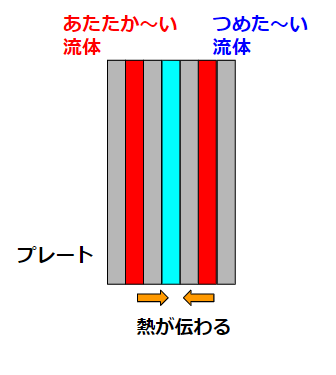
平板と流体の間で熱交換がされます。
伝導伝熱と対流伝熱を単純に組み合わせる熱貫流モデルを実現したシンプルな設備とも言えるでしょう。
伝熱の基本が詰まった設備です。
このモデルで熱交換の効率を上げるためには
- 隔壁であるプレートはできるだけ薄く
- 流体もできるだけ薄く
と薄さが大事になります。
薄さを重視するがゆえに強度を犠牲にしています。
だからこそ化学プラントでは強度が求められない部分の熱交換にプレート式熱交換器を使います。
- 液液の熱交換
- スラリーなど詰まり要素なし
- 非危険物
この辺りが対象になるので、適用できる場所は意外と狭いです。
液の流れの組み合わせは大きく2つ考えられます。
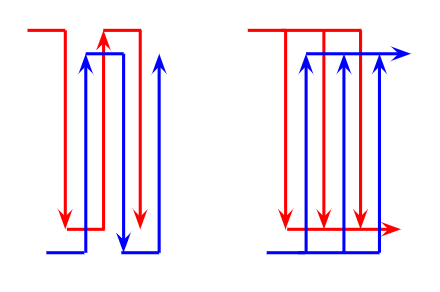
左の交互に流れるパターンが古典的に分かりやすい例。
右のように並列的に流すパターンの方が一般的でしょう。
- 1か所当たりの流速が低くなり圧損が低い
- 暖かい液を上から流し冷えて密度が上がったら下から抜き取る、という自然対流効果がある
というメリットがあります。
2つ目の自然対流効果についてはオプション的な効果です。
暖かい液を下から流して冷たい液を上から流しても、運転自体は可能です。ちょっと効果が下がるだけ。
バッチ運転ではある製品では加温目的で別の製品では冷却目的で、使いたい場合があります。
そういう時にプロセス液側・ユーティリティ側それぞれの入口を固定してしまう方が、やりやすいです。
プレート熱交の特徴を簡単にまとめましょう。
- 省スペース
- 熱交換の効率が高い
熱交換率の高さが最大のメリットです。
省スペースはどちらかというとおまけ的な要素。
プレート形状
プレート形状は1つの設計要素になります。
伝導伝熱だけを考える場合はプレートの板厚だけが設計要素となりますが、対流伝熱にはプレート形状が効いてきます。
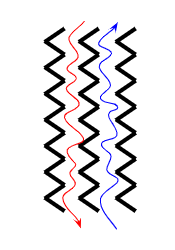
このように、プレートをあえて凹凸を付けることで、流体の流れを変えようとします。
流体の流れを変えることで撹拌効果を狙って、境膜部を薄くする・乱流効果を生み出すというような思想です。
これで伝熱性能を少しでも上げようという工夫をメーカーはしてくれます。
プレートの形状はメーカーによっていろいろな種類を開発していますが・・・
ユーザーレベルでは何でもいいというのが実態ではないでしょうか。
私も意識したことはほぼありません。
シール
プレート熱交換器はシールが大きな設計要素になります。
ガスケット
古典的なシール方法はガスケットです。
2枚のプレートで暖かい流体が流れるエリアと冷たい流体が流れるエリアを、ガスケットで分割する構造です。
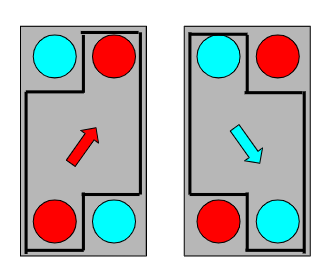
ガスケットタイプであるがゆえに以下の特徴を持ちます。
- ガスケット材質に制約がある
- 高圧では使用できない
- 分解が容易
化学プラント的には分解が容易という点に重きを置いています。
というのも清浄で安全な流体を扱う機会の方が少ないから。
腐食・閉塞との戦いである化学プラントでは、分解清掃はメンテナンス上とても大事です。
伝熱性を上げるために薄さを追求したプレート熱交だからこそ、隙間腐食の問題が常にまとわりつきます。
溶接
最近では溶接タイプが増えてきました。
溶接といってもいくつかの種類があり
- ろう付け
- 片側溶接
- 両側溶接
と種類はあります。
いずれもガスケットの漏れと強度不足を補うための手法です。
とはいえ、化学プラントでは使う機会は少ないでしょう。
材質
プレート熱交換器の材質はプレートとシールの2つが対象となります。
プレート
SS400はさすがに使わないでしょう。
隙間腐食を気にして寿命を延ばすために高級金属側にシフトしているイメージです。
ガスケット
ガスケットはゴム系もしくはフッ素樹脂系のどちらかです。
化学プラントで無難なのはPTFEでしょう。
シール性を追求すると効果になります。
プレート式熱交換器の拡張性
プレート熱交の特徴の1つに拡張性があります。
これはガスケットタイプを想定していますが・・・
正直言って邪魔でしかありません。
メーカー視点では「後々拡張できるように予め大きめにガイドを作っておく」という思想ですが・・・
拡張性を決めるのはユーザーであって、メーカーではないはず。
この辺、プレート熱交メーカーはなかなか頭が固くて融通が利きません。
プレート熱交換器のメリットである「省スペース」を自ら壊していくスタイルに見えています。
プレート式熱交換器のメンテナンス性
プレート熱交換器はメンテナンス性が問われる設備です。
チョット極端に言うと、
- 分解洗浄して何十年も使おうとする
- 5~10年くらいで取替する
という2択を考えないといけません。
分解洗浄を重視するならガスケットタイプになりますが、前述のとおり拡張性を勝手に付与されて省スペース性を失います。
その結果、他の設備を置く拡張性がないプラントになることも。
腐食環境が厳しくなっていけばいくほど、分解洗浄しても溜まり部の腐食が出てプレートを交換せざるを得ない状況になっていきます。
その結果、プレート全数を交換することも。
分解洗浄費用も含めれば一式購入しなおした方が安いということになります。
分解や洗浄をできる環境も限定されています。
自社の運転員や常駐協力会社員が行うのか、メーカーに輸送するのか。
SDMでの時間との勝負になりがちです。
そのために冗長性を持たせて並列設置したら元も子もありません・・・。
10年も持たない消耗品と考えて溶接タイプを選ぶのは1つの手だと思います。
運転・設計・保全の高度のコミュニケーションでどちらのタイプを選ぶのか、決めることになるでしょう。
プレート式熱交換器の液封
プレート熱交換器でプロセス液を加熱するのは注意が必要です。
というのも液封になる可能性があるから。
バッチ系ならではです。
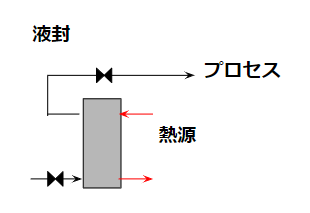
プレート熱交を通じてプロセス液を加熱して仕込みをした後、バルブを閉めます。
ここでプレート前後でバルブを閉めきってしまう例が考えられます。
プレート直近の前後バルブを閉めるのではなく、ポンプ出口とタンク入口のバルブを閉めきってしまって道中のプレート熱交が液封になってしまうという場合です。
こういう時は液封対策をしないと、簡単に漏れてしまいます。
プロセス液でなくても危険ですが、プロセス液なら火災爆発に繋がるので本当に注意が必要です。
最後に
プレート式熱交換器の特徴などを解説しました。
省スペース・高熱効率ですが、腐食・閉塞・強度などに課題があります。
液液熱交換器としては優秀なので、多管式熱交換器などと使い分けをしっかりしたいですね。
特にメンテナンスはこれからしっかり考えないといけないテーマです。
化学プラントの設計・保全・運転などの悩みや疑問・質問などご自由にコメント欄に投稿してください。(コメント欄はこの記事の最下部です。)
*いただいたコメント全て拝見し、真剣に回答させていただきます。
コメント