TBMとCBMの使い分けについて私なりの考え方を紹介します。
化学プラントのような設備産業と言われる設備では、設備のメンテナンスはとても大事です。
メンテナンス方法としてTBM・CBM・BMという3つの指標を使い分けますが、この中でもTBMとCBMは
「どっちを選べばいいの?」
「そもそもどういう違いがあるの?」
ということは意外と分かりにくいかもしれません。そこで、TBMとCBMの私なりの解釈を紹介します。
この記事は、TBMシリーズの一部です。
TBM?CBM?BM? 保全用語を“なんとなく”で使っていませんか?
TBMの設定周期を変更するときに考えるべきこと
TBMとCBM|設備保全のベテランでも悩む問題
TBMとCBMの定義
TBMとCBMはそれぞれ時間保全(Time Based Maintenance)と状態保全(Condition Based Maintenance)のことです。
簡単に言うと以下の通りになるでしょう。
- TBMは定期的に部品を交換
- CBMは定期的にデータを取りその状態に応じて部品を交換
ここまでなら分かりやすいです。
CBMは常時運転状況を監視して、あるタイミングで交換修理を判定するというニュアンスでとらえるでしょう。
でも、化学プラントのようなSDMや定期修繕が特定の時期に限られている時は、CBM的に保全をしようとしても結局はTBMという時間の概念の制約を受けてしまいます。
TBMとCBMの解釈
さて、私が担当する工場でのTBMとCBMの解釈をしても見ましょう。
TBM
一定の期間で絶対に交換修理をすることが求められる機器に対する保全。オーバーホールという言い方もします。運転時の診断はそれなりに行いますが参考情報という位置づけです。
CBM
交換修理の目安は大体決まっていますが、絶対条件ではなく前後の余地があります。運転時の診断はTBMと同じでそれなりに行い、劣化傾向の早い設備と遅い設備の優先度付けをします。
体感的にはTBMをしっかり設定して、その他の壊れやすい設備はCBMでフォロー、影響が低そうなものはBMという使い分けです。
補修費という視点からは、各年での費用が平準化されるか長期的な費用の見通しが立つことが大事です。
CBMで判定が付くのは、来期に設備を修理するという判断を前期に行うという程度だと思います。
というのもCBMの精度を上げるのはとても難しいから。
運転時の検査(OSI)で分かる情報を頼りにするのがCBMですが、温度・振動・電流などの古典的な情報では数年先の予想を立てるというほどの精度はでないです。
DXで設備診断技術を向上させるのは、この精度向上を狙う意味があります。
今よりも1年前余裕を持った予測をして、故障のリスクを下げるという価値になるでしょう。
TBMの設定方法
TBMの設定は保全上とても重要です。
設定方法についてよくあるパターンを紹介しましょう。
劣化と故障
まずは、設備が劣化して故障に至るまでの、状態変化を超簡単に図示してみましょう。
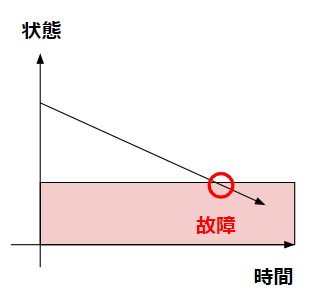
設備を使い続けていくと時間とともに状態が劣化していき、あるところまで劣化すると故障するというイメージです。
本当なら劣化するほど故障確率が上がるという確率論的な視点になりますが、実務的には判定ラインを設ける方が良いでしょう。
「設備の使用条件が一定である」というのが前提条件にあるので、製品切り替えが多いバッチ工場ではこの曲線の傾きは結構な変動があります。
生産品目を意識しないと痛い目を見る場合もあるでしょう。
修理
さて、設備が劣化していって故障したらとても困るので、修理しないといけません。
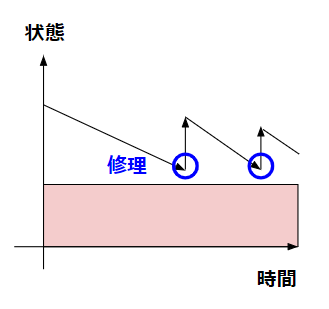
修理すると状態が一定のところまで回復します。購入時の状態までは戻りません。
そこからまた使用していくと、当然ですが劣化します。
この劣化速度は修理前よりも早いと考えるのが普通でしょう。購入時とは違うからです。
こうして劣化と修理を繰り返す形です。
私はこれをゲームのRPGなどであるHPと同じ視点でとらえています。メンテナンスは僧侶の回復って感じですね。大事です。
TBMの周期(実績あり)
TBMは保全周期を決めることが全てと言っていいです。
何期に1回交換修理をするか
これを判定するために時系列情報として管理しないといけません。
まずは実績が多数ある設備で、新規購入した設備のTBM設定についてです。
基本的には実績設備と同じTBM周期で決めれば良いでしょうが、絶対視はしない方が良いです。
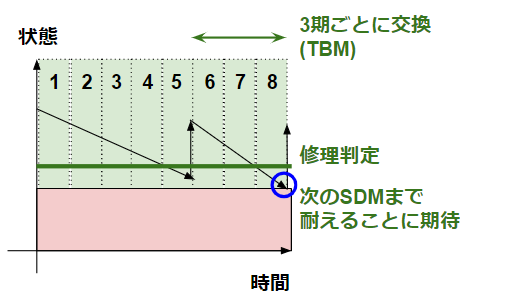
TBM周期を決めるには、修理判定というラインを決めることになります。
実績のある設備のTBMが4期だったから、新品の余裕を含めてTBM5期にしようと設定したとします。
このケースでは4期目の前半には修理判定ラインまで到達しているけど、5期目まで運転を止めれないので5期目に交換修理しています。予想通りに進みました。
そして6期目を迎えて、8期目の初期にはまた修理判定ラインまで到達しています。
それでも8期目終わりまで絶えざるを得ません。
こういう緊張感のある保全をしている会社は結構あると思います。
4期の周期で実績があって5期目まで持ったのだから、次は9期まで持つだろう!って安心していたら8期で駄目だった・・・というケースです
仮に8期目を持ったとしても、6期目~8期目のサイクルを見てTBMは3期と設定しなおすことになります。
初回購入から1回目までの修理のサイクルや過去の実績を、信じすぎては危険でしょう。
TBMの周期(新規)
実績のない設備に対してTBMを決めるときの方法を紹介します。
新たなメーカーの設備・新剤導入時の設備など、保全周期が読みにくい場合です。
この場合は、徐々に周期を延ばすという方法になります。
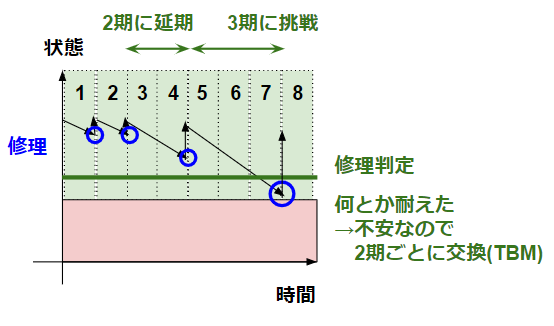
例えば、最初の1期を終えたらとにかく修理します。
その結果を持って2回目のサイクルを決めますが、運転条件や運転頻度の問題で2回目も1期で修理というケースが多いでしょう。
よっぽど運転条件が緩くて問題ないと言い切れない限りは・・・。
2期目を終えてようやく安心感が出てきたら、TBM設定の時期になります。
少なくとも1期ずつ見ていく必要がないと判断できれば、2期に延ばします。
次のサイクルでは3期に延ばしていく感じです。
どこかで、修理判定ラインを越えることになるでしょう。
この図の場合では、4回目のサイクルの5期~7期目で判定します。
7期目に修理判定ラインを迎えて7期目終わりまで何とか耐えたので、3期と判断したいところですが、余裕を見て2期とせざるを得ないでしょう。
CBMのイメージ
CBMのイメージを紹介します。
CBMはTBMのように時間を決めて交換するわけではありません。
設備の運転状態を定期的に監視して劣化度を調べます。
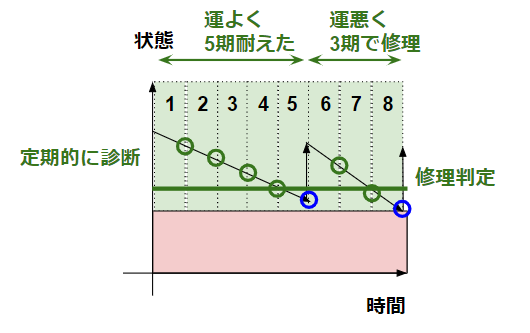
CBMには以下の問題があります。
- データ採取に費用が掛かる
- 統計的な解析が必要
- 得られた結果が活かしにくい
設備の状態診断に使うツールはアナログな測定器が多いでしょう。
これを人が設備の直近で使ってデータ採取するという方法です。
人が使うからこそ、診断の周期が定期的なものになってしまいます。
例えば振動値を測定して、振動値が一定値以上になれば保全をするという感じです。
人が介在するので費用が発生します。
これを解決するために測定装置を設備に付けて、オンライン監視する設備をDX関連商品として積極的に販売されています。
バッチ工場では24時間365日同じ状態で運転しているわけではないので、これがあまりうまく機能しません。
結構な統計的データを集める必要があるでしょう。
バッチ工場の場合は、人が測定するにしても「測定したときは設備が動いていなかった」ということはよくあります。
この瞬間にCBMの信頼度は落ちていきます。
さて、オンラインなどの常時監視システムでCBMを適切に設定したとして、修理判定ラインを迎えるかどうかがどのタイミングで分かるでしょうか?
- 仮に直線的に劣化する設備だったとして、TBM3期の設備に対して、1期目終わりに3期目の交換を判定できて得られるメリットは大きいでしょうか?
- 直線的に劣化するという予想は正しいでしょうか?
- CBMするくらいならTBMの方が分かりやすいのではないか?
この辺りの問題があって、少なくともバッチ工場ではCBMに重きをおいてはいません。
参考
最後に
バッチ系化学プラントの設備をTBMとCBMどちらにするか決めるときに考えたいことを解説しました。
TBMで周期を決めて予算を確保して適切に保全するのが基本です。
CBMは投資に対して得られるメリットが、修理費用だけを見るとほとんどないと思います。
どちらかというと労務費削減や少子高齢化の視点でしょう。
化学プラントの設計・保全・運転などの悩みや疑問・質問などご自由にコメント欄に投稿してください。(コメント欄はこの記事の最下部です。)
*いただいたコメント全て拝見し、真剣に回答させていただきます。
コメント