化学プラントのプロジェクトマネジメント(project management)で特に大事なことをトピックス的にまとめました。
化学プラントのオーナーエンジニアは日常の小規模改造工事などを通じてスキルを醸成していきますが、プロジェクトレベルの仕事をするときに必ずといっていいほど引っかかります。
1~2年程度の期間について大規模な情報をどうやって管理するか。
ある種のスキルと言えます。
世間一般には管理ツールの話にすぐに行きがちですが、その一歩手前の話です。
プロジェクトの見える化
プロジェクトを適切に処理するためには見える化がとても大事です。
頭の中だけで考えているのが一番良くない状態
若手にありがちです。
複雑な事象ほど構成する要素を分割整理するために、大分類で分割化していきましょう。
それを電子データ化して社内サーバーに保管しておけば誰でも見えます。
サーバーがない環境では紙で書いて掲示板として貼り付ければOK。
化学プラントのエンジニアリングで見える化しておくべき、大分類としての情報を紹介します。
プロジェクトのリソース
リソースとはここでは人のこと。
内部リソース・外部リソースと使い分けるでしょう。
内部リソースとしての社内エンジニア
オーナーエンジニアを持っている会社で、社内のエンジニアだけで概念設計ができる範囲のプロジェクトを考えます。
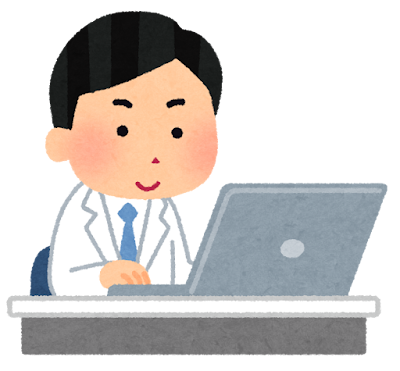
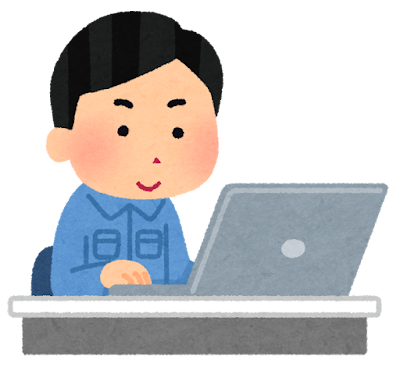
プロセス
機電系
同じ会社。謎の一体感!
見えない壁
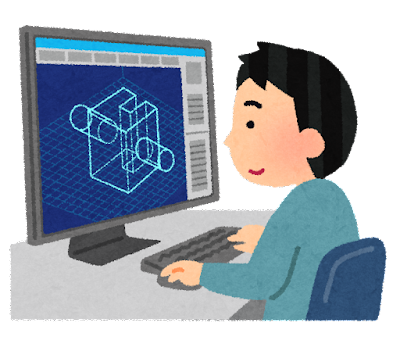
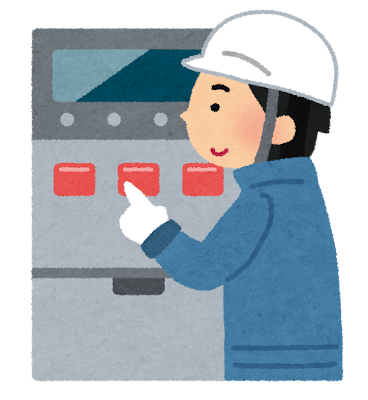
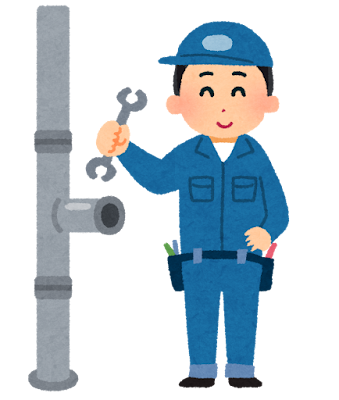
図面屋
設備メーカー
工事会社
全部違う会社
この場合は、ユーザーの機電系エンジニアは社内のプロセスエンジニアと同じ会社で、プロジェクトを一体感を持って進めていきます。
私のメインの仕事がここ。
図面屋・設備メーカー・工事会社などの外部リソースを活用しながら進めていきます。
外部リソースとしてのプラントエンジニアリング会社
外部プラントエンジニアリング会社を活用する場合のイメージはこんな感じです。
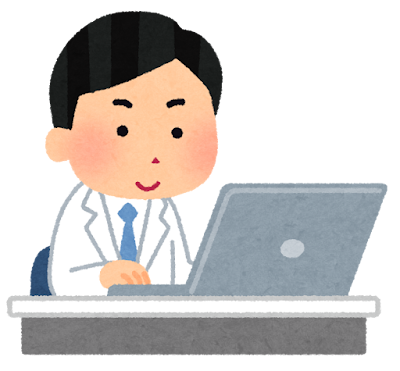
プロセス
見える壁
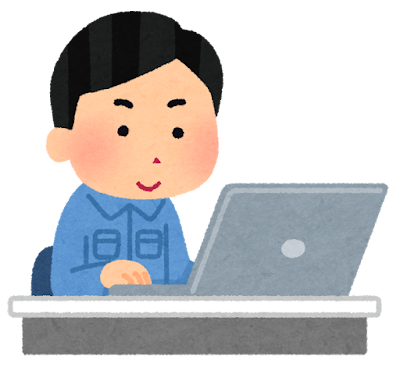
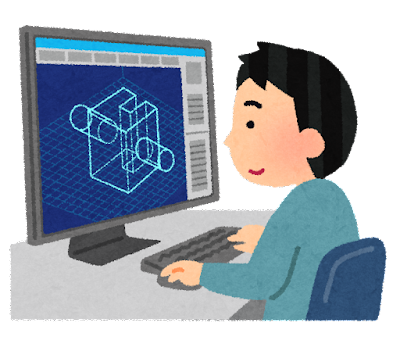
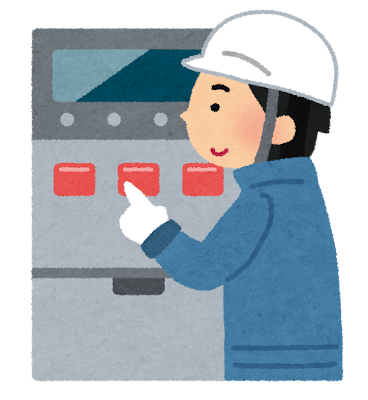
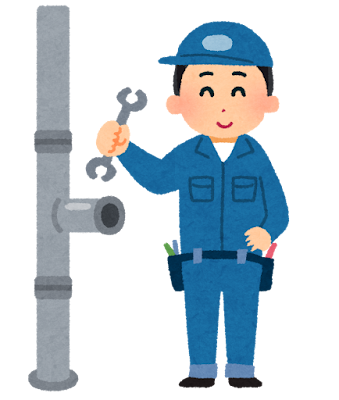
機電系
図面屋
設備メーカー
工事会社
機電系エンジニアだけが異動している格好ですね。
プロセスエンジニアを自社で持つか外部に依頼するかは会社の形態によって違うでしょう。
完全に製造を委託していて販売だけを行う会社から見たら、プロセスエンジニアも含めて外部リソースを頼ることになります。
化学プラントでは化学反応に関する技術を自社の占有技術として確保しておきたいので、プロセスエンジニアを外部に委託することは少ないと思います。
逆に、機電系エンジニアは相対的に需要ではないから外出しアウトソーシングが可能。
大規模なプロジェクトになると自社の機電系エンジニアだけでは数が足りないから、外部プラントエンジニアに依頼することになるでしょう。
何が大規模かは社内リソースで賄えるかどうかで決まります。
本質的には金額の問題ではありません。
プラントエンジニアリング会社の仕事を見ていると超ビックプロジェクトばかりにスコープが当たりがちですが、小さな仕事でも当然依頼しています。
図面屋
図面屋もリソースとして考えないといけません。
エンジニアなら取引の深い図面屋さんを確保していることが多いでしょう。
その図面屋さんだけで人数が足りるかどうかというのは、いつも悩みの種。
プロジェクトが決まるタイミングがどんどんギリギリになっていき、図面屋さんは仕事が絶えないように外部の仕事を行っている。
月ベースで仕事のあるなしを調整していかないといけません。
自社で抱える範囲内で図面屋さんが足りないから、外部プラントエンジニアに依頼するというケースも今後は増えてくるでしょう。
設備メーカー
設備メーカーは完全に外部リソースです。
外部リソースだから何もケアしないというわけにもいきません。
設備の大量発注に耐えれる設備メーカーが非常に少ないからです。
納期遅延・予算超過の可能性は高いので、着工前から大体の注文数量を伝えておいて設備メーカーとしても生産できる体制を整えていかないといけません。
この辺は調達部とやり取りすることになるでしょう。
施工会社
施工会社も図面屋とほぼ同じ扱いをすべきです。
内部リソースであって外部リソースでもある存在。
元請は確保できたとしても下請け孫請けクラスまで抑えようとすると結構なプランニングが必要です。
これも調達部の仕事であるべきです。ちゃんとしているかどうかは別問題ですが・・・。
設計管理
設計管理はエンジニアなら機器リストや計器リストの形で行うでしょう。
機器番号 | 材質 | 仕様 | ・・・ |
P-001 | FCD | 1m3/h×30m | ・・・ |
X-002 | SUS304 | 20m2 | ・・・ |
こんな感じですね。
当然だと思うでしょう。
でも、オーナーエンジニアでは、機器リストに重きを置いていない人が実際にいます。
というのも小規模工事なら機器リストなんてあってないようなものだから。
大規模工事なら設備の設計を一気に行えるわけでなければ、調達や工事設計も段階的に行うことになります。
各設備のステータスを表示したり期限や課題を残したりと、スプレッドシートはさまざまな活用ができる応用の高いツールです。
機器リストとして是非ともスプレッドシートを活用したいですね。
最近はDXで専用のシステムを導入する傾向があります。
機器リストもシステムの方が良いだろうと勘違いする人が多いですが、基本的には反対です。
スプレッドシートをどれだけ効率的に活用するかに注力するべきです。
ブラックボックスになったシステムに入力するだけのマシーンではなく、何の情報をどうやって整理するかという頭を使う訓練にもなります。
工程管理
プロジェクトの工程を管理するためには、既存のSDMに対する理解が欠かせません。
何もない更地からプラントだけでなく事務所・原料・廃棄物などの工場に必要な施設一式を建てる機会なんてそうそうありません。
既存プラントの一部を改造する場合には、SDMに対する理解が絶対に必要です。
化学プラントではSDM(定期修理)は2パターンに分けることができます。集約型と分散型です。
集約型SDM
一般的にイメージするのは集約型です。
下の図は、3つの工場(A、B、C)の一年間の生産スケジュールです。
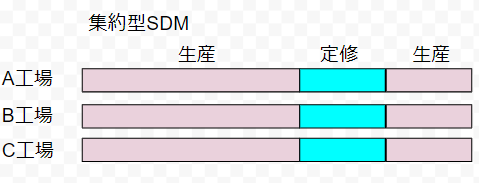
事業所内にあるプラントをすべて停止して、一度にSDM(定期修理)を行います。
SDMの語源であるShut Down Maintenanceという言葉どおり、工場全体をシャットダウン
工場萌えとして夜の工場のライトアップを見る機会はあるかもしれませんが、シャットダウンをすると逆に廃墟のような状態になります。
電気も止めますので ^^
集約型SDMに対するエンジニアリングのタイムスケジュールを見てみましょう。
集約型のSDMなので、エンジニアリングも集約されます。
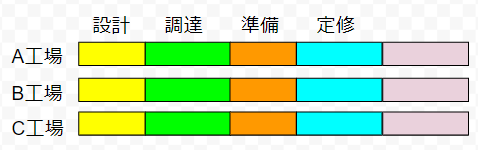
集約度が高い工場ほど、エンジニアリング業務が集約されます。
工事会社の作業員が集約されるだけでなく、プラントエンジニアも集約されます。
一点集中できるというメリットがあるので、マネージャーもプレイヤーも仕事としては分かりやすいです。
分散型SDM
集約型の反対は分散型です。
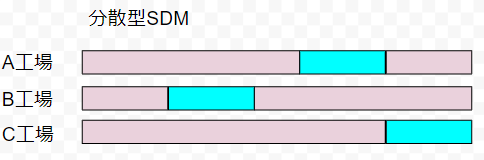
SDM期間が工場ごとにバラバラです。
分散型SDMが可能なのは、ユーティリティが分散化されている工場に限定されます。
分散型SDMに対するエンジニアリングのタイムスケジュールを見てみましょう。
分散型だと下のとおり、バラバラになります。
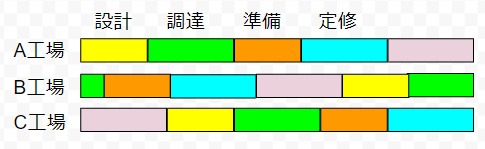
分散型で1人の担当者が3つくらいのプラントを担当することは、ごく普通のことです。
上の例では、A工場が定修の時にB工場向けの設計をしつつC工場向けの準備をするという仕事の切り替えが必要です。
これは、コンカレントエンジニアリングの発想そのものです。
集約型に慣れてしまうと、分散型への対応はかなり難しいです。
頭の中で仕事の切り替えを器用にしないといけないからです。
連続プラントのエンジニアリング担当者がバッチプラントでエンジニアリングを器用に回せない
という声をよく聞きますが、私はこの分散型SDMが1つの要因だと思います。
その意味で、最初から分散型SDMに対応しているプラントエンジニアは強いと思います。
工事時期の設計
化学プラントでプラント建屋の増設は、非常に大きなプロジェクトとして扱います。
5年に1回くらいあれば十分という頻度です。
これくらいの規模だと外部プラントエンジニアに依頼しようとするかも知れませんね。
頻度が少ないけど、投資額が大きく、失敗が許されません。
設計期間を十分に取り、慎重に検討をします。
日常的に行う設備更新以下の単純な業務とは違います。
土建工事を分割
化学プラントの工程設計をする場合、土建工事を分割させることは知恵の1つです。
バッチプラントの場合はプロジェクト着工後、1回目のSDMでプロジェクト工事ができるケースはあまり多くはありません。
というのもSDMが1年に1回行うとして、プロジェクトは2年に渡ることが普通だから、
1年目のSDMで工事の一部を先出しして行うことが考えられます。
その候補が土建工事。
土建工事は化学プラントの工事の30~50%を占めます。
土建工事を分割することは、配線や配管のレイアウトを考えて工事効率化を図るよりも圧倒的に効果的です。
2年目の本格SDMでは配管や配線などのメイン工事に注力できます。時間的な余裕も取れます。
戦略的に土建工事を分割する案を考えます。
- 機器の荷重を受ける梁を先行して工事する
- 機器の荷重を受けるコンクリート基礎を予め工事する
これらを実現するためには、機器の仕様が決まっていないといけません。
ローディングデータという荷重情報が「ある程度」確定していないといけません。
そのためにはプロセス設計・設備詳細設計を優先して行い、設備メーカーを確定させてる必要がありますね。
プロジェクトの初期に何を行うか、という優先順位設定に大きく左右します。
工事エリアを分割
化学プラントで工事エリアを分割する方法も有力です。
危険物製造所の仮使用申請を行えば、工事をしている部分以外の部分を生産活動に使うことが可能です。
適切な火気養生をして、
- 生産活動で発生する可燃性ガスが工事現場に到達せず
- 工事現場の生火が生産エリアに到達しない
という環境を構築することが重要です。
こうすれば、既設のプラントといえども工事期間をかなり自由に設定することができます。
建屋増設のケースがメジャーな例です。
建屋増設とは以下のような、既存工場の一部分を延長するような工事です。
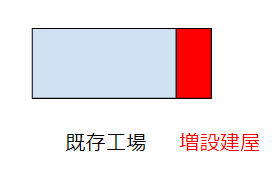
既存工場の能力増強が主な目的ですね。
運転中プラントへの影響を無くす
建屋増設が運転プラントへの影響を無くすことが第一です。
イメージは以下のとおり。
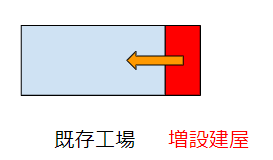
プラント建設するけど、現在運転しているプラントに迷惑を掛けない。
この思想で対応を考えないといけません。
- 工事火花が飛び入らない 防炎シート
- 作業員が運転中プラントに入らない 動線の確保
- 資器材がプラントに影響しない 資材置き場の確保・車両やドラム缶の運搬ルート確保
- 用役を止めない SDM時にバルブ切込み
プロジェクト初期段階から用役の縁切りのタイミングはしっかり考えましょう。
他の対策はある程度は柔軟に対応できますが、用役だけは工場の停止に関わるのでとても大事です。
運転中プラントからの影響を無くす
運転プラントへの影響と逆で、運転プラントからの影響も考えないといけません。
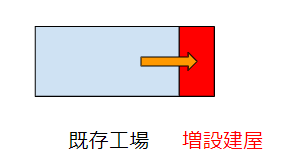
- 廃油が侵入しない ガス検の常時携帯
- 排水が侵入しない 土のうによる遮断
生産に伴って発生する廃油排水がいつのまにか、生火を扱う工事現場に侵入していて火災が起きたとなればシャレになりません。
平行して工事をする場合には、いつも以上に気を使って運転しなければいけませんね。
機器の取合配管図は後回し
機器の取合配管図は後回しにするという発想です。
配管図は以下の順番に行うのが普通です。
- ステップ1機器の仕様を決める
設備メーカーに発注
- ステップ2機器周りの配管設計
設備メーカーの機器図が必要
- ステップ3設備道中の配管設計
配管ルート確保が課題
これが普通です。
ところが近年では、機器の仕様を決めきれないで配管図を書き始めないと工事期間を確保できないケースがあります。
- 設計期間が確保できない
- 設備メーカーの納期が長期化している
- 図面屋さんが確保できない
- 施工会社の作業員の確保に時間がかかる。
こんなにたくさんの不確定要素がある時のために、配管設計としてできることはフランジの切込み。
これ1つで実は解決できます。
図面がない機器周りの設計ではフランジを切り込んでおき、図面が確定した後でいくらでも配管の対応ができます。
この辺は極めてシンプルな発想ですが、この考え方をエンジニアと図面屋が共有していないと
「機器図面が提示されるまで配管図を書かない」というような杓子定規な仕事の仕方をする図面屋がでてきます。
コンカレントエンジニアリングとは真逆の発想ですね。
- ステップ1機器周りの配管設計
フランジを切り込んで適当にかわす
- ステップ2設備道中の配管設計
配管ルート確保が課題
- ステップ3機器の仕様を決める
設備メーカーに発注
図面屋としては設備導入の配管設計という最大の課題に集中できるようになります。
既存プラントだと配管が多すぎて、通すルートを考えるのがとても難しいですからね。
予算管理
プロジェクトでは予算管理も大事です。お金は大事。当然です。
家計簿なら毎月定期的にチェックすれば良いでしょう。
小規模工事でも同じ考え方で行います。
ユーザーエンジが行う程度の大規模工事なら、もうすこしざっくりと段階を分けて管理します。
- ステップ1機器の発注が終わった段階
機器の費用はみんなが注目している
- ステップ2工事の発注が終わった段階
工事の費用は大抵予算を越える
- ステップ3工事が完成した段階
現場調整などの実費精算
- ステップ4試製造の段階
突貫工事で発生した費用
これらの費用を段階的に整理します。
機器の発注
機器の発注が終わった段階で予算を整理しましょう。
機器の単価は機電系エンジニアだけでなくプロセスエンジニアや経理も興味を持ちます。
というのもラング係数法に大きく効くから。
設備が高騰しているかどうかをチェックできる絶好のタイミングです。
次の設備投資に活かすためにも、発注が決まった段階で情報を共有したいですね。
工事の発注
工事の発注が終わった段階で予算を整理しましょう。
工事の発注が終わった段階で、着工予算の大半を使い切るはずです。
この段階で予算内に収まっていることが絶対条件です。
現地工事や試製造で発生するトラブルに対する追加費用にどれだけ割り当てができるか、実態を把握して安心感を得ることが目的です。
常日頃お金が動いていくので、今どれだけ使っているか分かりにくいのがプロジェクトの特徴。
工事の発注が終わった段階でちゃんと締めておきたいですね。
この段階で、現地工事での追加工事がどれだけ発生するか何となく予想するのも予算管理の1つ。
工事エンジニアで経験を積めば、それなりの精度で見積ができるでしょう。
工事の完成
工事が完成した段階で予算をまとめましょう。
工事が完成して安心し切ったり、試製造に意識が行きがちですが、予算も大事。
施工会社とコミュニケーションを良く取って、実態の把握に努めましょう。
工事前に予想した額と大きく差があるかどうかがポイントです。
試製造
試製造が終わった段階で予算をまとめましょう。
と言ってもここで過剰な意識をするケースは少ないでしょう。
トラブル解決に全力を費やしがちでお金のことは後回しにしがちだし、仮にお金が足りなくても補修予算等から割り当てようという腹積もりもできるからです。
最悪の手段であってできればしたくないですけどね。
というより、この最悪の手段にもっていかないことを確認するために、各段階での予算整理があると言っても良いでしょう。
参考
関連記事
最後に
化学プラントのプロジェクトマネジメントで特に大事なことについて紹介しました。
プロジェクトは数が最大の課題です。頭の中だけで考えずしっかり見えるかしましょう。
リソース・設計・工期・予算の4つは最低でもはっきりさせます。
化学プラントの設計・保全・運転などの悩みや疑問・質問などご自由にコメント欄に投稿してください。(コメント欄はこの記事の最下部です。)
*いただいたコメント全て拝見し、真剣に回答させていただきます。
コメント