化学プラントでは頻繁にプロジェクトマネジメントと称した増改築を行います。
ここで機電系エンジニアも大活躍します。
社内でプロジェクトを渡り歩いた人もいるでしょう。
外部プラントエンジニアリング会社に近く、自社のプロジェクトばかりを担当。
その代わりに日常の改造やメンテナンスなどの運営は担当できなかったという人。
私のような人ですね。
プロジェクトを経験すれば人は成長すると言われます。
化学プラントではそれくらい大事なイベント。
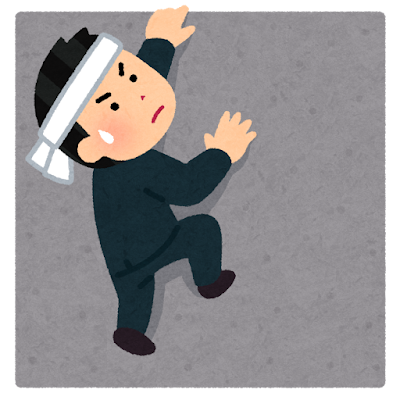
精神論
プロジェクトは長期間にわたる仕事です。
運転や保全がその日その日を繋いでいく仕事であるのに対して、
プロジェクトはその日を積み重ねていく仕事。
思考やメンタル面で違いが出てきます。
運転や保全はどちらかというと体力勝負。
プロジェクトはどちらかというと精神勝負。
多くの問題が起こり、プレッシャーも強いですが、問題は絶対に解決しないといけない立場です。
プレッシャーに負けそうになる人も多くいます。
プロジェクトを処理するためには、各種教育が大事ですが、その中でも精神論が意外と大事です。
ポイントと心構え
プロジェクトのポイントと心構えについて説明します。
現象の理論的解析
化学プラントのプロジェクトなので、化学反応が中心的な存在です。
化学反応に対する現象の理解や理論的な解析が大事であることは、いうまでもありません。
これは研究部門に対する心構えであり、運転部門ではあまり必要とされていません。
エッセンスだけを理解していれば十分です。
最低限の範囲では、高校の化学程度の知識があれば十分です。
私でもやり過ごすことができたくらいですので ^ ^
スケールファクターの理解
これも研究部門やプロセス開発の部門の課題です。
フラスコレベルとプラントレベルでスケールが違います。
スケールとは寸法と読み替えても良いでしょう。
距離の1乗で効くファクター、2乗で効くファクター、3乗で効くファクター
いろいろあります。
フラスコレベルではこれらのバランスがたまたま一致していたが、実機レベルでは距離のファクターが強くて、運転ができなかった。
という例もわずかですが存在します。
例えば、3乗で効くファクターとしての化学反応の発熱量に対して、冷却能力は距離の2乗で効いてきます。
装置が大きければ大きいほど、冷却能力が弱くなっていくので、
例えば反応時間を延ばすなどの対応をしないといけないでしょう。
その結果、歩留まり・収率が低下する方向に移ることもあります。
スケールファクターをかっこよくいうと時間と空間の差
スケールファクターは色々な要素が考えられますので、予想外のことも起こりえます。
経済性
プロジェクトでは必ず問題になる課題です。
- 生産原価・売価
- 固定費・変動費
- 投資額
いろいろな経済性を考えないといけません。
研究に無制限に投資ができた時代がベースとなった課題であり、
今では経済性は当然の課題なので、シビアに考えすぎる必要はないかもしれません。
人間関係
これはプロジェクトの最大の課題。
異なる立場・考え方の人間が集まってプロジェクトを実施します。
ここでは共通認識を持つことと、意見の対立を認めることが大事。
これが意外と難しい。
初心者は周囲の人全員の立場を知らないので控えめな行動をしますが、
ある程度慣れてくると周囲の人の無理解にいら立ちを起こします。
その時期を過ぎると、悟りの境地に達していらだちも消えてきます。
プロジェクトを推進する立場・プロジェクトに協力する立場
それぞれの立場を認識して、役割を担うというロールプレイングが求められます。
その意味で「演技」そのもの。
基本設計
これは化学プラントに限らず、重要でしょう。
法規、プロセスフロー、配置、材質、製法などを基本設計段階で明確にしておかないと、
後で変更する場合にはコストや納期のインパクトが膨大になります。
これを担当するプロセス屋の責任はかなり重たいですね。
設計の高度化
基本設計から工事設計資料を作るための部隊が、工場の設備エンジニア
ここでは新たな技術を行使するというよりも、既存の多くの技術を効率的に高速で処理することが求められます。
研究とエンジニアリングを分けているのは、この辺りの話だと思っています。
膨大な量に対して、最速で最適な解を見出すための取り組み
これが建設設計段階では重要です。
教科書のみでは習得できず、経験が必要という意味で精神論。
どこの会社でも課題になっているでしょう。
工事安全
ここはプラントエンジニアや保全担当者の範囲です。
工事に関する安全・資器材の手配・スケジュールの管理などが大事です。
同じ工場で一定の経験年数を持った人が対応すれば、だいたいは上手いこと進みます。
難易度的には低めですが、経験年数が必要となる分野です。
しぶとく経験するという意味で、精神論でしょう。
試運転
試運転には①機器の単体試運転や水運転などと、②実液運転に分かれます。
①は一般的なマニュアルと数回の経験で、それなりの対応ができます。
難しいのは②。
プロセスによって千差万別の結果が出るだけでなく、
プロジェクトに関わる全ての人の精度によって、問題の発生量が変わります。
ある意味、運です。
会社の組織の中で、有力なリソースを投入できたかどうか。
これが重要となる世界です。
こうなると精神論以外の何物でもないでしょう。
哲学
プロジェクトの哲学について解説します。
哲学というと古臭く見えますので、心構えの方が適切かもしれません。
この辺こそがプロジェクトでは大事ですが、年々薄まっていっています。
論理を重視する
化学は科学の一分野なので当然論理がありそうに見えます。
そこにあるのは、論理ではなくて理論ですね。
この理論も数学や物理に比べれば不十分。
化学工学のような実学は近似式の嵐であり、そこに理論での肉付けを多少できるという程度です。
こういう環境にあると、以下の発想が生まれがちです
- 現実こういう反応が起こっているから仕方ない
- 良く分からないから超安全側の対応をする
- 駄目だったらその時に考える
理系の技術集団とは思えない、発言が出てきます。
理論はおろか、論理すらない…。
化学プラントのプロジェクトでは論理的に行わずに、感情的・刹那的に処理していることが多いのでしょう。
だからこそ、40年前から「論理」を強調しています。
プロジェクト計画に論理を
プロジェクト計画に論理は必須です。
- 予算としてこの額が必要な理由
- この時期に投資が必要な理由
- 現在判明している主要課題
- 投資の結果、得られるメリット
プロジェクトの初期には、分からないことだらけです。
その状態でも前に進めるためには、課題の明確化が大事。
プロジェクトでは特に予算確保が問題となります。
課題が不明確な状態でも予算を確保しにいかないといけません。
そのためには、上記のような論理をしっかり練ることが大事です。
基本設計に論理を
基本設計がしっかり決まっていないと、後の工程全てが振り動かされます。
- 何となく必要だから
- 要らないかもしれないけど、念のため
- とりあえず今の設備と同じモノも増設
これくらいの理由しかなくても、設備投資をする部分があります。
そういう設備はたいていが失敗します。
大きなケガには至らなくても、「もうちょっとこうしていれば良かった」というレベルです。
こういう結果は、後の設備投資が非常に難しいです。
明らかに駄目な設備であれば、理由は立ちます。
設備投資に対するメリットが説明できるから。
微妙に駄目な設備であれば、費用対効果が低く優先度を落とされます。
一回のプロジェクトなら気にならないレベルですが、こういう微妙な設備が積み重なると、駄目な工場となります。
配管設計に論理
配管設計はエンジニアリング的要素が強いから論理がありそうに見えます。
ところが、大半の配管設計はとりあえず空いている所を通すという残念な設計です。
- プラントの将来的用途
- 切替配管などの作業性
- 適切な配管ルートの探索
一度配管を通してしまっても、後で改造が簡単だから適当に施工する。
という積み重ねが一般に行われます。
それが、二重投資という結果になります。
予算感覚を持つ
プロジェクトであれば、予算が大事であることは言うまでもありません。
ここでは予算に対する考え方を紹介します。
応急的投資は意味がない
設備投資をするときに、「とりあえず現状を解決」という思考が増えていくと
判断はかんたんですが、投資額は増えていきます。
応急的投資は守備的な投資です。
会社である以上は攻撃的な投資が必要。
応急的投資の方が緊急度が高くプロジェクト感はでますが、それは勘違い。
原因を解析し本質的な対策をするために、時間を掛ける投資こそが攻撃的な投資。
「とりあえず」「急いでいるから」
こういう表現が頻発している会社はジリ貧になります。
投資をケチらない
投資額を膨大に積み上げる人は残念ながらいます。
その逆に徹底的にケチる人がいます。
設備投資はminが良いという風潮が強い会社ほど、危険度が高いです。
- 更新が必要な設備なのに、投資しない
- 転用できるか調べていないのに、転用を決める
- 工事費が暴投しているのに、無視をする
こういう判断をすると、後で痛い目を見る場合があります。
この辺は本当にバランス感覚や運の問題。
特に設備投資の延期や転用は。結果として良い判断だったというパターンの方が多いです。
分割投資
投資額をminにするという時に考えるのが分割投資。
「100の投資が必要な時に、1年目に70を投資して、2年目に30を投資する」というような考え方です。
化学プラントのプロジェクトでは、設備発注と工事発注とに分割することが多いです。
設備発注と工事発注の間に、1年以上の差があることも多いです。
一括で投資額を配賦するよりは、分割投資する方が経理的にも助かります。
上の項目で上げた「転用」もこの範囲。
- 新製品導入に伴い、設備購入が必要なプロジェクトだった。
- お金がなかったので、設備は使いまわすことにした。
- 新製品導入後、1年でその設備が壊れた。
- 新しい設備を購入した。
これは二重投資ではありませんよね。
1年間持ったという実績もあります。
結果として分割投資になっています。
この壊れた設備を購入するための予算申請時には、上で述べたような論理が必要です。
壊れたから更新する!だけでは不十分ということですね。
新技術を取り入れる
プロジェクトでは何か新しいことを必ず1つは取り入れろ
こういう言い方をします。
化学プラント向けの設備はこの30年くらい何も進歩していないのに、何を取り入れよう・・・。
そう考える機械エンジニアは多いです。
ですが、対外的に発信する効果は低くても、新しいことはいっぱいあります。
- 海外の設備を導入した
- 工期を短縮するために、分割工事を行った
- 資材調達の方法を見直した
1や2は対外発信できる部分もあります。
3は難しいですが、それでも自身の中では新しいこととして認知していいと思います。
プロセス
化学プラントのプロジェクトでは化学プロセスは当然大事です。
プロセスの優劣が全て
化学プラントのプロジェクトでは「プロセス」が全てを決めます。
改めて言うこともないかも知れませんが、大事なことです。
プロセスが大事
この考え方は特に連続プラントで如実に現れます。
というのも、連続プラントの反応はシンプルだから。
ほぼ反応条件が決まっていて、それをどれだけ安いコストで建設するか・運転するかで、競争力が決まります。
日本で作るべきなのか、もっと安価な国で作るべきなのか。
そういう厳しい戦いをします。
一方、バッチプラントはそこまでの勝負はしません。
「競争相手が少ない」プロセスが多いからですね。
とはいえ、暢気に構えてもいられません。
ジェネリックとの闘いがあるからですね。
いずれにしろ、どんなプロセスにするかは化学プラントのプロジェクトを左右します。
「製造業における製法」という意味で、製造業全体に展開できる話です ^^
反応系の動特性を把握
化学プラントではプロセスの中でも反応が特に重要です。
化学反応という加工法を使ってモノを作るからですね。
反応の動特性とは以下のようなものを言います。
- 物質移動・熱移動の大きいもの
- 活性化エネルギーが大きいもの
- 長時間放置したときに影響が大きいもの
- 反応マスの状態が変わるもの
反応の動特性とは、反応によって動く特性のことです。
反応によって物質が変わる・熱が変わる・物性が変わる…
物理の動特性のような表現とは、意味が異なりますので、若干の注意が必要です。
物性を把握
プロセスの動特性とほぼ同義に見えますが、物性も大事です。
機械エンジニア的にはこの2つが特に大事。
- 密度
- 粘度
もっと端的に「密度」に限定しても良いでしょう。
- 撹拌動力
- ポンプ動力
- タンクの強度
- 液面計
- 流量計
いろいろな検討事項に、密度が直結するからです。
プロセス面で重要になる物性として、以下があります。
- pH
- 腐食性
- 熱安定性
- 安全衛生関連
- 環境処理関連
安全衛生や環境処理はかなりざっくりした表現ですが、ここにはいろいろな情報が含まれます。
安全衛生や環境処理は、プロセスというより研究段階で調べつくすものであり、
そのうち問題になるものだけが工場に上がってくると考えて良いでしょう。
物質収支を把握
これはプロセスの中でも、重要度は極めて高いです。
反応で発生した不純物がどこにどういう形で逃げるのか
これを追いかけることが物質収支と言っても良いです。
不純物の量を極小化し、収率を向上させれば、コストに直結します。
これはバッチでも連続でも同じくらい重視します。
個々の単位操作の目的を明確に
プロセスに含まれる個々の単位操作がなぜ必要かを明確にしないといけません。
昔のプロセスでは、何となくバッファのためにタンクを置いているという場合もあります。
こういうタンクやポンプなどは本来不要なのに、生産に使用してコストとなります。
プロジェクトで新規購入する場合は、投資コストに直結します。
最近では、単位操作を極小化するために、目的は明確化されています。
昔はひどかったと考えればいいです。
フローシート
化学プラントではフローシートはプロセス条件に次いで大事です。
機電系エンジニアとしては影響範囲が大きいのでこれも解説しましょう。
プロセスの動特性を考えた計装設計
プロセスの動特性を考えた計装設計が必要です。
反応の動特性とは違います。
バッチ系化学プラントでよくあるプロセスの動特性はこちら
- 常圧と真空の両方の圧力を測りたい
- 液量が少ない時の温度を測りたい
- 液を送っている間の液面を測りたい
常圧と真空の圧力
真空の圧力計は一般に、常圧では測定できません。
バッチ運転で常圧と真空を繰り返し運転する場合は、「常圧は常圧・真空は真空」として圧力を測定したいです。
真空引きするときの条件、真空ブレークの条件を測定するためですね。
こうしたときに、圧力計を2つ(常圧用、真空用)を準備しないと失敗します。
液量が少ない時の温度
バッチ運転では反応器に液量を入れます。
反応器内の温度測定は、邪魔板に温度計を設置することが一般的です。
反応器で取り扱う液量が少ない場合、邪魔板に液がつからずに、温度が測定できないときがあります。
第一弾の投入液量が少なく、第二弾で液を薄めるという場合です。
この第一弾の液が危険なものである場合は、液を受け入れた時に温度をすぐに測りたいということもあります。
反応器底のピストン弁に温度計を付けるというような、やや特殊な対応が必要となります。
液を送っている時の液面
差圧式液面計を使う場合の注意点です。
差圧式液面計では、液を受けれていたり払い出したりしている時は、測定がうまくできません。
バッチ運転のように、液の受け入れが一時的に行われる場合は、受け入れが測定値の変動要因になります。
機器の転用は要注意
プロジェクトで機器を転用する場合は、特に注意が必要です。
機器を新規購入する側は、あまり問題になりません。
- 微妙に改造をしていたが、図面に反映されていない
- 大きな補修をしていたが、チェックしていない
- シール部の耐食性をチェックしていない
いろいろな問題が起こりえます。
古い設備を転用するときほど、注意が必要です。
図面を信じていてはいけないという現場主義的なエンジニアが発生します。
改造や補修なら、さすがに図面に修正することも考えるでしょう。
シール部の耐食性など、細かい点は見落としがちです。
FKM問題としてバッチでは有名です。
FKMで使えない薬液が増えているけど、既存設備はFKMが多いという問題です。
竜頭蛇尾にならないこと
竜頭蛇尾とは「初めは勢いが盛んで、終わりはふるわないこと」です。
フローシートを作る最初の段階では、やる気も高く必死に検討します。
ところが一度修正図面が上がってくる頃にはどうでもいいという状態になります。
これは非常に多いです。
メーカーの図面でも同じです。
最近のメーカーはこれをわざと使ってるとしか思えない対応をしてきます。
- 図面の指摘
- 修正に2か月かける
- 時間がないので承認
この手を使うメーカーとの付き合いは避けた方が賢明です。
仕事上で精神衛生に有害となります。
そんなメーカーは日本に山というほどありますよ。
ヘッド送液に注意
ヘッド送液は、自重落下しかエネルギーがありません。
自重落下でも十分に液を送れるように思えます。
雨を見ていれば分かりますよね。
水が天から降ってきて、避けることはできませんからね。
こういう開放系なら問題はありません。
問題は閉鎖系。つまり配管内にある液体です。
これは開放系とは性質が異なります。
- 配管が長すぎて摩擦損失がある
- 液が確実にたまってしまう
- ガスが抜けない
こうしたトラブルにより、液が流せなくなることがあります。
ポンプなら高い圧力で強引に送ってしまうことができますが、ヘッド送液なら配管高さ分しか圧力を取れないですから。
5m~10m分の液注圧力しかなく、それ以上に高い圧力を増やせません。
マテハンを軽視しない
マテハンも軽視してはいけません。
マテハンとはマテリアルハンドリングのことです。
化学プラントでは、原料の仕込み・サンプリング・製品や廃棄物の充填などの人の作業のことをマテハンと言います。
フローシートではマテハンが見えにくいです。
フローシート作成段階では竜頭蛇尾になりやすく、マテハンが目立たない段階です。
ここでマテハンを考えずに、プロジェクト後半になって考えだして、どうしようもない状態になり、マテハン作業性が悪い設備となることが、非常に多いです。
レイアウト
化学プラントのまさにエンジニアリングの部分では、レイアウトは非常に大事です。
直近のことだけを考えずに、将来のことまで考えないといけない点が特に課題。
人の作業性はレイアウトで決まる
化学プラントの作業員の作業性はレイアウトでほぼ決まります。
安全性のレイアウト
作業性という意味でのレイアウトは、真っ先に下記のような課題があります。
- 作業ルートはシンプルで真っ直ぐに
- 作業ルートに行き止まりを作らない
- 作業ルートの幅を確保する
この辺は古典的で原則的なレイアウト課題です。
作業性というよりは、安全性という方が正しいです。
昔は、「これらの課題さえ確保していれば、安全性は確保できる」と言われていました。
現在は、これだけでは不十分です。
何もない通路やありきたりな街中でも、転倒などの問題が起きています。
今では、人間の歩き方にまで視点を向けて、安全性を考えるようになっています。
作業性のレイアウト
作業性の中でも、レイアウト上はまずはマテハン以外に注目されます。
- 反応器の配管ヘッダーの操作性
- ポンプでの操作性。特に分液作業
- 切替配管の作業性
- 流量計の視認性
- サンプリング場所の確保
いろいろな作業性がレイアウトに左右されます。
これらの作業性のうち、重要なものを以下に紹介します。
平面図だけでなく立面図も重要
平面図だけでなくて立面図も重要です。
レイアウト検討上は平面図で議論することが多いですが、立面情報を無視して議論になりがちです。
- 反応器の入槽作業がしやすいか
- 反応器の上部配管ヘッダーに手が届くか
- 反応器の下部配管の切り離しができるか
- 反応器の下部に人が通るスペースがあるか
反応器1つをとっても、建築物と反応器との高さ関係で、作業性は大きく変わります。
これは立面図を見ないと分からない事項です。
反応器よりも、ろ過・乾燥系列の方が遥かにシビアな建屋設計が求められます。
こういった場所で建屋高さをシビアに決めた結果が、後のマテハン作業の障害になります。
現場をよく確認する
レイアウト検討は現場が大事です。
レイアウト検討を平面図だけで行うと、思わぬ見落としがあります。
というのも平面図にはすべての現場情報が記載されているわけではないからです。
思わぬ配管・ラック・柱・梁などが存在します。
現場を見て、こういう障害物の位置関係を抑えて、図面上に記載して検討するのが、レイアウト検討の基本です。
最近では、写真やカメラの性能が上がり、現場を見なくてもかなりの割合を検討できます。
現場は「最後の頼みの綱」という位置づけで考えても良いでしょう。
調整弁・スイッチが場所を取る
調整弁やスイッチは意外と場所を取ります。
調整弁やスイッチ自体がスペースを取るわけではありません。
それらの設備にアクセスするための作業スペースが必要です。
作業通路として最低でも60㎝は求められます。
調整弁やスイッチの作業面に対して、60㎝の空間を確保しないといけません。
そこには設備や配管を通すことはできません。
これがレイアウトの制約となります。
マテハンをよく考える
マテハンはレイアウトに直結するため、よく考えないといけません。
マテハンでも原料の仕込み・製品の充填などの作業は、立面図での検討となります。
これらのマテハンは特に高い作業場が重要です。
レイアウトが良くないと、階段の上がり下がりが増えるという問題が起きます。
現在のプラントでは、階段の数も極小化しています。
昔のプラントは、1つの階でも途中に階段が設けている場合が多いです。
設備の設置高さをランダムに設定して設備同士を階段でつないで建築物とする、という構図が多いからです。
「設備 → 建築物」という順番に考えた設計が多かったです。
今では逆ですね。
「建築物 → 設備」の準で考えます。
この目で、古いプラントを見てみると階段の多さに目が行くと思います。
試運転
プロジェクトの最後は試運転で終わります。
終わりよければすべてよし。
試運転ポイントを説明しましょう。
用意周到な準備
試運転では用意周到な準備が必要です。
大きなステージとして以下の4つくらいに分類されます。
- 工事
- 機器試運転
- 水運転
- 試運転
プロジェクトでいう試運転は「4」のことを言います。
プラントエンジニアは「1」の工事でほぼ終わり、「2」の機器試運転が儀式的な扱いになっているでしょう。
製造部は「4」の試運転からが本番。
「1」の工事が終わってから、すぐに「4」の試運転を行うわけでなく、
「2」の機器試運転や「3」の水運転という入念な準備を行います。
その後、遮断板の抜き差し・バルブの開閉・計器の調整などの準備を徹底的に確認してから、試運転に掛かります。
「3」の水運転が終わったら、すぐに「4」の試運転に掛かると失敗します。
ここで、慌ててはかえって遠回りになります。
チームで協力する
試運転はチームで協力する必要があります。
バッチ系化学プラントでは少なくても2週間~1か月程度の仕事になります。
1日に2交代で回すとしても、チーム体制は必要です。
徹夜で仕事をしても、思考力が落ちてバテてしまい、良いことはありません。
18時間くらい計器室にいると、眠たくなってしまいます。
水運転でトラブルを潰す
「3」の水運転で次元の低いトラブルは潰すべきです。
もっと言うと、手前の工程で潰すものは潰すべきです。
「1」工事の気密試験で漏れを潰す。配管チェックで配管間違いを潰す。
「2」の機器単体試運転で、機器に問題がないことを確認する。
「3」の水運転で、計器調整・自動運転の基本シーケンス・異物がないことを確認する。
「4」の試運転で、運転条件の最適化を行う
「4」の試運転では、反応条件に特化した調整を行うべきであり、「3」の水運転までで発覚するトラブルを全て解決すべきです。
トラブルに対応できる人材
トラブルに対応できる人材が大事です。
「原因を的確に見つける目や判断力」とも言えます。
情報が不確定な状況でも、決断を求められます。
これは勘と思考と度胸のお話。
一朝一夕で身に付くものではありませんが、大事なことです。
むやみに工事をしない
「3」や「4」の段階で、むやみに工事をしてはいけません。
何か問題が起きた時に良く分からないけど、ある改造をしよう!
という圧力が働きがちです。
これで改造してしまったがゆえに、かえって失敗することもあります。
工事前に色々な人が知恵を出して工事したラインを、試運転中の想いつきで改造してしまうと、プラント全体がカオスな環境に移行する側に移ります。
製造部の課長の権力が強い組織ほど、こういう風潮になります。
試運転で問題が起きた時には、その原因を徹底して調べることが大事です。
仮に工事をしないといけない場合でも、現場で調整しやすいような工事を行って、トライアンドエラーがしやすいような設備にすべきです。
気になるところは放置しない
試運転では気になることは放置してはいけません。
少しでも気になったことは、関係者で議論して解決します。
誰か1人に責任を押し付けるわけではありません。
責任はすべて管理職にあります。
気になっても議論もせずに、放置していることが問題です。
参考
関連記事
最後に
化学プラントのプロジェクトのポイントをまとめました。
哲学・心構え・プロセス・フローシート・レイアウト・試運転
機電系エンジニアはフローシートやレイアウトで関わることが多いですが、全体を俯瞰してみたいですね。
そうしなければ試運転で結局痛い目を見ます。
化学プラントの設計・保全・運転などの悩みや疑問・質問などご自由にコメント欄に投稿してください。(コメント欄はこの記事の最下部です。)
*いただいたコメント全て拝見し、真剣に回答させていただきます。
コメント