タンクのノズルオリエンテーションについて解説します。
ノズルオリエンテーションは、タンク設計の中でも相当複雑な部類にあります。
タンクの容量を決めて板厚を決めるまでが限界で、ノズルオリエンテーションは後回しにしてスケルトンを書いてとにかく発注!
っていうパターンは非常に多いです。
この結果、メーカーから図面が来た時になって悩み、既設と同じ配置にしたり配管の繋ぎこみだけを考えて決定したりする展開になります。
でも、本来はこれではダメ。
機械設計の立場でノズルのオリエンテーションの主要な制約条件を決めたうえで、機器製作の都合や配管レイアウトの都合を織り込む、という形にしたいものです。
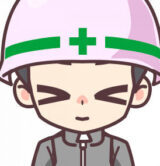
ノズルは優先順位を決めて設計可能です!
タンクのノズルに影響を受ける設計要素
タンクのノズルを設計変数としたときに、影響を受ける設計要素をまとめました。
ノズルオリエンテーションを考える場合の基本として理解しておきましょう。
作業性
ノズルによって影響を受ける最大の要素は、作業性です。
- 現場での運転作業
- 工事作業
2つの側面で考えます。
最近の機電系エンジニアの中には現場での作業よりも工事作業を優先する傾向があります。
オーナーエンジニアなら現場での作業を優先させたいものですね。
コスト
ノズルはコストに影響を与えます。
ノズルが増えるとコストアップしますね。
当たり前ですが大事なこと。
- 1つノズルを追加してプロジェクトの予算範囲内に収まるのか
- 追加したノズルは金額に見合った機能を発揮するのか
この辺りを考えないといけません。
機能は分からないけどとりあえず付けたいという意思表示があればまだしも、ノズルを追加したいという要望すらでないのが現実です。
さすがに、予算は見てほしいところですが金額が少ないから無視しているエンジニアも多いです。
拡張余地
ノズルの数は将来の拡張余地に影響を与えます。
これも当たり前のこと。
とはいえここはプラント設計の思想が結構色濃く出ます。
強度
ノズルの数は、設備の強度に影響を与えます。
ノズル数が多いほど強度は下がります。
当たり前のことですが、(以下略)
オーナーエンジニアはタンクの強度計算はメーカーに丸投げすることが普通なので、1個ノズルを足してもメーカーが何とかしてくれると思っています。
強度を落としてまでノズルを足す必要があるのか、という視点でも考えたいところです。
バッチ系化学プラントではかなり低圧の条件でしか使わないのでほとんど気にならないですが、影響がでるという意味で正確に理解しておきたいことです。
底抜きノズルがある場合
ここから先はタンクのノズルオリエンテーションを考えていきます。
タンクの底抜きノズルがある場合を考えましょう。
底抜きノズルの特徴
底抜きノズルの特徴をまずは整理しましょう。
当たり前のように見えますが、言語化することで本質が見えてきますので。
全量液抜きができる
底抜きノズルがあると全量液抜きができます。
逆に言うと底抜きノズルがないと全量液抜きはできません。
当たり前のように見えますが、非常に大事なことです。
これはバッチ系では特に大事です。
切替生産をするということは、プロセス設備を洗浄しなければいけません。
次の製品で使用できる程度まで洗浄しようとすると、
全量液抜きは非常に有利に働きます。
連続工場でも程度の差はあれ、全量液抜きは必要です。
だから、化学プラントのかなりの設備が底抜きノズルが付いた設備で構成されています。
底の中心部に液抜き
底抜きをする場合、中心部に向かって抜くようにするのが基本です。
これも当然のようですが、大事なことです。
設備の重量バランスが中央に来るようにするためです。
下のようなイメージになります。
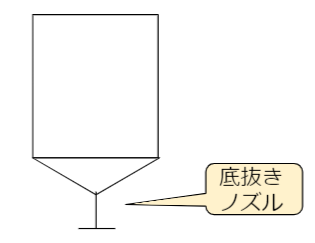
漏れると大ごと
底抜きノズルを付けるということは、いったん漏れると全量漏れることを許容しているといえます。
それはそうですよね。
全量抜き出しを前提とする底抜きノズルで、万が一ノズルから漏れれば、全量漏れます。
水などの安全な液体なら気にならず、家の水回りでは気にならないですよね。
でも、危険な化学薬品を扱うタンクでは、底抜きノズルにはメリットとデメリットの両方があることを意識しておくべきです。
あまりにも多くの設備が底抜きノズルを付けているので、当然のように思っている人もいますが、注意したいところです。
タンクの底抜きノズルラインに、ねじ込み継手や挟み込み部品を付けているケースが見られますが、これは漏れのリスクを考えていない設計です。
タンク上部
底抜きノズルがあるタンクのオリエンテーションは、タンク上部の問題に限定されます。
というのも設置状況を考えれば分かること。
底抜きノズルが付いたタンクの設置イメージは以下のとおりです。
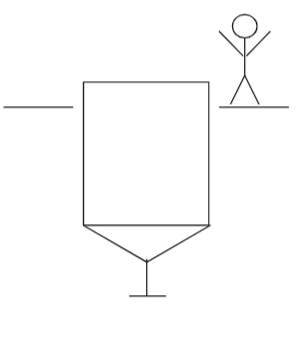
タンクの上部に人がアクセスする場所があり、そこで何らかの作業がある。
底抜きノズルが付いているのでタンクは床面から浮かせないといけません。
底抜きノズル自体の高さが、人が作業できる場所に設定します。
そうすると、タンク上部は非常に高い位置になります。
ここにアクセスして作業することが大事な問題になります。
一部のタンクでは横抜き・横出しなどの機能を持たせることもありますが、レアケースなので今回は除外します。
タンク上部のノズルオリエンテーション
タンク上部のノズルオリエンテーションを見てみましょう。
以下のようなイメージになります。
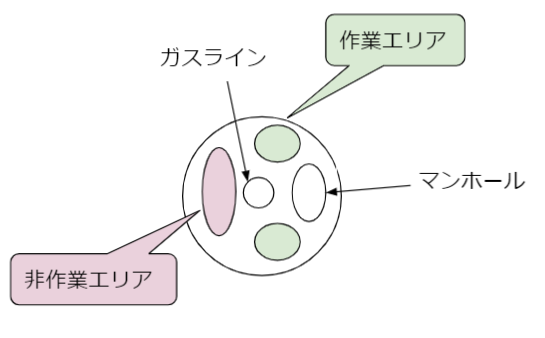
ガスラインは中央
ガスラインはタンク中央に配置します。
これはタンク上部が皿型やコーンルーフ型である場合をイメージしています。
平蓋タンクでタンク中央に配置する必然性はありませんが、
設計思想を統一するという意味で、中央部に配置する方が分かりやすいと思います。
反応器などタンク中央部に攪拌機を設置する場合は、ガスラインは中央には配置できませんが、それは別に考えましょう。
マンホールは通路に近い位置
マンホールは通路に近い位置に配置します。
これも当然といえば当然。
マンホールを付けれる余裕がない小さなタンクでも、200A程度のハンドホールは設置しておきたいです。
いずれにしろ、マンホールという大きなノズル位置を最初に決めるべきです。
バッチ系化学プラントでは、例外は粉体系に限定されるでしょう。
ヘッダーは作業エリア側
ヘッダーは作業エリア側に配置します。
作業エリアとはマンホールに近い側の部分です。
ヘッダーだから液を受け入れる口のことですね。
液の受入ヘッダーにはバルブが付いているのが普通なので、そのバルブ操作をするために、作業エリア側に配置します。
窒素の入口だけを単独ノズルにしている場合もありますが、これも作業エリア側に配置する方が良いです。
非作業エリアのノズルは避ける
その他の用途のノズルは非作業エリアに配置します。
非作業エリアはマンホールと反対側の位置のこと。
非作業エリアにはノズルそのものを配置したくないです。
付けるとしても以下のような用途に限定したいですね。
- 照明口
- 液面計
- 破裂板
これらは作業頻度や点検頻度が少ない用途ですね。
底抜きノズルがない場合
底抜きノズルがないタンクの場合を解説します。
これは例えば屋外タンクのような平底タンクをイメージしています。
タンク貯槽の底部形状が平底である理由ってなんでしょうか?
基本的すぎて改めて問われると困るのではないでしょうか。
平底タンクを選ぶ理由はいくつかありますが、以下の理由が多いでしょう。
- タンク容量が非常に大きい
- コストを削減する
- 全量送液が求められない
屋外タンクが基本的に平底形状であるのは、容量が大きいからですね。
形状が大きいタンクであればあるほど、ノズルオリエンテーションの自由度は高くなり難易度が上がっていきます。
高い自由度の設計では、自由度を限定するための思考を第一におこなうべきです。
側板マンホールと天板マンホールは距離を取る
ノズルオリエンテーションのうち最初に設計すべきノズルはマンホールです。
ノズルオリエンテーションに限らず、プラント設計においては「大きなものから順番に決める」というのが大事です。
プラント建設において反応器や塔を最初に決めるのと同じこと。
マンホールはノズルの中でも最も大きなものです。
ここから決めましょう。
マンホールは「天板マンホールと側板マンホールの距離を取る」というのが基本思想。
以下のようなイメージです。
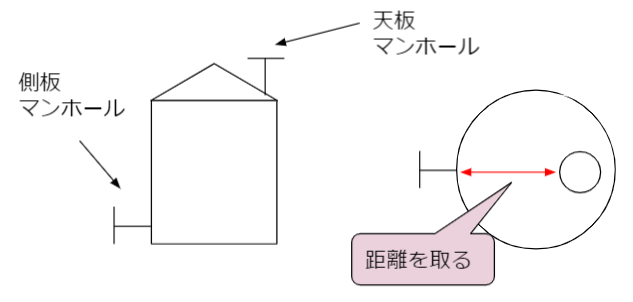
全量液抜きができない平底タンクには側板にマンホールを付けます。
これは中に人が入って掃除をするためです。
側板マンホールだけでなく天板マンホールも必要です。これは、
系内を空気で置換するときに滞留を少なく置換できるという思想から来ています。
これだけでもマンホールの位置はほぼ決まってきます。
天板マンホールと側板マンホールはできるだけ離す
マンホールの位置は、ノズルオリエンテーションの大きな制約条件となります。
液入ノズルは液出ノズルから離す
マンホールの次は、液入ノズルと液出ノズルの位置関係を考えます。
ここにも制約条件があります。
液入ノズルが液出ノズルから近すぎると問題があります。
液がタンク内に入る時に、液体内に溶け込んだガスが気相部に出ていきます。
これが液出ノズルと近いと気泡がポンプ側に巻き込まれ、キャビテーションが起きやすくなります。
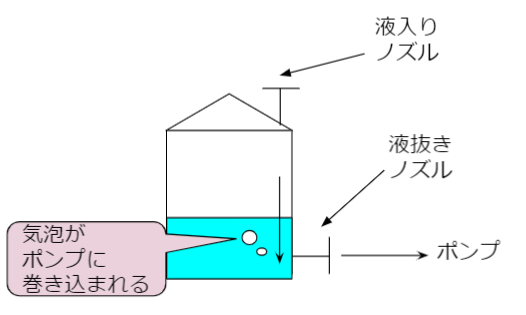
液入ノズルと液出ノズルはできるだけ離す
これが液入・液出ノズルの制約条件となります。
マンホール側の制約とノズル側の制約がセットで効いてきます。
タンクとポンプの位置
タンク単体にはマンホールやノズルの制約があることが分かりました。
タンクのノズルオリエンテーションを決めるためには、タンク単体だけでなく他の要素と関連付けないといけません。
その代表例がポンプ。
タンクとポンプの距離はできるだけ近くしたいもの。
キャビテーション防止の目的からも配管長さの最小化からの面からも当たり前。
ところがポンプの位置を決めようとすると、意外にも制約が出てきます。
- 通路からポンプが近い位置にあるか
- ポンプの近くに配管ラックがあるか
- ポンプの近くにローリーを寄せることができるか
ポンプの位置が作業性に直結するので、大きな制約条件になります。
ポンプの位置から液出口ノズルはできるだけ近く
天板上での作業を極小化する
平底タンクなど底抜きノズルがないタンクの場合、天板上での作業は極小化したいものです。
天板上の作業の有無は、タンクのノズルと配管部品との関係で決まってきます。
- 逆火防止装置の網と開放口は天板上が好ましい
- 配管のバルブや逆止弁は地上が好ましい。
- 配管の閉止板を設置するのは地上が好ましい。
- 複数の配管をタンクに接続する場合は、できるだけ地上でヘッダーを組む方が好ましい。
- 天板上のノズルは全方位均等ではなく、一方に固めた方が良い
天板上に設置しなければいけない配管やアクセサリーは少ない方が良いです。
天板の高いところに定期的に登る作業は、一般化すべきではありません。
天板のノズルの一方に固めるという思想は、普通の配管エンジニアは思いつきません。
これは機械エンジニアが気付いてあげるべきポイントです。
イメージとしては以下のとおり。
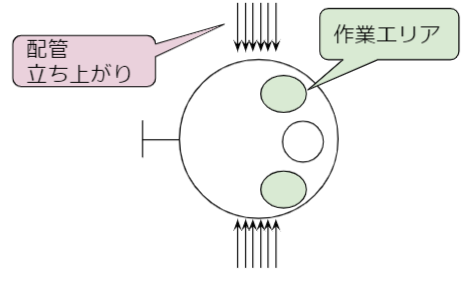
天板上のマンホールに近い部分に作業エリアを設けます。
液入りノズルはこの作業エリア近くに配置するのが好ましいです。
天板上のマンホールから離れた場所は、できるだけノズルを設けない方が良いです。
というのも、作業デッキの大きさが過剰に大きくなるからです。
タンクの大きさが大きくても、実際に作業に必要な面積は大きくなく、作業エリアを集中する方がコストメリットがあります。
作業エリアやマンホールを外した位置に、配管の立ち上がりスペースを設けます。
これはタンクに対しては大きな制約はありませんが、天板や側板のマンホールから外した方が良いでしょう。
配管立ち上がりスペースは、周囲の配管ラックの位置で決まるので、タンクとポンプの位置関係で決まってきます。
タンクとポンプの位置関係に影響を与えるのは液抜きノズルですよね。
付属品(昇降口・液面計)
これまでに上げた制約条件を重ねていくと、ノズルオリエンテーションの自由度はかなり下がります。
具体的には以下の程度まで限定できるでしょう。
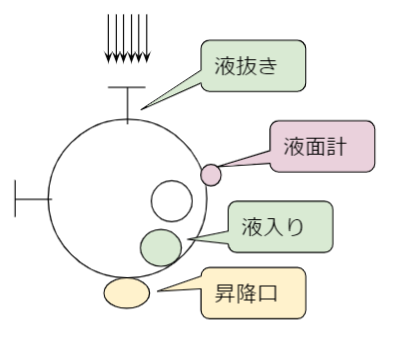
- 天板・側板のマンホールの位置を決めて、
- 液入口と液抜き口の方位が決まれば
- 配管立ち上がり位置が決まります。
- 昇降口は配管立ち上がり位置を回避する位置に付けて
- 液面計は液入口と液抜き口の間くらいに配置します。
これだけ決まれば、あとは細かい位置の設定に限定されますよね。
5番の液面計を「液入口と液抜き口の間」に配置するのは、差圧式液面計を想定しているから。
液入口や液抜き口の近くに差圧式液面計を設置すると、液の脈動の影響を受けやすくなります。
液の動きによる動圧が最も低くなる部分が、液入口と液抜き口の間くらいの部分です。
液入口と液抜き口のノズル位置を180°確保した場合、差圧式液面計を90°の位置に持ってくると良いです。
これは、流路面積が最大となる方位です。
なお、差圧式液面計の均圧口を天板に設ける必要があるので、天板にはノズルを立てないといけません。
均圧ラインも最小化したいので、液面計の取付方位と同じ方位の天板上にノズルを立てます。
そうすると、昇降口は少しずらした場所に設置しないといけません。
タンクサイズが大きい場合は問題になりませんが、中途半端に小さい場合は昇降口の場所に多少悩むことになりがちです。
全部の制約条件を完全に満足することはできないので、ある程度は妥協しないといけなく、昇降口や液面計はそのターゲットになりやすいですよ。
標準化と専用化
タンクのノズルオリエンテーションは標準化と専用化という2パターンで考えます。
上で考えた例はいずれも専用化の例です。
特定のタンクに対して最適なノズルオリエンテーションを決めるという視点で設計しています。
これは鉄やステンレスのタンクなら問題が起きにくいでしょう。
将来の拡張余地がそもそも少ないからです。
でもグラスライニングやフッ素樹脂ライニングのタンクだとこうはいきません。
切替生産を前提としたバッチ生産の場合、ノズル数が多い方が切替作業を減少できます。
どれだけノズルがあれば作業性が楽になるかを考えることになりますが、そんなことを考えるくらいなら強度に問題ない範囲でできるだけ多くノズルを付ける方が良いです。
これが標準化の発想です。
標準的なノズルを目指す場合、以下の要素を考えると良いでしょう。
- マンホールは400Aや450A
- ガスライン・粉体投入口は200A
- バッフルは専用化
- その他ラインはすべて100A
これは10m3以上のタンクを想定しています。
もっと小さなタンクだと口径は小さくても良いでしょう。
タンクの容量が小さいほど、設置できるノズルサイズが小さくなりながら、送液ポンプの流量が小さくてもよくて、配管口径を小さくできるからです。
標準タンクに対してガスラインや粉体投入口のためのノズルを確保していないと、後々に影響がでやすいです。
本体フランジを付けて天板を交換できるようにしていれば後で改造は可能ですが、漏れやすくなるし無駄な空間容量が増えるのであまりしない方が良いでしょう。
そうなるといったんタンクを設置してしまうと後で交換できないので、最初に考えることが大事です。
参考
タンク設計に関する教科書はほとんどありません。
どちらかというとプラント設計や配管設計に関連してきます。
だからこそ機器設計の前にプラント設計や配管設計の考え方を理解しておく必要がありますね。
関連記事
タンクに関する情報は非常に奥が深いです。さらに知りたい方は、以下の記事をご覧ください。
最後に
タンクのノズルオリエンテーションの考え方を紹介しました。
作業性・コスト・拡張余地・強度などにノズルオリエンテーションは影響を与えます。
底抜きノズルの有無で分けて、ノズルオリエンテーション専用化の考え方を紹介します。
標準化についても紹介します。
化学プラントの設計・保全・運転などの悩みや疑問・質問などご自由にコメント欄に投稿してください。(コメント欄はこの記事の最下部です。)
*いただいたコメント全て拝見し、真剣に回答させていただきます。
コメント
はじめまして
ノズルオリエンテーションについて
大変勉強になしました。
タンクを設計する際に
ノズルの高さの寸法公差を
どのようにして決定するか?ということを
考えてます。
何か、参考になる規格などありましたら
ぜひご教授お願いしたくぞんじます。
コメントありがとうございます。
ノズル高さの公差は、基準で明確に定めているものは無いはずです。
JIS B 8265や8266が規格の参考になりえますが、そこには記載がありません。
JIS B 0419にも明確な記載はありません。
高さがズレても配管とガスケットで対応できる可能性が高いです、
例えばノズル上部にバルブを置くと前後ガスケットの厚み3mmとして、6mmは調整代ができそうです。
私もほぼこの値で考えています。