化学プラントのオーナーエンジニアは、設備や工事に関するチェック業務の比重が非常に高く、自分で設計や施工をするというより、委託先からの成果物を確認・判断することが主な仕事です。
図面・仕様書・見積書など膨大な資料が日々積み上がり、限られた人員でそのすべてを確認するのは至難の業。
しかも、たった一つの見落としが重大事故や数千万円単位の損失に繋がる可能性もあるため、チェックミスは可能な限り減らさなければなりません。
本記事では、化学プラントにおけるエンジニアリング業務の中で、実際に私が行っている「チェックミスを減らす工夫」を紹介します。
チェックでミスを減らすためには、何となくチェックしている以上の取り組みが必要になると思います。
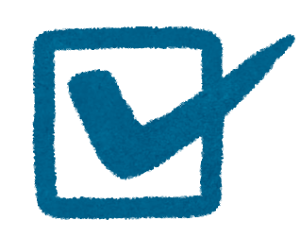
エンジニアリング業務ではチェックミスが起きやすい
エンジニアリング業務はチェックが非常に多いです。
業務の50%以上はチェックと言っても過言ではありません。
例えば以下のような内容をチェックしないといけません。
1個1個の内容はかんたんですが、問題はその圧倒的な物量。
質より量の世界です。
それでも1つでもミスがあれば大きな問題に繋がりかねません。
何を拾って何を捨てるか、という判断に迫られることも。
大事なことは、見間違いの確率を下げること。
現実的に誰にでもできることを3つ紹介します。
リストを作る
一番最初に意識することはリストを作るです。
当たり前のように見えますよね。
でも、意外とできる人が少ないですよ。
Excelで表やリストを作る時の基本ができていない人が多いです。
例えば、以下のような表を作ろうとしましょう。
りんご | 10個 |
いちご | 3個 |
みかん | 7個 |
普通に上記のように書けばいいのに、こんな風に書くエンジニアがいます。
りんご | 10個 |
いちご みかん | 合わせて10 |
あえて間違いを指摘しなくても、問題は分かりますよね。
セルを結合する例は典型的な例ですが、これだけではありません。
属性を揃える、表記を揃える、単位を揃える。
これはリストという意識が無いパターンです。
リストを整理して、リストで漏れを無くすというのはチェックの基本です。
リストの順番を統一させる
次はリストの順番を統一させるということ。
これは機電系エンジニアに限らず、プロセスエンジニアでも意識しない人が増えてきました。
機器リストと略フローを作ってプロセス合理化や見積を仕様としたときに、機器リストと略フローの並びが違うのでチェックが漏れるという例が典型的。
機器リストと略フローの順番を並べるだけで、2つの資料のチェックする速度や精度が変わり、見間違いを防ぐことができます。
機器リストから派生する設計書や仕様書なども全く同じ発想です。
変に順番を操作せず、並びを統一するだけで、複数の資料の転記チェックが簡単にできて、単純な見間違いをぐっと抑えることができますよ。
これだけでも数千万円の損失を防げたりしますからね^^
同じ人が作っているはずなのに、複数の資料で並びが違うのは不思議です。
どちらかが親資料で残りが子資料となって親資料から転送すればいいだけなのに、なぜかそうはいかないようです。
リスト化とほぼ同義ですが、そもそもリスト化をするのかリスト化をしてもう1歩踏み込むべきなのかという世界で違います。
チェックした箇所を色付け
チェックした箇所を色付けするということもとても大事です。
Excelで作業する場合は、セルの着色や文字の着色を使ってチェック機能を持たせましょう。
エンジニアリング業務ではP&IDや配管図で紙によるチェックが大活躍します。
P&IDと配管図を照合して、確認が終わった箇所から順番にP&IDと配管図にマーカーで着色する。
これだけです。
着色が増えていくたびに達成感が出てきます。見間違いのリスクも下がります。
資料のチェックはどちらかだけに統一した方が良いです。
親資料でなくて子資料をチェックする方が多いでしょう。
同じ目線で一通り見てみる
チェック項目や数が多い場合は、同じ目線で一巡させてみるという方法があります。
P&IDが50枚あって、主にチェックすべきことが10項目あったとしましょう。
P&ID50枚にその10項目のチェックポイントがある場合、単純に500個チェックしないといけません。
チェックリストをつくって1枚1枚確認することも1つの手ですが、大変です。
リストを作るだけでも面倒。
それなら、まずは1つの目線で一巡させるという方法があります。
P&IDなら接続だけを見るので一巡、口径だけを見るので一巡、機器の仕様を見るだけで一巡・・・という感じです。
これで10周させれば理論的には全部チェック可能。
何週も回るのも結構大変なので数周で回せるように、一巡目に数個のチェックをするというのが私は好きです。
他の人に見てもらう
恥ずかしがらずに他の人に見てもらいましょう。
1人で見れる範囲が限定されているという認識が大事です。
若くて責任感が強いけど能力が育っていない人ほど、他の人に見てもらいにくいです。
極端な例ではプライドが邪魔をしているというケースもあります。
1人でできることが限られているということを認識するのは、特にプラントのエンジニアリングでは大事なことです。運転でも同じですけど。
組織のルールとして周りに頼るという風潮は作り上げておきたいですね。
これとは別に検図というシステムを採用している会社もあるでしょう。
時間を置く
人数が不足している組織などでは、周りに頼る余裕もないでしょう。
こういう時は1人でチェックしますが、時間を開けましょう。
時間を空けると前とは違った目線で見れる可能性があります。
1日開けるだけでも結構違います。
書類チェックをその日に80%・翌日に90%まで仕上げる、というようなマネジメントができるとチェック業務の自由度も上がってきますね。
参考
最後に
化学プラントのエンジニアは「チェック力」こそが業務品質を左右します。
- リスト化と順番統一で抜け漏れを防ぎ
- 色付けと目線の固定で見間違いを抑え
- 他者の目や時間のフィルターで精度を上げる
一つひとつは小さな工夫ですが、これらを積み重ねて習慣化することで、大きな事故や損失を未然に防ぐことができます。当たり前のように実践して、ミスの確率を下げたいですね。
化学プラントの設計・保全・運転などの悩みや疑問・質問などご自由にコメント欄に投稿してください。(コメント欄はこの記事の最下部です。)
*いただいたコメント全て拝見し、真剣に回答させていただきます。
コメント