化学プラントの設備ライフサイクルに関わる検査の種類を紹介します。
設備保全エンジニアは設備のライフサイクル全体にわたって関連します。
設備を作って工場に設置してから、工場から撤去廃止するまで、全般にわたって検査を行います。
極端にいうと人間と同じ。
検査という目線で設備の一生を見ていきましょう。
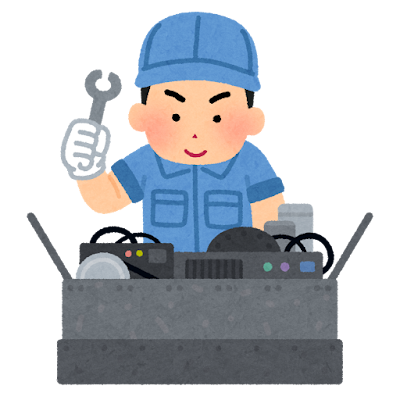
立会検査
立会検査とは機器の新品製作時の検査です。
製作終了段階の機器について、ユーザーがメーカー工場に赴いて検査をします。
普通は完成時の1回のみ。特別な要求で中間検査を設けることもあります。
立会検査の目的はただ1つ。
責任回避。
メーカーが責任を回避したいと強く考えます。
完成検査でユーザーが立会をせずに、現場に納入して使い出してからトラブルが起こったとしましょう。
このときに、製作メーカーに責任問い合わせが行きます。
そうするとメーカーも製作工程のどこで問題があったのか、詳細に調べて多大な工数をかけて対応しなければいけません。
記録がちゃんとしていないと問題を見つけきれない可能性もあります。
そこに時間を掛けるくらいなら、ユーザー立会検査をして問題ないことをユーザーに認めさせる方がいいでしょう。
立会検査で健全性が確認できているのだから、何か問題があったとしても以降の工程のはず。
ユーザー側の問題の可能性が高いでしょ?と論理を展開できるわけです。
新品の機器やメーカー工場の実際を見る機会は少ないです。
立会検査は品質管理だけでなく業界調査などの目的にも活用したいですね。
受入検査
立会検査が終わって、機器がユーザーに到着したときに受入検査を行います。
といってもすごく単純に外観と員数検査を行うくらいです。
外観の問題は輸送時のトラブルで起こりえますので、ユーザーは確実にチェックしておきたいところです。
ここまでチェックできれば、メーカーはほぼ責任を免れるでしょう。
本来ならメーカーも受入時に立ち会えればいいですが、通常はしないですね。
単体試運転
機器を受け入れて、プラント現場の工事が完了したら試運転を行います。
これも立派な検査の1つ。
こういう検査を行うでしょう。
私の職場ではポンプのみに限定して行います。
ポンプを1日くらい水で運転してみて、電流・振動・温度などの時間変化をデータ採取します。
これらのデータが問題ないことを確認して、実液の運転に入ります。
系統水運転
機器の単体試運転が完了すると系統水運転を行います。
系統水運転では以下のような目的があります。
- 配管・機器全系統から漏れがない
- 配管・機器全系統の洗浄
- 現場の作業性の模擬確認
- 制御シーケンスが意図通りに動く
大規模な改造工事や建設レベルでは、工事完了後に危険物をいきなり扱うことはせず水を流すことが多いです。
簡単な補修程度の工事の後なら系統水運転をパスすることもありえるでしょう。
工事段階ではいろいろなごみが系統内に侵入する恐れがあります。
塵・石・油・テープ・ボルトナットなどならまだ分かりますが、ウエス・番線などもありえますし、ヒドイ時には下着なども混入していました・・・。
ガラスやカーボンなどの割れやすい設備が、工事段階で破損したかどうかもチェックが可能です。
そういうゴミを取り除くためにも水を使って洗い流します。
と同時に系統の漏れチェックも可能になります。
増改築や建設の段階ではシーケンスを大幅に変更しますので、シーケンスが予定通り動くかどうかの現場チェックも水運転では大事です。
水運転の本来の目的はシーケンスのチェックと言い切っても良いくらいです。
理想的にはシーケンスもプログラム開発段階で100%完成していればいいのですが、配管図と同じように現場外では限界がありますね。
試運転
水運転を完了したら試運転に突入します。
試運転では1つ1つの工程を確実に実施するのが普通です。
工程をゆっくり進めていって反応が適切に進むかどうかをチェックします。
研究レベルで反応を開発していって最後の成果が試運転で判明します。
- 反応収率
- 工程時間
- 制御性
- 作業性
こういった要素を現場の商業運転に耐えるように最適調整を行う段階です。
問題が続出してその場で関係者が議論して解決していく、とてもダイナミックな仕事です。
ユーザーのエンジニアリングや建設では味わえない醍醐味ですね。
プラントエンジニアリング会社クラスのビックプロジェクトならこういうダイナミックな仕事ができるかもしれませんが、オーナーエンジニアではほぼ無理です。
日常点検
試運転が終わると商業運転に突入して、設備の日常点検の段階に入ります。
日常点検では運転員が生産活動をしながら簡単なチェックをしたり、OSIという形で運転段階でできる検査を行って診断します。
日常点検は傾向監視のためのデータ集めであり、補修タイミングを見極めるために必須です。
日常点検の対象になるのは、重要度の高い動機器や破損しやすい設備に限定されるでしょう。
ユーティリティ系のポンプやガラス・カーボン・PTFEなどの高耐食性機器が該当します。
プラント内の全機器を対象にしていると、メンテナンスコストが異常に上がっていきますよ。
定期点検
日常点検の結果、必要があれば定期点検を行います。
SDM(Shut Down Maintenance)という言い方もするでしょう。
設備保全エンジニアが大活躍する場面。
というより設備保全エンジニアは定期点検のために計画・準備をします。
大きな工場なら工場全体を止めずにプラント単位で定期点検も可能ですが、小さな工場なら全プラント停止です。
運転中と定期点検中とでは作業員や保全員の仕事の仕方が大きく変わります。
定期点検では設備を分解して整備したり部品を交換したりします。
オーバーホール(OverHaul)という言い方もします。
定期点検対象の設備をリストアップして必要な部品の手配をして、プラントを止めてオーバーホールします。
検査データの位置づけ
検査データの位置づけについて解説します。
検査データの目的
日々積上げていく検査データ。
これってどういう目的で使うでしょうか。
大きく2点あります。
- 定期点検によるオーバーホールのタイミングの見極め
- 機器更新タイミングの見極め
検査データを人間の健康診断に考えれば、何となくイメージができるでしょう。
定期点検でのオーバーホールのタイミングの見極めが保全の本質とも言えるでしょう。
どれだけ長期間同じ設備を使えるかは投資金額の抑制に繋がり、プラントの競争力を高めます。
しかし設備はいつの時期か限界が来るでしょう。
これを見決めるためにも検査データは活用されます。
検査データの種類
検査データの種類は大きく2種類あるでしょう。
- 定量的なデータ
- 定性的なデータ
定量的なデータは電流・温度・振動・板厚などのデータです。
これをリスト化すれば傾向監視はできるでしょう。
でもこれを綺麗なデータにするには結構大変です。
特に板厚は難しいでしょう。
1つのデータに統合しずらいです。
定性的なデータはA・B・Cなどのランク分けをするものです。
このランク分けすら綺麗にできないケースもあります。
仮にランク分けをしたとしても、評価者の目線に均一性が無ければ意味がありません。
判例も含めてランク分け基準を作るのは意外と難しいです。
定量的なデータも定性的なデータもデータ管理の分野ですので、やってやれなくはないですが人が不足しているのが実情です。
設備保全エンジニアはデータを活用できると存在価値が抜群にあがりますよ。
参考
最後に
化学プラントの設備寿命やライフサイクルに関連する検査の種類について解説しました。
立会検査・受入検査・単体試運転・水運転・試運転・日常点検・定期点検
メンテナンスという投資に関わる重要な検査ですので、データ整理をしっかりするのが設備保全エンジニアの役目ですね。
化学プラントの設計・保全・運転などの悩みや疑問・質問などご自由にコメント欄に投稿してください。(コメント欄はこの記事の最下部です。)
*いただいたコメント全て拝見し、真剣に回答させていただきます。
コメント