プラントのライフサイクルとメンテナンスコストについて解説します。
オーナーエンジニアにとってプラントは、建設してから廃棄するまで、ずっとその場にあって担当するもの。
特に保全担当者は異動のチャンスも少ないので、入社してから定年まで1つのプラントを担当するということもあり得ます。
そこではプラントの経年劣化に伴って、メンテナンスコストの話題が欠かせません。
ちょうど、自身が高年齢になって病院に行く頻度が増えて、治療費が増えるのと同じ関係。
日常の保全業務に追われて、長期的な視点が身に付きにくいですが、設備保全エンジニアとしてプラントの経営に直接かかわる重要テーマです。
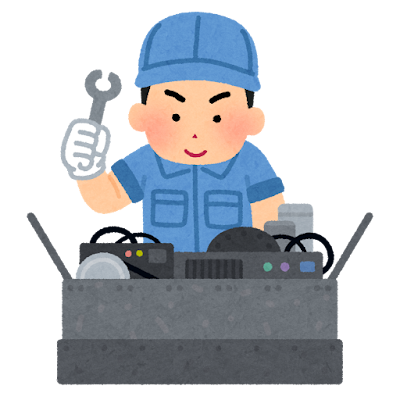
プラントのライフサイクル
化学プラントの視点では、プラントのライフサイクルは非常に重要なテーマです。
この部分において、機電系エンジニアの保全は非常に重要な役割を担っています。
プラントライフサイクルを考える場合に基本となるバスタブ曲線から解説しましょう。
バスタブ曲線は3つのフェーズに分けることができ、それぞれ初期故障期・偶発故障期・摩耗故障期です。
これらの詳細を見ていきましょう。
初期故障期
初期故障期ではプラントの馴染み運転の期間と考えましょう。
約2~3年が初期故障期として設定されるでしょう。
特に1年目は試行錯誤の嵐です。
人間でいう、赤ん坊の状態です。
- プラント建設段階で発生していたが解決できなかった不具合
- プラント立ち上げ後に発生した不具合
- 運転員や関連メンバーの習熟期間
- 運転に対する各種体制の構築
こういった問題を解決するための期間が初期故障期です。
立上時は大勢の人間がフォローしますが、本番は立上が終わってから。
必要がある時のみフォローするという体制に移行し、フォローがすぐに得られないケースも出てきます。
機電系エンジニアの保全部隊のように、付きっきりでそのプラントを見る人がぐっと減っていきます。
その中で運転データを蓄積し不具合を抽出し、SDMのタイミングで少しずつ改善をしていきます。
さすがに3回もSDMを行えば、ほとんどの問題は解決するでしょう。
偶発故障期
初期故障期が過ぎれば、偶発故障期に移行します。
初期故障期でトラブルはほぼ出尽くしている状態なので、安定的な運転や保全ができる段階です。
この期間は30~50年続きます。
安定した運転が可能で、保全コストの削減などのカイゼンにも取り組める時期です。
会社からは保全の最適化を図って、定期的な補修費の削減を要求される時期でもあります。
TPMの発想がまさにそうですね。
摩耗故障期
偶発故障期を通り過ぎると摩耗故障期に到達します。
この段階になるとプラントの各種設備が故障しだします。
人間でいう、おじいちゃん状態です。
摩耗故障期になるとメンテナンスコストが跳ね上がり、運転機会を損失していきます。
プラントとしての競争力が無くなるので、建て替えを推奨されます。
いつ摩耗故障期に到達するかは傾向が読みにくいでしょう。
とはいえ摩耗故障期を適切に見定めることは、化学プラントの経営上非常に重要な決心となります。
- 機械設備の故障
- 建築物の耐震基準との乖離
- 原料の供給
- 製品の需要
摩耗故障期に入るとプラントの建て替えも検討しないといけませんが、製品のライフサイクルとプラントのライフサイクルは必ずしも一致しないという問題が起きます。
摩耗故障期直前に導入された新製品ならライフがまだまだあるのに、プラントのライフがもうないから建て替えをする。
こうなったら新製品の競争力は無くなっていきます。
経営判断としてさまざまな要素を考えなければいけません。
補修費の設計
初期故障期とくに1年目の補修費の設計はどうすればいいでしょうか?
実はあまりいい方法はありません。
- 各種設備のメンテナンス費用の積み上げ
- 類似プラントの補修費に係数をかける
一般には、1の方が2よりも安価な金額として算出されます。
メンテナンスの立場からは2を提案するのが良いでしょう。
初期故障期でどんなトラブルが起こるかも分からないのに、メンテナンス費用を限界まで削る理由はありません。
プラント建設レベルならプラントエンジニアリング会社に依頼するので、建設投資費用が一定量余らせるように投資額を決めやすいです。
1年目はそこから費用を捻出することも可能でしょう。
問題はプラントの増改築レベル。
プラント建設に比べて厳しい投資判断を迫られ予算の余裕がなくコストアップ要因が増え続けている現在では、投資予算が不足する傾向にあります。
大きな投資を伴う増改築だと1年目の運転は初期故障期に近い発想が必要なのに、その費用が補填できない。
こんなパターンに陥りがちなので、補修費の設計上は新製品の導入など機器数の増加も加味したいところです。
補修費の解析
補修費の運営管理上は、補修費の解析が非常に大事です。
これは日々の補修依頼とその実績を積み上げていく地道な作業になります。
積上げたデータは例えば以下のような形で見えるでしょう。
機種ごとに費やした補修費の割合の形です。
- 動機器 47%
- 静機器 14%
- 配管弁 20%
- その他 19%
理由ごとに費やした補修費の割合の形もあるでしょう。
- 単純修理 71%
- 運転中整備 6%
- 定期修理 14%
- 運転改善 6%
- その他 3%
動機器が壊れやすい
一般的な化学プラントでは動機器の修理が多いです。
費用的にも頻度的にも高くなるでしょう。
運転を止めないといけない可能性が高く、設備保全エンジニアも注意を払っている部分です。
単純修理が多い
化学プラントでは単純修理の割合が多いです。
バルブの内通・ガスケットの破損・配管のピンホール
いろいろな単純修理があります。
単純修理という分類をすると設備改善の機会を失ってしまいます。
特に配管の問題は老朽更新ではなくて、配管レイアウトによる問題がありえるからです。
とはいえここに設計労力を割いて寿命を延ばすにしては、費用対効果の面で課題があります。
少し設計要素を考えて改善しても寿命が少ししか変わらないから、単純更新で我慢する。
こう書けば否定的なニュアンスがありますが、家庭で単純更新や消耗品扱いしている物って結構ありますよね。
それと同じ扱いにするかどうかという考え方の違いだけです。あまり真剣に考えない方が良いでしょう。
運転中修理は少ない
成熟した化学プラントでは運転中の修理・応急補修の頻度は少ないです。
計画的に保全ができている証拠ですが、SDMまで我慢しているというケースも多々見られます。
この辺の塩梅が統計的なデータとしては読みにくいですね。
補修費の見直し
定期的に補修費は見直しが必要です。
TPMなどの保全活動による補修費の削減効果を期待できたのは過去の話です。
補修費は一般的には増額させていく方向でしょう。
増額・減額の要因に分けて補修費の見直しの理由を整理しましょう。
増額
補修費の増額要因としては以下があげられます。
- 労務費の増加
- 資材費の増加
- 機器数の増加
- 生産中止
- 外注工事の内省化
労務費や資材費の増加は世間一般の常識でしょう。
これを自社の補修費レベルで増額アップの要因とするには、労務費や資材費に関するデータ蓄積が大事でしょう。
調達部の仕事です。
機器数の増加は新製品の導入や合理化が大きな理由でしょう。
重要機器に対して据付予備を設置するだけでも機器数の増加になります。
生産中止はイレギュラー的要素です。
メーカーが生産停止をしたために、別のメーカーの設備に更新しないといけない。
これを補修費で割り当てるか別の予算を使うかは判断が分かれそうです。
外注工事として外部会社に依頼していたものを自社で対応しようとすると当然コストアップになります。
外注化する方が一般的なので、レアケースとなるでしょう。
減額
補修費の減額要因としては以下が挙げられます。
- 合理化
- 予備品の統一
- 省エネ
- 機器数の減少
合理化とはTPMクラスの話です。
現場でのカイゼンで設備の寿命を延ばしたという系統の話。
TPMが流行ったころはこういう改善が絶大的な効果を発しました。
いまではカイゼンの種が少なくなっていって、補修費の減額の要因にはなりにくいでしょう。
予備品の統一は、プラント数が多いほど有力です。
保全レベルでは担当者での予備品管理をするでしょうが、担当者の垣根を越えた管理はあまりされません。
これができれば予備品の数量を削減できたり、トラブルが起こったときに速やかに対応できたりと、対応がとりやすくなります。
予備品を過度に持たないという意味で補修費の減額要因となるでしょう。
省エネも補修費の減額要因となります。
省エネ前には動力設備を使っていたが、動力設備を使わずに運転できるようになれば省エネです。
ここで動力設備が無くなる分だけ機器数の減少つまり補修費の減額となります。
機器数の減少はそのままですね。
プラントの限界点
プラントのライフサイクルを考えた時に、建て替えという決心をどこかでしないといけません。
ここがプラントの限界点です。
摩耗故障期の前後に設定することが一般的です。
プラントのライフだけを考えれば限界点は容易に決めれますが、課題は製品のライフ。
製品の供給責任、運転員への仕事の提供など会社として考えるべき要素が絡まっていて、簡単に考えられるものではありません。
こういう背景があるということを認識したうえで、プラントのライフとしてはどういう状態にあるかという視点で議論ができるように、設備保全エンジニアはなりたいものです。
メンテンナンスコストの個人的な考え方
さて、メンテナンスコストに関して個人的な考え方を最後に述べます。
削減しすぎ
メンテナンスコストは一般に削減されすぎの傾向があります。
これは会社側の都合が大きいです。
今まで問題が無かったから今年も大丈夫だろう
というチキンレース的な発想で補修費の増額を認めず年々経過している結果です。
責任回避をする思想が積み重なった結果が、メンテナンスコストの削減という形で現れるでしょう。
勉強してなさすぎ
運転員や設備保全エンジニアが勉強してなさすぎという傾向があります。
メンテナンスコストを削減するのは会社側の都合ですが、仮に無限にメンテナンス予算を割り当てた場合、
設備保全エンジニアは湯水のごとく予算を消費するでしょう。
予算の運用には、お金に対する知識や経理に関する知識が欠かせません。
設備保全エンジニアでこういう知識を十分に持っている人は多くありません。
自分に割り当てられた財布を使っていって給料日間近になると節約するという思想だけでは、メンテナンス費用が増額される方向にはなかなか動かないでしょう。
アピール目当ての新技術
メンテナンスコストを考える場合、新技術の導入が1つのテーマになります。
予算的に余裕がある会社ほどこういう分野に積極的です。
DXもその1つの例。
でもメンテナンスコストを考える場合に有用な手段というのは実はあまりありません。
- 特定の検査に対して有効
- 特定の補修に対して有効
- 一般的なツールだが、カスタマイズできない
こういう目新しいものに着目して、導入される場合があります。
実態としてアピール目的であり、メンテナンスコストには直結しません。
下がる方向では作用せず、変化しないか上がる方向でしょう。
それでも新技術を導入したことこそが実績としてアピールポイントになり昇進するのであれば、前向きに取り組み人もいるでしょう。
参考
関連記事
さらに知りたい方は、以下の記事をご覧ください。
最後に
化学プラントのライフサイクルとメンテナンスコストについて解説しました。
バスタブ曲線、補修費の設計・解析・見直し、プラントの限界点について一般的な考えをまとめています。
プラントの経営に直結しますので、設備保全エンジニアが活躍する分野です。
化学プラントの設計・保全・運転などの悩みや疑問・質問などご自由にコメント欄に投稿してください。(コメント欄はこの記事の最下部です。)
*いただいたコメント全て拝見し、真剣に回答させていただきます。
コメント
検索してて辿り着きました。事務屋は、こういったメンテコストを削減したくなりがちです。一方で、設備屋さんは、「とにかく、メンテコストは増大するんだ!」と定性的に語りがちです。世間一般の化学プラントにて、経時(老朽化)よるメンテコスト増大を定量化して示した論文とか、無いものですかね?(値上げ活動中の営業マンですw
少し調べていたら相当時間が経ってしまいました。
そういう論文は私も見つけることができませんでした。
年数によってメンテ頻度があがり、昨今の単価上昇を加えて
メンテ頻度の上昇×単価上昇=コスト上昇という表現になると思います。
前者は工場のメンテナンスマンのカバー範囲、後者は調達や営業の方が詳しいと思います。