化学プラントの設計や保全では、現場のトラブルや失敗を個別に捉えがちです。しかし「仕事は点ではなく線として捉える」視点があれば、見過ごされがちな原因や改善策に気づけます。
本記事では、プラントエンジニアが持つべき“流れ思考”の重要性と、それを実践するための具体的な観点を解説します。
仕事の流れ
どんな仕事にも流れというものがあります。
時間の流れ・人の流れ・物の流れ・・・といろいろありますが、時間の流れが最もわかりやすいでしょう
時間の流れを1つ取っても職種によってバラバラです。
例えばプラントエンジニアの設計の場合は1年~2年くらいのスパンの仕事が多く、保全の場合は数日~数カ月のスパンが多いです。
本当なら設計はプラント全体を見るという意味で10~20年先を考えた設計をすべきですし、保全はプラントが無くなるまでずっとを視野に置かないといけません。
保全の方が長期的な物の見方が必要ですが、実際には短期的な物の見方で終わりやすいです。
問題が起きたときにその1つ手前の事象だけは見るけど、その前を見ないという人が大半です。
下手すると1つ手前の事象も振り返らない人もいます。今起きていることだけに夢中というパターンです。
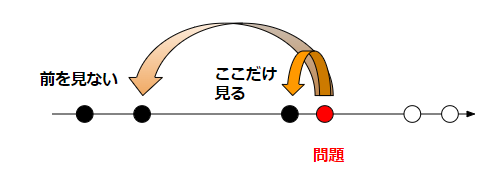
そういう例をこれからいくつか紹介していきましょう。
使いにくい設備が導入された
設計でよくあるのが、現場から使いにくい設備と言われる例。
これを設計の失敗と簡単にとらえる人が多いです。
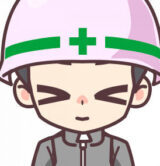
設計者としてもっと学習しないと・・・
こういう思考パターンができているうちはまだ良いのですが、長期的にこの仕事をしていると疲れてきます。
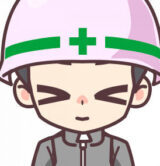
情報を出さない製造が悪い!私は悪くない!
こんな責任転嫁をしだすようになると、精神的に疲れてきている証拠です。
どちらのケースでも注目したいのは、流れの1点だけを見ているということ。
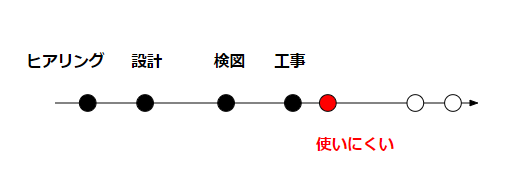
製造が設備が使いにくいということが分かるまでに、いくつもステップがあります。
- 設計者から製造にヒアリングがあったタイミング
- 設計書の検図が来た段階でチェック
- 設備図面の検図が来た段階でチェック
- 設備の据付工事があったタイミングで確認
いろいろな確認フェーズがあります。
もちろんこれ以外のタイミングで、製造は確認することはできます。
そういう手間を惜しんで、設計者に丸投げして委託しているのに、結果が使いにくいと言われてもエンジニアとしては気にしすぎない方が良いです。
情報の共有は組織を効率的に動かすために大事。
そこを意識していない製造にも一因があります。
「知識をより習得するべき」という設計者の気持ちも大事ですので、バランス感覚を保てるようにいろいろな目線で見れる方が健全です。
納期が間に合わない
納期は時間の流れとして典型的。
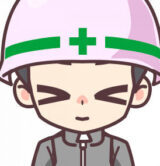
4か月後に間に合わせて!
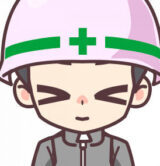
納期1年かかりますが・・・
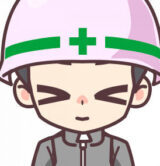
それを何とかするのが仕事でしょ!
というような流れはさすがに聞こえなくなってきました。
真面目な人ほど、何とか要求にこたえようと無理をしてしまいます。
- 調達部に無理な依頼を押し通してもらおうとする
- メーカーに強いプッシュを掛ける
昨今はコンプライアンスの問題にすぐに繋がるので、こういう行為は辞めておいた方が良いです。
逆に、製造が無理な要求をしてきた場合は、コンプライアンスを盾にしましょう。
そのためにもコンプライアンスに対する体制を、会社としてはしっかり構築して教育したいですね。
設備が壊れた
設備が壊れたときの対応は、保全としてよくある例です。
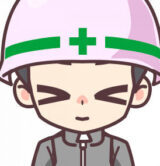
壊れた!直した!
保全としては直すことに全力を費やしてしまうので、その手配にだけ目が行きがちです。
- メーカーに最速納期で要求する
- メンテナンスマンを最速で呼ぶように努力する
- 自分で治す
いずれも今にしか視点が行っていません。
本来なら、もっと前後を考える必要があります。

保全は設計の思想を知ろうとせずに、実物だけを見ようとする傾向があります。
化学プラントの場合は運転員の使い方も大事ですが、これもスルー。
壊れた設備にだけ目が行き、他に行ったとしてもこれまでの修理履歴を見る程度です。
これまでの保全方式が適正だったのか、予備品を適正に持とうとしていたのか、次に導入される設備に注文を付ける。
こういう先に繋がる目線はなかなか持てないようです。
予算が足りない
予算が足りないという場合も、いろいろ考えることはあります。
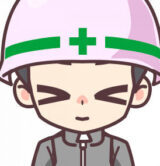
価格が高騰した!
今はこれを言い訳のように使いやすくなりました。
予算が足りなくなって、急にこの言い訳を使います。
これも流れを俯瞰するとできることはあります。
- 最近の予算高騰の傾向を見て、補正して予算化する
- 予算の執行段階で、定期的に状況をチェックする
- 定期的にメーカーと話をして状況を調べる
- 類似設備の実績から推算する(0.6乗)
全部が全部できる場合とは言えませんが、できる手段をピックアップしておきどのカードを切るかという考えを持っておくと良いでしょう。
1つしかないとそこに依存してしまいます。
単純な予算だけでも時間と金の流れを考えると、できることはあります。
参考
関連記事
さらに知りたい方は、以下の記事をご覧ください。
最後に
化学プラントの設計・保全で成果を上げるには、点ではなく線で仕事を捉える“流れ思考”が欠かせません。問題発生時には、それぞれの段階を俯瞰し、多面的に原因を探ることで、根本的な改善策が見つかります。
視野を広げ、流れの中にある要点に気づけるエンジニアを目指しましょう。
エンジニアだと起こった問題の直近にしか目がいかないことが、とても多いです。時間的スパンはそれなりに長いので、時間の流れの中でできることはいっぱいあります。
化学プラントの設計・保全・運転などの悩みや疑問・質問などご自由にコメント欄に投稿してください。(コメント欄はこの記事の最下部です。)
*いただいたコメント全て拝見し、真剣に回答させていただきます。
コメント