熱交換器の性能評価に欠かせない指標である総括伝熱係数U値。
教科書ではよく見かけるこの「U値」ですが、実際の化学プラントでは設計値と現場測定値にギャップが出ることも多く、現場での取り扱いに悩むエンジニアも少なくありません。
この記事では、総括伝熱係数Uの意味・算出方法・現場とのズレの読み解き方を、初心者向けに丁寧に解説します。工場現場での総括伝熱係数のデータ採取と解析の例を紹介します。
計算式は教科書的ですが、データの採取はアナログなことが多いでしょう。現場レベルではどんなことを行っているのか、エンジニアは意外と知らないかもしれません。
トライアンドエラー的な要素がありますが、ぜひともチャレンジしたいですね。
U値(U-factor)の計算式
U値の計算式から紹介しましょう。
下記の式が基本となります。
$$ Q = UAΔt $$
この式を変換して、U値を求めることを意識した表現にしておきましょう。
$$ U = \frac{Q}{AΔt} $$
この式からU値を求めるには、以下の要素が必要であることはわかるでしょう。
- 交換熱量Q
- 伝熱面積A
- 温度差Δt
それぞれの要素をもう少し細かく見ていきましょう。
交換熱量Q
交換熱量Qは運転条件によって変わってきます。
以下のフローを考えましょう。
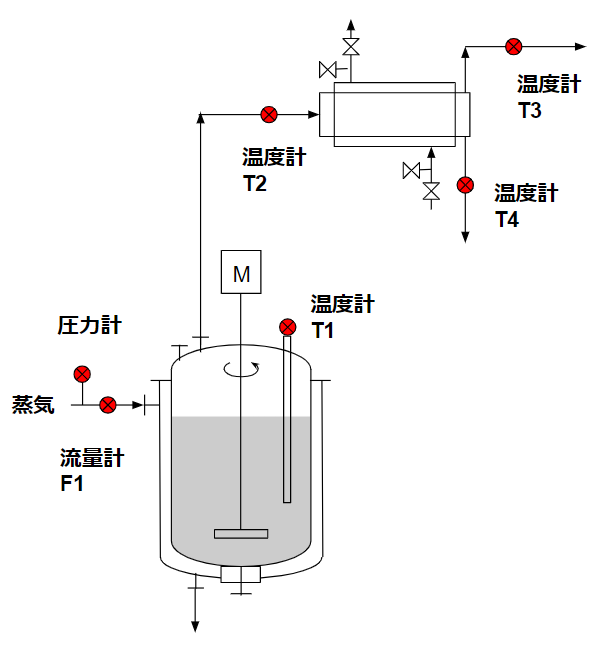
これは典型的なバッチプロセスです。
バッチ運転なので各種条件に応じてU値の計算条件が変わってきます。
反応器の加熱
反応器を加熱する段階を見てみましょう。
この段階での交換熱量のデータ採取は簡単です。
反応器内のプロセス液の温度変化を調べれば終わり。
温度計の時刻データを採取して、液量mと温度差ΔtからmCΔtで計算します。
比熱Cはそれなりの仮定を置くことになるでしょう。
プロセス液量の測定のために液面計が必要となるので、場合によっては使えない手段かもしれません。
スチーム側を調べる方が安定するかもしれません。
スチームの蒸発潜熱Qvと流量F1から、QvF1を計算すればいいです。
Qvを計算するためには圧力のデータが必要です。スチームの圧力は運転時に大きく変動する要素が少ないので、一定と仮定してもいでしょう。
加熱条件を制御するためには、スチームの流量計は必須です。
反応器の蒸発
プロセス液の加熱が終わり蒸発する段階になると、加熱段階とは違ってスチームの流量に絞って考える方が良いでしょう。
数学的には反応器内の液面変化を計算すればよさそうにも見えますが、運転時の液面は変動するのが一般的です。
撹拌や蒸発に伴う液の上下が発生するからです。
一方で、スチームの流量は安定します。
熱交換器の冷却
蒸発したガスを熱交換器で冷却する場合を見てみましょう。
これはガス流量mp×温度差Δtとして計算されるでしょう。
ガス流量mpはどうやって計算するでしょうか?
反応器内での交換熱量/プロセス蒸発潜熱できまります。
スチームで計算したQvm1と同じ計算を行います。
プロセスの蒸発潜熱Qpガス流量mpとおくと、
$$ Q_vm_1 = Q_pm_p $$
として計算します。単純と言えば単純。
Δtの計算は温度計に頼ることになります。
現場計器でもいいので、熱交換器の出入口には温度計を基本セットとして組み込んでおきましょう。
温度計がない場合は、結構悲惨な計算を行うことになります。
冷却水側の流量を間接的に測定しつつ、出入口の冷却水をサンプリングして温度を測ります。
アナログです。
熱交換器の冷却水向けにインラインの流量計を設置することは少なく、管外からでも測定できる流量計に頼ろうとするでしょう。
この精度がどれだけ信頼できるかだけで計算結果が変わります。
さらに、サンプリングにも相当の気を使います。
サンプリングしても気を許していたら温度がどんどん低下します。
信頼感はぐっと下がるでしょう。
流量計と同じく管外から測定できる温度計を使ったとしても信頼性はぐっと下がります。
とはいえ、熱交換器でU値の測定をシビアに行う例はあまりありません。
単一製品の特定の運転条件でU値を求めたとしても、生産レベルでは冷却水の変動がいくつも考えられます。
- 他ユーザーの熱負荷
- 季節要因
- 冷凍機の運転状況
一年を通じで、十分に冷却されて入ればOKと緩く考えるくらいで良いと思います。
冷却水の温度+10℃くらいまで冷えていれば十分でしょう。
一般には30~40℃くらいです。
伝熱面積A
これは実務的には単純な幾何計算だけの話です。
メーカーの図面にも伝熱面積を書いている場合もあるでしょう。
現場レベルでも簡単に計算可能です。
鏡の伝熱面積の計算が面倒かもしれませんが、ネットで調べればいくらでも出てきます。
便利な世の中です。
そうは言いつつ、この伝熱面積は結構厄介です。
蒸発を行う場合はプロセス液面が時々刻々減少するので、伝熱面積も下がっていきます。
熱交換器で凝縮を行う場合は、凝縮に寄与する伝熱面をそもそも測定できません。
温度差Δt
温度差Δtは対数平均温度差もしくは算術平均温度差が思いつくでしょう。
現場レベルでは算術平均温度差で十分です。
$$ t_a – t_b $$
の世界です。
- 反応器の加熱・蒸発ならプロセス温度計-スチーム飽和温度
- 熱交換器なら熱交換器温度計-冷却水温度
反応器側はデータ採取が楽です。
- プロセスは温度計の指示値を読み取るだけ。
- スチームは圧力一定と仮定して飽和蒸気圧力と飽和温度の関係から算出
- 2つのデータを引き算
これだけです。
熱交換器側は冷却水の温度に仮定が入ってしまいます。
この瞬間に熱交換器のU値の測定はあまり信頼が置けませんね。
重要な熱交換器で熱制御を真剣に行う場合はちゃんと温度計を付けますので、熱交換器の全部が全部に対してU値の計算を真剣にしないという意味ではありません。
バッチではそんな重要な熱交換器があまり多くないという意味です。
U値(U-factor)は時々刻々変わる
U値は時々刻々変わります。
温度計や液面計のデータが時々刻々変わるからですね。
設備設計でU値の計算を行う場合は、瞬間的・最大的な条件を計算していることが多いでしょう。
真面目に計算しようとすれば、液面の変化などの時間変化を追いかける微分積分的な世界になります。
そこまで計算するとなるとちょっとだけ面倒。
その面倒に手を出せる機電系エンジニアはあまりいないと思います。
参考
伝熱の知識は化学プラントではとても重要な分野です。
熱に関する知識を深めるには以下のような本での勉強も大事です。
関連記事
伝熱に関してさらに知りたい方は、以下の記事をご覧ください。
最後に
総括伝熱係数Uは、熱交換器の性能評価やトラブル診断に役立つ重要な指標です。
しかし、現場で得られるU値は、設計値とは異なるのが当たり前。
Uの変化を定点観測することで、保守・点検・設備更新のタイミングを見極めることができます。
若手エンジニアの方も、ぜひ「Uの読み方」を身につけて、設備改善に役立ててください。
化学プラントの設計・保全・運転などの悩みや疑問・質問などご自由にコメント欄に投稿してください。(コメント欄はこの記事の最下部です。)
*いただいたコメント全て拝見し、真剣に回答させていただきます。
コメント