化学プラントのオーナーエンジニアって、仕事ができるように見えますか?
見えないと思ったあなたは、おそらく独立系のエンジニアリング会社でしょう。
見ると思ったあなたはエンジニアと取引がある会社や、技術に詳しくない事務系の人でしょうか。
オーナーエンジニアの実態は「仕事ができない」エンジニアです。
そんな実態をまとめてみました。
反面教師的に使ったり、自分でも就職できるかもというチャンスととらえてもらったり、参考になればと思います。
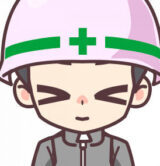
丸投げでも仕事が回ってしまいますが、1人立ちしようとすると絶対に自分で考え行動することが欠かせません。
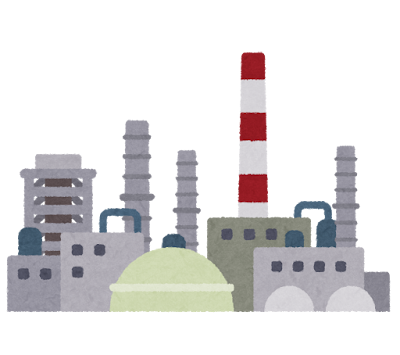
オーナーエンジニアの技術的サービス
ユーザー系エンジニアの技術的能力に視点を当てる場合、エンジニアとしての技術サービスについて先に見た方が良いでしょう。
ユーザー系エンジニアに求められる技術サービスとしては以下のような項目があります。
- 日常補修
- 定期修理
- プロジェクト
日常補修や定期修理は設備保全エンジニアが、プロジェクトは設備設計エンジニアがそれぞれ担当を分けて取り組むでしょう。
いずれにしろ工場の製造部をお客さんとしたサービスを展開します。
それぞれの会社でサービス内容は違うでしょうが、一例を紹介します。
- 補修の受付
- 補修会社の手配
- 修理報告書の作成
- 現地工事の立会
- 再発防止対策の立案
- 定期修理で行う項目の整理
- 補修会社の手配
- 工事計画書の立案
- 現地工事の立会
- 工事報告書の作成・報告
- 次年度以降の補修計画の修正
- FSや予算見積
- P&ID他工事資料の作成
- 設備の設計・仕様の確定
- 設備図面のチェック
- 必要資器材の手配
- 現地工事工程の立案
こうやって書くとエンジニアは立派な仕事をしていると思いますが、実態は結構差があります。
日常補修の実態
日常補修でよくある例は単なる「手配屋」としての仕事です。
- 製造部から電話やメールが入る
- 修理会社に依頼して日程を決める
- 工事の時間を製造部と調整する
突発的な仕事が日常補修の性格なので、電話で即応答するやり取りが多いです。
とりあえず手配することが大事なので、他の仕事は後回しになりがち。
付帯業務をエンジニアが行う余裕は少なく、費用の清算は総務担当者に依頼したり報告書の作成や修理会社に依頼したり…
とにかく手を動かすことなく口を動かすことが多いです。
定期修理の実態
定期修理も日常補修と似たような側面があります。
定期修理で何をするのか?というプランニングが大事ですが、これは中長期的な保全計画を定めるのが普通。
一度計画を定めるとそんなに大きくはずれません。
生産品目が増えた減ったという要因や、生産条件や原料が変わったという要因で、設備の劣化傾向が変わって保全計画を見直すことは発生し得ます。
逆に言うと、保全計画の微修正さえしてしまえばあとは事務的な処理をしていくだけ。
決まりきった事務処理なのでデジタル化・自動化ができる要素だらけ。
でも実際には誰も取り組もうとしません。
要件定義できる人が居ないから。
ここに設備保全エンジニアの存在価値があるはずなのですけどね…。
プロジェクトの実態
プロジェクトは設備設計エンジニアの職務ですが、実態はかなり怪しいです。
- 見積の精度が甘すぎて、実施段階で予算が余りすぎたり不足しすぎたりする
- 機器や配管の仕様はプロセス設計でほぼ決まっている
- P&IDや配管図は図面屋さんが作るので、チェックをするだけ
- 資器材は積算された数量を機械的に手配するだけ
設備保全エンジニアの定期修理作業で事務処理が多いというのと同じで、設備設計エンジニアも事務処理が多い側面があります。
設計のメインでありそうな設計書は実はなくても仕様書さえあれば物はできてしまう。
仕様書も過去の物をコピーすれば、それなりの物が作れてしまう。
P&IDや配管図は図面屋さんにお任せ。特別な指示があればまだいい方で、実態はプロセス設計資料を丸投げするだけ。
メーカーや図面屋さんから質問が来ても、過去の実績集を調べるだけ。
時間を掛けている事務処理の中でも必要な資料を調べるのに時間が掛かるようです。
この資料体系を構築して最速で結果を出すことが設備設計エンジニアの価値でしょう。
でもできる人がほとんどいません。
体系を理解するのに時間が掛かるから。
プロフェッショナルになって要件定義ができるようになるまで10年15年。
そうこうしている間にマネジメント層にあがり、管理業務が増えていく。
機電系エンジニアの実際の対応
化学プラントの機電系エンジニアが実際にどんな対応をしているか、その特徴を紹介しましょう。
- 徹底した受け身
- 依頼内容を理解せずに進める
- 成果を説明できない
機電系エンジニア以外の職務を経験した私から見ると、機電系エンジニアはこういう目で見ています。
徹底した受け身
機電系エンジニアはとにかく受け身です。徹底しています。
- 依頼があれば対応する。
- 言われたことをそのまま行うだけ。
- 質問はほとんどしない。
こういう受け身になってしまうのは実は理由があります。
- 化学プロセスについて知らない
- 依頼者である製造部の説明が下手
- 製造部より学歴が低いという負い目
これらの要素を克服するには経験年数くらいしか現実的ではないでしょう。
成果を積み自信ができて自分の意見が出るようになるまで、5年~10年掛かってしまいます。
特に入社してからずっと機電系エンジニアだけを経験している人は弱いです。
製造部の経験を数年だけでも積んでいる人はこの辺がとても強いですね。成長速度にも明らかに影響しています。
依頼内容を理解せずに進める
機電系エンジニアは依頼内容を理解せずに進めがちです。
というのも化学に対する理解が薄いから。
これは仕方がありませんね。
設備に特化した内容だけを理解して取り組みがちです。
この結果、プロセスの特性や関連性を理解せずに対処療法的な保全や設計をしがちです。
ユーザー系エンジニアならそのプロセスの全容をある程度理解しておきたいのですが、バッチ系化学プラントでは特に難しいですね。
- 生産品目が多い
- 化学構造が複雑
- 反応数が多い
有機化学の世界になると高校化学の世界では太刀打ちできませんね。
製造部のプロセスを理解したいと思っても、日々の業務に追われて理解する時間が無いというのが問題です。
負のローテーション。
成果を説明できない
機電系エンジニアは自分が出した成果を上手に説明できません。
これも理由があります。
- 設備のことを知っている製造部が少ない
- 説明の仕方を知らない
- 業務のポイントとなる部分を理解していない
設備のことを知らない化学屋にとっては、設備が治れば良いと思うのは当然のこと。
これに対応するように「治りました!」という報告だけを繰り返していくと、報告の仕方を学ばないまま経験年数だけが増えていきます。
報告という名の説明をして質疑応答の仕方を学ぶことは、業務スキルを上げる絶好の機会です。
自分が何を説明すればいいのか、どう説明すれば相手は分かってくれるか、試行錯誤の連続です。
この機会が相対的に少ない環境が、機電系エンジニアの置かれている環境です。
業務の本質を考えない社員
化学プラントの機械エンジニアは業務の本質を考えない傾向が強いです。
- 自分から改善案を出さない
- 現状の仕事方法に不満を持っていない
- 採用された改善案を実行しない
- とにかく否定的な意見を言う
簡単に言うと「現状維持」。
現状維持で会社にしがみついている、と言われても仕方ないでしょう。
とにかく手動
昨今、DXが流行っていますよね。
紙で行っていたことを電子化しましょう、自動化しましょうと。
こういう流れがあるにも関わらず、手動にこだわるのが機電系エンジニアです。
Excelでマクロを組むという高等なテクニックは望まない方が良いです。
ブラインドタッチすら怪しいですからね^^
紙の見積書を貰って、電卓を使って査定したりしていますよ。
システム変更の影響を考えない
自発的なシステム開発が望めない環境でも、外発的なシステム導入はされます。
ここで、現状のシステムを考えない機電系エンジニアは、変更後のシステムの弊害を考えることができません。
要件定義ができずに導入されたシステムに対して不満を持ちながら使い続ける。
かえって時間が掛かるが仕方がないという諦めモード。
計器を信じ込む
1つの計器のトレンドだけを、グラフに落とし込み解析するプラントエンジニアが多数存在します。
例えば、流量のトレンドデータを出して、ある点で異常があったからその情報だけを報告する。
こんなプラントエンジニアが多いです。
流量に異常があったとして、その1つの流量計のデータだけを信じることはできません。
流量と液面の情報を合わせたり、複数の計器の情報を総合的に判断することが
プラントエンジニアには求められます。
ここは、まだまだコンピュータの判断が追い付ていない領域。
最近は、ビッグデータやAIも台頭していますが、それでも人が判断することは重要です。
それなのに!
1つの計器だけを信じ込むようなデータつくりをするのは、危険すぎます。
複数の計器の因果関係を考えない
例えば、液をタンクAからタンクBに送る場合を考えましょう。
ここで、タンクBの液面だけのデータを出して議論するのが、上の例。
危険な例。
タンクAの液面の情報があった方が正確性はぐっとあがりますし、タンクAからタンクBへの流量計のデータがあれば、もうほぼ完ぺき。
ポンプで送るのであれば、そのポンプの電流値があれば、素晴らしい。
これだけの情報を集めれば、以下のようなアプローチができます。
- 液面計と流量計の情報を照合することで、何か異常がないか判断が可能
- 電流とポンプの性能曲線から、流量も推定可能
瞬間データの比較だけを行う
バッチ運転なら、例えば1日に1バッチの運転を行います。
ということは1日で1サイクル。
それなのに、10分くらいの詳細データにだけ目を向けて、議論しようとする危険なプラントエンジニアが増えています。
24時間のうち1時間くらいしか使っていないポンプの、1時間での流量を10%程度変えることで、何が問題あるか?
こういう議論の時に、使っている1時間の流量データを眺めて、議論するようなプラントエンジニアがいます。
ところが、24時間のうち23時間は使っていないので、そこで議論する方が速いでしょう。
瞬間データだけを比較せず、全体を見るようなアプローチが大事です。
とにかく否定的
現状維持を好む機電系ンジニアはとにかく否定的です。
改善を遅らせようとする抵抗勢力だらけ。
一気に変えると抵抗が出るからゆっくりと
聞こえはいいように見えますが、実態は先送り・事なかれ主義。
世界一般のビジネスの変わり方に付いていこうとしないぬるま湯思考。
ある書類の手続きで紙から電子化しようとしても、電子化の仕方が分からないからチーム全体では紙を基本にする!
みたいな発想ばかりです。
紙に関していうと、機電系エンジニアは紙を愛していると言っても良いでしょう。
仕事の動き出しが遅い
機電系エンジニアは仕事の動き出しが遅い傾向にあります。
- 人に頼めば後は他の仕事に取り組めたのに、依頼してなかった
- 方針がズレないように最初に認識合わせをすべきなのに、しない
- 催促されないと結果を出さない
こういう傾向は、一定割合で存在します。
別にエンジニアに限らないですけど、近年増加傾向にあります。
依頼を受けて「分かりました」って回答しておきながら、いつまで経っても返事をせずに気が付いたら「できません」というパターンだらけ。
これは自身の立場を理解していなければ、化学プラントの経営的な思考も理解していないからこそでる結果です。
頭の中にある発想はこんな感じでしょう。
- 正式な資料が無いと、動かなくていい
- 適当な回答をすると後で痛い目を見るから、時間を掛けて回答したい
- 納期ギリギリに対応すればいい
実際には忙しくて考える余裕がないというのが背景にあるでしょうが、言い訳に見えますよね。
製造部としては以下のような想いを持って機電系エンジニアに依頼を掛けますが、この想いは理解されないでしょう。
- 概算でもいいから(間違っていても良いから)、速報が欲しい
- 大きな方針はできるだけ早く決めたい
- 期限管理のような業務管理はできるだけ減らしたい
タスク管理ができない
一部のエンジニアはタスク管理そのものができません。
エンジニアというか社会人としてどうなの?っていうレベルです。
新入社員ならタスク管理って難しいですよね。
メール・紙・口頭・・・いろいろな形で仕事が来て、期限をいつに設定して、何をいつまでに実施するかのプランを立てないといけません。
ここには依頼元の要求を読み取ったり、自身の業務内容をしっている必要があります。
でも一定の年数を経ってもタスク管理ができない人は居ます。
- 何度言っても最小限の仕事しかしない人
- 今日明日の仕事内容しか考えれない人
- 非常に細かいところにしか目が行かず全体を見れない人
- 業務管理表を作れない人
日本を代表するような大企業でもこういう社員は存在します。しかも少数ではありません。
2:8の法則とかパレートの法則とか言われる現象そのもの。
関連記事
さらに知りたい方は、以下の記事をご覧ください。
最後に
ユーザー系エンジニアの技術的能力の実態についてまとめました。
日常補修・定期修理・プロジェクトのいずれのサービスでも付加価値はあまり高くありません。
仕事内容を理解せずに手配屋になる傾向が高いからです。
経験年数を積めば成長して本質を考えて改善する人もいますが、どちらかというと現状維持を好む人の方が多いでしょう。
化学プラントの設計・保全・運転などの悩みや疑問・質問などご自由にコメント欄に投稿してください。(コメント欄はこの記事の最下部です。)
*いただいたコメント全て拝見し、真剣に回答させていただきます。
コメント