蒸気を使う設備では「スチームトラップ」という部品が欠かせません。でも、「どの種類を使えばいいの?」と悩んだことはありませんか?
この記事では、特によく使われるディスク型とフロート型のスチームトラップに絞って、構造や動作の違い、そして現場での使い分けのポイントをやさしく解説します。
省エネ・カーボンニュートラルで話題となるスチーム。せっかくエネルギーを使って生成したスチームを無駄に捨てないようにするために、スチームトラップはとても重要です。
ディスクかフロートか。これだけです。
ディスク
まずはディスク式について解説します。
ディスクは蒸気とドレンの熱力学的性質を利用したもの。
何のことか良く分かりませんよね。
結局は圧力の話になります。熱力学的性質というからややこしくなるだけです。
少し解説を進めましょう。
構造
ディスク式は以下のような構造をしています。
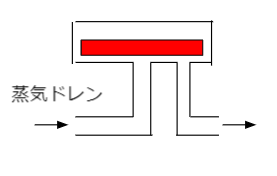
蒸気ドレンが通る道のある部分に、ディスク(赤部分)があります。
このディスクが弁としての開閉機能を持っています。
蒸気を通し始めてから、トラップが作動するまでのプロセスを見てきましょう。
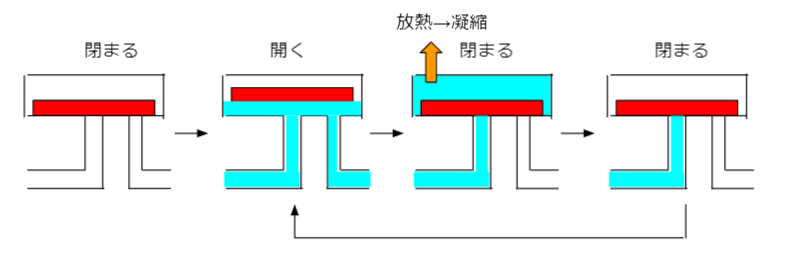
ステージ1:空状態
最初は蒸気が通っていない空の状態です。
この状態ではディスクは閉まった状態です。
ディスクの上面も下面も空気で満たされた状態で、ディスクに掛かる力とディスクの重みで下に押されている状態です。
ディスクの上面と下面で圧力を受ける面積が大きく違うのは、
下面がケーシングと接触する割合が大きいから。
言い方を変えると、ドレンが通る面積が少ないから。
ディスクの上面と下面で圧力を受ける部分は、下の図のように大きく変わります。
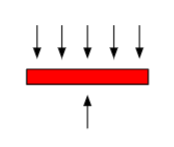
上面も下面も同じ空気の圧力を受けていると、下面に押される力の方が当然大きくなります。
これにディスク自身の重力も加わるので、ディスクは当然閉まる方向に動きます。
ステージ2:ドレン排出
蒸気を使い始めて、ドレンが発生した時の動きを見ましょう。
ドレンは蒸気の圧力を付加された状態で、高い圧力を持っています。
ディスクの下面にドレンの圧力が加わり、上面には空気の低い圧力しか加わっていません。
ここで
(ディスクの重み) < (ディスク下面の力) – (ディスク上面の力)
となれば、ディスクは浮きます。
ディスクが浮くと、ドレンは外部に排出されます。
ステージ3:凝縮開始時
ステージ2の段階になると、その瞬間にステージ3が発生します。
この状態ではディスクが収まっている部屋はドレンで満たされます。
ドレンで満たされた瞬間に、(ディスクの重み) < (ディスク下面の力) – (ディスク上面の力)という力関係は破綻して、
(ディスク上面の力) > (ディスク下面の力)
(となります。
ディスク上面の圧力) = (ディスク下面の圧力)だからです。この結果、ディスクは下がっていきます。
ディスク上面はドレンだけで満たされることは無く、蒸気を含みます。
この状態でずっと放置していると、蒸気はドレンに変化します。
外部に熱が放散されるからです。
蒸気がドレンに変化すると、圧力は急に減少します。
体積が急に減少するからですね。
ステージ4:凝縮完了時
ステージ4はステージ3とほぼ同じ段階です。
ステージ3で蒸気が凝縮していきますが、それが終わると圧力は極端に少なくなります。
この瞬間にステージ2に戻ります。
トラップ入口のドレンの圧力でディスクは開く方向に動きます。
このステージ2~4を繰り返すことで、ドレンを排出するディスク式スチームトラップは機能します。
凝縮という工程を含むから「熱力学的性質」と呼んでいます。
実際には、蒸気やドレンの圧力でディスクの上下をしていますよね。割と単純ですよ。
トレース・配管スタンド上向け
ディスク式はトレース用のトラップや配管スタンド上のトラップに向いています。
これはディスク式の方がフロート式よりも小容量向けであることと、寿命が相対的に長いからです。
トレースや配管スタンド上では蒸気ドレンの発生量が少なく、フロートにする必要性があまりありません。
また、ディスク式のメリットは寿命の長さにあります。
スチームトラップの寿命を決める要素は摩耗です。
長いこと使っていくうちに摩耗ですり減っていくと、トラップは使えなくなります。
- 150℃以上の高温
- 30m/s程度の高速
- ウォーターハンマーもある
こういう条件で使うので、スチームトラップは過酷な使用条件と言えます。
ディスク式の場合は、以下の要素が摩耗と関係します。
- ディスクがスチームから受ける力
- ディスクが落下してケーシングに衝突する力
ディスクがスチームから均等な位置に力を受ければ、ディスクはそのまま垂直移動を行います。
3点で力を受けるとバランスが取れるというのは、剛体の基本ですね。
仮にある1点だけでスチームの力をディスクが受けた場合、ディスクには回転モーメントが加わります。
これがディスクの偏減りを呼びます。
最近のディスク式では対策が取れていますので、積極的に使用したいですね。
フロート
フロート式は密度差を利用したものです。
ディスク式に比べても単純です。
原理
フロート式のイメージを下に示します。
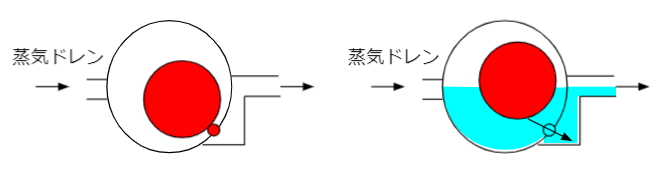
フロートという浮きがあって蒸気ドレンという液体に対して浮いて蒸気という期待に対しては沈むというフロートの構造をしています。
フロートが沈むとケーシングのオリフィスを閉めて、フロートが浮くとオリフィスを開くという機構を持ちます。
単純ですね。
大容量向け
フロート式は大容量向けです。
装置の昇温用として大活躍します。
設計指針
フロート式の設計は使用量・使用圧力は装置の運転条件で決まります。
反応槽のジャケットをスチームで温める場合は、以下の要素が大事です。
- プロセス液の顕熱
- 温度上昇速度
- プロセス液の潜熱
特に重要なのがプロセス液の潜熱。
蒸留などで炊上速度を決めるために必要となります。
炊上速度にはスチームの流量だけでなく温度も関係するので、反応条件を適切に設計する必要があります。
そこで決まる使用量・使用圧力に対して、2~3倍の余裕を見た数値をメーカーに提示すると良いでしょう。
バッチ系化学プラントでのスチームトラップ(steam trap)の使用場所
バッチ系化学プラントで使用するディスク式とフロート式のトラップの使用場所を紹介します。
大半はディスク
バッチ系化学プラントで使用するスチームトラップの大半はディスク式です。
というのも、ほとんどすべての場所は主管やトレース配管だから。
主管やトレース配管で発生するドレン量は少ないので、ディスク式で対応できます。
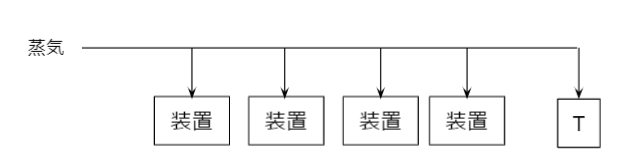
スチームトラップと言えばディスクと妄信するエンジニアが大量発生するくらい、ディスク式は圧倒的に使用します。
装置周りはフロート
フロート式は装置周りに使用します。
これはドレン発生量が多いから。
ディスク式とフロート式の使い分けは、ドレン発生量にあります。
ドレン発生量で比較するとディスク < フロートとなります。
装置周りではフロートを使うのが無難です。
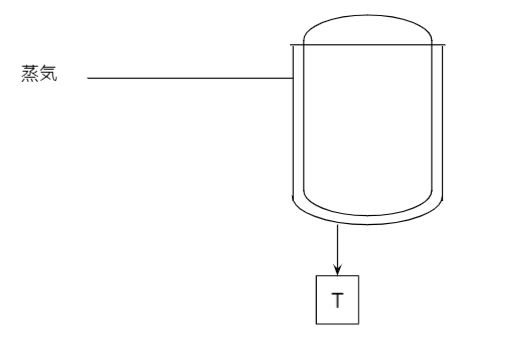
バッチ系化学プラントでは装置周りに使用する蒸気として、500kPaG×500kg/hという条件が付くことが多いです。
カタログスペック上はディスク式でも対応できそうな気がしますが、これは危険。
スチームトラップでは余裕率を2~3倍取るのが普通です。
500kg/hだと3倍の余裕率を取って1500kg/hと考えた瞬間に、ディスク式は使えないという判断になります。
バッチ系化学プラントでは汎用的な設計思想を好むので、特定の条件で500kPaG×500kg/hであったとしても、他の製品では蒸気圧力や使用量を上げたいという場合は多いです。
500kg/hだからディスクでも運良く対応できていた場合でも、新製品を入れた時に使用量が増えて、フロート式にすべきだったのにディスク式のままで使用して問題になった。
こんなケースは山のようにあります。
スチームトラップ(steam trap)配管の組み方注意点
スチームトラップの配管を組み際にはいくつかの注意点があります。
トラップ配管とバイパス配管
トラップを付ける箇所にそれぞれバイパスラインを付けることになります。
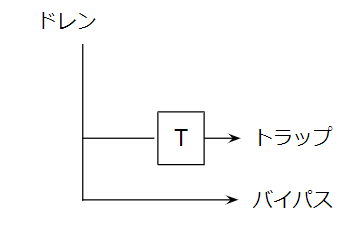
スチームトラップ配管は結構詰まります
鉄配管中の錆を拾うからです。
トラップにバイパスを付けておき、錆をブローできるようにしておきましょう。
SDMなど停止時に活躍します。
トラップとバイパスの位置も大事で、バイパス側が主管・トラップ側が枝管となるようにします。
これも錆を極力トラップ側に行かせないため。
水平配管と垂直配管
トラップは水平配管と垂直配管のどちらに付けるかによって種類が変わります。
普通は水平配管中に付けると思いますが、垂直につける場合はこういう絵になります。
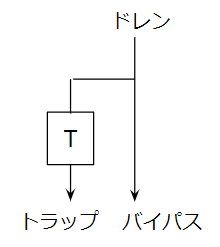
省スペース化
トラップは1つの装置でも複数個設置することが多いです。
この場合、以下のようなヘッダー的な配列を組むことが考えられます。
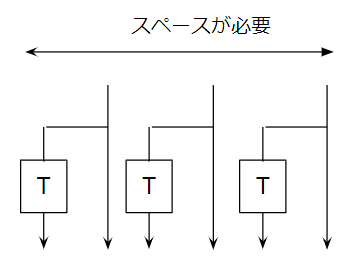
これ結構なスペースを取ります。
配管設計の立場からすると邪魔な存在です。
トラップ1個に対してバイパスが必ず必要なので2本の配管が、順次並んでいく。
これを回避する一つの方法が段を変えるという方法です。
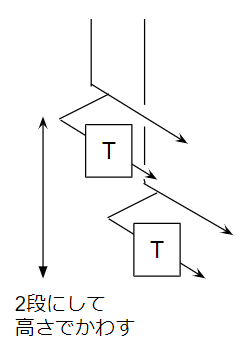
この例は水平にトラップを組んだ時に、高さでかわすという発想です。
トラップは何も考えない場合は床面+100mmくらいで組むでしょう。
地面近くに配管を添わせる地這い配管にしやすいからですね。
ところが床面+500mmでもおかしくはありません。
2段にしても、上段側のトラップは作業性にはあまり影響がなく、課題となりそうな下段側のトラップが適切に点検修理できれば大丈夫です。
2段と言わず3段でも組むことは不可能ではありません。
こうすることでスペースを有効活用できます。
垂直配管でトラップを組んだ場合は、高さでかわすことが非常に難しいです。
というよりできないと思っていた方が良いでしょう。
ドレン回収配管は開放させる
ドレン回収配管を集合管にまとめる場合、いったん解放させましょう。
開放させずに連結させる場合がたまにあります。
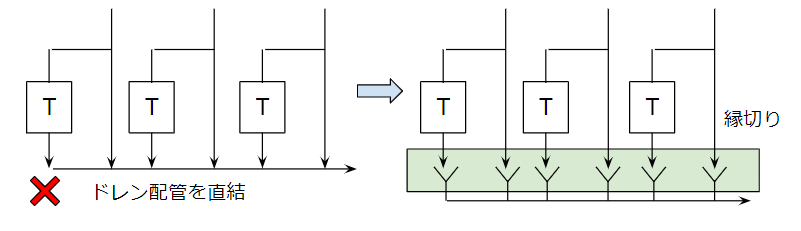
でも運転管理を考えると、集合管に接続する前に開放させるべきです。
トラップから集合管にそのまま連結すると、どのトラップが壊れているか分からなくなります。
手で触って確認するなどのアナログな方法になるでしょう。
それを定期的に行わないといけません。
でも縁を切っていたら、パトロール中に目で見たら分かります。手間が一つ減ります。
ドレン配管を1本にまとめると言っても、トラップ・バイパスの1セットと配管を連結させる必要はなく、ちょっとした工夫で縁を切るだけでも効果は絶大です。
省エネ化の面からも運転管理の面からも、確実に点検できるようにトラップと集合管の間に開放部を設けるべきです。
参考
関連記事
さらに知りたい方は、以下の記事をご覧ください。
最後に
スチームトラップは、蒸気設備の効率と安全性を左右する大切な部品です。
ディスク型はコンパクト・低コスト重視向き、フロート型は安定したドレン排出が必要な現場向きという特徴を押さえて、うまく使い分けましょう。
トラップとバイパスを水平取り付けでくみ上げていき、回収管手前でいったん縁切り開放すると良いでしょう。
化学プラントの設計・保全・運転などの悩みや疑問・質問などご自由にコメント欄に投稿してください。(コメント欄はこの記事の最下部です。)
*いただいたコメント全て拝見し、真剣に回答させていただきます。
コメント