プラントライフサイクルについて考えてみます。
実施にこの単語を意識して仕事をしている人は、残念ながらほとんどいないでしょう。
特にプラント保全担当者だと、現場仕事に追われて対応する暇がありません。
どちらかというと生産企画系の話題です。
ですが、現場の保全レベルでも本当は知っておきたい内容です。
「緊急ではないが重要」というカテゴリに入る内容です。
設備の寿命
保全担当者がプラントライフサイクルについて考えるとき、真っ先に思いつくのは設備の寿命です。
新しく買った設備が何十年持つのか
設備を持たせるためにどういう保全をすればいいのか
リソースはどうやって確保しようか
こういった議論が必要なはずですが、そこまでしっかり議論できている会社は少ないと思います。
- 今の設備をとにかく長持ちさせるために手を打つ
- 生産を止めないように応急補修をする
- SDMでしっかり整備をする
こんな展開が99%以上を占めると思います。(弊部もそうです)
だから「この設備が何年まで持つのか?」ということを答えることは難しいです。
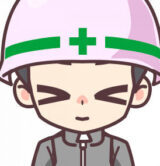
設備によって変わるから・・・
プラントの運転方法によって変わるから・・・
メーカーが部品供給停止したりするから・・・
こんな感じで、良く分かりませんという対応をすることになります。(弊部です)
現実的にはいろいろなファクターがあって予測できないのが設備寿命。
と言いたいところですが、第一ステップとしてはそんなファクターは考えずにまとめて考えれば良いでしょう。
設備を更新したときに「更新前の寿命」のデータを集めるだけ。
数が集まって統計的なデータになれば、それなりに信頼性が上がってきます。
人間の寿命でも同じような感じですよね。
工場内の各プラントにある設備の寿命を地道に集計していくだけ。
その作業が面倒だからといった理由で進まなかったりします。
生産技術よりも固定資産を管理する生産管理が、集計した方が良いかもしれませんね。
プラントの寿命
プラントライフサイクルを考えるとき、設備の寿命だけに着目してはいけません。
電気や計装も寿命を考えないといけません。
電気室内の盤関係はもとより、ダクトなどフィールド内の設備もそう。
各種計器や調整弁などもそう。
でももっとクリティカルなものがあります・・・。
それが土建。
道路くらいなら舗装を計画できますが、土壌は厄介です。
地盤沈下がしやすい環境なら、土の中がスカスカになっていてどうやって補修するかという課題がでます。
もっとクリティカルなのが架構そのもの。
長いこと使っていて、柱や梁が腐食していったり、建築基準に適合してなかったり・・・。
補強もできない修理もできないので、スクラップビルトしかない。
という判断をどこかでしないといけません。
建物としての設備診断をするのはとても難しいでしょう。
特に化学プラントのように一般建築物とは違う腐食環境下にある場合では。
このデータは設備の寿命よりも数少ない貴重なデータになります。
保全費用は下がらない
プラントライフサイクルを考える上で、保全費用は下がらないという前提はとても大事です。
一般的に知られているバスタブ曲線を使って、解説しましょう。
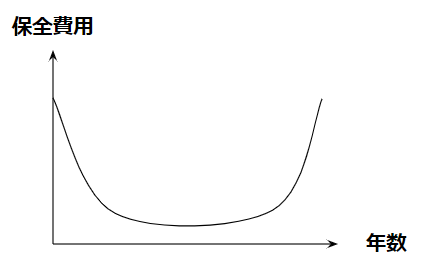
このように初期故障・偶発故障・摩耗故障というような3つのフェーズに分けて、保全費用がシフトしていくイメージです。
概要としてはこれで良いのですが、実際の保全では以下のような対応をされていると思います。
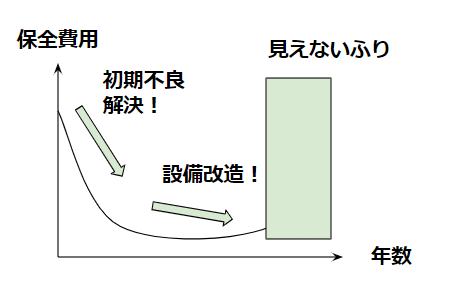
保全の努力によってとにかく費用を下げていくだけ。
初期不良の早期解決は当たり前。
偶発故障期に至っても、TPM的な設備改善を地道に繰り返していくことで少しずつ寿命を延ばしていく。
摩耗故障期はなかったことにする。
こういう感じだと思います。
設備が寿命を迎えそうになって、更新が必要ですと工場に訴えても「金がない。現状を維持せよ。さらなる努力で寿命を延ばすこと」というような回答が来ます。
摩耗故障期という概念を理解したとしても、保全費用を上げるという流れは難しいと思います。
現在割り当てられている保全費用の中で優先順位を付けて、摩耗故障期の設備を先に補修して偶発故障期の設備に我慢してもらう形をとると思います。
そうこうしている間に、時代は変わっていきます。
労務費・資材費の高騰や長納期化などのファクターが顕著になっているからです。
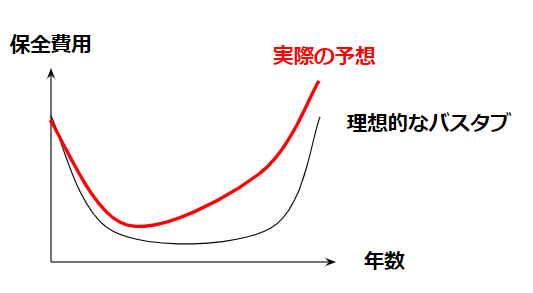
初期不良段階から保全費用は上がっていきます。偶発故障期の長期間の間には年々上がります。
これまで同じ発想で設備の寿命を定めたとしても、費用高騰の影響を考えると実は実績寿命よりも前に更新する方がお得、というケースが考えられます。
保全が生産技術を名乗るにはこの辺りの解析が必要と思います。
そうでなければ製造管理の一環としての設備管理のポジションになるでしょう。
保全を意識した設計を
保全にだけスコープを当てているように見えますが、設計もプラントライフサイクルに対して良く考えないといけません。
設計はプラント建設や合理化の大きなプロジェクトで、設備を導入します。
ここで保全を度外視した設計が往々にして行われます。
ポンプの仕様を個別最適設計して、予備品がバラバラ
配管は1円でも安い仕様にする
プラント内の配管を全部溶接して、後で取外しができないようにする
設備の更新のために、障害物が多すぎて費用と工期が掛かるプラント設計にする
これらの例は本当に多いです。
保全や運転を知らずにいきなり設計をしてしまうと、無理はありません。
上流のプロセスエンジニアも同じような思想が多いと思います。
機電系エンジニアとして設計を担当するなら、保全の立場に立った設計をしてほしいものです。
保全をしっかり意識した設計であれば、保全に掛かる費用を長期的に下げることができます。
建設当初のイニシャルコストを下げることで、ランニングコストを度外視せざるを得ないかもしれませんが、ちゃんとしたコスト比較ができれば説明はつくはずです。
問題はランニングコストを設計者が適切に評価できないこと。保全者に依頼しましょう(保全も無理かもしれませんけど・・・)
参考
関連記事
関連情報を知りたい方は、以下の記事をご覧ください。
最後に
プラントライフサイクルについて、生産技術職lの保全担当者が考えたいプラント寿命や保全思想を解説しました。
設備の寿命のデータを適切に集めていくことから始まります。
最終的には土建の寿命予測にたどり着きます。
バスタブ曲線の考え方や推移を適切に評価していきましょう。
保全を楽にする設計を意識しましょう。
これらは保全だけ・設計だけの思想では対応できません。お互いの領域を理解していないと難しいでしょう。
化学プラントの設計・保全・運転などの悩みや疑問・質問などご自由にコメント欄に投稿してください。(コメント欄はこの記事の最下部です。)
*いただいたコメント全て拝見し、真剣に回答させていただきます。
コメント