撹拌機のフローパターンに関する知識を紹介します。
化学プラントの機電系エンジニアにとって、撹拌機や撹拌槽はなじみの深い設備です。
でも、撹拌って真面目に考えたことがあるでしょうか?
撹拌機という機械的な部分に興味が行ってしまい、化学工学的な部分は疎かにしがちです。
もしくは反応に固有の技術なので、研究段階で決まってしまったり、前工程のプロセスエンジニアによって決まることも多いでしょう。
メーカーに依頼しても、研究者とメーカーが直接打ち合わせすることになって、機械エンジニアが立ち入る場面がないことも多いです。
だからといって、撹拌機を知らない機械エンジニアは、化学プラントとしては疑問符が付きます。
ですので撹拌機の基礎的な部分は理解しておきましょう。
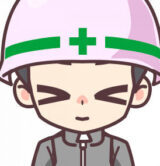
撹拌機は奥が深すぎるので、専門家に任せましょう
撹拌能力の性能
撹拌の能力を示す性能って何でしょうか?
ゼロベースで考えると意外と困ります。
いくつかの指標がありますので、見ていきましょう。
撹拌動力
撹拌能力の性能を示す最大の指標は撹拌動力です。
特にバッチ系化学プラントでは「撹拌性能=撹拌動力」と考えて良いレベル。
これはスケールアップと関連します。
フラスコレベルの実験で起こった現象を実装置で再現できるか?
というのは化学プラントの研究と現場の間で問題になります。
というのもスケールアップでは、すべてのファクターを相似形にすることはできず何かを犠牲にしないといけないから。
化学反応を考えた時に各種要素と寸法とには一定の関係があります。
- 取扱量は体積に関係
- 熱制御は面積に関係
- 反応速度は比表面積に関係(するかもしれない)
- 気液反応は界面に関係(するかもしれない)
1乗で効いてくるのか2乗で効いてくるのかはさまざまですが、物理的に関連するのは直感として分かると思います。
ここで大事なことは、スケールアップをすると面積・体積の比が変わるということ。
球を考えれば分かりやすいです。
球の表面積は4πr2、体積は4/3πr3。
rを2倍にしたら表面積は4倍、体積は8倍になります。
この瞬間に表面積と体積を同じ関係でスケールアップすることはできません。
スケールアップをするときに伝熱性能を合わせようとすると、反応などの別の要素が会わなくなってきます。
これらの複数の要素を何となく均一に合わせようとするのが撹拌動力
撹拌動力/容積を一定にすればスケールアップをしてもだいたいの要素が揃うという慣例があります。
吐出流・循環流
撹拌機である以上は液の流れは一つの指標です。
撹拌機の世界では吐出流・循環流という2つに分けます。
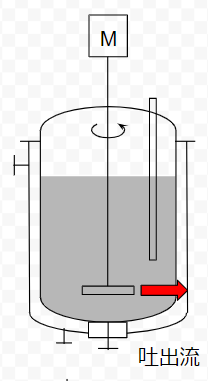
吐出流は撹拌羽根から直接吐き出される流体の流れです。
循環流は吐出流の周囲で吐出流の流れに伴って発生する流れです。
撹拌が回る → 液が半径方向に動く(吐出) → 液が分散する(循環)
というイメージで良いと思います。
お風呂場で手でお湯をかき混ぜたりすると、この辺のイメージは何となくつかめると思います。
吐出流と循環流の定性的な関係性を示します。
羽根の形状が吐出流に影響する
吐出流が速いほど循環流は速い。
吐出流が撹拌容器全体に回る流れであるほど、循環流も大きく均一な撹拌が可能。
流速の視点では吐出流や循環流が速いほど良さそうに見えますが、必ずしもそうではないところが問題です。
せん断速度
せん断速度も撹拌の性能の1つです。
せん断速度は羽根先端部での速度そのものです。吐出流とかなり関連があります。
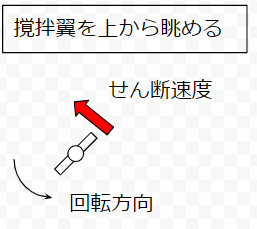
せん断速度は本来は流体力学や材料力学で習う概念ですね。発想は同じです。
撹拌におけるせん断速度は羽根径と回転数でほぼ決まります。
せん断速度が速い → 吐出流が速い → 循環流が速い
という関連性は体感的に理解できると思います。
羽根径が大きいほどせん断速度が速くなるので、スケールアップをするときには回転数を犠牲にするという思想になるでしょう。
フローパターン
撹拌による液体の流れ(フローパターン)を少し見ていきましょう。
撹拌羽根の形状に大きく影響します。
撹拌羽根の形は色々ありますが、例えばパドル・ディスクタービン・プロペラなどが汎用的です。
吐出流の方向が羽根の形状によって半径方向と垂直方向に分かれます。
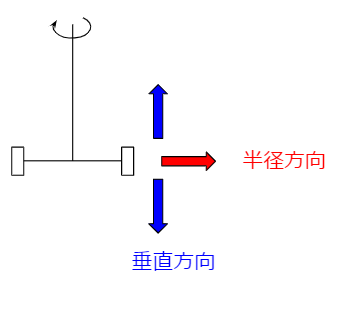
- 垂直パドル・平羽根ディスクタービンは半径方向
- プロペラは垂直方向
半径方向
半径方向の吐出は直感的にも分かりやすいでしょう。
羽根が回る → 遠心力で液体が半径方向に押し出される
羽根の向きは垂直方向・水平方向・斜め方向などいろいろな向きに設定可能です。
羽根の向きを垂直向きにすると半径方向の吐出が最大となります。
この分だけ垂直方向の吐出は弱くなります。
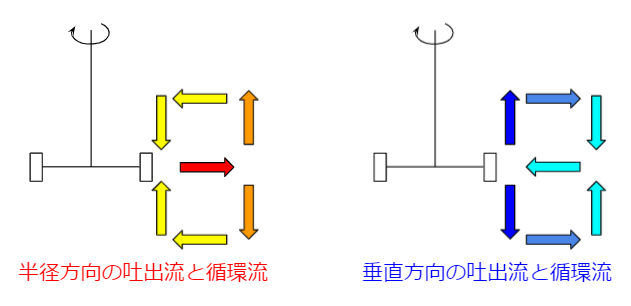
垂直方向
プロペラ翼などでパドルとは正反対で吐出流は撹拌軸と同じ垂直方向に流れます。
垂直の流れが強いということは、タンク下部に液体を吐き出そうとする流れです。
スラリーの堆積などを嫌うために、バッチ系化学プラントではあまり使用されません。
羽根の位置
フローパターンと羽根の位置は密接に関係します。
羽根がタンク底に近いと、上下の流れのバランスは変わります(吐出流でも循環流でも)。
これは羽根がタンク底に近いほど下側の流れがタンク底とすぐにぶつかるからですね。
羽根をタンク上部・中部・下部というように数段に分けて配置して均一な流れを設計しようとする場合もあります。
固体うず域と準自由うず域
フローパターンは撹拌羽根がある部分とない部分で分かれます。
タンクを水平方向に切った断面を見てみましょう。
うず流と呼びます。
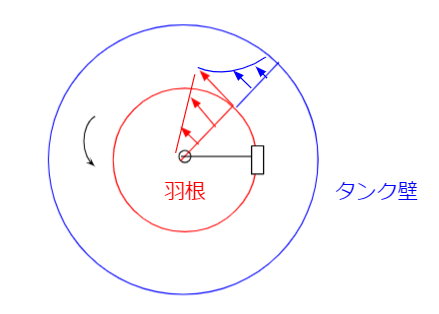
固体うず流と準自由うず流と区分します。
固体うず流は撹拌羽根の動きと同じ速度で流れる流れです。
撹拌羽根が通る部分は固体うず流として考えられます。
うず流の速度は羽根の径と回転数に比例する直線関係と考えると分かりやすいでしょう。
準自由うず流は、撹拌羽根とタンクに囲まれた領域の流れです。
撹拌羽根先端の吐出流が駆動力であり、タンク壁が固定されています。
固体うず流のように羽根の径や回転数の要素だけでなく、液体の密度や粘度などの影響を強く受けます。
粘度が高い方が吐出流が弱く、準自由うず流はすぐに減衰します。
タンクを垂直方向に切ったときも同じような発想で考えることができ、撹拌による液の盛り上がりを議論することがあります。ボルテックスなどと呼びますね。
撹拌条件と邪魔板
撹拌機には邪魔板がつきものです。
邪魔板の効果を改めて確認しましょう。
- 準うず流領域の減少
- 循環流の変化
固体うず流や吐出流という撹拌による液のシンプルな流れを、意図的に変化させようとする効果があります。
フローパターンを複雑にすることで、液の流れを均一にして速やかに撹拌できる効果を期待しています。
その分だけ撹拌動力が増える方向になります。
身近な例では以下を考えると良いでしょう。
- コーヒーにミルクを入れてマドラーで撹拌するだけの状態が邪魔板なし。
- マドラーで撹拌して液の流れができているときに、マドラーを止めるとマドラーが邪魔板扱い
無邪魔板での撹拌条件
攪拌機の設計条件として撹拌羽根の寸法があります。
邪魔板が無い条件での撹拌羽根の寸法として、一般に下記の条件が適切だと言われています。
撹拌羽根の幅 | 撹拌槽の径×1/3 |
撹拌羽根の高さ | 撹拌槽の径×0.05~ 0.1 |
撹拌羽根の傾き | 撹拌羽根の幅×1/4 |
実務的にはユーザーが設計することはほとんどなく、攪拌機メーカーに依頼することになるのであまり意識はしないでしょう。
完全邪魔板での撹拌条件
邪魔板がある場合の撹拌羽根の条件は、邪魔板が無い時とくらべて当然変わります。
この最適条件が完全邪魔板条件と呼ばれるようです。
数学的・化学工学的な知見をあまり深掘りしても実務ではなかなか使えません。
完全邪魔板条件はディスクタービンやパドルを対象にしています。
- 撹拌速度は邪魔板が無い時の2/3程度
- パドル翼の幅は撹拌槽の径×1/2
専門的なデータが多く、各社でデータを蓄積していることでしょう。
ユーザーレベルではメーカーにお任せとなりがちで、メーカーのラインナップから最適な撹拌羽根や邪魔板を選定するということになります。
粒子の浮遊
バッチ系化学プラントではスラリー系を多く扱うため、粒子の浮遊は検討対象です。
槽の中で固体の入った液体を撹拌した時に、2つの状態を分けて考えます。
- 固体粒子が単に浮いている
- 固体粒子が均一に分布している
固体粒子が浮くだけで良ければ単に撹拌をし続ければ解決する可能性が高いです。
ここに均一な分布という条件が加わることで、攪拌機としての設計が必要となります。
撹拌速度と溶解速度の関係
スラリー液は撹拌をしないで静置していると、固形分が沈降しようとします。
この沈降速度はスラリーの性能によって大きく変わります。
さて、この状態で撹拌翼を動かすとどうなるでしょうか。
- 撹拌速度が低い時は、部分的に浮遊する。
- 撹拌速度が高く時は、全ての粒子が浮く。
何となく理解できると思います。
撹拌速度が低いと吐出流も循環流も弱く、撹拌羽根の近傍だけがフローパターンができます。
その他部分は静止した液と同じ状態。
液が動くことで固形分が浮遊したとしても、止まっている部分はそのまま。
撹拌の速度をあげていくと、どこかでタンク内の全固形分が浮きます。
浮遊限界撹拌速度
タンク内の固形分が全て浮くときの撹拌速度を浮遊限界撹拌速度と言います。
邪魔板が無い条件の定義のようですが、あまり意識しなくて良いでしょう。
固形分が浮くかどうかという視点では、撹拌機の形状・固体粒子径・固体密度・固体嵩密度・液体密度・液体粘度など様々な要素に依存しますが、直接的な運転面では吐出速度です。
吐出速度をあげるためには以下の要素が考えられます。
- 撹拌羽根の径
- 撹拌羽根の形
- 撹拌羽根の回転速度
メーカーのラインナップのうちから、最適なものを選ぶときの設計思想として大事なポイントです。
バッチは液液撹拌
撹拌機では何を撹拌するか?が第一にあります。
バッチ系化学プラントでは下記の4種類のどれかに該当します。
- 均一の液体(液)
- 不均一の液体(液液)
- 液体と気体(気液)
- 液体と固体(固液)
均一の液体
均一の液体は反応プロセスではほとんどあり得ません。
均一の液体を溜める装置として、原料タンク・回収タンクなどが該当します。
これらは反応の前後で必要な物ですね。
反応前には原料が必要、反応後には回収が必要。
そういう均一の液体には基本的には撹拌機を付けません。
不均一の液体
不均一の液体は撹拌が必須です。
バッチ系化学プロセスのほとんどはこれに該当します。
反応が起こると、普通は水層と油層の2層が形成されます。
そのうちの一方が目的物で、他方が不純物のケースが多いです。
反応自体で攪拌機が必要ですが、その後の洗浄処理でも攪拌機は必要です。
例えば反応後に水層と油層ができたとして、水層側が目的物で、反応後に油層を外部に排出するとしましょう。
単純に分液が終わって水層だけが残ったら、そのまま次の反応をするでしょうか?
必ずと言っていいほど、洗浄処理をします。
残った水層に、新鮮な油を投入して、撹拌機で混ぜます。
その後で、また油を分液します。
これを何回か繰り返して、所定の組成になった後で、次の反応を行います。
このため、撹拌機は反応プロセスではほぼ必須です。
大半は、標準的な撹拌機を使用します。
液体と気体の撹拌
液体と気体が関係する反応は、一部に該当します。
バッチ系化学反応では、反応時にガスが発生するためにガスを排出することは話題になります。
液体と固体の撹拌
液体と固体の撹拌も、バッチ系化学プロセスでは非常に多いです。
晶析で使用します。
これも攪拌機の性能が重要です。
とはいえ、撹拌機は標準的な物を使用することが多いです。
固液撹拌の晶析は、気液撹拌の特殊反応よりは、使用する数が多いです。
その晶析のために、特殊な撹拌機を使うのはリスキーです。
バッチ系化学プラントでは汎用性が求められます。
低粘度液が多い
バッチ系化学プロセスでは100mPa・s以下の低粘度液が多いです。
特に10mPa・s以下が多いです。
低粘度液であるというために、撹拌機に求められる性能も自然と固定化されます。
参考
関連記事
さらに知りたい方は、以下の記事をご覧ください。
最後に
攪拌機のフローパターンについて解説しました。
吐出流/循環流、半径方向と垂直方向のフローパターン、固体うず流・準自由うず流、邪魔板条件、固体浮遊。
難しい分野なので撹拌機メーカーにおまかせになりがちですが、設計思想の基本は押さえておきましょう。
化学プラントの設計・保全・運転などの悩みや疑問・質問などご自由にコメント欄に投稿してください。(コメント欄はこの記事の最下部です。)
*いただいたコメント全て拝見し、真剣に回答させていただきます。
コメント
連続運転している晶析槽でプロペラ翼の攪拌方向を逆方向にすることで槽内全体にスケーリングが発生することは考えられますか?
昨年設計上回転方向が逆だったと判明し従来とは違う方向にしました。運転上他の計器も変更しているため解明が難航しています。
コメントありがとうございます。
撹拌翼の回転方向は晶析にとってはとても大きな変更要因です。
スケーリングは十分に考えられるでしょう。