多管式熱交換器(シェル・アンド・チューブ式)は、化学プラントで最も一般的に使用される熱交換装置の一つです。中でもコンデンサー用途として用いられるケースは多く、特にバッチ系プラントではその設計がプロセス効率に直結します。
本記事では、固定式チューブシートタイプの多管式熱交換器(特にコンデンサー)を対象に、バッチ系プラントでの実用的な設計ポイントを初心者にもわかりやすく解説します。
機械系エンジニアが最も設計しがいのある設備とも言えます。熱交換器ハンドブックを使ったり、最近では専用の解析ソフトを使ったりしますが、その前に基本的なことを理解しておくべきです。膨大な情報量のハンドブックからどこを参照すればいいのか分からなかったり、ソフトにお任せで結果を検証できなかったり・・・
今回の内容だけを理解していれば、バッチ系化学プラントの多管式熱交換器の設計には十分に対応できるでしょう。
多管式熱交換器は固定式が基本
多管式熱交換器にはいろいろな種類があります。
それを一目見ただけでも、やる気を削がれがち。
とはいえ基本となるものは数少ないです。
特にバッチ系化学プラントでは固定式だけを理解してれば十分です。
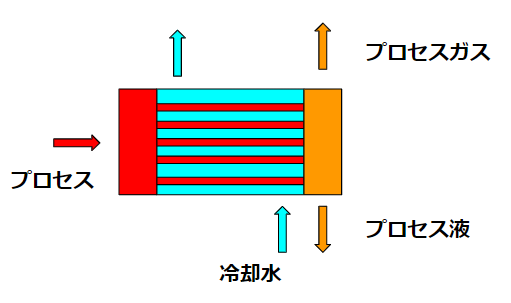
このタイプの熱交換器が工場内の99%以上を占めます。
固定式を使うにはいくつかの理由があります。
- 温度変化が少ない
- シェル側の洗浄をする必要が少ない
- 設置場所が狭い
- シール性が高い
例えば、固定式ではなく遊動頭式ではシェル側の洗浄も目的としていますよね。
チューブの抜出のためのメンテナンススペースなんていう表現で、バッチ系化学プラントでも設計時にも考慮されます。
これは遊動頭をイメージしています。
固定式ではチューブの抜出はそもそもできませんが、チューブの内部点検用にカメラを挿入する場合はチューブの抜出と同じようにメンテナンススペースが必要です。
固定式だから遊動頭式だから・・・といって、機器設計や工事設計で大きな影響がでるわけではありません。
固定式は遊動頭式よりも、グランドシールを使わない分だけシール性が高いのもポイントですね。
だからこそ、基本である固定式だけを理解していれば、十分に応用に耐えれますよ!
管内か管外か
コンデンサータイプの多管式熱交換器とまで仕様を限定しても、管内冷却か管外冷却かという問題があります。
管内冷却か管外冷却かを選ぶには以下のような要素を考えます。
- 材質
- プロセス液と冷却液の洗浄性
- 交換熱量
これらを具体的に見ていきましょう。
管内の設計項目
多管式熱交換器では管内と管外という2つの要素に対して設計をします。
それぞれについて考えるべきことを整理しました。
材質
真っ先に考えるべきことは材質です。
これは無意識でいる人もいるでしょう。
機器の詳細設計をする前の基本設計の段階で決まっていますからね。
この材質決定が、多管式熱交換器の設計において大きなウェイトを占めることを強調したいです。
グラスライニングなどの特殊材質かステンレスなどの汎用材質かで以降の議論は分かれていきます。
バッチ系化学プラントでは、グラスライニング・カーボンなどの特殊な高級材質が要求されます。
詳しく知りたい方は以下の記事をご覧ください。
この瞬間に、管内にプロセス液を通し・管外にユーティリティを通すことが確定します。
伝熱面積もだいたいは決まってしまうので、以降の設計要素のほとんどを考えることなく、自動的に設計完了となるくらい強力な設計要素が材質です。
ステンレス系ではチューブの材質は基本設計で決まるけども、管内冷却・管外冷却を決めることはできません。
どちらのケースでもチューブの材質そのものは変わりませんが、ステンレスの多管式熱交換器の場合では、
- 管内冷却ならチャンネルカバーがステンレス
- 管外冷却ならシェル・バッフルがステンレス
とステンレスにすべき部位が変わってきます。
流速
管内の設計要素として大事なことが流速
U値などの熱計算をするときにも最初に決めないといけないことが流速です。
逆に言うと、伝熱面積と流速が決まればU値の計算なんて答え合わせのようなものです。
特殊材質なら流速を計算することすらありません。
というのも流速を変化させる要素としてのチューブサイズ・チューブ本数・パス数を変化させることが非現実的だからです。
伝熱面積さえ決まれば、メーカー標準から設計するくらいで十分です。
汎用材質でもパス数を変えるくらいの設計要素しかありません。
チューブサイズ・チューブ本数を変えるということは大々的な設計をするということで、最適化に時間を要してまで効果を高めたい超特殊な設備に限定されるでしょう。
私は15年以上の間で一度も経験したことがありません。
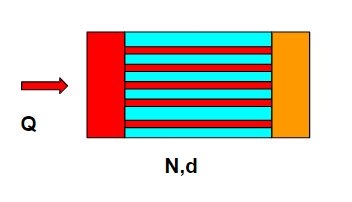
管内側の断面積は
$$ A = N\frac{πd^2}{4} $$
なので、流速は
$$ v = \frac{Q}{A} = \frac{4Q}{nd^2} $$
として計算します。
パス数
パス数は流速を決めるための直接的な設計要素。
具体的にはチャンネルカバーに仕切を設置します。
これがグラスライニングなど特殊材質では製作不可能。
だからこそ、特殊材質では管内は1パスに限定されます。
汎用材質なら、パス数を増やすことで流速を簡単に変えることができます。
後は圧力損失とのバランスを見ていけばいいでしょう。
でも、コンデンサー用途の場合は管内を2パス以上にすることは実はありえません。
コンデンサーはガスの凝縮をターゲットにしています。
片側のチャンネルカバーからにチューブを1パス通して、他方のチャンネルカバーにプロセス液が到着した瞬間に
ガスと液を分離させないと非効率。
ここでガスを分離させつつ残った液だけを2パスルートに通そうとすることは、実態としてはかなり難しいです。
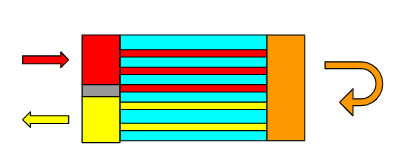
無理やり2パスでガスの凝縮をしたとしても、圧力損失が大きくなったり、その割に伝熱効果を高めることができなかったりと、費用対効果の面であまり意味がありません。
こんな場合は、素直に熱交換器を2台に分割する方が無難です。
管外の設計項目
管外の設計項目も管内の設計項目と大きな差はありません。
難しく考える必要はありませんよ。
材質
管外の材質は特殊材質の場合はSS400などの鉄系に限定されます。
特殊材質の場合は、管外がユーティリティに限定されるからですね。
汎用材質で、管内冷却の場合は特殊材質の場合と同じで、SS400系です。
結局はユーティリティを通すかプロセス液を通すかで決まってきますね。
プロセス液を管外に通す場合は、シェルやバッフルなどをステンレスなどの耐食性材質にします。
流速
管内と同じく管外も流速設計が多管式熱交換器の基本。
実は、管外でのガス凝縮の場合は流速設計は考えません。
流速設計が大事なのは管外に液を通す場合。
流速を上げて熱交換効率を上げて、少ない伝熱面積でも運転に耐えうる設備を作ることが狙いです。
バッフル間隔
流速を増やすためには、バッフル間隔を設計します。
バッフル間隔が短いほど、流体の通過面積が小さくなり、流速を上げる設計になります。
管内の場合でパス数を上げることと同じ扱いですね。
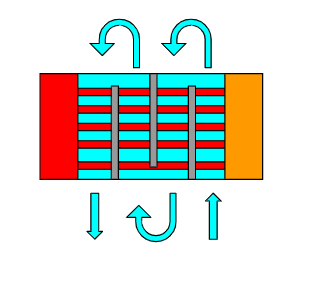
管外における流体の通過面積とは、以下の指標で考えると良いでしょう。
(シェル径-チューブ外径×チューブ本数)×バッフル間隔
これは厳密な通過面積ではありません。単なる指標という扱い。
というのも、管外の流体の通過面積は場所によって変わるから。
バッフル切り欠き部は上の指標よりも遥かに狭いです。
詳細の熱計算・流体計算をして熱的・強度的な問題を考える超高負荷の設備に限定されるでしょう。
その辺りを議論するのは、バッチ系化学プラントではありえないレベル。
バッフル間隔を短くするほど圧力損失が大きくなるので、ポンプ設計などとのバランスを考える必要があります。
日常的にはバッフル間隔は社内標準を作っておいて、よほどのことがない限り変化させないという思想が無難でしょう。
ガス凝縮の場合も設計上は影響がなくても、液冷却の場合と同じバッフル間隔にしておけば無難です。
無難なので、変化させてはダメというわけではありません。
その代わり変化させる場合には、それなりの検討が必要です。
バッフル切欠
バッフルの切欠も設計要素です。
切欠開度は25%が一般的なので、これを変えるような設計は普通はしないでしょう。
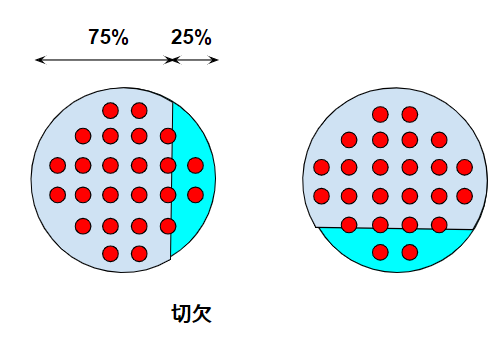
これもバッフル間隔と同じで変えるならそれなりの検討が必要です。
切欠の向きは設計思想が分かれます。
- 垂直切欠 相変化のない液体
- 水平切欠 相変化のある液体
こんな感じで言われますが、結構どちらでもいい要素。
25%垂直切欠なら、シェルの天と地はどのバッフルもシェルとほぼ接触しています。
これがガスや液の溜まりの要因となり、溜まりを嫌うなら垂直切欠を避けた方が良いという解釈です。
でもバッフルとシェルが溶接で繋がっているわけでもなければ、バッフルとチューブも同じようにすきまがあります。
バッフルの天と地に意図的に三角切欠きを付ける場合もあるでしょう。
気休めレベルです。
水平切欠なら垂直切欠で起こる溜まりを完全に解決できるかというと、そうでもありません。
バッチ系化学プラントなら清浄度が高くないユーティリティ液による錆や異物のたまりを気にして、垂直切欠にすることが多いです。
逆に綺麗なプロセス液やユーティリティしか通さない!という場合は水平切欠の方が若干でも効果を高めることができるでしょう。
洗浄性はどこまで考えるべきか?
教科書的には液の洗浄性が管内か管外かを左右すると書いていますが、この記事では管外のバッフル切欠で取り上げた程度です。
あまり重視していません。
その理由には、バッチ系化学プラントでは以下の背景があるからです。
- 使用条件がマイルド
- マルチ目的で使用する
- 高耐食材料が必要
特にグラスライニングやカーボンなどの熱交換器の場合、自ずと指定されてしまいます。
この辺の発想から、コンデンサーでは管内凝縮・管外ユーティリティという王道の設備構成ができあがります。
マルチ的でない専用設備に近い場合には、管内ユーティリティ・管外凝縮ということも考えられますが、非常にレア。
プロセス液がきれいなガスだけという場合が徐々に減っているからです。
本来綺麗なガスが通るプロセスだったけど、異物や触媒などの添加物を入れることになった結果、
コンデンサーにその固形分が到着して閉塞すると大問題です。
固定式で洗浄性を犠牲にしてでもシール性を上げているのに、閉塞問題に悩まされたら本末転倒。
ユーティリティの管理をしていない場合は、水の劣化に伴ってシェル内に錆が溜まってしまいますが、それでも20年くらいは持つので、定期交換をするという発想をする会社もあるでしょう。
ユーティリティの水質管理に日常のコストを投資するか、中長期的な設備に投資するか、という判断になります。
設備洗浄はプラント運転の1つの重要課題です。
詳しく知りたい方は以下の記事をご覧ください。
参考
熱交換器はすでに確立された技術で、疑いなく同じ構造を使いがちです。
一方で基本的な役割を知ると、改善する部分が見えたりします。
基本をしっかり理解したいですね。
関連記事
熱交換器について興味がある方は、以下の記事をご覧ください。
最後に
バッチプラントで使われるコンデンサー用途の多管式熱交換器は、固定型・シンプル構造での設計が基本です。
重要なのは以下の3点:
- 材質選定(特に管側)
- 適切な流速の確保(特に凝縮用での1パス設計)
- ユーティリティとの役割分担(プロセスは管側)
過剰設計を避けつつ、現場での保守性やコストバランスを踏まえた設計が求められます。
化学プラントの設計・保全・運転などの悩みや疑問・質問などご自由にコメント欄に投稿してください。(コメント欄はこの記事の最下部です。)
*いただいたコメント全て拝見し、真剣に回答させていただきます。
コメント