化学プラントで働く機械系エンジニアや設備担当者にとって、「溶接」は自分の専門外だと感じるかもしれません。でも実際には、配管設計や保全、トラブル対応において、基本的な溶接知識が不可欠です。
この記事では、専門家でなくても押さえておきたい溶接の種類や注意点、そして現場でよくあるトラブル事例まで、実務に即した視点でわかりやすく解説します。
過剰な専門性は不要ですが、ここくらいまでは知っておいた方が良いという情報をまとめています。
全部を理解して暗記する必要はありませんが、体系の深さ・広さをまずは認識するところから始めましょう。
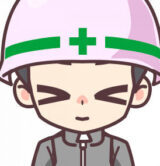
溶接は機械エンジニア必須の知識
溶接(welding)の種類
溶接の種類として教科書的に出てくる種類はおおよそ下記の通りでしょう。
- SMAW 被覆アーク溶接
- GTAW TIG溶接
- プラズマアーク溶接
- MIG ミグ溶接
- MAG マグ溶接
- セルフシールドアーク溶接
- SAW サブマージドアーク溶接
- FCAW フラックスコアードアーク溶接
さっそく種類が多くて心が折れそうになります。
SMAWとGTAW
色々な種類がありますが、SMAWとGTAWが基本だと思います。
- SMAWが鉄
- GTAWがステンレス
この2つは使い分けをちゃんとできるようにしましょう。
SMAWが昔からある溶接方法で、GTAWが比較的新しい方法でしょう。
化学プラントでは鉄かステンレスの溶接ばかりなので、この2つで基本はOK。
被服アークとガスシールドアーク
被覆アークとガスシールドアークという2つの区分があります。
2つとも溶接時に異物が混入することを防ぐ目的があります。
ここでいう異物とは風。wind。
溶接とは母材と溶接棒に熱を加えて溶かしこむもの。
溶けるときに異物があれば、化学反応をして金属の性質が変わります。基本は劣化します。
そのために異物を除去しようとします。
空気中の酸素や窒素は溶接の異物になります。
風が吹いている環境で溶溶接をすると、溶接をしているまさにその場所に空気が入ってきます。
これを遮断するために、被覆アークやガスシールドアークという方法を取ります。
- SMAWが被覆アーク
- GTAWがガスシールドアーク
この2つで基本はOKです。
FCAWが近年開発されていますが、これはガスシールドアークの一種。
被覆アーク溶接は溶接棒その物にシールド材が塗布されていて、空気と遮断します。
ガスシールドアーク溶接は溶接棒の周りにガスを吹き込んで、空気と遮断します。
ガスの種類や溶接棒が溶けるかどうかでいくつかの種類がありますが、実は私は全く気にしたことがありません。
GTAW | 不活性ガス | 溶接棒は溶けない |
MIG | 不活性ガス+CO2 | 溶接棒は溶ける |
MAG | CO2 | 溶接棒は溶ける(被覆材あり) |
FCAW | 不活性ガス | 溶接棒は溶ける |
手動・半自動・全自動
溶接の手動・自動については一時話題になりました。
昔は当然手動です。今では自動や半自動がかなり増えました。
昔と言っても10年くらい前の話。つい最近です。
- 手動 人が溶接する
- 半自動 溶けた溶接棒の補充を機械が自動的に行う
- 自動 機械が全て溶接してくれる
簡単に言うとこんな分け方です。
自動溶接は装置が大型になるので、大きなタンクなど限定的にしか使えません。
それでも特殊な技能は求められませんので現代では大活躍。
発展途上国でも立派な溶接タンクができるのは、自動溶接がちゃんとしているから。
自動溶接ではできない部分を手動や半自動で補います。
日本では機械の導入コストが掛かるため最近まで手動が多かったようですが、半自動に徐々にシフトしていっています。
そんな歴史の話を閑話休題として紹介しました。
溶接(welding)の設計
溶接の設計というほど大げさなことではありませんが、化学プラントの機電系エンジニアでも最低限知っておくべき知識を紹介します。
突合せ溶接
突合せ溶接は言葉どおり2つの金属を平行に繋げた形です。
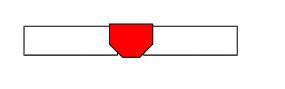
タンクの溶接など不連続部が無いように繋ぐにはこの方法を使います。
すみ肉溶接
すみ肉溶接は2つの金属を直角に繋げた形です。
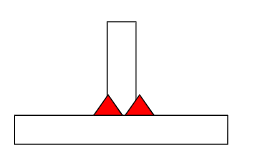
両側
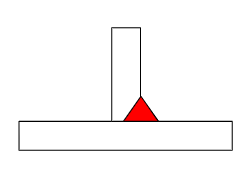
片側
左型が両側すみ肉溶接、右側が片側すみ肉溶接と言います。そのままですね。
タンクのノズルやフランジなどに使います。
I形溶接(welding)
I型溶接は、溶接の基本となるシンプルな形状です。
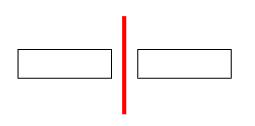
単語とおり、溶接の開先部分がアルファベットの「I」の形をしています。
溶接方法で重要なパラメータは開先とルート間隔です。
この2つのパラメータに関して、各溶接形状でどういう設計をするか、その思想を示します。
ルート間隔は以下の場所を指します。
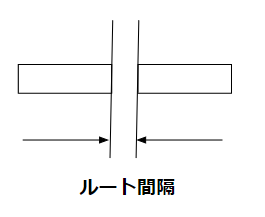
溶接する2つの部材の間隔のことです。
ルート間隔は板厚以下とすべきです。
ルート間隔を板厚より大きいという事は、強度が弱い溶接部が板厚以上に大きくなるという問題を抱えることになります。
鉄系なら板厚が3.2mm以下ならルート間隔は0mmでも溶接可能です。
板厚が3.2mm以上であればルート間隔を広げたり、開先を取ったりしましょう。
なお3.2mmというと、危険物タンクで規定される最小板厚でもあります。
V形溶接(welding)
V型は以下の図のような形です。
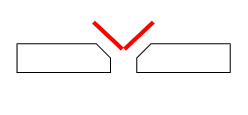
I形に開先を取ったタイプです。
開先は下の図を確認してください。
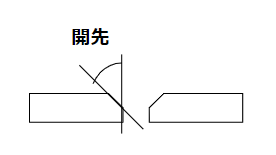
開先を取るのは、板厚が大きいからです。
板厚が大きい時には、1回の溶接では完了しません。
何回かに分けて溶接する必要があります。
- 板厚(t)
- ルート間隔(s)
- 開先角度(Θ)
- 開先を取らない部分の板厚(a)
このようなルールを決めている会社も多いでしょう。
装置周りはほとんどがV型で溶接しています。
L形溶接(welding)
L型溶接は以下のような形です。
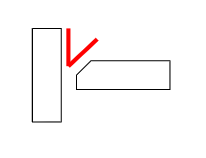
L形といいながら、実際にはレ型です。
アルファベットに無理やり押し込むとL型になります。
- I型・V型 突合せ溶接
- L型 すみ肉溶接
L型は部材を90度方向に付けたいときに使います。
部材は180度方向か90度方向に付けれれば、いろいろな形を作れますよね。
I型・V型の突合せ溶接は180度方向の溶接ですが、L型はすみ肉溶接で90度方向の溶接が可能です。
K形溶接(welding)
K型は以下のような形をしています。
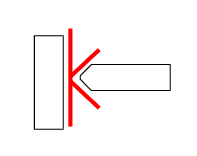
なんとなくピンとこないでしょうか?
実はI型・V型・L型・K型をまとめると以下の関係があります。
180度 | 90度 | |
板厚が薄い | I | L |
板厚が厚い | V | K |
板厚の厚い90度方向の溶接はK型を使います。
典型例はフランジとノズルの溶接でしょう。
板厚以上の溶接(welding)厚み
溶接設計の基本というかここだけはちゃんと抑えたいというポイントが溶接厚みです。
溶接の厚みは母材の板厚より厚くする
これが基本的な考え方です。
溶接の厚みの方が母材より薄い場合は、溶接部が弱い構造になります。
せっかく強度を持たせようとして母材の板厚を確保しているはずなのに、その意味がなくなってしまいます。
すみ肉溶接の場合は「のど厚」が溶接厚みになりますが、突合せ溶接と考え方は全く同じです。
特殊なものと思う必要はありません。
溶接をした後の強度としては「突合せ溶接>両側すみ肉溶接>片側すみ肉溶接」となるでしょう。
溶接の厚みに着目しつつ、不連続なつなぎ方をしない突合せの方が強いという考え方です。
WPSとPQR
溶接を語るうえで、WPSとPQRは避けて通れません。
ですが私はこの表現嫌いです。
外国語だからです(笑)
溶接施工方案書などの表現でも良さそうなのに、そこは残念な日本。
統一した表現を作ることができず、外国の「世界標準」に合わせざるを得ないという残念な結果。
WPSやPQRという表現自体は、世界各国で使われているので止むを得ませんが、そうしている内にありとあらゆる単語が外来語になっている現状にがっかりしています。
それはいいとして、WPSとPQRについて紹介します。
WPSは溶接施工要領書
WPSはWelding Procedure Specificationの略です。
日本語では溶接施工要領書です。
溶接の業務の流れとしては、溶接施工→試験というイメージなのでWPS→PQRの順番になりそうな気がしますよね。
どうやら、書類の流れとしてはPQR→WPSとなるようです。
それではPQRの方を先に見てみましょう。
PQRは溶接施工法確認試験記録
PQRはProcedure Qualification Recordの略です。
日本語では溶接施工法確認試験記録です。
ここにはWPSの内容+記録書という表記になっています。
システマティックな米国の書類らしく、PQR上のWPSに相当する表現は、WPSの書類そのものとなっています。
シンプルに考えれば当たり前のように見えますが、システマティックでない日本ではこうはいきません。
PQR上のWPSの表記とWPS上の表記がコピペできない表現になっていたりします。
PQRとはある方法で溶接をしたらこのような結果が出ましたという記録を示したものです。
実物をいきなり溶接するわけでなく、サンプルを使って溶接して試験します。
PQRをもって製作会社として溶接の品質を担保。
簡単なイメージにすると以下のようになります。
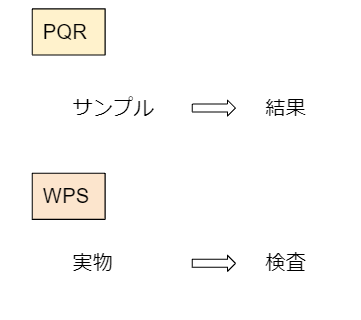
PQRには以下のようなデータがあります。
溶接作業:パス数・電流電圧特性・溶接棒材料・溶接棒寸法・溶接速度・入熱量
試験記録:引張試験・曲げ試験・衝撃試験等
WPSはPQR通りの方法を実施しますという要領書の扱いです。
その結果は非破壊検査で確認して製品として保証します。
溶接(welding)検査
溶接は欠陥があると疑った方が良いです。そのためにも検査をします。
外観検査
外観検査の項目としてどんなものがあるでしょうか。
非常に細かく決まっています。
ここまでの品質を要求される溶接という仕事を人間がしないといけないのか、少し疑問に思います。
溶接は機械に任せるという流れは当然でしょう。
どんな項目があるかとりあえずリストアップします。
余盛幅
余盛高さ
のど厚不足
開先面の残存
目違い
表裏のビードの凹凸
波目の粗いビード
ヒード幅の不揃い
裏ビードの凹み
開口欠陥
割れ
貫通孔
角変形
アンダーカット
オーバーラップ
溶け込み不良
クレータ割れ
検査項目が非常に多く嫌になりますよね。
でも、ポイントはたった1つ。
不連続部分があるかどうか
これだけです。もっと簡単に言うと綺麗か汚いか。
この目線で、異なる設備の溶接線を何本か眺めるだけで、ある程度の傾向が掴めます。
非破壊検査
非破壊検査として有名なのは、RT・UT・MT・PTです。
これも検査基準が明確に決まっています。
溶接(welding)の熱履歴
溶接は金属に熱を加えて溶かします。
これをいつどんな風に行ったかという記録を熱履歴と言います。
熱履歴とは熱を加えた回数・溶接をした回数と言っても良いでしょう。
熱履歴に関する概念をまとめました。
焼きなましと焼ならし
材料に対する熱履歴の話題で出てくる用語です。
とても分かりにくい表現。
焼なまし | 炉冷 | 900℃→600℃ |
焼ならし | 空冷 | |
焼入れ | 水冷 | |
焼戻し | 加熱 | 焼入れ→500℃ |
ザックリこれくらいの理解で良いでしょう。
焼なまし・焼ならし・焼入れと3つに分けているのは、金属を温めた後の冷却速度の違い。
金属は温めて成形しますが、日常の温度に戻してあげないといけません。
この速度が3パターンあります。
早く冷却する方が時間の無駄が無くていいでしょ?と思うかもしれませんね。
ここに罠があります。
金属は速く冷却すると性質が悪くなります。
金属の組織が温度によって変わっていくのですが、その変化速度が速いとダメということ。
金属の表面では早く変化しながら、内側ではまだ変わっていない。
こういう不連続ができることで性質が悪くなります。
不連続というのは機械関係ではとにかくタブーです
温めた金属の冷却速度は周囲の温度に依存します。
高温の炉の方がゆっくり冷え、常温の空気は中間くらい、水の方が速く冷えます。
焼入れという水で冷却すると性質が悪化するので、焼き戻しと言って再加熱をします。
焼なましなどの話は鉄板などの製鉄所をイメージしがちですが、これと同じことが溶接で起こります。
熱影響部
溶接をしたとき、その周囲にも熱履歴が加わります。
この熱履歴の影響範囲のことを熱影響部と言います。溶接の2番線やPWHTという言い方もします。
熱影響部に再度溶接をすることは基本的にNGです。
熱影響部に2回目の焼きを加えることになります。
目には見えませんが金属組織に確実にダメージを与えています。
熱影響部への再溶接は極力少なくしないといけません。
例えば周溶接と長手溶接のつなぎ目など避けられない部分は仕方がありません。
でもノズル・当て板など設計次第で何とかなりそうなものまで、溶接線を近づけてはいけません。
容器関係ならメーカーも気にしてくれますが、板取図を提出してもらってチェックしましょう。
溶接の予熱
予熱をしないで溶接をすると割れる可能性があるようです。
とはいえバッチ系化学プラントでは基本的に問題になりません。
- 鉄は25mm以上で気温10度以下
- ステンレスは不要
これくらいの感度で大丈夫だからです。
高圧反応器などになると鉄の板厚が25mmを越えるケースがあるので、予熱をすることもあるようです。しかしレアケース。
以下、予熱に関する補足情報です。
- 予熱は初層が大事
- 予熱は炎や電気抵抗やプラズマで
- 予熱温度は100~400℃
- 添加物が多いほど予熱温度は上げる
溶接の後処理
溶接の後処理は、焼なまし・焼ならしの話に直結します。
溶接レベルでは残留応力という視点で見ます。
焼なまし・焼ならしと同じく冷却速度の話になります。
- 炭素鋼なら19~38mm以下は後処理不要
- 温度と時間がパラメータ
バッチ系化学プラントの機電系エンジニアレベルではこれを使いこなして、PQRの指摘をすることなんてできません。
その意味で参考情報です。
溶接(welding)の欠陥
溶接の欠陥として有名な物を挙げます。
- ブローホール
- スラグ巻き込み
- 溶け込み不良
- 割れ
- オーバーラップ
- アンダーカット
- 融合不良
いずれも、溶接部に物理的な不連続部分が起こることが特徴です。
ブローホール
ブローホールとは、溶接時に発生するガスが逃げないうちに溶接金属が凝固したものです。
溶接金属の表面や内側に孔ができたものと思っていいです。
ガスとはCO・H2・N2などです。
原理的には、溶接時にガスが発生するのは仕方が無いので、発生しても逃がすようにするべきでしょう。
その意味で対策は、運棒速度が最重要です。
他にも対策として、溶接表面汚れを取ったり、溶接棒の湿度管理をしたり、溶接電流を強くしたり、という方法もありますが、それらは2次的な対策でしょう。
スラグ巻き込み
スラグ巻き込みはSMAWに固有の問題です。
SMAWで発生する溶接スラグが浮上せずに、溶接金属中に残る現象です。
融合不良もこれと同じ原因です。
普通は、スラグは溶接金属の周囲を覆っていて、溶接金属が形成されるとスラグは押し出されます。
これは溶接姿勢や運棒方法が最も確実ま対策でしょう
溶接姿勢、運棒の設置角度、運棒の速度など…テクニカルな話です。
溶接表面の汚れを除去したり、開先形状を適切に選ぶなどの対策もありますが、やはり溶接姿勢が基本対策となります。
溶込不良
溶込不良はルート面に溶接金属が溶け入らない現象です。
開先角度が狭すぎる場合に起こりやすいです。
という事で基本対策は、開先角度の確保。
次に、溶接棒を細くできるかどうかです。
電流が弱いと溶け込み速度が遅いために、溶込不良となる可能性があります。
アンダーカットとオーバーラップ
アンダーカットやオーバーラップは溶接金属が満たされないで溝ができた現象です。
これは完全になくすことは難しいですが、緩和することは可能です。
基本はやはり溶接姿勢や運棒方法です。
電流を抑えるといい時もあります。
電流が大きいと溶接金属にエネルギーがたくさん入り、溶接が固まるまでに時間が掛かるからですね。
エネルギーが高すぎて、母材も溶かすためにアンダーカットとなります。
電流が小さいと、逆に母材が溶けずに溶接金属が開先から溢れていく方向になります。
これがオーバーラップです。
低温割れと高温割れ
低温割れは化学組成、水素量、拘束度などの因子が効いてくるようです。
高温割れは比較的高温で発生する割れのようです。
低温割れ・高温割れいずれもやや専門的な内容だと思います。
溶接(welding)の異物
溶接の異物について紹介します。
簡潔に言うと水素H、酸素O、窒素N
分かりにくいですか?
水と空気です。雨と風です。
- 水素Hがある → 水素ガスが発生 → ブローホール
- 酸素Oがある → CO2ガスが発生 → ブローホール
- 窒素Nがある → 窒素酸化物が生成 → 欠陥
溶接は高温で行うので、基本的な化学反応が起きやすいです。
常温では起きないような基本反応が高温では起こりえるので、何気ないものが異物となってしまうわけですね。
異物の混入を防ぐためには以下のような方法があります。
- 被覆アークやガスシールドをちゃんと行う
- 雨風を防ぐガードを付けて溶接をする
- そもそも雨の時は溶接しない
- バックシールドガスを使う
- 溶接棒を乾燥させる
バックシールド
バックシールドは配管に対して行います。
配管の外周を溶接するとき、内側には空気があります。異物の元ですね。
空気を排除して別のガスを封入することをバックシールドと言います。
アルゴンArのガスが一般的です。
溶接棒管理
アーク溶接の溶接棒は乾燥庫で管理するべきです。
なぜかというと空気中では吸湿するから
吸湿すると水が溶接に貼ります。水は異物ですね。
乾燥し過ぎても駄目で、温度湿度を管理することが大事です。
大きな工場では部屋そのものの温湿度管理もしていますね。
溶接(welding)の一般的な対策
溶接の欠陥が起きないようにするためには、溶接の具体的な作業方法で対策をしないといけません。
各欠陥の個別具体的な対策は記載しません。
あくまで一般的な対策について記載します。
化学設備の機械屋ではこれくらいの理解で十分だと思います。専門家ではありませんので。
- 母材・溶接棒の材料を適切に選定する
- 溶接棒の乾燥・保管を適切にする
- 溶接の姿勢を適切にする
- 開先形状を適切に製作する
- 溶接棒の運棒方法を適切にする
- 積層法を適切に決定する
- 仮付方法や位置を適切に決める
- 温度・雨風・明るさ・狭さ等の作業環境を適切にする
溶接(welding)の順番
例えば竪型の円筒タンクを溶接する場合、長手方向と周方向の溶接が必要です。
これをどういう順番で溶接すればいいか、基本的な考え方を紹介します。
- 中央から自由端に向かって溶接する
- 下から上に向かって溶接する
- 溶接量の多い物から順番に溶接する
- 未溶接継手を通り越さないように溶接する
- 著しい拘束が発生しないように溶接する
- 突き合わせ溶接を先に、すみ肉溶接を後にする。
溶接の熱で母材は変形します。
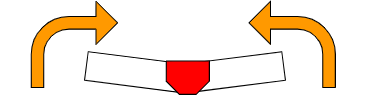
溶接の熱を受けた母材は溶接金属付近で熱による収縮を受けます。
その結果、溶接後には母材は少し変形してしまいます。
変形量を予測してひずみが拘束されなようにしつつ、強度が大事なところから溶接する。
この発想から順番を決めていけば、大きな間違いは起きないでしょう。
ひずみを少なくするためには一般に以下の方法が取られます。
- 開先を適正に取る
- 機械的にひずみを取る
- 加熱してひずみを取る
- 酸を掛けてひずみを取る(酸洗浄)
酸洗浄が一般的で硫酸や塩酸を含む液を、溶接後に溶接線にかけます。
ステンレスの鋭敏化
オーステナイト系ステンレス鋼には炭素C・クロムCr・ニッケルNiが含まれます。
オーステナイト系ステンレス鋼として機能するためにはCtとNiの含量が非常に重要です。
これが溶接では問題になります。
CがFeやCrと反応
溶接をすると溶接部は500℃以上の温度になります。
炭素鋼中の炭素Cが鉄FeやクロムCrと反応して結晶ができます。
もともと、オーステナイト系ステンレス鋼を製作した時には、CもCrもNiもFeもほぼ均等に混ざり合ったほぼ理想的な状態が実現できています。
ところが、溶接によってこのバランスが崩れることになります。
溶接で発生した結晶が繋がって粒界という形で顕微鏡レベルでは見えるようです。
粒界は耐食性が弱いのでここから腐食が起きます。これを留界腐食と言います。
炭素量が少ないL材
対策としては炭素量が少ないL材(Low Carbon)を使用します。
SUS304LやSUS316LというのはL材です。
TTS曲線という線図がありますが、加熱温度と鋭敏化までの時間をデータにしています。
L材ほど、長い時間熱を加えても鋭敏化しないという意味です。
溶接棒中のCrやNi
溶接棒中のCrやNiの含量も大事です。
これは溶接金属よりも含量を多くしなければいけません。
少なくとも溶接金属と同じとするのですが、多い方が確実です。
SUS304(Cr18%,Ni8%)の溶接ならType308(Cr20%,Ni10%)を使います。
希釈
溶接では希釈という概念があります。
これも知っておいた方が良いでしょう。
溶接は溶接金属と母材を溶かすものです。
これははんだ等の溶着とは決定的に違います。
溶接金属と母材が同一でない限り、溶接金属近辺の母材は必ず変化します。
オーステナイト系ステンレスの鋭敏化も同じでしたね。
このように、母材の組成が変わってしまうことを希釈と言います。
希釈はクラッド鋼で特に問題になります。
クラッド鋼ではステンレスと鉄を張り合わせた金属が有名です。
ステンレスの無垢で厚板を溶接してタンクを作る場合、入熱量が多くなり鋭敏化の原因となります。
それ以上に高価です。
だからこそ接液部のみステンレスにして外側の強度保証部を鉄にするという考えです。
ライニングと同じ発想ですね。
対策としては以下のとおり。
- 溶接の順番を工夫する
- パス数を増やす
- 開先を最小量にする
- 入熱量を制御する
特に注意したいのが溶接の順番。
ステンレス/鉄のクラッド鋼の場合は、鉄の溶接を先にします。
先にステンレスの溶接をしてしまうと、後の鉄の溶接でステンレス溶接部の希釈が起きます。
ステンレスの溶接量よりも鉄の溶接量が多く、入熱量が多いために希釈量が多くなるという意味です。
先に鉄の溶接をして、後でステンレスの溶接をしても希釈自体は起きますが、量が違います。
溶接というか伝熱の分野かも知れませんね。
人体への影響
最後に溶接が人体に及ぼす影響も紹介します。
アーク光による眼炎
溶接をした時に、光が出ます。
この光は強烈な可視光線や紫外線・赤外線を含みます。
太陽光と同じで直視してはいけません。
目を傷めます。
作業員は保護面を付けて対策をしますが、他の人は対策をしません。
通行をしている人は溶接の光を見て初めて気が付きます。
タバコと同じで、周りの人の方が被害に対する防止が遅れるという問題があります。
自衛手段はとにかく近寄らない・見ないということだけです。
残念ですが。
感電
こちらは実感がしにくいですが、やはり危険です。
溶接では金属同士に電流を流します。
溶接棒自身は溶接機を伝って地面にアースされています。
溶接母材自身も適切な方法でアースして、地面に電流を逃がします。
工事現場等で建築物や配管サポートを溶接している時が危険です。
溶接機自体は問題になりにくいですが、溶接母材側が問題です。
実際に溶接母材を溶接する場所ですぐにアースを取っていれば、あまり問題にならないでしょう。
普通は、溶接する近くを通行することはありえないので。
ところが溶接母材のアースをかなり遠い位置で取っていて、母材とアースの間に人が通ったとしましょう。
そこで、何らかの理由で金属部(例えば金属手摺)に手を振れたとしましょう。
溶接時の電流が人に流れて、感電する恐れがあります。
溶接の電流では心室細動を起こす危険があります。
溶接作業員は、絶縁体で保護するなどの対策を取っています。
怖いのは、溶接の怖さを知らずに通りかかる一般人です。
火災爆発
これは危険物製造所で特に気を使う箇所です。
溶接時に発生する生火や火花は、可燃性ガスに引火して爆発する恐れがあります。
見落としやすいのが、溝に滞留している可燃性ガスや、塗装に使う塗料缶などです。
これも、危険性がどんどん認知されていって、対策がレベルアップしています。
衛生
溶接では金属を溶かします。
溶けた金属が気体となって空気中を舞います。
金属・フラックス… 人体に悪影響があります。
作業者自身は防じんマスクを付けたりしますが、一般人は気が付きません。
シールドガスにCO2や不活性ガスを使うため、酸欠になる可能性もあります。
とにかく近寄らないことが最大の安全対策です。
爆発
溶接で使用するガスボンベが危険です。
GTAWで使うCO2やArガス、ガス溶接に使うアセチレンなどが非常に危険です。
直射日光で温められて圧力が上昇したり、転倒・打撃等でボンベが傷付いたりして、ボンベが爆発します。
とにかく近寄らないことが最大の安全対策です。
参考
溶接の知識は非常に幅広いです。
化学プラントのオーナーエンジニアが知っておきたい知識に限定して紹介しましたが、さらに知識を深めたい場合は以下のような本が有用で。。
関連記事
最後に
化学業界で働く機械系エンジニアや保全担当者にとって、溶接は「知らなくてもいい知識」ではなく「知っておくとトラブルを防げる知識」です。専門家レベルの深い理解までは必要ありませんが、最低限の種類、注意点、施工品質の確認方法などを知っておくことで、設計や保全の精度をぐっと高めることができます。
化学プラントの設計・保全・運転などの悩みや疑問・質問などご自由にコメント欄に投稿してください。(コメント欄はこの記事の最下部です。)
*いただいたコメント全て拝見し、真剣に回答させていただきます。
コメント