バッチ系化学プラントの反応器内で行う、典型的な工程を解説します。
バッチ生産は反応器単位で、工程を考えます。
例えば以下の反応器で1工程を実行します。
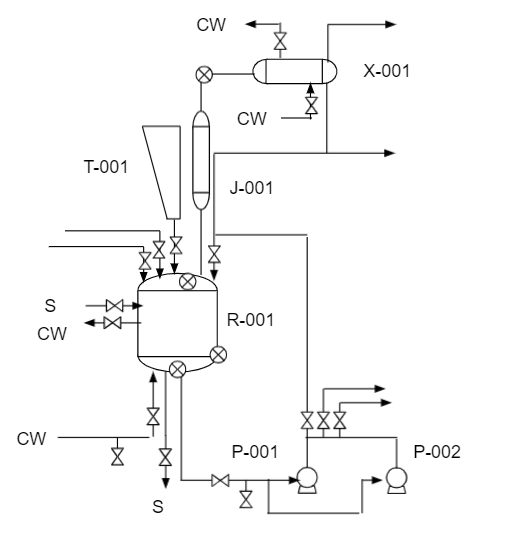
この1工程内にはいろいろな操作があって、今回はこれを9ステップで解説します。
工程ごとに別の反応器を使って、同じような操作で条件を変えて反応を進めていく・・・という感じです。
感覚的には電車が1つ1つ駅を進んでいくことに、そっくりです。
この理解が進むと、プラントの運転を理解しやすくなるでしょう。
反応器で行う操作
反応器内で行う典型的な操作を9ステップに分けてみました。
- ステップ1窒素置換
- ステップ2原料受入
- ステップ3温度調整
- ステップ4反応
- ステップ5熟成
- ステップ6サンプリング
- ステップ7冷却
- ステップ8分液
- ステップ9ライン洗浄
この典型例通りに行う反応はむしろ少なく、追加されたり省略されたりすることの方が多いです。
基本形としてここを把握しておくと応用がいくらでも効くので、プロセスを理解する上で役に立つでしょう。
窒素置換
最初は窒素置換を行います。
化学プラントでは有機薬液のほとんどは消防法危険物の第四類。
引火性物質であり酸素と混じって爆発性雰囲気を形成します。
液を動かすだけで静電気が発生するので、酸素を取り除かないと引火爆発する可能性があります。
最大の対策が窒素置換。
生産開始段階でタンク内を積極的に窒素置換をしておき、後は常時窒素を流し続ける運用が多いと思います。
最初の窒素置換はタンク底から行いましょう。
タンク上から窒素置換をすると、底付近の空気が窒素で置換されにくいです。
そのためにもタンク底に窒素ラインが必要ですね。
原料受入
系内の酸素を追い出すと、原料を受け入れます。
最小に投入する原料は溶媒が多いです。
AとBという2つの物質を混ぜて反応させる場合、どちらか片方だけ先に全量受け入れることが多いです。
Aを全量受入 → Bを滴下させて反応
こんなプロセスです。
Aの全量受入はポンプで、Bの滴下は自然落下で送ります。
反応熱が発生しないorほぼないプロセスでは滴下をせずに全量を一気に受け入れるでしょう。
この時でもAとBを同時に受け入れるということはほぼしません。
逆に同時に受け入れる反応はかなり特殊です。
受入速度が過剰になると流速が速くて静電気着火のリスクが高くなったり、ポンプの揚程が過剰に必要になったり良いことはありません。
標準流速の考えに従って配管設計をしたいですね。
温度調整
反応直前まで原料を受け入れた時に、温度調整に入ります。
常温よりも低い温度で反応させないと、反応熱で暴走する場合はここで冷却させます。
逆に高温で反応させる発熱反応の場合は、あえて温度調整をしない場合もあります。
常温で反応が進み反応熱で温度が上がっていくのをあえて利用する方法です。
緻密な温度制御が大事になってきます。
高温下で吸熱反応させる場合は、純粋に加熱します。
冷却なら冷却水やブラインで、加熱なら温水やスチームを使います。
反応
原料が投入され温度の調整もできれば、いよいよ反応工程に入ります。
反応までの準備って意外と多いですよね。
反応として反応熱が発生する場合を考えます。
この場合、反応物はゆっくり仕込みをします。
「滴下」と呼んだりします。
長い工程では10時間以上かかる場合もあります。
単位モル当たりの反応熱が大きくてどうしようもないため、時間を延ばして
発熱速度 < 冷却能力
となるようにプロセス設計します。
反応をできるだけ早くして滞留させたくない特殊な例では、そもそもバッチ式反応器を使わず連続反応システムを使います。
バッチ系では薄膜蒸発器が典型例です。
熟成
反応物を全量滴下したら終わり!というわけにはいきません。
「熟成」という待ち時間が必要です。
反応物を投入した瞬間に反応が完結するわけではありません。
反応には時間がかかります。
これを待つための時間が熟成です。
例えばこういうイメージです。
平均2時間で反応が完結する工程を10時間かけて滴下させる場合、
滴下開始10時間の滴下完了後には80%の反応が完結していて、残り20%はその後の2時間で反応させる。
塾生の時間や温度はプロセス条件によってさまざま。
ここでは単に一定時間が必要ということだけ知っていれば十分です。
サンプリング
反応が完結したことを確認するために、分析をします。
分析のためには、普通はサンプリングをしないといけません。
作業者への有害物質の暴露防止という衛生面の対策をしたサンプリングをしましょう。
サンプリング箱と局所除害装置は最低限の対策です。
単に普通の作業服で、配管の液抜きノズルからバケツで抜き取るということは止めましょう。
サンプリングした液を分析を掛けて合格であれば、次の工程に進めます。
不合格で反応が進んでいないだけの場合なら、原料を追加投入したり熟成の時間を取ります。
逆に反応が進み過ぎていた場合は・・・処分する可能性すらあります。
サンプリングしてから分析結果が出るまで一定時間がかかります。
その間にも熟成は進むので時間勝負となりやすい操作ですね。
冷却
反応が完結して分析が合格すると、次の反応器に輸送します。
ここで温度調整が入ります。
一般には加熱したプロセスを冷却する側が多いので冷却操作としておきましょう。
ジャケットに冷却液を入れて冷やしていくだけ。
プロセス的には安全側です。
プロセス液が冷やされることで気相部も冷やされて体積が減少するので、大気開放口から空気が流入してくる可能性があります。
そうなっては困るので窒素をちゃんと吹き込んでおきましょう。
近年ではできるだけ低温状態もしくは高温状態を維持したいというニーズが増えています。
こんなときはここの操作を無視して、すぐに輸送工程に入ります。
分液
輸送工程も単にポンプで液を送るだけとは限りません。
反応で油層と水層ができる場合は分液をするのが普通。
油層もしくは水層のどちらかが、次の工程で使う目的物で残りは廃棄物。
これを分けるために分液をします。
バッチ系化学プラントでは手動分液が多いです。
反応器の下にガラスを付けておき、ポンプで送液するときに界面を監視する方法です。
補助計器として導電率計や密度計を使ったり時間を測ったりもします。
人が界面をちゃんとキャッチして、精密に測り分ける作業が発生します。
ライン洗浄
分液などを含めて液をポンプで送った場合、配管内を洗浄します。
窒素でブローすることが多いでしょう。
いちおう、窒素ブローはするかしないかは工程によります。
安定性がよくなかったり固化したりするプロセス液は、配管内に溜まった液が問題を起こす可能性があるので積極的にブローします。
そうではなく比較的安全な液体なら、ブローせずに残しておく場合もあります。
分液を行うようなプロセスの場合は、ブローしますね。
油層が水層に混ざったりその逆があったりと、分液の意味を無くしかねませんので。
窒素ブローが終わったら、溶媒でライン洗浄します。
反応槽を経由させて溶媒で洗い流すことが多いですが、ポンプ吸込み口に洗浄ラインをあえて設ける場合もあります。
参考
反応器の知識は化学工学としてとても大事です。
機電系エンジニアとしても化学工学的な目線で見れるように、以下のような本で勉強することは大事です。
関連記事
反応器についてさらに知りたい方は、以下の記事をご覧ください。
最後に
バッチ系化学プラントでの反応器内で行う操作として典型的な例を9ステップで解説しました。
簡単そうに見えて、工程は非常に多いです。
24時間のサイクルでこれらの作業を繰り返し行うのがバッチ生産の基本でしょう。
交代勤務と合わせて慣れるまでは、運転状況の整理に頭が追い付かないかもしれませんね。
化学プラントの設計・保全・運転などの悩みや疑問・質問などご自由にコメント欄に投稿してください。(コメント欄はこの記事の最下部です。)
*いただいたコメント全て拝見し、真剣に回答させていただきます。
コメント