設備トラブルは、運転をしていく上で完全に防ぐことはできません。
逆に、いつ起こってもおかしくありません。
生産技術エンジニアはトラブルのたびに対応して、こういうことを言われるでしょう。
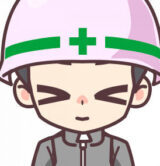
で原因は?対策は?
この質問に対して、私も完璧に答えを出したことは今までありません。
絶対に無理とすら思っています。
メーカーに聞いても正確な答えは出ません。
そういう時にも、メーカーの知見は必要なので、どういう話をしたらいいか?という現実目線で私が対応していることをまとめました。
この記事は、設備メーカーシリーズの一部です。
中小化学設備メーカーの技術力|専門性の実態
化学設備メーカー営業の嫌な対応3選【反面教師】
化学プラントで感じる“面倒なメーカー対応”の実態とは
エンジニアと設備メーカーがお互いに歩み寄ると効率化が進みます
まずはメーカー営業に聞く
トラブルが起きてメーカーに連絡すると、結構早く見てくれることが多いです。
そこで何かしらの見解をもらえたらいいでしょうが、持ち帰る時もあります。
ましてや報告書を求めようものなら、一生かかっても提出されないことの方が多いでしょう。
それでも、長期間放置されていると、メーカーには催促しないといけません。
ユーザー側では忘れ去られないようにするシステムが整っているから、完了させないといけません。
メーカーのように保証期限を切れたら後は放置する、ということが許されません。
メーカーの営業にアクションを掛けることが第一ステップです。
これで問題が解決することはおそらくないでしょう。次のステップに進みましょう。
運転条件は自分で調べる
メーカーと協議するときに、運転条件の不備で解決が遅れるということが多々あります。
トラブルが起きたときは条件を調べる余裕がなく、メーカーに来てもらって現状を調査。
そのやり取りが終わった時に、ユーザー側も運転条件を調べることを忘れがちです。
特に忘れるのが過去の生産条件。
トラブルが起きたまさにその生産の運転条件だけなら、すぐに調べることができます。
バッチプラントのように、何十年も同じ設備を使っていろいろな生産に使用している場合、トラブルの原因が別の生産条件にあったという可能性があります。
これらの条件を整理しましょう。
生産技術として製造から情報を集めましょう。
考えられる故障モードに対して、必要となる情報を集めます。
液量・温度・圧力などの基本条件以外にガス発生・スラリーの有無・pHなど調べることが多いのですが、全部を調べずに特定の情報を集めましょう。
例えば、金属が腐食ではなく物理的にすり減っていることが明らかな場合には、液量・温度・圧力の基本情報以外にスラリーの有無や撹拌条件をまとめていきます。
製造任せにしてしまうと、問題の解決に必要な情報が集まらなかったりします。
時間が掛かる可能性があるので、メーカー営業にコンタクトを取りつつ、調べるという感じですね。
オンライン会議でメーカー技術者を巻き込む
メーカーの営業に相談しても、明確な答えが返ってくることは稀です。
ほぼあり得ないと言っても良いでしょう。
技術者を積極的に巻き込みましょう。
ユーザーの現場に技術者が来てくれればいいのですが、技術者も忙しくて移動することができません。
今ではteamsなどのオンライン会議が有効なので、積極的に活用しましょう。意外と対面に拘って解決に時間を掛ける人が居ます。
生産技術以外に保全や製造など関連者を巻き込みましょう。
生産技術とメーカー営業が直接の窓口関係にあって、そこだけで解決したくなる気持ちは担当としては分かりますが、考え方を変えないといけないでしょう。
1人で考えずにみんなで考える。
プラント関係の業務ではとても大事にしたい考え方です。
メーカーに対策の責任を押し付けず、保全の管理方法を協議する
会議の場だと、メーカーから推定原因が提示されることは割とありえます。
報告書にはしにくいけど、○○の可能性がある・△△が関係していてもおかしくない、などの議論がなされます。
ここで、○○が原因であることをどうやって調べればいい?××が関係していないことをどうやって証明する?という議論がなされがち。
もしくは、それらのトラブルを避けるための対策を教えてほしい。
メーカーとしてもこれを聞かれても、答えに詰まってしまいやすいです。
メーカーはその設備のトラブル情報が全て集約されていて、お医者さんのように何でも答えられるというものでもありません。
それでもユーザーは聞いてしまいます。メーカーは逃げようとします。
この関係は非常に不健全。
私の経験では、これらの議論よりも以下の方向性の方が良い流れになります。
このトラブルが次に起きるのを避けるために、どこを点検していけば良い?
対策を取ろうとしたらメーカーは標準を変えたりするために抵抗が強いです。
数少ないトラブルのために、今の標準を変えるのは辛いでしょう。
しかも何が原因かを特定するのも難しい。
この場合に、ユーザーは長期的な運転の中で情報を掴んでいき、問題化する前に交換をするというTBMやCBM的な対応をしていく方が健全です。
この聞き方だと、メーカーももしかしたら案が出てくるかもしれませんし、ユーザーが調べた情報をもらえてメーカーとして知見を広げることができるかもしれません。
良い付き合いの継続を
メーカー営業や技術者と協力関係が築けている状況なら、これらの運用を是非とも行ってください。
付き合いが良くない会社なら、かなり非協力的です。
どうせ次は注文してくれないから・・・。
メーカーも消極的になってしまい、トラブルについて催促しても対応してくれません。
ユーザーも何回も聞くのが嫌になって、諦めてしまいます。
1つの会社ならそれでもいいのですが、全てのメーカーと同じような関係になれば、ユーザーとしてのメンテナンス体制が弱くなっていきます。
メーカーと良い関係を気付くためにも、メーカーに責任を押し付けないで前に進むような落としどころを見つけていきましょう。
参考
関連記事
最後に
設備トラブルの応急補修が終わった後、原因や対策を考えていくときに、メーカーと議論するにはコツが必要です。
出す情報が少なかったり、責任を押し付けたりすると、メーカーは逃げていきます。
メーカー技術者を捕まえるためにオンライン会議は有効です。
メンテナンス関係など未知の情報をお互いに調べていくという前向きな方向で議論すると、協力的になってくれやすいです。
化学プラントの設計・保全・運転などの悩みや疑問・質問などご自由にコメント欄に投稿してください。(コメント欄はこの記事の最下部です。)
*いただいたコメント全て拝見し、真剣に回答させていただきます。
コメント