化学プラントのガス洗浄や吸収、脱ガス処理などに使われる「充填塔」。設計にあたっては、液とガスの接触効率を高めるための構造やサイズを適切に選定する必要があります。
塔の世界は非常に幅広く例えば棚段塔などがメジャーですが、バッチ系では充填塔一択。塔はいかにも化学プラントという外見的イメージを持てる設備ですが、バッチ系ではほとんど目立ちません。
この記事では、充填塔の基本構造と設計ステップについて、初心者にもわかりやすく紹介します。設計の流れを押さえておけば、仕様書の理解や図面チェックにも役立ちますよ。
この記事は、塔シリーズの一部です。
ガス吸収のために使うプラント設備4選
冷却塔の原理をかんたんに解説
充填塔のフラッディングとは?
塔でガスケットの片締めを起こさないために
排ガス処理塔の設計の基本的な考え方
塔を径だけで適当に決めるバッチ系化学工場
全体構造
充填塔の全体構造を示します。
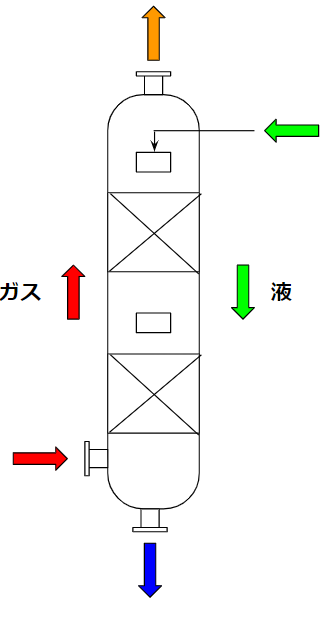
塔はガスと液を接触させるための設備です。
このために多数の工夫がなされています。
原則的にガスは液より重たいので、ガスを下から流して上に流れていき、液を上から流して下に流すという向流接触の構図を取ります。
塔を構成する設計要素を以下に解説します。
充填物
充填物は気液接触を効率よく行うための肝の部分です。
充填塔の中で最も重要な部品が充填物。
気体と液体の流れをあえて分散させることで、特定の領域にだけ流れる(片流れ)を防ぐ目的が充填物には課せられます。
充填物は規則充填物と不規則充填物の2つに大きく分かれます。
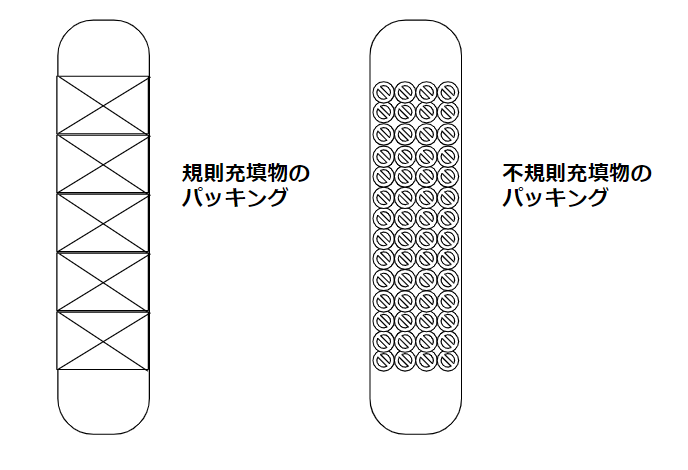
規則充填物は充填物を一定の規則に従って並べて大きな形を作ります。
塔径と同じ径で高さを適切なサイズに決めて1つのブロックとします。
充填塔全体に対して複数のブロックに分けて投入します。
規則充填物の形状は充填塔製作メーカーが独自に開発しています。
不規則充填物は小さな充填物を詰めていきます。
塔径よりも十分に小さな充填物なので、詰めるときにランダム性が出るから不規則充填物と呼びます。
不規則充填物は古くからある技術で、ポールリング・テラレット・カスケードミニリングなど様々なものが開発されています。
充填物の性能という意味では規則充填物の方が有利です。
メンテナンス性という意味では不規則充填物の方が有利です。
切替生産が多いバッチ工場では、コンタミの観点からも不規則充填物を採用する傾向が強いです。
サポートグリッド
充填物を支える部材としてサポートグリッドがあります。
充填物の重量と液重量を支えることが主な使命です。
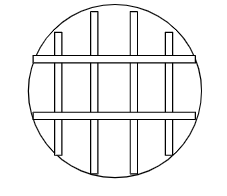
グレーチングに代表されるいわゆる格子状のグリッドで支えることが普通でしょう。
ですが、不規則充填物などでは下のような構造を取る場合があります。
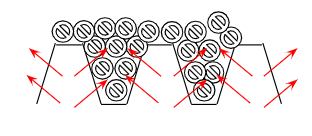
これはガスの流路面積を確保するため。
小さな充填物が落下しないようにするために、1つ1つの穴の面積を小さくすると塔の断面積に対して開口面積が十分には取れない場合があります。
圧力損失が出てしまってフラッディングの原因となりますので、面積確保のために山谷の構造を意図的につけるという思想です。
フィードパイプ
フィードパイプは液を塔内に均等に分散させる機能があります。
いくつもの種類が開発されていて、メーカーに検討してもらうことが基本ですが概要は理解した方が良いでしょう。
形状
パイプ型とトラフ型を解説します。
パイプ型は以下のような構造をしています。
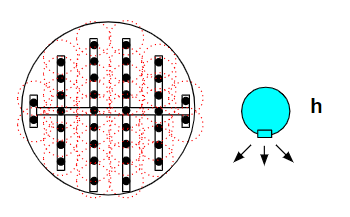
塔の断面積に均等にパイプを枝分けして、断面末端部に穴を開けます。
液がパイプ内に満たされて、開口部から液が流れ落ちて噴霧されます。
こうしてある程度の均等噴霧ができた状態で、充填物に降りかかった液は充填物を落下していく間にさらに分散されます。
パイプは小さな塔径の場合によく使います。
大きな形になると、パイプ内の圧損が効いてくる問題が起きます。
中央部と末端部で圧力が変わって噴霧の均一性が崩れます。
そんな場合にはトラフ側と選びます。
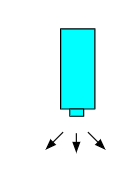
トラフ型はパイプ型のパイプを直方体にしたタイプです。
パイプではないのでポンプ圧力で加圧フィードはできません。
直方体の構造内に液を貯めこんで、液圧の低い圧力でフィードします。
フィードパイプは取り外しができるように分割構造にしましょう。
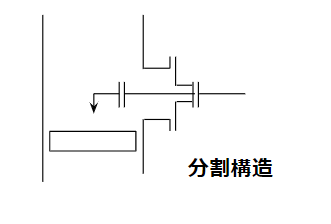
マンホールタイプの大きな穴を開けてフィードパイプが取り外せるようにします。
塔内のパイプフランジのガスケットをフッ素樹脂包みガスケットにする例がたまにありますが、意味はありません。
中芯が腐食します。
フッ素樹脂ガスケットにしましょう。
サポート
フィードパイプのサポートは塔内に設置しましょう。
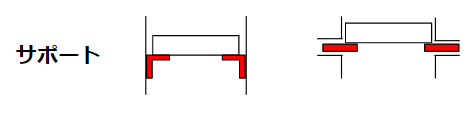
金属系の塔ならアングルを溶接します。
ライニング系ならフランジで挟み込みをします。
仮にアングル溶接でフィードパイプを溶接した場合でも、実は塔のフランジがあった方が良いです。
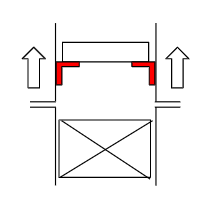
というのも規則充填物を投入しようとしたときにアングルが干渉して、充填物が投入できないからです。
不規則充填物でも投入・取外し作業のためにはフランジがあった方が良いです。
再分散
充填塔の高さが一定以上になれば、再分散パイプを付けることが多いです。
フィードパイプと同じ形状のパイプを塔中段に設置します。
その前に上段に液を集めるコレクターを設置します。
コレクター・再分散パイプという組み合わせです。
構造が複雑になっていきます。
塔径
塔径は運転条件から決める大きな設計要素です。
塔径を小さくしてガス速度が大きくなると以下の問題が起きます。
- 塔前段の圧力が高くなる
- 塔内でフラッディングが起きる
塔径を大きくするとコストが上がるだけでなく、液フィード量も大きくしないといけなくて動力に関係します。
これらの要素を加味しながら、充填効率を考えて充填物を決めるという複合的な設計を行います。
充填物高さ
充填物高さも充填塔の設計要素としては関係します。
とはいえ、定量的な計算で決まる物でもありません。
化学工学の蒸留計算で出てくる段数の概念をそのまま充填塔に当てはめるのが難しいからです。
既存実績に合わせて塔高さを決めているケースは少なくないでしょう。
材質
材質はステンレスとグラスライニングがメジャーです。
ステンレスの場合なら、塔本体・充填物・フィードパイプなどすべてステンレスで統一可能です。
グラスライニングの場合は、フィードパイプは高級金属や樹脂系、充填物はセラミックや樹脂系を選択します。
温度的に樹脂は避ける傾向です。
ガス液の流れで充填物が動いて充填物とガラスが擦れることがとても怖いので、PTFEのシートで本体を養生するという対策を取ることが多いでしょう。
セラミックの樹脂は割れやすいので、特にメンテナンスが大事です。
圧力
充填塔は蒸留システムで使うことが多いので、真空~大気圧下で使うことが多いです。
減圧系での取り扱いの場合には、塔の上下を鏡構造にしておかないといけませんね。
用途
充填塔は反応系での蒸留に使うのがメジャーです。
他にはガス吸収目的で除害設備にもよく使います。
この場合、塩など付着物が溜まりやすいのでSDMで分解清掃をすることが非常に多いです。
環境面に配慮した運転のためにはメンテナンスは欠かせませんね。
参考
関連記事
充填塔に関してさらに知りたい方は、以下の記事をご覧ください。
最後に
充填塔はシンプルな構造に見えて、実際の設計では多くの条件を総合的に判断する必要があります。
特に初心者は、「流れ(プロセス)」を基にした設計手順をしっかり押さえておくと、実務に対応しやすくなります。
この記事を参考に、まずは設計の流れをざっくり把握し、自信を持って図面や仕様書に向き合えるようになりましょう。
化学プラントの設計・保全・運転などの悩みや疑問・質問などご自由にコメント欄に投稿してください。(コメント欄はこの記事の最下部です。)
*いただいたコメント全て拝見し、真剣に回答させていただきます。
コメント