オーナーエンジニアの立ち位置について解説します。
スペシャリストやゼネラリストという単語はどこの職場でも話題になったことがあるでしょう。
化学会社の場合、研究などいかにもスペシャリストという部門もあれば、総務部や製造部のようにゼネラリストという部門もあるでしょう。
そんな中で、化学プラントの機電系エンジニアはスペシャリストであるかゼネラリストであるか、これを機電系エンジニア自身が理解していなかったりします。
電気や計装ならスペシャリストという認識を持っていますが、機械の一部のエンジニアはゼネラリストという認識を持っています。
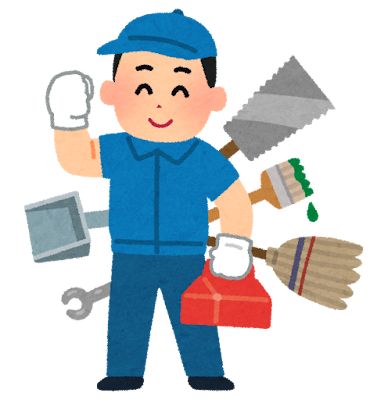
化学プラントの機電系エンジニアはスペシャリスト
化学プラントの機電系エンジニアはスペシャリスト
それが私の主張です。
とはいえ化学プラントの機電系エンジニアはゼネラリストだ!と主張する人もいるでしょう。
ゼネラリストと勘違いしてしまう背景を紹介したうえで、やはりスペシャリストだという主張をしたいと思います。
ゼネラリストである論拠
バッチ系化学プラントのエンジニアは「広くて浅い」です。
これは例えば研究や設備メーカーに比べれば、間違いないです。
これをもとにゼネラリストだと主張する人が居ます。
設備メーカーに依頼する
プラントエンジニアは、経験の浅いうちは、特に化学プラントの設備メーカーに言いくるめられるシーンが多いです。
化学プラントの設備メーカーは別に化学プラントの詳細を知っているわけではありません。
自社で扱っている商品を、プラントエンジニアに説得することに全力を費やしています。
彼らはプラントエンジニアの会社にとって最適な商品を売っているとは限りません。
それでも、経験の浅いプラントエンジニアは設備メーカーの言うことを信じてしまいます。
上司に報告するときに「設備メーカーがこう言ったから」という理由だけを押してくる人があまりにも多いのがその証拠。
プラントエンジニアは設備メーカーに丸投げする風潮が強くて、単なる伝言ゲームと化しているケースが多いです。
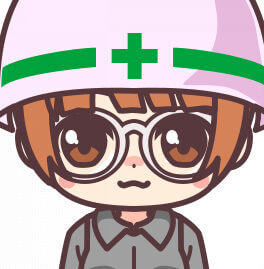
メーカーがこれが良いって言っていました!
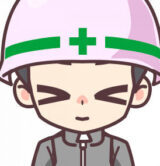
そうですか!それにしましょう!
これではプラントエンジニアは何の仕事をしているか分かりません。
これは業界や組織の構造上、どうしようもありません。
作る人・組み上げる人それぞれの立場があります。
そこでどちらがいい・悪いという話ではありません。
それでも「深くて狭い」ことはデメリットが多く、私は不満を持っています。
- 深く検討した割に、結果が大したことない(進歩が見込めない)
- 自分の世界にこもった説明で、他の人は理解できない
- はっきりと決断できない
こういう特徴は、深くて狭い仕事にありがちです。
そういう仕事の成果をくみ上げることがいかに大切で、大変か。
組み上げ型の仕事をしている人なら理解します。
組み上げ型の仕事をしている人が技術力がないというわけではありません。
狭くて深い仕事をする専門家の話を聞いて理解できる力は必要です。
多くの専門家の話を集約するために、膨大な知識が必要。
試しにポンプメーカーに熱交換器の話をしてください。
普通は全くついてこれませんよ(笑)
どちらがいい・悪いではありません。
機械・電気・計装・土建が力を合わせる
化学プラントの設備設計エンジニアは自分1人だけでは仕事が進みません。
機械・電気・計装・土建それぞれのスペシャリストが集合してやっとエンジニアリングが完成します。
機械の設備設計エンジニアなら機械の設計業務を習得していきますが、機械設計だけを知っていても仕事はできません。
接点業務という電気・計装・土建などと協力する部分の理解が乏しいと、
調整に多くの時間を割いて出戻り・やり直しが多く発生します。
4者のとりまとめ役になりがちな機械設備設計エンジニアは自分があたかもゼネラリストであるかのように錯覚します。
スペシャリストである論拠
機電系エンジニアがスペシャリストである理由を紹介しましょう。
10,000時間で成長速度は鈍化
一般的に言われることとして、10,000時間使えばエキスパートになります。
10,000時間って約5年です。
化学プラントの設備設計エンジニアの場合もこの法則に当てはまります。
実際には7~9年が必要ですが、程度の問題。これは業務スパンと業務1サイクル当たりの時間が関係します。
それ以上同じ部署で仕事をしても、学ぶことはどんどん減っていきます。
これくらいマスターまでに時間が掛かる仕事はスペシャリストと言って良いでしょう。
自社工場に特化したエンジニア
化学プラントは非常に多くの設備で構成されています。
バッチ系化学プラントの典型的な1工場を取ってみても、
- 設備数で200基以上
- 配管距離で10km以上
- 計装設備数で1000点以上
膨大な量があります。
この設備を1点ずつ設計し、配管を1ラインずつ設計する1点設計の極み。
この設計は他社や他の事業所では通用しない技術かも知れません。
ある程度の標準的なユニットを組むことは可能ですが、採用できる設備の選択肢はかなり多いです。
ろ過だけをとっても、遠心分離機だけでなく加圧式ろ過機もあります。
これだけでもろ過設備の数が多いと、組み合わせの問題で選択肢は増えていきます。
同じプラントはこの世の中で2つ存在しないなんて言われますね。
こういう設計思想そのものがスペシャリスト。
工場の情報が集まらない
化学プラントのエンジニアリング部門には工場の情報が集まってきません。
これだけでも機電系エンジニアがスペシャリストと言って良いでしょう。
本当にゼネラリストであれば、工場内の様々な情報が入ってきます。
そんな場所は製造部しかありえません。
製造部を経験したことがないからこそ、機電系エンジニアは「もしかしてゼネラリスト?」って勘違いしてしまうのでしょう。
試製造の経験をしたら分かりそうなものですが、その時は忙しすぎてゼネラリストとかスペシャリストとか考える余裕がないかも知れませんね。
業務サイクルが長い
機械設計業務は1年サイクルです。
1年以上経たたないと一通りの仕事が体験できないって、それだけでもスペシャリスト。
ゼネラリストはもっと短いサイクルでいろいろ回します。
ゼネラリストは周りのスペシャリストに依頼するのが仕事で、複数の案件を様々な部署に依頼します。
この時、1年以上経たないと結果が返ってこないものあれば、1日で返ってくるものもあります。
基本的には短いサイクルでPDCAを回せるし、細かい検討を時間を掛けることもないので、
仕事の全体像を把握するのは比較的早いのがゼネラリスト。
ゼネラリストである製造部なら1年でかなりの業務を習得できます。
化学工場ではゼネラリストは製造部
化学プラントの製造部はゼネラリストです。
製造部は日常運転において徹底した組み合わせ型の仕事をしています。
原料・生産・用役・廃棄・分析・環境・人事・設備
生産活動に関わるあらゆる要素を組み合わせて指揮します。
プラントエンジニアの広くて浅い、とは次元が違うレベルで広くて浅いです。
井の中の蛙大海を知らず。
まさにこの状態です。
この目線で見ると、プロセスエンジニアは生産の機電系エンジニアは設備のスペシャリストです。
広くて深い仕事。絶望的になりそうですね。
でもそうではありません。
広さや深さの差が分野分野で違うだけです。
プロセスエンジニアから基本設計情報をもらう立場である設備エンジニアは基本設計の情報でかなうはずがありません。
ところが、機器の詳細設計をして配管設計をした段階では、プロセスエンジニアはほとんどついてこれません。
フェースが変わると態度や対応が変わって、専門分野がはっきり見えてきます。
この意味で、製造部の人は支援部隊に依頼したり教えを乞う立場になったりして、態度としては分かりやすいですよ。
外部エンジニアは超スペシャリスト
外部エンジニアは完全なスペシャリストです。
機械は機械だけ、電気は電気だけ、でも恥じることなく立派な仕事ができます。
担当業務のエンジニアリングのことだけを考えればいいわけですから。
工場の建設・保全など設備の一連を通してみないといけない、オーナーエンジニアに比べればスペシャリストに特化するのは当然です。
外部エンジニアがスペシャリストだから、オーナーエンジニアはゼネラリストだ!って勘違いしそうになるのが問題ですよね・・・。
どっちも同じスペシャリストですよ。
関連記事
さらに知りたい方は、以下の記事をご覧ください。
最後に
化学プラントの機電系エンジニアの立場がスペシャリストであることを解説しました。
ゼネラリスト・スペシャリストそれぞれの立場の主張を考え、ゼネラリストである製造部とスペシャリストである設備メーカーとの比較をしています。
私のスペシャリストとしてのキャリアの概要も記載しました。
化学プラントの設計・保全・運転などの悩みや疑問・質問などご自由にコメント欄に投稿してください。(コメント欄はこの記事の最下部です。)
*いただいたコメント全て拝見し、真剣に回答させていただきます。
コメント