ポンプのメカニカルシールからの漏れは、プラント運転でもトップクラスの課題です。
- 対策を取ったつもりでも取れていない
- そもそも対策の取りようがない
- メカニカルシールは壊れるものだと割り切っている
いろいろと考えがあると思いますが、原因と取りうる対策は理解していると、可能性は広がっていくと思います。
運転方法に依存しやすいので、整理して考えていきましょう
摺動面から漏れる
メカニカルシールの漏れは、摺動面から起きることが一般的です。
摺動面とは固定環・回転環からなるシール部ですね。
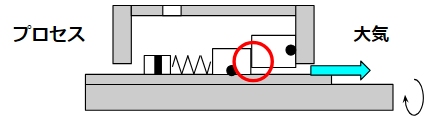
ここから漏れることが、メカニカルシールでは多いです。
他にも実は漏れる要素があって、2次シールと呼ばれるOリングやガスケット部からも漏れる可能性はありますが、圧倒的に摺動面からの漏れが多いです。
異物
メカニカルシールの摺動面が漏れる最大の原因は異物です。
清浄液でメカニカルシールから漏れが起きることは、そうそうありません。
異物があるとなぜメカニカルシールは漏れるでしょうか。
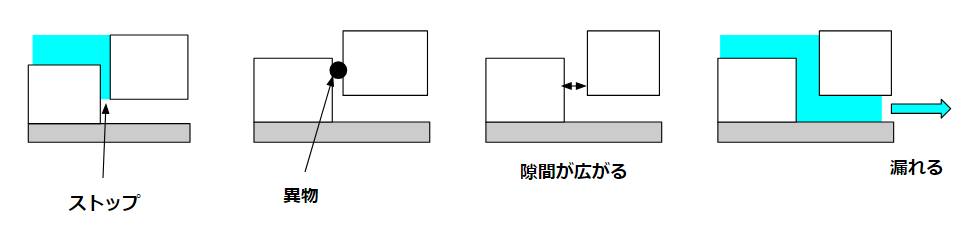
メカニカルシールは、摺動面と呼ぶ非常に小さな隙間部があります。
ここまで液体は到達しますが、隙間が小さすぎるためにそれ以上進むことはできなくなります。
こうして、液体の漏れをストップさせるのがメカニカルシールの機構。
ところが、異物が入り込んだとしましょう。
例えば、錆や結晶が典型的な異物です。固形分と考えて良いでしょう。
この状態で摺動面が動くと、摺動面には傷が入っていきます。
この傷が成長していくと、隙間が広がっていきます。
隙間がある程度以上大きくなると、液体がすり抜けてしまいます。
異物により摺動面が傷つき、漏れが起きる
冷却不足
冷却不足によってメカニカルシールから漏れが起きます。
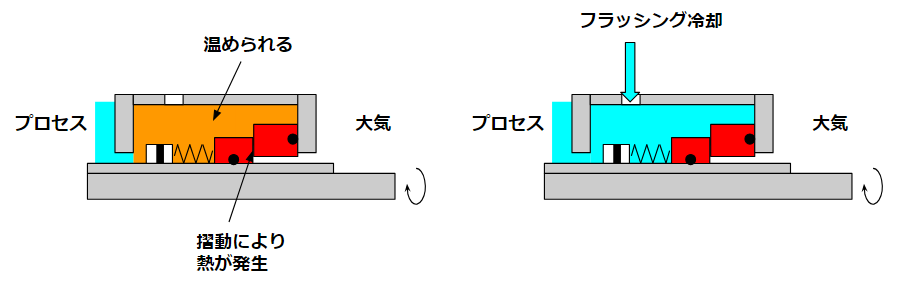
メカニカルシールが動いている間、摺動部には熱が発生します。
メカニカルシールボックスと呼ぶメカニカルシール周辺のケーシング内の液体は、プロセス液よりも温められた状態になります。
温められた液体は摺動部を冷やす能力は無くなり、摺動面はさらに熱を持って破損の原因となります。
だからこそ、フラッシングなどの冷却液で、メカニカルシールボックスを常時冷やさなければなりません。
冷却液がないと、一瞬で漏れが起きます。
冷却不足で摺動面が傷つき、漏れが起きる
取れる対策
メカニカルシールの漏れ対策として、できることを紹介します。
運転前のチェック
運転前までにできる対策を並べていきます。
- ポンプ据付が正しくされている
- 冷却液が通っている
- ライン洗浄をして異物を取り除く
ポンプが適切に据え付けされているという点は、ちゃんとした施工会社に依頼していたら通常は問題になりません。(もちろん素人では駄目です)
冷却液が通っていることは大前提ですが、バルブの開け忘れなど起こりえます。
ライン洗浄も、通常ならテンポラリーストレーナーを使うなどして徹底しますよね。
ここに書いていることは、当たり前のことを当たり前にしておきましょう、という意味です。
それでも漏れるのがメカニカルシールですね。。。
定期メンテナンス
メカニカルシールの定期メンテナンスは必須です。
動機器である以上、ノーメンテナンスは絶対にダメ。
摺動部など摩耗によるダメージが蓄積されていきます。
TBM,CBMどちらでも良いので、部品交換をしていきましょう。
冷却液の選定
冷却液の選定は、メカニカルシールでもかなり難しいです。
メカニカルシールで発生した熱を奪うだけなら、常温の水などでOKの場合がほとんどです。
問題は、水が入ったらダメな系、温度が高かったり低かったりで水が使えない系です。
水が入ったらダメな場合は、外部フラッシングで溶媒を流したり、ダブルメカニカルシールで緩衝液に溶媒を入れて外部冷却するなどの、複雑な対応が必要です。
この辺りになると、手動での対応は煩雑になるので、自動化していかないといけないでしょう。
プロセス温度が高い場合に水を入れると、水が沸騰してメカニカルシールにダメージを与えたり、プロセス温度が冷えて結晶が出たりします。
この問題は、バッチ運転では非常に多いです。
プロセス温度が引く場合は、水が氷になってメカニカルシールにダメージを与えます。
ブラインが考えられますが、セルフフラッシングにすると詰まりの原因になってしまうので、悩みとしては複雑です。
断熱は疎かにできない
メカニカルシールには断熱をしなくていいだろう。
バッチ運転経験者なら、そう思う人もいます。
ところが、バッチ運転でもメカニカルシールの断熱をシビアに考えないといけない場合があります。
70~80℃以下になると結晶が出るプロセス液です。
この場合には、冷却水の温度も問題ですが、メカニカルシールが外気で冷やされないように断熱をしましょう。
本来ならこの部分は、冷却液と合わせてメカニカルシールで発生する熱を外に逃がす部分です。
断熱を付けてしまうと、冷却液だけが頼りになります。
詰まりがないか流量確認が特に大事なるでしょう。
運転後の洗浄は必須
運転後はポンプの洗浄をしましょう。
連続運転の場合なら全系統の洗浄になります。
バッチ運転は、バッチ間の洗浄が欠かせません。
- ポンプでプロセス液を送った後は、タンク内に洗浄液を入れてポンプ側に流す
- ポンプ吸い込み口に洗浄液ラインを付けて、洗浄を行う
このどちらかが必須です。
プロセス液で完全な綺麗な液体であれば考える必要はありませんが、大抵は何かしら異物があります。
安定運転状態なら問題なくても、品質異常などで結晶が出る場合もあれば、原料中に異物があったり、設備が破損して異物となる場合もあります。
一見無駄に見えるかもしれませんが、何が起きてもおかしくないという前提で、ポンプ周りの運転を統一化させておく方が安心です。
参考
関連記事
最後に
ポンプのメカニカルシールから漏れる原因と取れる対策を考えました。
異物と冷却不足が大きな原因です。
運転前のチェックと定期メンテナンスが基本対応になります。
冷却液の選定・断熱の有無・運転後の洗浄などの対応が、運転条件によって変わってきます。
化学プラントの設計・保全・運転などの悩みや疑問・質問などご自由にコメント欄に投稿してください。(コメント欄はこの記事の最下部です。)
*いただいたコメント全て拝見し、真剣に回答させていただきます。
コメント