日本の化学プラントでは、日本製の設備や部品への信頼が根強く、多くの企業が「国産=高品質・安心」と考えています。とくに海外の拠点でも、日本製機器をそのまま輸出・導入する企業も少なくありません。そして痛い目を見た会社も多いことでしょう。
2020年以降のサプライチェーンの混乱や地政学的リスクの高まりにより、「日本製だから安心」とは言い切れない時代に突入しています。
本記事では、日本製に過度に依存することのリスクや、設備調達における現実的な視点について掘り下げます。
メンテナンスではサプライチェーンも考慮すべき対象になりますが、設計段階では無視されがちです。この辺の考え方は、残念ながらなかなか転換しにくいでしょう。ユーザーレベルでは気が付かないうちに複雑化している設備調達の課題について、考えていることをまとめました。
【原則】設備ベンダーはできるだけ地元がいい
化学プラントの設備は、そのベンダーがとにかく地元の方が好ましいでしょう。
設備的には動機器であるポンプや減速機などがターゲットとなりがちですが、静機器であるタンクや熱交換器も似たような発想です。
この考え方はあくまで原則なので、とても満足できないような地域もあるでしょう。
その場合は、輸送費や輸送時間がプラントの安全安定運転のコストとして加わってきます。
同じ会社で複数の事業所の設備保全エンジニアが議論するときに、メンテが充実していている工場とそうではない工場が見つかったときは、まずはこの辺の地域差を疑ってみましょう。
タンクなどになると部品というよりは補修ができる作業員という問題になります。僻地だとそういう鉄鋼会社が少なかったりします。
【現実】遠くてもアフターケアが良いベンダーを選びたい
多くの会社はコンビナート地域に工場を持っていますが、微妙に離れていたりする場合もあるでしょう。
現実的にはいくつかの妥協をしないといけません。
この場合には、遠くてもアフターケアが良いベンダーを選ぶことになるでしょう。
- 電話をしたらすぐに連絡が取れる会社
- メールの対応が早い会社
- 取引が多く優先度を上げてくれる会社
- 自社で在庫を一定数以上確保してくれる会社
- 何かあったらハンドキャリーで運んでくれる会社
こういう会社があれば、ぜひとも長いお付き合いをしていきましょう。
イニシャルだけを見るエンジニア
保全を担当していると、ベンダーによる対応の違いに頭を悩ませることが多いです。
そうしているうちに、「なぜこのベンダーの設備が導入されているのだろう」と疑問に思うことも出るでしょう。
いくら不満を言っても改善されずに諦めてしまっている人もいるかもしれませんね。
調達をする側の設備設計エンジニアの目線では、実はこんな苦労を知らずに「イニシャルコスト」だけを見て選ぶ場合が多いはずです。
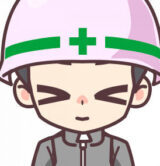
プロジェクトとして投資額を予算内に抑えないといけない。だからイニシャルが安い会社を選ばざるを得ない。
これくらい思ってくれていればいいのですが、現実には・・・
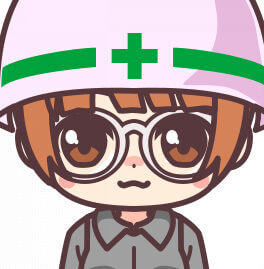
安い会社だからそれでいいでしょ。
くらいの浅い発想で選定して、その後は設備保全エンジニアに引き渡し。なんてケースも見られます。
調達部は工場のことすら考えずに、金額しか見てないという人もいるくらい。
プラントエンジニアリング会社が入ると、オーナーエンジの時よりももっと露骨にイニシャルで判定されます。
「嫌なら建設後に取り替えたらいいでしょ?」って発想です。間違ってもいませんが、最初の苦労を現場に押し付ける格好になります。
海外工場でも日本製を導入する?
海外(日本以外)に工場を建設したことのある日本企業なら、特定の設備は日本から輸出することもあるでしょう。
特に重要度の高い機器だからコスト低下は度外視する、という思想です。
これは後で苦労するパターンです。
海外の工場から見たら、日本製が「外国製」になります。
特殊な機器であるほど、部品も特殊になります。メンテナンスできる人も限られます。
SDMの時期や頻度がすごく制限されます。
マニュアルも現地の人にとっては分かりにくい物をあり(そもそもマニュアルなんて見ないかも・・・)、現地の運転員の思想とも会わない機器だったりします。
例えば、機器は壊れるもの・壊れたらすぐに直せばいい、という発想で運転する人だらけの場合は、海外製はとても使いにくくなるでしょう。
こういう場合は、慎重に扱ってね!機器を大事に!というようなTPM的な発想を醸成するまでに、機器が壊れてしまうかもしれません。
それくらいだったら、現地で手に入る「劣化品」を複数台の予備を持たせる方が良いと思います。結局安心感を変えます。
【妥協】海外製ってそんなに悪い?
日本製だけで調達しようとすると限界があるので、海外調達をしようとしても抵抗感を持つエンジニアは多いでしょう。
海外調達が進まない会社は本当に進みません。
「できるだけ地元で」という発想からしたら、海外製はその真逆の発想です。
導入しようとしたらそれなりに考えるべきことがあります。
- 実績があるかどうか
- 生産拠点
- 日本の支社や商社があるか
- 日本国内でメンテナンスができるかどうか(サービスマン、在庫)
- 日本国内で販路を広げていく予定があるかどうか
こういうヒアリングをベンダーに対して行うでしょうが、どれも「決め手」にはならないはずです。
というのも、実態が良く分からないからです。
導入の時には、メーカーは良いことしか言いません。その後の対応では、「できない」の連発をするというケースはいくらでもあります。
海外ベンダーを調達するときも全く同じです。
だから、何だかんだと日本製が良いですよねって結論になりがちです。
でもこれって本当ですか?
2020年のコロナ禍以降、サプライチェーンを揺るがす問題が多発していますよね。
PTFEや半導体なんてかなり手に入りにくくなっています。
- ガスケット
- Oリング
- メカニカルシール
- モーター
- インバータ
こういう部品、本当に手に入らないですよね。
これ、日本ベンダーだから手に入らないという可能性はありませんか?海外ベンダーの日本支社なら流通がマシという可能性はありませんか?
私は今、この辺りの世界で悩んでいます。
海外ベンダーなら、杓子定規な対応だけで突発の納期対応に答えてくれないという先入観はありませんか?
日本製を過信しているけど、実態として競争力はかなり落ちていて、サプライチェーンも回りにくくなっていて、「ユーザーのわがまま」に対応できない日本ベンダーが増えていますよね。
少しギャンブル的な要素があるかもしれませんが、日本製にこだわって考えが固定化されてしまう方が危険な気がします。
なんというかJTC的な思考ではなさそうですけど・・・。
JTCの中でもちゃんとしている会社は、とっくに海外調達も含めて複数ベンダー化が確立しているでしょう。古い体質のJTC(ちょっと意味が分かりませんが・・・)なら、とにかく日本製!といいがちです。この記事の対象はそんな古い体質のJTCの保全です。
参考
関連記事
最後に
日本製への信頼は揺るぎないものがある一方で、それだけに依存するのは危険です。サプライチェーンの混乱や海外拠点の事情を踏まえると、「柔軟な設備調達体制」こそがこれからの保全の鍵になります。
「できるだけ地元で」「アフターケアを重視」「海外製も選択肢に」というバランスの取れた視点が、今後の化学プラントの設備調達には求められます。
日本製の質やサプライチェーンの悪化に伴って、海外ベンダーも悪くないのでは?という発想がより強くなっていくと思います。
化学プラントの設計・保全・運転などの悩みや疑問・質問などご自由にコメント欄に投稿してください。(コメント欄はこの記事の最下部です。)
*いただいたコメント全て拝見し、真剣に回答させていただきます。
コメント