抽出を実現するためのミキサーセトラーについて解説します。
抽出とは2つの異なる物体に対して、1つの物体のある成分を別の物体に移す作業です。
例えばコーヒーの抽出なんて表現もします。
これは固体のコーヒー成分を水である液体に抽出するという意味。
同じように、2つの異なる液体間でも抽出が行われます。
化学プラント的にはこのケースの方が多いです。
方法は連続・バッチの2つがあります。
連続抽出ならミキサーセトラー、バッチ抽出なら反応器をそのまま使います。
反応器を使う方が汎用性がありますが、無理やり装置を組み上げるという表現に近くなります。
この無理やりで装置を構成してプロセスを作り上げれるのが、バッチのメリットでしょう。
ミキサーセトラー(mixer settler)
ミキサーセトラーの典型的な例を紹介します。
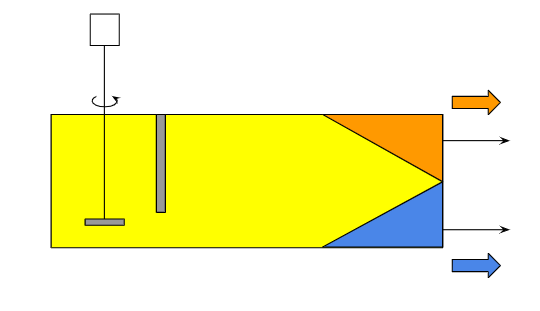
これは連続的に抽出と分液を行うための装置です。
抽出をするための撹拌槽部分(ミキサー)と、分液を行う分離機部分(セトラー)の2つを結合した方式です。
撹拌されて水と油が混じり合った状態で分離機にフィードされると、自然と分離する方向に移動します。
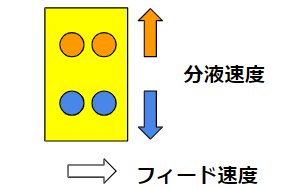
これは水と油が溶けあわないから。
どれくらいの速度で分離すかを示す指標として分液速度という表現を使います。
連続的に抽出をする場合、プロセス液は連続的にフィードされます。
「フィード流量/装置断面」で決まるフィード速度が設計指標となります。
装置サイズを長手方向にL、高さ方向にHと取りましょう。
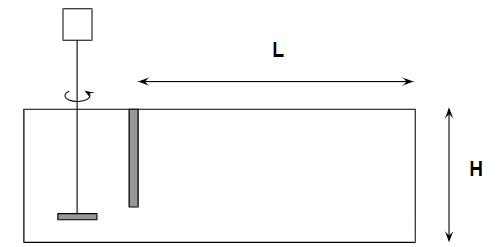
分液速度・フィード速度はL・Hと時間という単位で比較が可能です。
- 分液時間 = H/分液速度
- フィード時間 = L/フィード速度
分液時間 < フィード時間であれば分液は十分に可能という評価です。
こういう重力沈降を利用した分離機は長さLを伸ばすほど有利に働きます。
ミキサー部のタンク寸法にHが縛られやすく、Lと奥行き寸法もそれなりの制約を受けます。
自由度が低くなりますが寸法や装置を最小化できるので、運転条件が決まって固定化されるような連続処理に向いています。
設計の自由度を増やそうとしたら、ミキサー部とセトラー部を完全に分離して別の装置にします。
タンク自体は圧力を持たないので角槽、温度もほぼ常温という緩やかな条件が多いです。
反応器
反応器で抽出操作を行う場合を考えましょう。
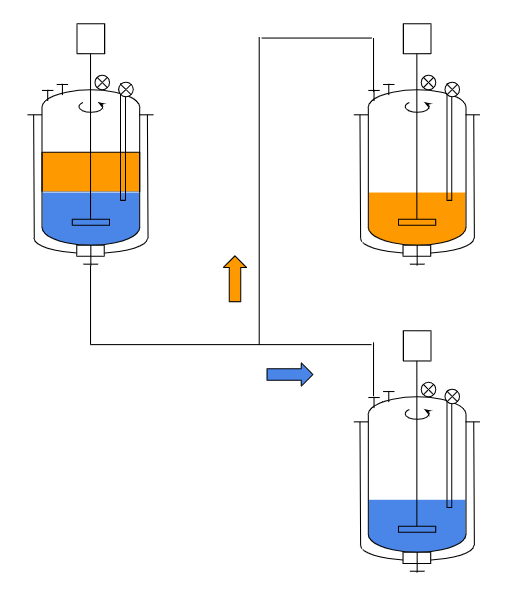
1段目の反応器でプロセス液(油)に水を注入します。
その後、一定時間静置しておくと水層と油層に分離します。
分離の速度は主に密度に依存します。
粘度にも若干の依存性があります。
- 温度が低い方が密度差が出やすい傾向
- 温度が高い方が溶解度が増える方向
このバランスなどを考慮して抽出の温度を決めていきます。
抽出を1回で終わらせずに2回行う場合は、抽出後のプロセス液(油)に水を入れて同じ操作を行います。
2回目の抽出も1段目の反応器で行うことが普通ですが、場合によっては2段目の反応器で行う場合もあります。
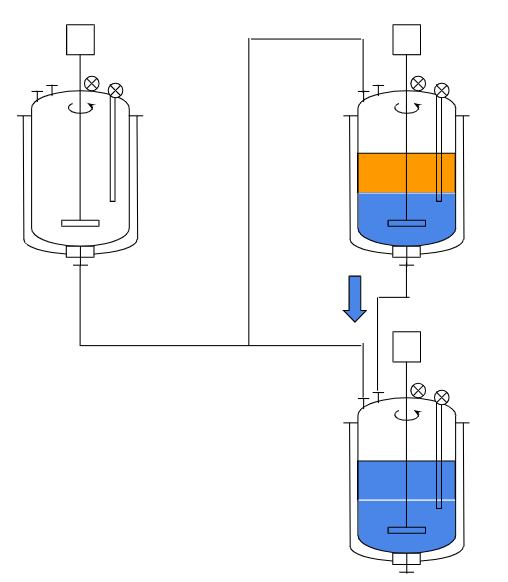
ラインが複雑になったりポンプが必要になったりと課題がありますが、汎用性は広がります。
設備のトラブルがあっても運転を継続できやすくなります。
撹拌機の設計
抽出に対して撹拌機を最適に設計するということはあまりありません。
悪く言うと「混ざれば何でもいい」という思想が多いです。
- 羽根は適当にパドル翼
- 速度調整のインバータは付けない
- 軸封はグランドパッキン
- 材質はステンレス
バッチプラント的には安物の装置という扱いです。
参考
ミキサーセトラーのような設備は化学工学としては典型例です。
液体の流れや混合抽出といった概念が分かるようになると、理解もしやすいでしょう。
以下のような本がおススメです。
参考
関連記事
さらに知りたい方は、以下の記事をご覧ください。
最後に
抽出装置の例として連続向けのミキサーセトラー、バッチ向けの反応器を紹介しました。
抽出操作としての攪拌機の設計はあまり重要ではなく、重力沈降を利用した分液が課題になり、必要な装置構成が増えていきます。
自由度の多さを取るかどうかで思想が分かれるところです。
化学プラントの設計・保全・運転などの悩みや疑問・質問などご自由にコメント欄に投稿してください。(コメント欄はこの記事の最下部です。)
*いただいたコメント全て拝見し、真剣に回答させていただきます。
コメント
ミキサーセトラーは装置であり、抽出は選択的抽出剤が重要です。いま、エマルションフロー方法が、コスト、運転操作の面で、有利と、宣伝されてますが、いかがですか?
単純な抽出を目的とするなら、エマルジョンフローは魅力的です。
ただ、個人的には「運転時に苦労するだろうなぁ」と思います。
思いつくままにコメントします。
・入ってくる液の組成が安定している
・運転条件や分離性能が多少触れても製品に影響がない
・洗浄方法やメンテナンスはどうするのだろう
・運転状況の監視や世寿命評価はどうするのだろう
・流量、圧力、材質はどこまで可能なのだろう
・ミキサーセトラーですでに長年実績がある場合、あえて変える理由が少ない
気になることは多いですね。