化学プラントでの設備や機器の海外調達は、コスト削減の手段として注目されがちですが、実際には多くのトラブルやストレスの原因になります。特に実務レベルでは、設計や運用の現場が振り回されることも少なくありません。
本記事では、現場視点で語る「なぜ海外調達はうまくいかないのか」を解説します。
基本的にその地域で手に入る物を使うというのが安定生産において大事なこと。プラント建設レベルの一過性のイベントなら、その地域外から物を調達するということも考えられるでしょう。また、一時の日本のように、コスト競争力を求めて海外調達を考える場合もあります。
今回は日本の化学プラントに対して、海外メーカーから調達する場合について解説します。
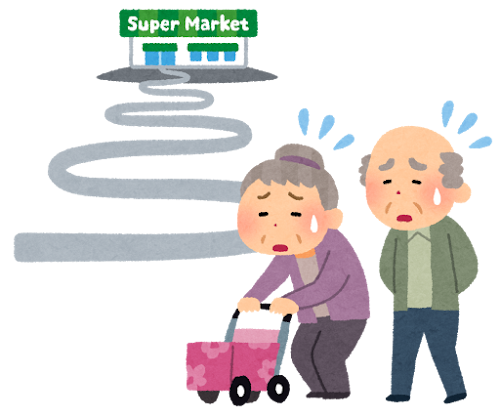
化学プラントの海外設備メーカーに対する考え方
化学プラントで海外設備メーカーの新規調達が進まない理由を紹介します。
調達部が海外を知らない
調達部は一般に海外を知らないローカル社員だらけです。
彼らは国内の仕事は当然回せます。
しかし、海外になると途端にハードルが上がり、関わりたくないという思考が働きます。
これは個人としては心情的には理解できます。
国外の知らない会社に急にアポイントを取るのですから。
でも、調達部は新規ベンダーを調査することは日常的な仕事です。
新規ベンダーの調達先を開拓するためのマニュアルがあってしかるべき。
海外の新規ベンダーの開拓が進んでいない会社は、このマニュアルが不足しています。
そういう意味で「調達部が海外を知らない」と言えるでしょう。
調達部が独断と偏見で決める
調達部は新規ベンダーを開拓するときには、エンジニアの主張は無視して調達部のロジックを優先します。
ここで調達部の眼に止まった会社に対して、エンジニア側に連絡を掛けます。
エンジニアがいくら新規ベンダーを調査しようが、
調達部が「嫌」と言えばそれまで。かなり理不尽です。
その理由は、会社間の話というような政治的な話が多いようです。
調達部の個人としても新規ベンダーを開拓したいのに、会社として許されない。
そういう圧力が働きがちです。
こういう情報は、一般に社内で共有されません。
その結果、エンジニアは調達部に対して不信感を抱きます。
こういう例、今の日本で多いですよね。
調達部が日本の仕様にこだわりすぎる
海外ベンダーを調査するときに、調達部が日本の仕様に拘り過ぎる例が多いです。
日本と同じ仕様では作れる会社を見つけれなかったから、海外ベンダーは採用しない。
こんなロジックを真顔で言うのが、調達部。
調達部がエンジニアの要求仕様を熟知しているわけでもないのに、これ。
海外ベンダーを採用したくないという想いがヒシヒシと伝わります。
仕様の例をいくつか紹介しましょう。
材質に拘り過ぎる
【日本】SUS304 → 【海外】SUS304相当
【日本】ハイテンボルト → 【海外】ハイテンボルト相当
どちらの例も材質の話です。
日本と同じ組成の材質で作れるはずがないのに、日本の仕様を要求して作れません。
こういう報告が普通に行われます。
ハイテンボルトはオリンピック需要で、2019年ごろに大問題になりましたよね。
寸法に拘り過ぎる
【日本】JIS10k → 【海外】ASME
フランジ規格の話です。
JIS10kフランジで製作できないから、そういうメーカーは採用しません。
この例も非常に多い。
設備本体のフランジなら、圧力温度さえ持てばフランジ規格はどこの国のでもいいし、
配管との取り合いフランジなら、規格違いのフランジを接続する単管を作るだけ。
それだけなのに、エンジニアに相談なくベンダーの採用を拒否する調達部だと、海外ベンダーの開拓は進みません。
エンジニアのこだわりが強すぎる
海外ベンダー開拓では、調達部の責が強いですが、エンジニアも傾向はあります。
エンジニアも日本仕様に拘りが強すぎると、海外ベンダーの開拓が進みません。
例えば以下のようなこだわりを持ちがちです。
- 材質
- フランジ規格
- 溶接方法
- 予備品
材質やフランジ規格は調達部も共通認識を持っています。
だからこそ調達部が独自判断でベンダーに聞いてしまって、拒否してしまうのですね。
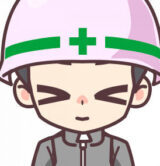
溶接方法はエンジニアである私もちゃんと理解していないのに、
日本の溶接より弱そうだから不安
という理由だけで新規ベンダーを拒否するケースがあります。
溶接方法の違いが、設備の寿命や安定生産にどれだけ影響があるかを判断せず日本と違うからダメっていうロジックです。
この話は、設備の配管ノズルの当て板を何mmにするかとかそういう世界の話ですよ。
予備品はエンジニアとしてはこだわりたいところ。
こだわりが強すぎると、海外ベンダーの採用を妨げます。
ユーザー側で予備品を持つ余裕が無いから、新規ベンダー側で確保すること。それも日本国内で。
こんな感じです。ケースバイケース。
日本の商社経由で海外ベンダーを採用した場合に、この問題が起きます。
100%とは言いませんが、かなりの確率で在庫・予備品問題に衝突します。
コスト
化学プラントの設備を海外調達するのは「安さ」つまりコストに目を向けています。
20年以上前に海外に工場を建てた企業も、大半は「安さ」を求めてのこと。
その後、どういう展開になったかは企業によって大きく変わりますが^^
このコストを化学プラントの設備という面で解説します。
人件費が50%以上安い
海外で製品を調達する場合、人件費の安さに目を向けます。
日本より人件費の安い場所で作れば、工数は当然下がります。
化学プラントの設備加賀君の場合は「製作費」という項目に計上されます。
同じ設備を日本の会社と海外の会社の2つで競争見積を取ると良く分かります。
例えば500万円のタンクがあった場合、日本では人件費は200万円のオーダーです。
これが20年前の中国では人件費が約1/10つまり20万円程度。
安すぎますよね^^
今では1/3~1/2のレベルまで高騰しています。
それでも100万円程度のメリットがあります。
人件費が安い地域で制作する場合、作業効率が低くて製作日数が伸びる傾向にあります。
とはいえ、設備を作るために必要な日数が多少伸びても、単価が安ければ、人件費は安くなります。
材料費が安い
海外調達をする場合、材料費も安い傾向にあります。
これは材料を作る会社の人件費も安いからですね。
というよりは単純に物価が安いという表現の方がいいでしょうか。
地域によっては日本と同等の材質を調達できるとは限りません。
その分、日本よりも材料費が上がる可能性があります。
そこは運転条件と材料の耐食性、運転管理やメンテナンス体制との相談になります。
輸送費が高い
海外で設備を製作する場合、輸送費は当然高いです。
日本の場合、島国という特徴から国外で設備を調達する場合は海送に頼ります。
海上輸送はコストが急に跳ね上がります。
化学プラントの設備の場合、熱交換器のような小物だとコスト面では有利です。
タンクの場合は空気を輸送しているに近いという表現をします。
また、化学プラントの設備の場合、オーダーメイドで数量が少ないため輸送費の削減しろがほぼありません。
大きなコンテナに1基だけ設備を入れて輸送するなんていうもったいない構図も出てきます。
欧米から調達する場合は、このコストが非常に高価になります。
汎用的なポンプなどを部品単位で大量に輸送して、日本国内で組み立てる場合は輸送費を削減できる可能性があるでしょう。
管理費が高い
化学プラントの設備を海外調達する場合、管理費が上がります。
人件費が安い国で作る場合は、現地で制作が進んでいるかどうかを確認するために
監視人のコストが乗ります。
純粋な人件費が管理費としてプラスされます。
例えば、1か月50万円の監視コストが乗ると、日本で500万円のタンクを200万円で作れる国があっても、製作日数が6か月を越えると、海外で作る方が損をします。
200+50*6=500という計算ですね。
欧米などの先進国の設備を購入する場合は、部品管理のコストが乗ります。
欧米からの調達は部品での大量輸送を前提とした設備なので、ポンプなどの動機器に限定されます。
これは当然ながら故障していくので、メンテナンスのための部品を定期的に調達しないといけません。
これが管理費としてプラスされます。
数量
化学プラントの設備を海外調達する場合は大量購入が基本です。
金額に直結するというのも1つの理由です。
海外調達に関する金額の記事も確認してください。
金額以外にも大量購入するメリットや注意点について紹介します。
大量購入するメリット
化学プラントの設備を海外調達する場合のメリットについて紹介します。
設計期間が短縮できる
同じ仕様を大量購入をする場合、設計時間が短縮できる可能性がでます。
1基1基の設備について個別に仕様を決めたとしても、大量購入をする場合は思想が似てきます。
同じプラントの複数のタンク・複数の熱交換器というように、設備に求められる特性が似るからです。
1つの設備思想を理解できれば、残りの設備は微小な差だけ注意すればOK
大量購入をする場合は設計期間が短くとれるメリットが出ます。
製作時の間違い要因が減る
同じ仕様を大量購入をすると製作時の間違いが減ります。
製作時間が短縮できる効果も期待できます。
設計期間が短縮できるのだから、当然といえば当然です塩。
日本の会社だとオプションを山のように付けて、分かりにくいシステムって多いですよね。
外食屋なんか典型例。
オプションを極力廃止し、選択肢を与えず、迷わせない。
これが製作者にとってもメリットが出ます。
海外のメーカーは、日本の製作者のように思考力のあるメーカーばかりではありません。
大量購入をして同じものを大量に作る。
これが海外調達のメリットとなるでしょう。
検査時間を短縮できる
化学プラントの設備で大量購入をすると、検査時間を短縮できるメリットがあります。
海外調達時には立会検査が長引く傾向があります。
日本では1日で済む検査が2日~3日となるケースです。
長引くほど、納期遅延のリスクが出るので、早く決着をつけたいところ。
大量購入をして、仕様を統一化すると、同じ検査ができるので時間も短縮化できます。
個別最適設計は全体最適設計ではない
大型プロジェクトが減った現在、大量購入をする機会が少なくなり海外調達をするメリットの1つが減っています。
個別最適設計が進んだ古い工場では、エンジニアの設計思想を根本的に考え直さないと全体最適設計が進みません。
大型プロジェクトの減少
海外調達をする場合、大量購入が基本です。
1基2基程度の個別アイテムではメリットは出にくいです。
調達部の調達戦略が育っていない場合は、コストが高くなってきた海外よりは日本の方が良いという判断をすることもあります。
海外調達が流行っても動き出さず、下火になってから少し動こうとして、結局中止する。
変わらない日本思想を引きずると、1周回ってくることもあるのですね^^
プラント設計思想の統一化が必要
さて、プロジェクトの規模や調達戦略が整っていても、プラント設計思想が統一化されていないと、大量購入は成立しません。
複数の機器の仕様を統一化させず、全てオーダーメイドだと設計も製作も非常に大変です。
既設と同じということに拘り過ぎるのが化学プラントの設備エンジニア。
10m2の熱交換器でもノズルの大きさや位置をバラバラにして発注するということを
何の違和感もなく行いがちです。
これは、既設がそういうノズルオリエンテーションだからですよね。
機器の個別最適設計としては成立しますが、全体最適設計にはなりません。
プラント全体を考えた最適設計こそが、ユーザー系のプラントエンジニアの存在価値ですが、
エンジニアにその視点が備わるのは10年程度のオーガーの時間が掛かります。
品質
化学プラントの設備を海外調達するとき「安物買いの銭失い」というフレーズが飛び交います。
確かに、コスを面を最重視して海外調達をします。
海外調達品に対する品質を見てみると、日本で制作する設備と海外で制作する設備の品質に対して思うことはあります。
細かい点に目が行かない
海外とくに発展途上国で調達すると「細かい点に目が行っていない」と評価することが多いです。
化学プラントのタンクを例に上げると
- 本体の溶接線はきれい
- 脚の溶接は雑
というのが一般的に言われています。
これは作業員の技能が育っていないことと関連しています。
手動溶接のレベルは高くなく、手動溶接が必要な脚の溶接は汚い。
自動溶接や半自動溶接でできる部分は、きれいに溶接できる。
タンクにおいて最も重要な部分は本体なので、そこだけでもきれいに溶接できていれば問題ない。
こういう発想で作ります。
日本の会社が発展途上国でのこうした発想を見るとき、お互いに以下のように思っているでしょう。
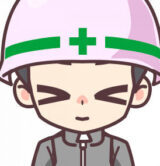
溶接者に技能を持たせる発想がおかしい。自動化を進めるべき。
手動溶接しかできない部分は重要でない!
そこまで要求するなら、できる会社に頼むべき。
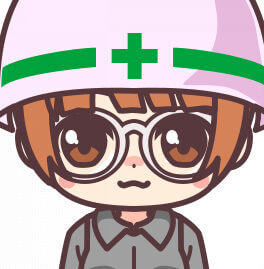
溶接は技能が最重要。細かい所まで溶接するのが普通。
それができないレベルの低さを反省すべき。
悔しかったら技能レベルをあげなさい。
言い方はそれぞれでしょうが、根底にある考え方は大きくずれてはいないと思います。
世界各地に販売
海外会社の安い製品でも世界各地に販売している場合は多いです。
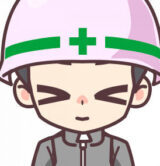
この品質で世界各地で販売しているのだから、細かい注文は付けないでくれ。そんなことをしても、使用に何の影響もない
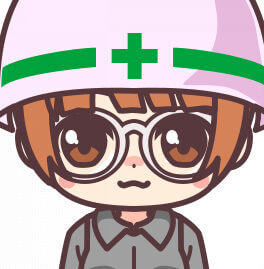
世界各地に販売していると言っても、ユーザーは苦労している。
そんな会社に頼むくらいなら、長く付き合える日本企業の方が良い。
こういう議論はあちこちで行われています。
私は「使いこなしが大事」と思っている派です。
日本企業の品質は「無駄に過剰」であり、品質を落とせる要素はあります。
それを高級というブランドで売ろうとしても、需要は少ない。
ユーザーも要求品質とコストの関係をもっと精査しないといけません。
コストを重視するなら品質を落とす、その代わりにメンテナンスやライフサイクルを考える。
こういう発想転換ができていなくて、日本企業を無条件に推すエンジニアは多いです。
エンジニア個人に頼るのではなくて、会社や部署の方針として考え方の筋を一本と押すべきところですね。
日本でも品質を犠牲
日本で製作した製品は確かに品質が高い設備ができます。
ところが、この日本製は確実にレベルダウンしています。
それも恐ろしい勢いで。
タンクの例を挙げると、細かい点がポロポロこぼれ始めています。
- ステンレスのタンクに鉄の溶接跡が残っている
- ステンレスの溶接の酸洗いが雑
- 図面と実物が違うが、図面を修正しない
日本なら高い品質のものができて当然。というのはすでに時代遅れです。
設計者も製作者も集まらなくなった日本では、過去と同等の良質の設備を作ることはできません。
今の50歳以上のエンジニアで現場を見ていない人には、信じられないことでしょうけどね。
10年前は下に見ていた中国製の設備でも、今では日本静と同等というケースが確実に増えています。
ユーザー側は「過去の付き合い」だけで品質の劣化を見過ごしているケースが多いと推測します。
コストアップが必須
コスト重視で海外調達する場合に、品質を犠牲にしない道はあるでしょうか?
個人的には不可能だと思っています。
海外調達で品質を保つために、検査回数を上げれば良いと安易に主張した時代はありました。
これをやり過ぎると、今ではクレーマーと認識されます。
安い額で買っているのだから文句を言うな
この主張は最近の日本でも取り上げられてきていますね。
検査回数を上げるために、常駐検査者を入れてコストを上げたところで逆効果。
製作メーカーに金が流れない以上。検査に口を出しても品質が劇的に上がることはありません。
常駐検査者に対して払うコストが、品質向上に繋がりません。
それなら常駐検査者に対するコスト分だけ、無駄銭となります。
60点の品質で100万円の設備を、65点の品質にするために200万円を払う
こういう結果になりがちです。
この場合、日本では90点の品質にするために200万円という世界でしょう。
そこだけを見れば、日本製の方が良いに決まっています。
問題は日本メーカーの体力がないことでしょうね。
納期
化学プラントの設備を海外調達する場合、基本的に納期が早い方向です。
これは発展途上国での生産を想定しているからです。
先進国から購入する場合は商社が部品を調達するシーンが普通なので、デリバリータイムをちゃんと考慮しています。
化学プラントのオーナーエンジニアが直接購買する設備は、自身で納期管理をしないといけません。
そこで海外調達は納期が早い側にシフトするので、オーナーエンジニアとしては大助かり。
日本で設備を買う時に比べて納期が早くなる要素・遅くなる要素を整理しました。
人海戦術が取れるから早い
発展途上国なら人海戦術が取れます。
人件費が安くて多くの人数を一度に割くことが可能。
製作コストが安いだけでなく、製作時間も早いです。
日本なら3か月程度かかるタンクでも、海外なら1か月でできる
こんなことは珍しくありません。
図面が完成し材料までそろっていざ製作、という段階で人海戦術は圧倒的に有利です。
材料在庫が大量にあるから早い
発展途上国なら、材料の在庫を大量に持っている場合があります。
これは土地が広いということが背景にあります。
日本だと製作工場はとても狭くて、製作物を外に出さないと次の材料を仕入れることができません。
化学プラントでも空地が少なくて、建設工事の資材置き場に苦労します。
発展途上国だと敷地が有り余っていて、材料を大量に保管できます。
図面が完成して材料を調達するために、時間が掛かる日本とは大違い。
設計に時間がかかるから遅い
海外調達の場合、設計にとても時間が掛かります。
これは取引が浅い人間関係であること以外にも、言語・文化などのギャップがあるからです。
ユーザーである日本側が、図面確認に時間が掛かったり・細かい要求を出すことで時間が掛かるというケースです。
日本企業は判断が遅い、なんてよく言われます。
細かい要求はバッサリと切り捨てないといけませんね。
日本だと1~2か月で仕上がる製作図面が、3~4か月くらいは見ておいた方がいいでしょう。
これは10年前までの常識でした。
今では、日本でも3~4か月はザラで、6か月程度かかる会社も普通にあります。
取引の浅い・深い、企業規模の小さい・大きいは全く関係ありません。
何十年も取引があって大手であっても、設計期限が6か月以上というケースが普通にあります。
「日本の方が納期が短くて安心」という神話を崩すには十分すぎます。
輸送時間がかかるから遅い
海外で物を作るのだから、輸送に時間が掛かって当然です。
日本なら1~2日で納入できる設備でも、1~2週間は余裕を見ないといけません。
海上輸送なので。いつ納入されるかも不安定になります。
これでは工場内での荷下ろし対応が取れなくなる可能性がでます。
工場内で揚重機を確保していればいいのですが、普通はリースですからね^^
検査は比較的遅い
海外調達では、製作後の立会検査は遅い方向です。
これもユーザーの要求とメーカーの常識とのズレの問題です。
- タンクの水張後の放置時間が長い
- 附属品の取付・取外しをする
- 熱交換器のチャンネルカバーの取付・取外しをする
こういう作業を、何をどれだけ行えばいいか分からないメーカーが戸惑うからですね。
とはいえ、最近では日本のメーカーでも遅くなってきています。
工場での作業人数を極力少なくしていて、検査に対応してもらえる作業員が1人いるかいないか、という世界ですからね。
海外ならすぐに3人4人準備してくれますけど^^
予備部品
海外調達では予備部品が相当大事なポジションを占めています。
予備部品は戦争における補給と同じ扱いです。
補給が無いと戦線はすぐに崩壊しますよね。
これと同じことが海外調達でも起こります。
化学プラントの設備でも動機器はいつ壊れるか分かりません。
傾向監視をして寿命予測をしますが、壊れる手前に交換するTBMやCBMで対応するのが普通。
壊れてから直すBMでは対応しないでしょう。
動機器を海外調達する場合、その設備の予備部品を適正に確保しておかないと、すぐに生産が止まってしまいます。
生産工場を安定的に動かすためには、海外調達はリスキーです。
海外調達は海外から日本に調達するケースを考えますが、その逆も含めて解説します。
日本に輸入する場合
海外から日本に輸入する場合を考えます。
この場合は商社に任せることになるでしょう。
バッチ系化学プラントでは渦巻ポンプや真空ポンプが当てはまります。
これらの予備部品といえば、メカニカルシール・スリーブ・オイルシール・Oリングなどです。
その国でしか作れない特殊形状の部品がありがちです。
この場合、商社は常に予備部品を抱え、ユーザーも最低限の予備部品は確保しないといけません。
ランニングコストは確実に上がります。
そこまでしてイニシャルコストを下げるべきかどうかは、会社の判断です。
日本から輸出する場合
日本製を海外に輸出して、生産する場合も注意が必要で主。
日本に輸入する場合の真逆の現象が起きるからです。
メカニカルシールやオイルシールは日本と同じ物が大量に手に入るとは限りません。
この他にも、モーターや減速機なども同じです。
海外に生産工場を移管する場合は、プロセス原料の調達性のみを考慮しがちですが、設備資材の調達性もしっかり調べる必要があります。
そうしなければ、日本に輸入する場合の商社と同じく「海外支社」で予備部品を確保しておかないといけません。
その管理をするくらいなら、現地の動機器を調達する方が楽だと思います。
海外で生産管理・設備管理の経験をした私は、強く実感しています。
静機器では予備部品は不要
静機器では予備部品は基本的に不要です。
最近では特殊材質の熱交換器が海外から輸入するケースが出ています。
とはいえ、補修の方法が限定化されているので、「壊れたら直す」BMで対応できるかもしれません。
熱交換器なら、チューブを閉塞することである程度は場繋ぎができますからね。
ガスケットやフランジなどの配管部品はすでに海外調達が一般化されているので、商社がノウハウを持っているというきれいな表現が通用するでしょう。
熱交換器も2021年現在では供給体制に不安があっても、近い将来には当たり前のことになっているかもしれませんね。
商社やメーカーには自分から聞くべし
日本の工場で導入している設備類って全部日本製だと思いますか?
アパレルや食料品が中国製だけど、化学プラントの設備は海外製なんてほとんどないはず。
いつの間にか海外製は導入されていると思います。
こんなことを未だに思っているユーザーは意外と多いです。
機械エンジニアならこれを知っているかもしれませんね。
典型例がガスケットやフランジです。
商社やメーカーは情報を出さない
商社やメーカーは原料の変更に対して大きなこだわりを持っていません。
聞けば答えてくれるけど、聞かれないと何も情報を出さない
こういう商社やメーカーばかりです。
そして、気が付いた時には実績ができていて、他のベンダーが存在しないから従わざるを得ない。
ユーザーが選ぶ権利はほとんどありません。
製造業で4M変更を口酸っぱく言われますが、設備メーカーはそんな意識はほとんどありません。
客であるユーザーへの説明も基本的にしません。
- 説明したら資料を作るのが面倒だから
- 嫌なら買うな
こんな思想で対応するのが化学設備メーカーです。
ユーザーが意識を高く持つべし
商社やメーカーが「これから海外製の部品を使います」と事前アピールをした場合、ユーザーは色々要求しますよね。
実績や会社の状況や生産体制など根掘り葉掘りと。
ユーザーとしては当然の要求ですが、商社やメーカーはこれを嫌がります。
面倒だと思っているのでしょう。
説明能力がない営業担当者が多い・そもそも営業担当者の数が少ないなど、背景には根深い問題があります。
ユーザーとしてはアンテナを高くして、商社やメーカーに都度ヒアリングする心構えが大事でしょう。
調達部や同僚なんかに任せても意味ありませんよ。
エンジニア自身が海外志向を高めていくのが現実的です。
そのためにも海外出向は一定数をキープしておきたいですね。
参考
関連記事
最後に
化学プラントでの海外調達は、一見安価で魅力的に見えるかもしれませんが、実際には設計・運転現場に大きな負担をかけることが多々あります。技術力やサポート体制、情報整備の観点から、慎重な判断が求められます。コストだけに目を奪われず、全体最適の視点で検討することが大切です。
化学プラントの設計・保全・運転などの悩みや疑問・質問などご自由にコメント欄に投稿してください。(コメント欄はこの記事の最下部です。)
*いただいたコメント全て拝見し、真剣に回答させていただきます。
コメント