TPM(Total Productive Maintenance)という単語が流行って20年~30年以上。
死語と化していてもおかしくないのに、いまだにTPM活動を続けている会社もあるでしょう。
無駄なコストを払っているのが実際なのに。
その中でもトップクラスに無駄なのがTPM指導会。
TPM指導会が無駄だという理由を3点紹介します。
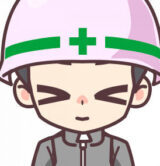
TPM辞めませんか・・・?
TPMの定義
TPMは1971年に提唱されたようです。
- 生産システム効率化の極限追求(総合的効率化)をする企業体質づくりを目標にして
- 生産システムのライフサイクル全体を対象とした”災害ゼロ・不良ゼロ・故障ゼロ”などあらゆるロスを未然防止するしくみを現場現物で構築し
- 製造部門をはじめ、開発・営業・管理などのあらゆる部門にわたって
- トップから第一線作業員にいたるまで全員が参加し
- 重複小集団活動により、ロス・ゼロを達成することをいう
難しいですね。
超簡単に言うとみんなでがんばってロスをゼロにしましょうということです。
それぞれの項目を解説します。
生産システム効率化の極限追求をする企業体質づくり
この表現は、日本にマインドに非常に合致します。
日本人は1つの事を極めようとする力が凄いですから。
今ある生産設備は30年・40年も前に買ったものかも知れません。
それを捨てて新しい物を買えば、現代の技術にあった効率的な運転ができるはずです。
極限追求した結果、新たな設備を導入するという結論にいたればいいのですが、大抵は却下されます。
新しい設備を買う金を、会社は出すことができないので、今の設備を徹底して使いこなしましょうと言います。
今の設備は30年・40年前の者ですが機能の中で90%くらいしか使っていないでしょ?
残り10%を極めれば、もっと効率化しますよ。
こういうニュアンスで、会社はこの文言を提示していると、私は解釈しています。
30年前の技術で90%使いこなしている時点ですでに十分すぎます。
逆に新しい技術を導入する阻害要因になってしまいます。
生産システムのあらゆるロスを未然防止するしくみを現場現物で構築し
これは非常に重要です。
日本の会社では、当たり前のようにやっているので気が付かないかもしれません。
でも、ふと目を別のところに向けると、これができていないケースって結構あります。
例えば、新幹線や飛行機に乗る時にこんな光景を見ませんか?
あなたより先に入った人が座席の近くの通路に立ったまま、上の棚に荷物を置くシーン。
その人が荷物を入れ終わるまで、他の人は中に入れません。
全員をいったん先に中に入れて、荷物を後でいれればもっと早く出発できそうなのに。不思議としませんよね。
小学生の方がむしろちゃんとしているくらいです。
気が付いている人はちゃんと行動していますが、気が付かない人は行動しません。
こういうロスを各職場で見つけて、誰に言われるでもなく自分たちで解決しましょう、ということをTPMは言っています。
これが機能すると、上の人は楽でいいですよ。
あらゆる部門にわたって
これも日本人のマインドに会っています。
家族みんなで。村みんなで。
赤信号、みんなで渡れば怖くない、と。(笑)
あらゆる部門という綺麗な表現に騙されてはいけません。
全員が参加し
拒否権無し。
それが合理的であるかどうか判断せず、盲目的にやらざるを得ません。
やる気を持って取り組む人の方が少なくても当然。
それでも一度始めたら辞められない会社が多いのではないでしょうか?
TPM担当者みたいに専門の役割を付けてしまえば、TPMを辞めた瞬間にその人は無職になりますからね。
重複小集団活動により、ロス・ゼロを達成する
これは今の日本人に全く合いません。
ワイワイガヤガヤ、居酒屋のように盛り上がって、意見を言い合おう。
そこから素晴らしいアイデアがでるはずだ。ロスはゼロにできる!
そういう思考。
でも現在の大手の製造業で、意見を言い合う雰囲気ってないと思います。
規模が小さい職場なら意見を言いやすいですが、大きくなればなるほど個人の意見は通りにくくなります。
意見を言えばパワハラだ・他の人が委縮するだ、出る杭を打つ思考ばかり。
それでも全員参加に絶対的な価値があると思い込んでいるのがTPMの思想。
意見を言いたくない人にも強引に意見を言わせるという意味で、危険な要素があることには気が付かずに。えげつないことです。
TPMの8本柱
TPMはさまざまな製造業に対して提唱されている概念です。
企業によって業種・生産方式・設備の状態・問題点・技術水準・管理水準など幅広いレベル差があります。
対象範囲が広いと、一般的なことしか言えないのは仕方がありません。
TPMとして多くの企業で展開されているのは、以下の8本の柱です。
- 設備効率化のための個別改善
- 自主保全体制つくり
- 保全部門と計画保全体制つくり
- 運転保全の技能教育訓練
- 設備初期管理体制つくり
- 品質保全体制つくり
- 管理間接部門の体制つくり
- 安全環境の管理体制つくり
今回は、この8本柱のうち化学プラントで展開されているものを紹介します。
設備効率化のための個別改善
TPMとして令和の現在も生き残っているといえるのは、これくらいではないでしょうか。
むしろ、TPMというと個別改善くらいしかありません。
残りの7つは全て「体制」など組織の話。
それを維持管理していくマネジメントシステムの構築にターゲットがあります。
監査でも大事なマネジメントシステム。
TPMでもそれは大事だろうということで8本の柱と組織に紐付いた表現になります。
この瞬間に「改善」とはほど遠い姿となります。
本来の保全活動以外の部分が目立つようになるからですね。
自主保全体制つくり
自主保全は運転部門が行う保全活動を指すことが多いです。
壊れたら直してもらうというのがTPM導入前の運転部門の考え方。
TPMで考え方が変わり自主保全を推進すると、できることは自分たちでやってしまおうという判断になります。
令和現在では、それなりの化学会社で自主保全体制は構築されています。
動きが遅い全問保全部隊に依頼するのは時間のコントロールがしにくいですからね。
保全部門と計画保全体制つくり
保全専門部門が存在しない会社は少ないでしょう。
これが機能していないと、製造業として非常に危ないです。
保全部門は計画保全を行うことが目的です。
故障ゼロが目的ではありません。
故障と言っても各社で定義が変わるでしょうから、表現が難しいですね。
設備が壊れても、運転を継続するための体制を作ること
これが保全部門の責務だと思っています。
このために計画的な保全を行います。
これも自主保全と同じで、一担当がどうにかできる世界ではありません。
人はそんなに簡単には変わりませんので。
私も一時期は頑張りましたが、担当レベルなので変えることはできませんでした。
運転保全の技能教育訓練
教育訓練は継続して実施している会社が多いでしょう。
教育プログラムが確定しているので、関連会社に委託している企業も多いと思います。
教育はすべての企業で問題になっています。
だからこそ今ではDXの活用先として考えられています。
講師が生徒に対面して教科書を読み上げるくらいなら、
動画や文書をイントラや社内システムに上げてしまえばいい。
そういう企業が増えてきています。
私の所属する会社もそういう取り組みを始めています。
少なくとも対面での講習は劇的に減って、オンライン会議が激増しています。
移動時間は無駄ですからね。
異なる事業所の人が出張して集合するとか、無駄が多すぎます。
設備初期管理体制つくり
こ子から先は、「体制つくり」として共通の事項が多いです。
初期管理体制を担うのは、保全部門でしょう。
保全部門の計画保全の一環として考える企業もあります。
化学プラントなら新製品や新設備導入時の、立ち上げを対象とします。
この場合は保全部が主体というよりは、設計部門が主体となります。
私の会社も初期管理体制の構築は、設計部門が主体となっています。
品質保全体制つくり
ここから先は、「全員参加」だからグルーピングしているにすぎません。
実務上はTPMという単語すら意識せずに、仕事をしている企業が多いと思います。
品質管理部門が仕事をするわけではなくて、
運転部門や保全部門に品質ゼロを目指しなさい
と指示するだけの簡単な仕事です。
管理間接部門の体制つくり
これも「全員参加」の弊害。
研究開発・営業・生産計画・人事などの間接部門です。
安全環境の管理体制つくり
これも「全員参加」の弊害。
安全や環境を専門の部隊として設置している場合を対象にしています。
総務部の組織内に配置している企業もあるでしょう。
TPM指導会が無駄だと言われる3つの理由
TPM指導会が無駄だと言われる理由を3つ紹介します。
TPM指導会は日々のTPM活動を披露する場です。
でも、この活動は費用対効果が非常に悪いです。
全員参加の一体感に意味がない
TPM指導会の全員参加には一体感が生まれません。
TPM指導会はなぜか全員参加が基本です。
TPM活動が全員参加が基本という思想が根強いからでしょう。
他の業務をなげうってでも、TPM指導会に参加しないといけない
こうして膨大な工数を払った指導会が発生します。
そこで得られるメリットはほぼなし。
あるとすれば満足感。気持ちの問題です。
発表準備や練習など含めれば相当の時間を使っていて、話を聞く人も仕事を止めないといけないのに得られる効果がただの満足感。
工場の規模が大きくなればなるほど、TPM指導会によるデメリットである時間の浪費の影響が大きくなります。
テーマが枯渇
TPM指導会はテーマが枯渇しています。
TPM活動を行って早や20年以上。
製造業どころか日本が20年以上進歩がないのに、TPM活動で毎年テーマが創出されることはありません。
テーマは枯渇していきます。
それでも工場では毎年TPM指導会を行います。
どこの課が指導を受けるかローテーションするでしょう。
発表に当たった課は悲惨です。
テーマを選び、日常業務に加えて発表資料を作成し、発表練習を繰り返さないといけません。
残業代が付くから喜んで取り組む作業員もいるでしょう。
それでも乾ききった雑巾を絞り上げるかのごとく、テーマは枯渇しています。
テーマを考えるだけでも時間が掛かります。
効果が捏造できる
TOM指導会では必ず「効果」について報告します。
○○の取り組みをすることで、△△の効果があった。
効果としては金額や時間が取り上げられます。
でもこの効果、簡単に捏造できます。
そもそもその効果を適正に評価できる人はいません。
瞬間風速的に効果があったり、別の合理化で埋もれてしまったり。
評価時間を長くすればするほど捏造ができます。
最近ではDXで同じ展開が見られますね。
参考
TPMの情報は今さらと思うかもしれませんが、製造業に入る人は基礎知識として持っておきたいです。
最近は社内で教える人が少なくなっているので、書籍での勉強も活用しましょうね。
関連記事
TPMについてさらに知りたい方は、以下の記事をご覧ください。
最後に
TPM指導会が無駄だと言われる理由について紹介しました。
全員参加の一体感に意味がない・テーマが枯渇・効果が捏造できる
こういう辞めるという決断をできない会社は、一度できたイベントがどんどん増えていって生産性を悪化させるだけです。
特定の人のポジションつくりのために、他の大多数の人の仕事を止めてしまう・・・。
化学プラントの設計・保全・運転などの悩みや疑問・質問などご自由にコメント欄に投稿してください。(コメント欄はこの記事の最下部です。)
*いただいたコメント全て拝見し、真剣に回答させていただきます。
コメント