バッチ系化学プラントでは粉体を非常に多く扱います。
ここでもあそこでも粉体、粉体・・・。
気体や液体と同じ発想で配管を組んでいくと、確実に失敗します。
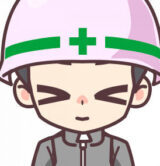
詰まってどうしようもありません
この問題は、いざ生産が始まってからようやく気が付きます。
その時には設備屋にはどうしようもなく、クレームだけを受けることになります。
無力感が漂います。
そういう辛い思いをしないように、設計段階・工事段階で失敗しないための粉体配管の基本的な考え方をまとめました。
粉体の特徴
バッチ系化学プラントで扱う粉体の特徴を、配管設計に限定して紹介します。
粉体は詰まる
粉体を取り扱ったことがある人ならわかると思います。
というより日本人なら家でラーメンを食べるときにテーブルコショーを使わないでしょうか?あれが非常に分かりやすいです。
コショーを掛けようとして、コショーを逆さに向け、容器を振ります。コショーが落ちてこないと思い、ガラス容器の中を確認すると詰まっているように見える。
これと同じことが配管内の粉体で起こりえます。
もちろん粉体の種類によります。それは化学プラントでどういう粉体を扱っているか?に依存するため一概には言えません。
ですが、バッチ系化学プラントでは「詰まる」と考えて設計するものです。疑ってかかります。
粉体は舞う
粉体は舞います。
コショーや小麦粉と同じで、バッチ系化学プラントで取り扱う粉体は舞います。微粉です。
詰まるだけでなく舞う。
このために専用の集塵ラインが必要になります。
粉体の移送方法
粉体を移送するときは自重落下が基本です。
粉体を移送する必要があるのは、どういう場合でしょうか?
- 予め液体の入った反応容器に粉体を仕込む
- 容器内で出来上がった粉体を別の場所に移送する
簡単に言うと、これくらいでしょう。
できるだけ粉体としての取扱をしたくないのが、実際です。
その粉体を移送する手段はあまり多くはありません。簡単に紙袋の中の粉体を容器に移した後の手段を考えます。
- 自重で別の装置に投入する。
- 機械式スクリューなどで別の装置に移送する。
- 圧縮空気などを使って強引に移送する。
これらの中でも、自重が大原則です。
機械スクリューは装置を購入する必要があり、圧縮空気は動力が必要だからです。
これ以外にも理由はいくつかありますが、基本的な考えとしては上の理解でOKでしょう。
低コストな自重落下に勝るものはありませんね。
自重落下配管は真っ直ぐ
粉体が詰まりやすいのであれば、できるだけ詰まらないように配管設計すべきです。
具体的には、真っすぐ落とすです。
自重で落としつつロータリーバルブで一定量のフィードを確保します。
ここまでは簡単な話です。ですが、実際にはそうではないケースが多いです。
現場を見てみると、自重落下配管の大半は歪んでいます。
理由は結構かんたん。
- 据え付け工事の時にちゃんと指示をしていないから
- 配管図でちゃんと指示していないから
- 配管を繋ぐ設備間の中心がずれた時の対応を考えていないから
こういう現場で設備更新をする時には、必ず適正な処置をしてください。
- 設備間の位置がずれないように、設備基礎の位置をレーザーで位置決めする。
- 基礎工事完了後、設備設置までの間に、現場検証をする。
- ずれたときに無理して配管を変形させてつなぎ合わせるのではなく、伸縮継手でつなぐ。
こういう対策を取らないと、工事がどんどん進み最後になって、歪んだ設備が導入されていることに気が付きます。
この段階まで進んでしまうと、困るのはお客さんである「運転員」です。
機械屋も図面屋もこの原則を忘れてはいけません。
集塵ライン
バッチ系化学プラントで扱う粉体は舞うために集塵しないといけません。
これは自重落下で粉体を移送するときに絶対に必要です。
そうしない現場では粉体まみれになります。
製品のロスというだけでなく、作業員の環境衛生面でも非常に問題。
吸引式の集塵機で粉体を集めましょう。
この集塵機の種類もいくつかあって、課題も山積み。
配管設計上は、流速設計とフランジの切込みが大事。
特にフランジ切込みはちゃんと考えていないと、集塵ラインの洗浄や閉塞解除ができなくなります。
粉体の空気輸送を避ける理由
バッチ系化学プラントの粉体の移送には、空気輸送は使いません。
空気輸送は世間一般にも多いイメージなので、空気輸送のメリットデメリットから見て、空気輸送を避ける理由を解説します。
メリット
空気輸送は機械輸送に比べて、以下のメリットがあります。
- ラインが簡潔にまとまる
- 粉じんの飛散・異物混入が無い
ラインが簡潔にまとまるとは、配管で輸送できるからです。
大きな機械を設置する必要がありませんからね。
配管なら施工の自由度も高く、輸送ラインをコンパクトにまとめることが可能です。
配管輸送が可能という点から、粉じんの飛散や異物混入も制御しやすいです。
デメリット
空気輸送のデメリットはいくつもあります。
- コストが高い
- 静電気着火を起こす
- 閉塞する
コストが高いのは空気輸送の動力費が高いから。
モーターで粉の体積分をフィードするより、その体積のフィードする空気を作る方が動力が掛かります。
バッチ系化学プラントで扱う粉体は、有機物がほとんどです。
だからこそ、バッチ系化学プラントで扱う粉体は静電気が溜まりやすいと言えます。
空気輸送は閉塞も怖い要素です。
機械的輸送や水力輸送でも閉塞可能性はありますが、空気輸送はそれよりも1ランク危険性が高いと考えます。
理由は圧縮空気を使うから。
仮に輸送中に閉塞が起こった時、圧縮空気が配管内に存在します。
閉塞を解除するために配管を分解しようとしたとき、圧縮空気が急に大気中に放散されます。
圧縮空気の圧力が無くなると、空気は急膨張します。
粉体配管で考慮すべきこと
粉体配管の設計で考慮すべきことをまとめます。
以下のモデルを考えましょう。
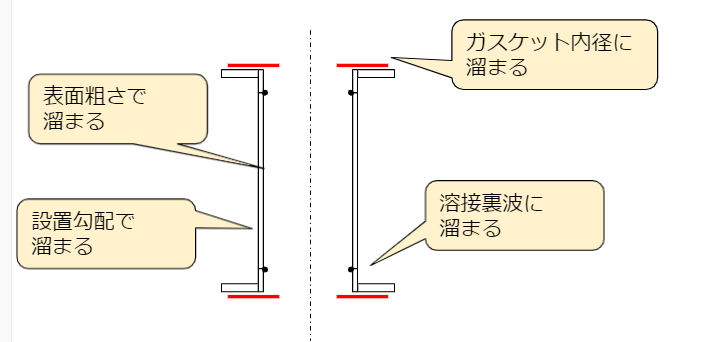
汎用的に製作する配管で粉体を自重落下させる場合を考えています。
粉体の閉塞する要素を並べてみましょう。
- 配管の設置勾配があると、溜まる
- 配管の表面粗さが粗いと、溜まる
- ガスケット内径が配管内径より小さいと、溜まる
- 配管の溶接裏波が出過ぎていると、溜まる
幾何的な視点でたまりを無くそうとしたら思いつくようなことばかりですが、配管設計をしようとするときには忘れそうになります。
設置勾配
配管の設置向きが垂直でなくて、勾配が付いている場合は溜まる要素があります。
水平向きに配管が付いている場合は、ほとんど流れません。
配管に勾配が付いているとしても、粉体の安息角との大小関係で流れるかどうか左右されます。
マルチ的な発想にするなら、完全に垂直な向きに配管を付けると良いでしょう。
ちょっとくらいなら大丈夫だろう。
こういう甘えの元に、配管に傾きを付けるとかなりの確率で後悔します。
設備を設置するときも、設備位置やノズル位置が配管を垂直にさせるように決めます。
通常は設備の設置位置が決まってから配管を繋げていくので、設計順番が逆ですね。
表面粗さ
配管の表面粗さも粉体の溜まる要因となります。
とはいえ、これが主要な要因になることはレアケース。
その他の要因の方が遥かに影響が大きいです。
表面粗さを下げるためには、バフ研磨や加工済み材料を使います。
研磨にしても加工済み材料にしても、納期が延びたりコストが高くなったりします。
表面粗さの効果を見極めながら使っていきたいですね。
ガスケット内径
ガスケット内径が配管内径より小さい場合は、当然ながら溜まります。
スラリー系ですらガスケット内径には気を使うことが多いので、意識しているエンジニアは多いでしょう。
ところが、ドライケーキを自重落下するラインですら、ガスケット内径に気を使わないケースがあったりします。
こういうラインを見かけたら、ガスケットの入れ替えを行いましょう。
溶接裏波
溶接の裏波も粉体の溜まる要素となります。
バフ研磨をするにしても、完全に除去するには結構な手間が掛かります。
多少は凹凸が残っても仕方がありません。
ここに拘るくらいなら、配管の勾配やガスケットの方によっぽと気を使うべきでしょう。
長手方向の溶接はシームレス配管にすることで防げますが、フランジやエルボなどとの周方向の溶接は防げません。
特にエルボがいっぱいある配管は、それぞれの溶接部での裏波の目視監視すら難しいレベル。
参考
粉体配管はトラブルが多いことで有名です。
できるだけトラブルを起こさないように、シンプルな配管を心掛けましょう。
関連記事
さらに知りたい方は、以下の記事をご覧ください。
最後に
バッチ系化学プラントでの粉体配管の考え方を解説しました。
粉体は詰まるし舞ってしまいます。粉体の移送は自重落下が基本で、空気輸送は基本的に採用しない。
粉体配管の設計上は、勾配・表面粗さ・ガスケット内径・裏波などを考えます。
化学プラントの設計・保全・運転などの悩みや疑問・質問などご自由にコメント欄に投稿してください。(コメント欄はこの記事の最下部です。)
*いただいたコメント全て拝見し、真剣に回答させていただきます。
コメント