2005年4月25日はJR西日本の脱線事故(JR west)が起こった日です。
当時私は会社に入社して数年の素人状態でした。
2022年現在で17年。
月日が経つのは早いものです。
この時にも叫ばれていたメンテナンス体制。
メスを入れないといけないことは関係者誰もが痛感しているのに、全然進みません。
これはJRだけに限らず日本の製造業のかなりの部分で当てはまることでしょう。
JR西日本の脱線事故そのものはとくに扱いません。
JTCでは各部署が我慢に我慢を重ねてしまいどこかで露呈してしまう、という認識がポイントです。
今回は、バッチ系化学プラントのメンテナンスの今後というテーマで考えてみます。
メンテナンス体制の実態
私の職場の例を通して化学プラントのメンテナンス体制の実態をまとめます。
技能伝承ができなかったワケ
化学プラントが発展したのは高度経済成長期。
1950年後半から1970年前半くらいの間です。
そこでスキルを蓄積していった人は、2021年現在ではすでに定年退職しています。
1970年で20歳の人でも、2021年現在では71歳ですからね。
当時の人たちは、体系だった知識なんて無ければインターネットなどの情報共有源もなく学歴もなくまさに手探りの状態で保全体制を築き上げていきました。
全員参加のTPMってこの辺の時代の思想を、後世に引き継がせるためのものだと思います。
そこは素直に尊敬しています。
先輩に対する話は尊敬というところまでで話が終わることが多いでしょう。
でも実態として技能伝承をちゃんとしてこなかったという課題がでています。
大きなツケ。
技能伝承を部のテーマとして取り上げて、推進していたはずなのに。
失敗。
そんな判断をしている組織はけっこうあるでしょう。
技能伝承をしていないのにはしっかりと背景があります。
- 言語化能力が低い
- 見て盗んで覚えさせたい
- 自分たちの努力をタダで渡したくない
- 技術を渡すと会社から解雇される
- 自分たちが技術なんて持っていないかったことが公にされたくなかった
定年延長して給料が下がっても会社に残ってわりに技術伝承はされなかったです。
別会社への委託
いわゆる保全技術というと、こんなイメージでしょうか。
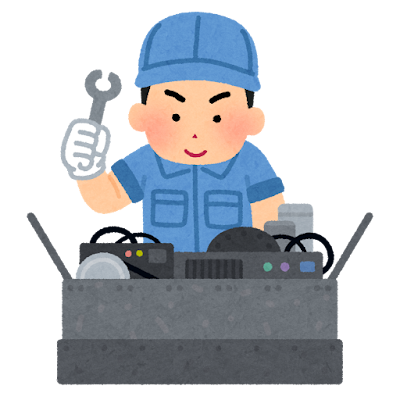
修理屋さんの印象ですよね。
実際に現場で作業をするメンテナンスマンは工具を使って機械を分解組立をしてくれます。
大手の化学会社ならメンテナンス会社に委託することが普通でしょう。
自社の工場内にメンテナンス会社の常駐事務所を設置して、そこで仕事をしてもらいます。
本体としてはメンテナンス技術を持っていません。
本体のオーナーエンジニアの保全部隊というとこんなイメージです。
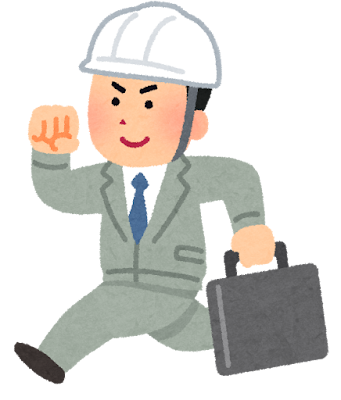
ちょっと良い方を厳しく言うと「手配屋」です。
かくいう設備設計エンジニアも手配屋みたいなもの。
- 危険
- 保証が取りにくい
- 作業負荷が不安定
- 計画・実施・修正のPDCAサイクルも大事だから
最も分かりやすい理由は作業負荷の不安定性でしょう。
今月は作業があったけど来月はほぼゼロ。
こんな不安定な職種を技術系として本体で抱えるには、リスクがあると考えていたのだと思います。
そうこうしているうちに技術系以外の職種もアウトソーシングされるようになり、親会社としては技術を持たない体制が確立しました。
メンテンナンス人員は足りない
ではメンテナンス会社に任せているから大丈夫と安心して良いのでしょうか?
ここにも問題があります。
メンテナンス会社にも人が集まってきません。
まぁ、それはそうですよね。
オーナー会社の手配屋ですら人が集まってこないのに。
もっと現場作業で3Kの職場にそんなに人が集まってくるかというと・・・
しかもその中で手に職を付けようとする人なんて・・・。
- 給料が安い
- トラブルがあったら夜間でも呼び出しされる
- 直して当然だと思われている
こんな職場環境で働く人が減っていって当然です。
もともと少子高齢化ですしね。
JR西日本と同じ構図は製造業どこにも見られます。
コストカットの限界
TPMが流行った当初は保全コストは年々下げれるものだという、思い込みがありました。
当時はあながち間違っていませんでした。
TPMをちゃんとして適切に資金と人材を投入することで、突発的に設備が故障することがなくなり予測可能な運転ができるようになる。
ここまでならいいのですが、
現場のカイゼン活動を推進することで、年々補修費を下げれるはず。
というロジックが強く残っています。これが厄介。
補修費を毎年〇%カット
みたいな無茶ぶりがずっと残り続けます。
労務費が上がっていて工事コストが上がり、技術も確立されている分野なのに、補修費をカットしたらどうなるか。
何かを我慢します。
- 今にも液が漏れて大ごとになりそうな配管でも補修ができず
- 実際にことが起こっても復元ができず
- ここだけは止めてはいけないという最低限の部分にのみしか投資ができない
そういう実態は現場の中だけで処理されて、公開されません。
我慢に我慢を重ねた結果、気が付いた時には大ごとになった。
こういう展開は今でも増えているのに、これからも止むことはないでしょう。
JR西日本の件も同じでしたよね。
工期カットの限界
コストカットと似た感覚で工期カットも問題になっています。
工事日数を短くするほど生産日数を確保できるから、オーナー会社としては要求するでしょう。
大手の会社なら、メンテナンス会社に無理をさせて当然だと思っています。
2交代で夜も作業をすれば、半分の日数で工事ができる。
こんな単調なロジックです。
そういう工事をしている場所はあります。
公共に関わる場所でゼネコンが入るような工事ですね。それは超一流の環境が整備されているから。人も資本も十分に揃っているから。
そういう背景には目をつぶって、他社ができているから自社もできるはずだというロジックで
設備保全エンジニアやメンテナンス会社に無理させようとする経営層がいます。
毎年定期的に30日工事を取る工場があって、何かしらの無理をして29日で完成させてしまった場合、
次の年からは29日をベースに議論しようとします。
それが会社です。
その割に、安全は大事だ!というパトロール部隊が入ってきて、平日に実作業に割く時間が減っていきます。
工事を早く終わらせたいのか終わらせたくないのか。
経営層と安全管理者のどちらも思想が偏り過ぎていて、バランス感覚を持っていません。
この辺をちゃんと考えて主張するのが設備保全エンジニアの仕事の1つですが、言語化能力に難があるのでなかなか進みません。やはり我慢してしまいます。
製造部の管理者も保全側に立ってくれる場合は社内で意見をアピールしてくれますが、敵側に回ってしまうと悲惨です。
今後のメンテナンスのあり方
技術はない・人はない・コストはカットされる・工期も絞られる。
という環境で今後のメンテナンスがどんな方向になるのか予想していきたいと思います。
設備の統一化
設備の統一化はメンテナンス負荷を下げるという意味でとても大事です。
Aプラントでは15m2の熱交換器を使っていて、Bプラントでは20m2の熱交換器を使っていた。
なんて例があったときにBプラントの20m2が壊れたからAプラントの15m2を使おうとして、各種検討を高速で行います。
で、どこかで無理をさせつつAプラントの15m2を使うことを決心するでしょう。
こんな時に、AプラントもBプラントも20m2だったら何も悩まなくて済みますよね。
同じ伝熱面積でも脚の位置が・配管の取り合いが違っていて困ったなんて例はいくらでもありまsう。
このレベルまで仕様を統一化させていくことが極めて大事です。
これが難しいのは、情報の共有化。
一匹狼は設備保全エンジニアだけに限らず設備設計エンジニアも同じ。
Aプラントの設備設計エンジニアはAプラントの個別最適設計をして、Bプラントも同じように個別最適設計をしてしまいます。
ここでお互いに情報を持ち合って全体最適を目指すなんて思想を持つ人は、ほとんどいません。
この思想を持ってちゃんと運営できている組織はとても強いと思います。
私の職場なんて全然ダメですからね笑
古い工場の取り壊し
古い工場はさっさと取り壊しましょう笑
プラントライフサイクルを考えるという類の話です。
- 建替はお金がかかるから
- もうちょっと我慢できるから
- 場所や時間が無いから
こんないろいろな理由を付けて無理をさせている場所、多いですよね。
いつまでその対応を続けるのでしょう。
「我慢して」といつまで言い続けるのでしょう。
そうしている間にも、状況は悪化していく一方。
無理をさせていて何も対応しない人たちは、2~3年の任期を終えて別の部署に行くことしか考えません。チキンレース。
オペレーションとメンテナンスのバランス
設備設計エンジニアはオペレーションとメンテナンスのバランスを持ちましょう。
日本人は結構極端に振れます。
私が入社したときは、とにかくオペレーションの作業性を優先させなさいという指導が多かったです。
ある時からメンテナンスも考えましょうという風潮が出てきたかと思えば、
今の若手に設計の考え方を確認すれば、とにかく工事だけ考えた・メンテナンスだけを考えたという発想ばかり。
今度はオペレーション側に我慢をさせる格好になります。
そんなにバランスを持とうとすることって難しいのかな?ってくらい極端に振れますよ。不思議です。
メンテナンス技術の確保
オーナーエンジもメンテナンス技術を持った方が良いという意見はあります。
ここは工場の規模や組織の構成でかなり意見が変わるでしょう。
大きな組織なら、まずは1~2人レベルで技術者を養成するという流れがあっても良いかも知れません。
障害は多いです。
特にメンテナンス会社からは抵抗されるでしょう。
自分たちの仕事が無くなりますからね。
メンテナンス会社に作業をしてもらうために、最低限必要な知識として作業を経験する程度ならOff-JTでもできるでしょう。
そういう教育部隊としてのスキル保有者を自社で抱えておくというくらいから始めるしかないでしょう。
というのも手配屋だけでも仕事が多いので、スキルを身に付けるだけの時間がないというのが実際でしょうから。
駄目なことを駄目という風潮
駄目なことは駄目、もう限界です。
こういうことを言える風潮はその組織の文化として醸成させるべきです。
典型的なJTCほど、この風潮からは遠ざかっているでしょう。
組織内の立場や指名の問題で、なかなか言いにくいもの。
とはいえ、誰かがストップをかけないとどこかで問題が起きます。
安全・品質・環境・・・色々な面で日本の製造業は昨今問題を起こしています。
弊社の私の個人的な業務でもそう感じます。
JTCであれば、上の立場の人ほど「下の立場の人は言いにくいという主張をしていく姿勢が、まずは大事だと思います。
最後に
日本はメンテナンスに対する理解が低い風潮にあります。
メンテンナンス後進国。
私の会社でも、あと10年もしないうちに大きな問題になると思います。
いつ起こってもおかしくない時限爆弾
化学プラントの設計・保全・運転などの悩みや疑問・質問などご自由にコメント欄に投稿してください。(コメント欄はこの記事の最下部です。)
*いただいたコメント全て拝見し、真剣に回答させていただきます。
コメント