据付ボルト(Installation bolt)は、化学プラントの設備を固定するうえで極めて大事です。
機械的な部品なので、機電系エンジニアがその本領を発揮する場。
ボルトだからと軽視するオーナーエンジニアが多いですが、長い間確実に使ううえでは据付ボルトはとても大事です。
基礎ボルトというくらいで基礎的で大事なことです。
ボルトと言っても方法は複数あります。固定方法を理解して、その中から最適な物を選びましょう。
脚式とブラケット式
化学プラントにタンクを据え付けする場合、脚式とブラケット式の2種類があります。
一般にはブラケット式を選択するでしょう。
脚式には脚式のメリットもありますが、ブラケット式のメリットの方が目立つのでブラケット式を採用していると思います。
その違いを比較してみましょう。
脚式とブラケット式の概念から説明しましょう。
下の図のようなイメージです。
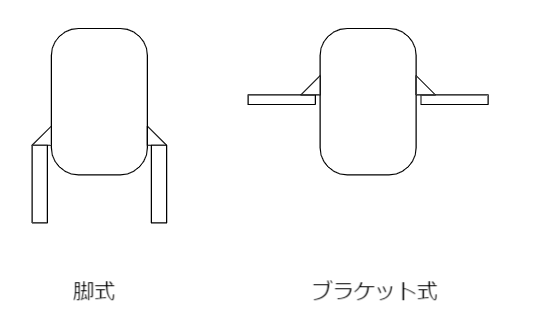
タンクは竪型を想定しています。
脚式はタンクの胴部が底部から言葉どおり脚を出したタイプです。
胴から脚を出す場合は、胴部と脚を直接点付け溶接する場合もあれば、ブラケットを取って脚をボルトで取合う場合もあります。
底部から脚を出す場合は、溶接をすることでしょう。
脚の底部にプレートを付けて、コンクリート基礎とアンカーボルトで取合います。
ブラケット式はタンクの胴部にブラケットを溶接したタイプです。
各階の梁を加工して受梁を取り、ブラケットを受梁とボルトナットで取合う方式です。
竪型タンク(あるいは撹拌槽)に限定しているのは以下の理由があります。
- ポンプはコンクリート基礎。チャンネルベースで固定するにしても見た目はほぼ同じ。
- 横型タンクや横型熱交換器はブラケット式が一般的。
- 塔はバッチ系化学プラントではサイズが小さので、ブラケット式が一般的。
というように選択がほぼ自動的に1つに絞られるから。
脚式
脚式のメリットを紹介します。
- 架構の梁や柱を細くできる
これくらいしか思いつきません。すみません。
脚式のメリットはほぼありません。
タンクを架構に預けないで、コンクリート基礎にタンクや液の荷重を預けることができるので、
建物の強度を抑えることが可能です。
結果的に梁や柱を細くすることも可能かもしれません。
その代わり、独立した基礎を地面に埋め込む必要があります。
屋外タンクなどタンク周りにプラットホームや架構を付けない場合は脚式に限定されますが、
そうではない場合はプラットホームや架構の基礎とは別にタンク用の基礎を作らないといけませんね。
胴板から取る
もっとも一般的な脚の取り方は胴板から取る方法です。
イメージは以下のとおり。
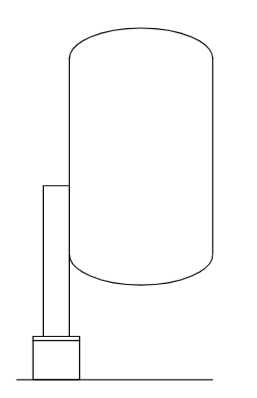
タンクの脚を胴板と溶接する方法です。
もう少し詳細を見てみましょう。
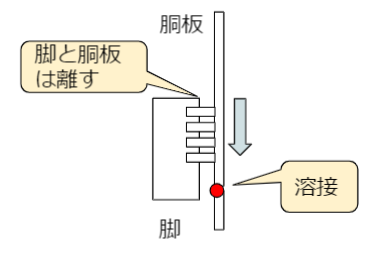
胴板と脚を複数枚の平板を挟んで溶接していきます。
脚と胴板を直接溶接しても良いように思うでしょうが、ちょっとした工夫が必要になります。
というのも、胴板と鏡板の溶接ビードが脚と干渉するからです。
部分的に脚を切り欠く形もよく見かけますが、格好悪いですね。
胴板に当て板を付けて強度を上げる場合もあります。
この場合当て板の板厚分だけ脚が胴板から離れるので、溶接線と干渉しない場合もあります。
一枚の板で脚と胴板を繋いでも良いですが、溶接数量や材料費を削減するために複数の小さな平板で繋ぐ方式が多いです。
ユーザーが脚に関する指示をださずにメーカーに発注した場合、メーカーは標準的にこの方法を選定するでしょう。
鏡板から取る
胴板から取る方法の別の方法として鏡板から取る方法があります。
下の図のようなイメージです。
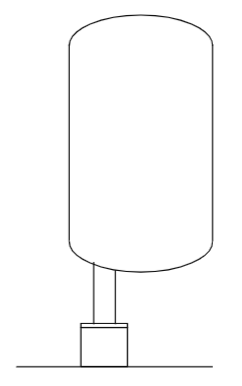
脚の位置がさきほどとは違いますよね。
詳細を見てみましょう。
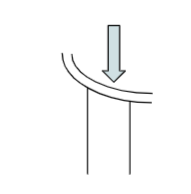
鏡板に足を溶接しています。
胴板から取る場合に比べてちょっとした工夫はありません。
あえていうと、胴板に当て板を付けてから脚を付けるくらいでしょう。
胴板から取る場合と鏡板から取る場合の比較
胴板から取る場合と鏡板から取る場合の2ケースの比較をしてみましょう。
タンクに掛かる力の向き
タンクに掛かる力の向きは大きく違います。
胴板から脚を取った場合は、胴板を軸方向に引っ張る力が加わります。
鏡板から脚を取った場合は、鏡板に外圧として曲げ応力が加わります。
材料は一般に引張応力と曲げ応力なら、よほどのことがない限り引張応力に対する抵抗力の方が強いです。
曲げ応力はモーメントで効いてくるので腕の長さが長いほど大きくなりますからね。
強度が高い方が設備としての信頼感があるのは当然で、胴板から取る方が安心ですね。
メーカーが標準的に胴板から脚を取る理由の1つでしょう。
鏡板の方が胴板より1サイズ板厚を上げる場合もあるので、鏡板でも強度は強いのでは?という意見もありますが、
鏡板の板厚が胴板の板厚と同じという場合もあるので、例外的にとらえる方がいいでしょう。
脚ピッチ
鏡板から脚を取る最大の理由は、脚ピッチを小さく取れること。
工場が狭い日本なら大歓迎されます。
タンク大きさと脚ピッチを指定した場合は、鏡板から脚を取るようにメーカーも設計してくれます。
転倒バランス
タンク自体の転倒バランスは胴板から取る方が安定します。
脚ピッチがタンク径より大きいため、タンク自身が転倒しにくくなります。
極端に考えるとタンク中央に1本の脚で支える場合、タンクの方が脚より寸法が大きいので転倒しやすそうですよね。
メーカーが胴板から脚を取る理由の1つですね。
ブラケット式
ブラケット式のメリットを紹介します。
- 脚が不要なので、タンク底面を配管や通路スペースとして有効活用できる
- タンク上面へのアクセスに独立したプラットホームが不要(架構や建物が兼用できる)
- タンクの重心近くで荷重を支えることができて安定する
- 装置本体としても脚そのものやテンプレートなどの附属品が不要で安価
脚式に比べるとメリットだらけ。
特に1のスペースは日本のどの製造業でも大ごとでしょう。
競争力を持たせようと投資コストを下げるために、建屋面積を最小化しようとすると
どうしても有効スペースの問題が発生します。
ここで脚という邪魔ものがあると配管の取り回しが複雑になって高価になります。
その代わり上階ではブラケット部が作業スペースを圧迫する要因にはなります。大した問題ではありませんが。
2のプラットホームはケースバイケース。
3の重心で支えるということ」も実はありがたいこと。
ブラケットでタンクの重心を支える方が、脚でタンクの端部を支えるよりは明らかに安定します。
ロードセル付きのタンクでも同じ問題が発生しますね。
4の脚やテンプレートが不要という点もコストを削減しようとすれば、努力代になりえます。
脚式のメリットであった建物の柱や梁のサイズはブラケット式では大きくせざるをえません。
とはいえその影響は大きなものではないでしょう。
柱サイズは配管設計上は多少問題になりますが、絶対にダメと拒否するほどの設計要素にはなりません。
梁サイズは脚式でもブラケット式でも結果的には大差がないと私は考えます。
というのもタンク荷重があろうがなかろうが、大梁のサイズは建物の大きさで決めるからです。
最初は脚式タンクを設置する意図で設計していた建物に対して、ブラケット式タンクを置けないことが分かると、そのプラントは応用が効きません。
融通が利かない使いにくいプラントは競争力も無くなっていきますね。
立面図
基本である立面図を紹介します。
とはいえ、これは略立面図。

ブラケットの設置イメージを何となく理解したり表現するときに使います。
ブラケット式の場合は、床面に穴を開けてブラケットと梁を取り合う格好になります。
このイメージは機械エンジニアに限らず、工場に勤務している技術系なら誰でも知っているレベルの話です。
平面図
次に平面図を解説します。
ここになると難易度がぐっと上がります。
現場をよく観察できる製造部の人の方が、機械エンジニアよりも詳しいかもしれないレベル。
この図を書ければ、据付設計で土建と十分に議論ができますよ。
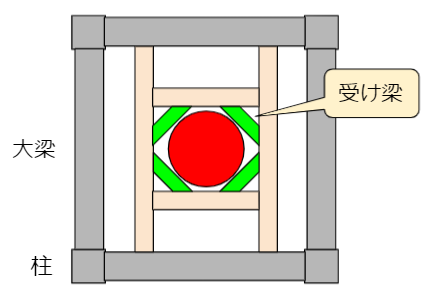
システムの構成を全体から詳細に向かって解説します。
4本の柱をそれぞれ梁で結びます。この梁は大梁と呼びます。
大梁とタンクが直接接続することは普通はありません。
小梁を大梁と直角になるように2本取ります。
その2本小梁を繋ぐように小梁を2本渡します。
これで小梁4本が四角形の形を構成します。
この四角形の中にタンクをはめ込みます。
小梁とタンクのブラケットを取り合うために、小梁に斜材を入れます。これを受け梁などと呼びます。
大梁の大きさが4mだから、4m近くのタンクが設置できるはずだ!
なんていうことを真顔で言うエンジニアもいますが、この平面図を見れば分かりますよね。
配管などを考えると結構難しいことがイメージできます。
少なくともバッチ系化学プラントでは大梁の長さの半分程度のタンク径までしか設置できないと考えた方が良いです。
受け梁詳細
平面図が理解できていれば基本的なことはOKです。
応用的な内容として受け梁の詳細を解説します。
小梁と受け梁の取合
小梁と受け梁の取り合いを解説します。
この図は断面図です。立面図と同じ向き。
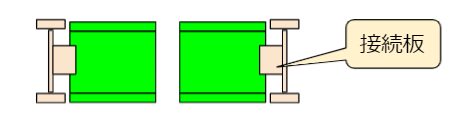
構成は小梁に接続板であるガセットプレートを溶接して、受け梁とボルトナットで取り合う形です。
どうでもいいですが、土建図って絵が多くて向きが分かりにくくて、どこのことを指しているか悩みませんか。
小梁と受け梁の図も実はこれと同じ。
受け梁が斜材である以上、同じ断面で記載するのが難しいです。
上の図で左右に分割しているのは、小梁の向きが違うことを意図的に表現したかったからです。
実際には受け梁の両端を2本の小梁で接続しています。
受け梁とブラケットの取合
受け梁とブラケットの取合も微妙な問題を抱えます。
基本的にはボルトナットで取合うだけですが、まれに受け梁に補強を付けます。
下の図のようなイメージです。
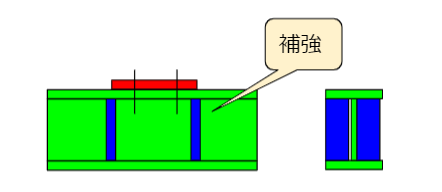
受け梁がC型チャンネルではあまり見かけませんが、H鋼の場合は補強のためにブラケット両端の幅に対して補強板を付けます。
受け梁の片側でしかブラケットを受けないため、曲げモーメントが加わりやすくなるから補強は欲しいところです。
片側に補強を入れると溶接の熱でひずみが出るかもしれないので、反対側も補強を入れたいですね。
バッチ系化学プラントでここまで補強を入れる例はほとんどありません。
強度を上げるための工夫として知っておいたら良いと思います。
ボルトシステムと据付ボルト(Installation bolt)
ブラケットタイプの設備を取り付ける時の典型的なボルトシステムを紹介します。
以下のようなイメージです。
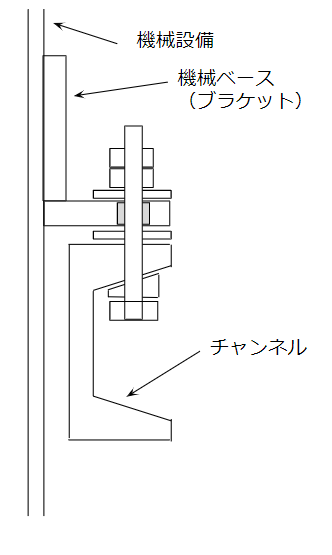
これはブラケットとC型チャンネルを取り付けるイメージですね。
C型チャンネルでなくて、H鋼だとほんの少し状況は違います。
サイズ
ボルトシステムはサイズが必ず話題になります。
ボルトと穴の関係を整理しましょう。
暗記するレベルかも知れません。
穴 | ボルト |
15 | M12 |
19 | M16 |
23 | M20 |
27 | M24 |
33 | M30 |
ボルト径は機器メーカーが選定してくれるでしょう。
それに合わせてボルトを準備して、ボルト穴も適切に開けます。
傾斜座金
まずは傾斜座金について説明します。
これはC型チャンネルに対して使用します。
化学プラントの設備を取り付ける時はC型チャンネルが多いですからね。
傾斜座金は以下の場所に付けます。
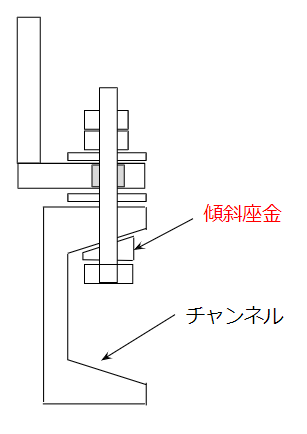
C型チャンネルは実は傾きがあります。
これをボルトで強引につけようとしても、ボルトが傾いて適切に取り付けることができません。
その傾きを吸収するために、傾斜座金が必要。
ダブルナット
化学プラントの設備ではダブルナットを使うのが普通です。
下の図のようなイメージですね。
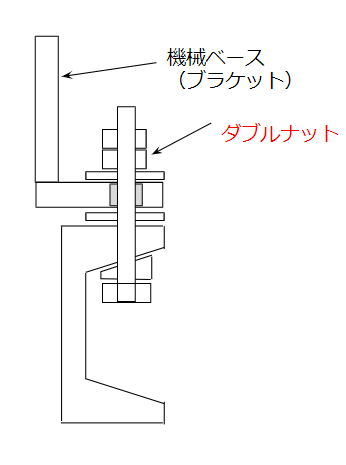
ダブルナットとはナットを2個使うことです。
簡単ですが、ゆるみ止めにとって非常に効果的。
ナットを1個だけ使う場合は、運転時の振動で緩むことがありますが、2個付けるだけで確率はぐっと下がります。
ワッシャー
ワッシャーはナットとベースの間に付けます。
化学プラントの設備ではワッシャーを標準的に使います。
下の図のようなイメージですね。
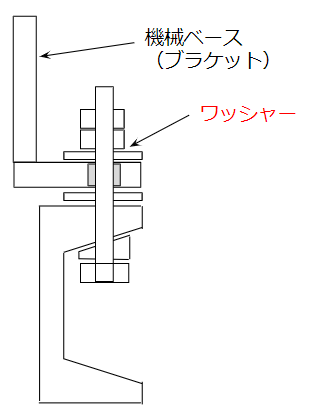
ワッシャーを付けるのは、ボルトの締付力をベースに均一に伝えるため。
ナットとベースの当たり面が十分に取れている場合は問題ありません。
これはボルトサイズとボルト穴が最低限の寸法で決まっている時のみ使えます。
例えば配管フランジ。
M12のボルトを使う時はボルト穴はΦ15、M16のボルトを使う時はボルト穴はΦ19です。
最低限のボルト穴サイズで設計されています。
化学プラントのような大型設備は、製作誤差などを吸収する目的で、ボルト穴を大きな穴にすることがあります。
一般的には長穴と言う一辺だけが長い穴を使いますが、単純に穴を大きくする場合も。
いずれにしろ、ナットとベースの当たり面が小さくなります。
この状態で、ボルトとナットを占めると、ベースを変形させる恐れがあります。
それを防ぐために、ワッシャーを使います。
ライナー
ライナーとは薄板のことです。
化学プラントの設備を据え付ける時の高さ調整のために使います。
下の図のようなイメージですね。
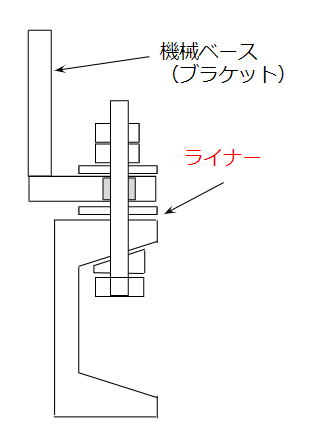
化学プラントの設備は数m以上のサイズで非常に大きく、mm程度の製作誤差は絶対に発生します。
土建施工上もmm単位でのズレは起きます。
この状態で強引に据付をしたら、水平度・垂直度が出ません。
動機器の場合、これがエネルギーロスや異常振動などの悪影響が出ます。
それを解決するために、据付時にライナーで高さ調整をします。
アンカーボルトは据付ボルト(Installation bolt)の基本
アンカーボルトの種類について解説します。
化学プラントでは大型の設備を建物に固定する工程が必ず発生します。
プロジェクトでも現地工事段階では設備をどうやって据え付けするかが最も重要な要素になります。
場合によっては、工期を大きく左右することも。
工期短縮の調整をする場合や設計業務を進める場合などに、役立つ内容です。
土建エンジニアの方が詳しい分野ですが、機械エンジニアが理解しておくべきことをまとめました。
今回の記事は、コンクリート基礎を対象にしています。
梁に固定する場合は以下の記事を参考にしてください。
埋込式
コンクリート基礎にボルトをセットする方法の基本は埋込式です。
埋込式は以下のイメージです。
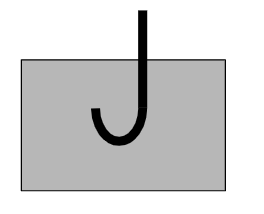
コンクリートを成形するときにボルトを差しこんでおくだけです。
普通はコンクリート内の配筋にボルトを固定して位置決めをします。
メリット
埋込式のメリットは強度が高い。この1点です。
コンクリートの強さは均一であるかどうかがポイント。
コンクリート一発仕上げでボルトと接触させる埋込式は、他の方法に比べても強度が高い特徴があります。
デメリット
埋込式のデメリットは、精度が要求される・コストが高いという2点です。
コンクリート基礎をいったん作ってしまうと、ボルトの位置は後で変更が効きません。
機械設備のボルトピッチとコンクリート基礎のボルトピッチをmmのオーダーで合わせる必要があります。
ボルトとボルト穴は3mmくらいのズレしかありませんからね。
あらかじめテンプレートを準備しておくことが普通です。
テンプレートを準備しない場合、必ずといって良いほど据付ができず、
機械設備のボルト穴を大きく開ける対応を迫られます。
テンプレートが必要な分だけコストは上がります。
適用先
埋込式を使うのは、大型設備に限定されます。
バッチ系化学プラントでは、大型の撹拌槽でコンクリート基礎上に脚を載せる場合に限定されます。
そもそも大型の撹拌槽を脚で固定するということ自体が無理のある発想なので、適用する例は珍しいです。
箱抜式
箱抜式は埋込式の簡易版という位置づけです。
箱抜式は以下の流れで行います。
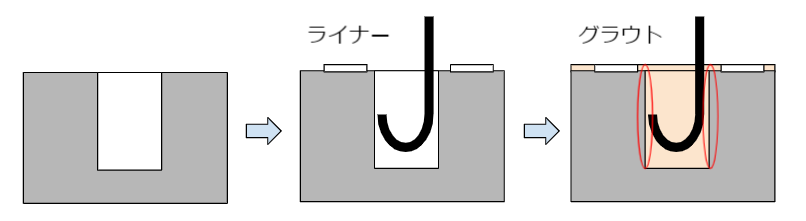
コンクリート基礎のボルトを設置する周りだけ穴(箱)を開けた状態で、コンクリート基礎を成形します。
ボルトを箱の中にセットした状態で、機器を据え付けます。
据え付けする段階で水平レベル調整のために、ライナーをセットします。
最後に、モルタルを充填して完成。
メリット
箱抜式のメリットは埋込式のデメリットの逆と言えます。
安価・位置調整が可能です。
テンプレートがいらないし、位置調整をシビアに考える必要もありません。
デメリット
箱抜式のデメリットは埋込式のメリットの逆と言えます。
強度は若干弱いです。
コンクリートを一体成型しておらず、コンクリートとモルタルで不連続部分ができます。
これは強度を弱くする大きな要因です。
コンクリートを成形した後で、モルタルを塗るという二度手間もデメリットでしょう。
適用先
バッチ系化学プラントでは箱抜式は各所で使います。
コンクリート基礎に機械を固定する場合のほぼ全てで、箱抜式が使えます。
ホールインアンカー
ホールインアンカーは箱抜式よりさらに簡易版という位置づけです。
ホールインアンカーは以下の流れで工事をします。
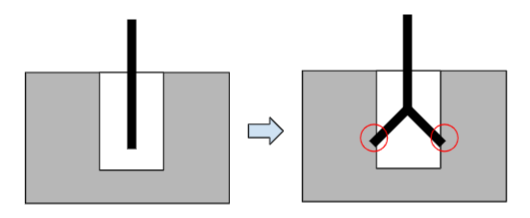
箱抜式アンカーと同じように、箱をあらかじめ開けておきます。
機械を基礎にセットするときに、ボルトも同時に差し込みます。
差し込んだ後で、ホールインアンカーボルトの頭を叩いて、はい完了!
箱抜式のようにライナー調整やモルタルの工程がないのが特徴です。
メリット
ホールインアンカーのメリットは、安価・施工しやすいという点にあります。
工事会社には喜ばれます。
箱抜き穴が小さく、コンクリート基礎をコンパクトにできる点も特徴です。
デメリット
ホールインアンカーのデメリットは、強度が弱いという点にあります。
コンクリートとボルトの接触面積が小さく、ボルトの末広部だけがコンクリートと接触しています。
ボルトで設備を固定するときは、ボルトの引き抜き力が強度に直結します。
ボルトの引き抜き力は、ボルトとコンクリートの接触面積に比例するので、
接触面積の小さなホールインアンカーは強度面で不安が出ます。
また、箱部分に水が溜まりますので、モルタルやコーキングで蓋をする方が良いでしょう。
適用先
バッチ系化学プラントでは小型の設備はほとんどホールインアンカーを使います。
小型のポンプやカートリッジフィルターなどが該当します。
配管サポートもホールインアンカーですね。
ケミカルアンカー
ケミカルアンカーはホールインアンカーと似ていますが、箱に固着剤を充填します。
強度が高ければ施工も楽です。
一般の施工会社はケミカルアンカーを基本にしています。
化学プラントではケミカルアンカーの使用は慎重になった方が良いです。
というのも固着剤に化学物質を使っているから。
固着剤の組成を調べて、化学プラントの雰囲気に適合しているかを判断しなければ、
使っているうちに、設備が傾いてきたり倒れるという最悪の結末を迎えかねません。
代表例としてビニルエステル樹脂や不飽和ポリエステル樹脂がありますが、
これってFRPと同じ材質です。
化学プラントでFRPを使っているなら同じ材料をアンカーボルトの固定に使っても良いだろう、という意見と
溶媒に弱い樹脂系は極力使わない方が安全安心、という意見の対立構造になります。
アンカーボルトを据付ボルト(Installation bolt)に使う時のメンテナンス
アンカーボルトは意外とメンテナンスが必要な部品です。
たかがボルト・・・と軽視するわけにもいきません。
キャップで外面腐食防止
アンカーボルトを長い間使い続けるためにできる効果的な方法にキャップがあります。
キャップを付けてキャップ内を樹脂で充満させ、コンクリート基礎との隙間をシリコンコーキングで埋めます。
こうすることで、外気や雨によるアンカーボルトの腐食を大きく軽減することができます。
アンカーボルトは鉄製ですので、使っているうちに腐食していきます。
ボルトナットで固定しているだけなら取り替えできますが、アンカーボルトはコンクリートに固定しているので取替は大変。
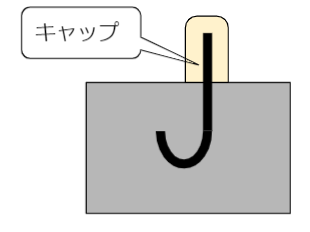
アンカーボルトを使う工事の基本セットとしてキャップを付けていきたいですね。
ステンレスライナーでモルタル保護
箱抜アンカータイプで使うライナーはステンレス製の方が良いです。
何も考えずにいると鉄板を使うでしょう。
この鉄のライナー。結構錆びます。
錆が進行すると体積が膨らんできて、ライナーを押し上げて浮いてきます。
ライナーとコンクリートの隙間を水が伝っていって箱の部分やアンカーボルトを腐食していきます。
工事段階で簡単にできることで長期的な効果ができるので、ぜひともやっていきたいですね。
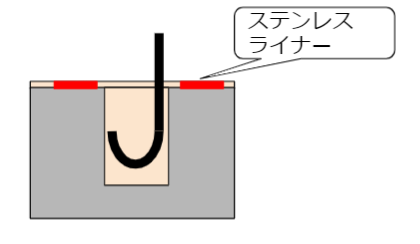
どうしても駄目なら溶接
ボルトの溶接も1つの手です。
キャップやステンレスライナーをしていてもボルトが腐食していった場合に、工事期間をちょっとでも短縮しようとする最終手段です。
積極的に採用するものではありませんが、使用条件によっては採用しても良いでしょう。
ボルトの腐食している部分を切断して、ネジ棒を継ぎ足すという方法です。
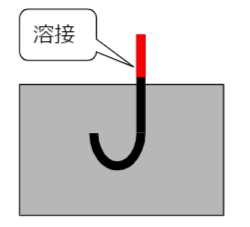
かなり強引ですよね。
溶接をしたボルトは、既定のボルトより当然弱いです。
下手に採用してボルトが折れてしまっては元も子もありません。
ボルトの数・大きさや強度を良く考慮したうえで、実施できそうであれば採用してもいいという程度です。
とっておきの裏技であって、ずっと採用しないくらいでちょうどいいです。
中間脚
大型機器を据え付けるときは中間脚の考え方をしっかり持っておきましょう。
中間脚とは下の図のようなイメージです。

右の図が中間脚のイメージ。
足が一本中間に入っています。だから中間脚。
中間脚を付けることでメリットはいっぱいあります。
- 機器のボルトピッチが分からなくても建屋設計ができる
- 機器の長距離運搬時に短い車両で運搬できる
- 狭い工場内で機器を運搬するときに楽
- 据付時の微妙な位置調整が可能
この発想は配管のフランジと全く同じです。
反応器など大型の設備だと1の建屋設計との調整は期待しない方が良いでしょう。
大型機器の重心が狂うと振動が発生したときに危険だからです。
バッチプラントではそんな機器はほぼなくて、基本的にはマシンボルトでの据付で十分。
中間脚のメリットを活かしやすいです。
短いプロジェクト期間で機器設計と建屋設計を同時に処理しつつ、現地の土建工事を分割する場合には、中間脚の発想がむしろ普通というくらいです。
テンプレート
テンプレートは中間脚と似ていますが、使い方が若干違います。
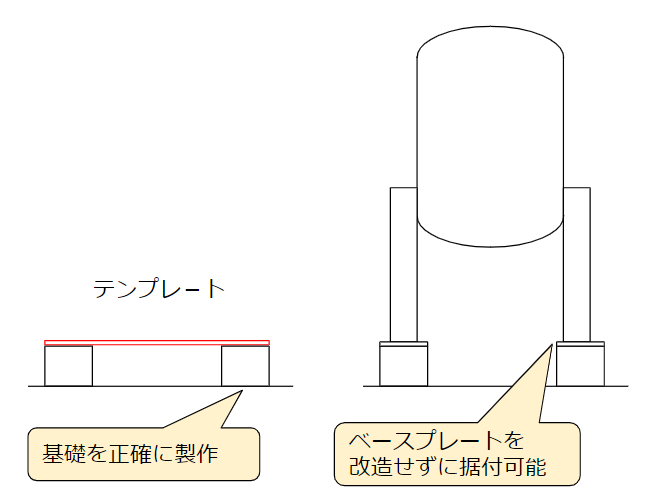
テンプレートは機器製作段階で作ります。
- ステップ1機器の外形製作
- ステップ2機器に脚を取り付け
- ステップ3テンプレートと合わせてボルト穴加工
- ステップ4テンプレートを客先に渡す
- ステップ5テンプレートを使って基礎工事
- ステップ6機器が納入されて据付が難なく完了
テンプレートとは鍵の複製と似たような発想です。
機械も基礎も一度作ってしまうと修正が難しいわりに、高精度の製作が要求されるから、しっかり合わせて置きたいです。
設備設計エンジニアがせひともこだわりぬきたい部分です。
テンプレートを使わないで、埋込アンカー方式を採用する場合は機械側のベースプレートの加工が必須です。
通常は下のような長穴加工を予めしています。
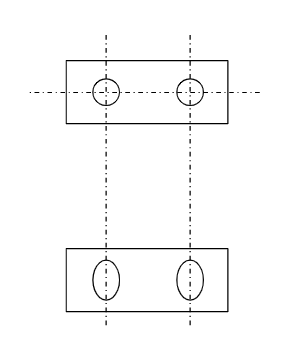
この例は熱交換器などの、運転温度で設備が膨張するのを逃がす意図で使うことが多いでしょう。
据付の位置調整としても使えます。
この処理をせずにテンプレートも使わずに、据付工事に入って据付できないとなったらどうするでしょうか。
現場でガスを使ってベースプレートを切っていきます。
これはエンジニアとしては負け。明確な失敗です。
ちゃんと設計をしていれば防げますし、設計者としては起こしてはいけません。
なお、テンプレートはメーカー支給が普通ですが、逆パターンというのも存在します。今となっては離れ業的な扱いですが。
参考
据付の話はボルトの話に戻ってきます。
ボルトに対する知識を深めるには以下のような本が良いでしょう。
関連記事
本記事の前提となるタンクや反応槽について、詳しく知りたい方は以下の記事をご覧ください。
最後に
化学プラントの設備を据え付けするときに最初に考える足回りの思想について紹介しました。
脚・ブラケットの違い、アンカーボルトの種類としての埋込・箱抜き、ホールインアンカー・ケミカルアンカー、中間脚、テンプレートなどを解説しています。
設計者としては絶対に失敗したくない部分。
化学プラントの設計・保全・運転などの悩みや疑問・質問などご自由にコメント欄に投稿してください。(コメント欄はこの記事の最下部です。)
*いただいたコメント全て拝見し、真剣に回答させていただきます。
コメント