ラントの装置日常点検は、安全運転を維持するために欠かせません。しかし、近年注目されるDX(デジタルトランスフォーメーション)による自動化やデジタル管理だけでは、日常点検のすべてを代替するのは難しいのが現実です。
なぜなら、日常点検には技術だけでは捉えきれない「5感」を使った細やかな観察や感覚が不可欠だからです。
この記事では、DX時代における日常点検の限界と、現場で求められる「5感」の重要性について解説します。
化学プラントで設備を安全安定に動かすためには、日常点検(daily check)が非常に大事です。忙しくなってきた現代では手を抜きがちになりますが、日常点検は手を抜いてはいけません。DXで人の代わりに点検してくれる未来はそう遠くはないですが、まだまだ人間の方が有利。
特にDXを推進している人は、設備のことを詳しくなく何をチェックしたらいいのか分からずに、設備導入をしようとします。日常点検で何を見るか?ということは設備を扱っている人しか分からないので、機電系エンジニアの価値はここでも発揮されます。
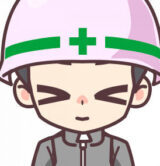
設備を正しく理解して、日常パトロールをしよう!
日常点検(daily check)が安定運転のカギ
24時間365日運転する化学プラントなどでは日常点検がとても大事です。
一般に、日常点検・操業中・定期点検それぞれで異常が発見する割合は
日常点検・操業中・定期点検 = 3 : 5 : 2 と言われています。
ここで日常点検・操業中・定期点検の定義をはっきりさせておきましょう。
- 日常点検は、製造部の管理者やスタッフが日々のパトロールで確認する点検
- 操業中は、設備の起動停止や周囲のバルブ操作などをするとき
- 定期点検とは、設備を全停止して、設備を分解して確認する点検
この定義によると、実際には日常点検と操業中というのはほぼ同じ意味で捉えてもいいでしょう。
日常点検に操業中も含めると日常点検:定期点検=8:2という比率になります。
多分言い過ぎではありません。
やはり現場で使っている人が一番大事です。
ポンプでも攪拌機でも動かすときが一番異常が発見しやすく、動かすときに現場を確認する運転員が、その情報を最も掴める立場にあります。
- いつもと違う!
- 何か変だ!
というレベルで気が付くだけで運転員としては十分すぎます。この感度があることが大事です。
何も言わないよりも、気が付いたことはドンドンあげていく方が大事です。
ここで異常を発見して、定期修理時の準備をすることで安定的な設備運用が可能です。
日常点検(daily check)は5感
現場主義派の論調に乗っかかりそうで怖いですが、現場での日常点検は5感がすべてです。
5感とは、目・耳・鼻・味・触です。
これらを最大限活用することが現場では求められます。
日常点検の基本は運転中の設備をできる範囲で確認するということに尽きます。
現実的にできることがどれくらいあるかという視点で確認しましょう。
目で計器・漏れの有無を確認
五感の中でも最重要のセンサーが目です。
現場で目を使って得る情報とは何があるでしょうか?
最も分かりやすいのが計器の情報です。
でも必要な情報はDCSに取り込めば現場でなくてもOKですよね。
重要度がやや低い計器だけでもとりあえず見たいという計器が現場にあって、それを目で見るというニーズがあるくらいでしょう。
- 圧力計・負圧計
- 常時運転の流量計
- 熱交換器の出口の温度計
- 撹拌機の電流計
いずれも重要度が高くないので、現場パトロールでも見落としがちな情報ですね。
計器以外に現場で見るべき情報として漏れがあります。
化学プラントでは特に漏れの早期発見は安定運転のためにとても大事。
漏れとして確認すべきものをいくつか例を紹介しましょう。
- フランジのガスケットからの漏れ
- サンプリング口からの液漏れ
- 粉体仕込口からの粉漏れ
- 潤滑油の漏れ
いかにも保全的な内容ですね。パトロールの基本でしょう。
耳で異音を確認
日常点検では耳は意外と大事です。
というのも人間の耳は結構優秀だからです。
いつもと違う音がするかどうか。
ここに注意をするだけでOK。
回転機器やバルブ前後で異音が出ていれば何かがおかしいと感じます。
何が正常であるかさえわかっていれば、正常でなければ異常と判断することができます。
専門保全レベルなら聴診棒などを使いますが、日常点検レベルならバルブハンドルやボールペンでも代用できます。
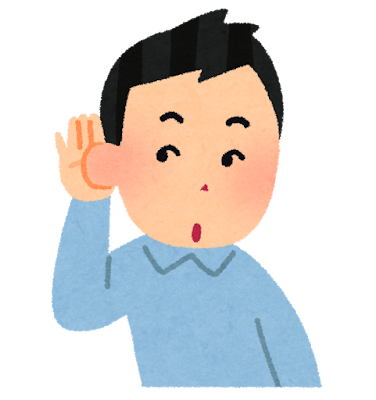
鼻で臭気を感じる
日常点検では鼻もすごく大事です。
ガスが漏れた時に鼻で検知できる確率は高いです。
工場の近隣地域住民の方から「変なにおいがする」というクレームがでるときもあります。
臭いは音よりも直感的に分かりやすいですよね。
化学プラントで扱っている薬品には異臭が強いものもあり、判定しやすいです。
ガス検知器などを使うことも大事ですが計測範囲が限定されるので、人間の鼻はまだまだ活躍します。
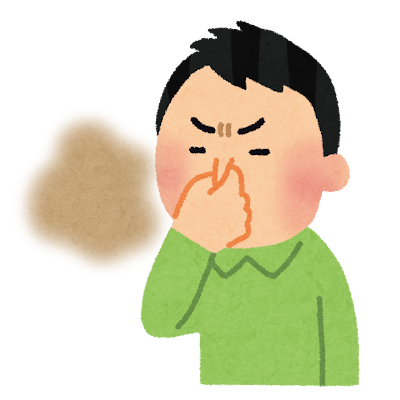
味わう → なし
工場で味覚を使って保全をすることはありえません。
昔の研究者は未知の薬液をちょっと舌で舐めてみるということをしたことがあるらしいですが、今の工場では即否定されるレベル
手で振動や温度を調べる → 反対
手で電動機を触って振動や温度を調べる、ということがよく言われます。
ですが、私はこれに反対します。
少なくとも日常的に行う作業ではありません。
- 手で回転部を触ると、挟まれ巻き込まれの思想が醸成されない
- 手で設備や配管を触ると、火傷する恐れがある
手で触るとケガをする可能性があります。
昔はちょっとした怪我でも許容されたと思いますが、すでに時代は違います。
DXで代用できる五感
日常点検は人間の五感が大事というのは今後も変わりませんが、DXで代用できる部分はどんどん増えていきます。
DXで保全の自動化という点にターゲットを当てている分野もありますが、五感を自動化するというのが基本になるでしょう。
その例を紹介しましょう。
目はカメラ
五感の中でも目は非常に大事でしょう。
現場に行くとき「現場を見ないと分からない」と自然に言いませんか?
見るという「目」の情報が大事だという意識があるわけですね。
目で見れる情報は色々ありますが、実は結構な部分は監視カメラで対応できます。
化学プラントで監視カメラを使う例はいくつもあるでしょう。
- 現場計器や測定器の値を観測する作業
- サンプリング・仕込・充填などの現場作業
- 反応器内の状況
- 分液作業のガラス管内の液の状態
- バルブ開閉の確認
- 窃盗盗難などの監視
- 火災などの監視
いわゆる普通の防爆カメラでもかなりの部分を確認できますが、赤外線などの特別なセンシングを使って人間の眼よりも効率的に監視できる装置もでき始めています。
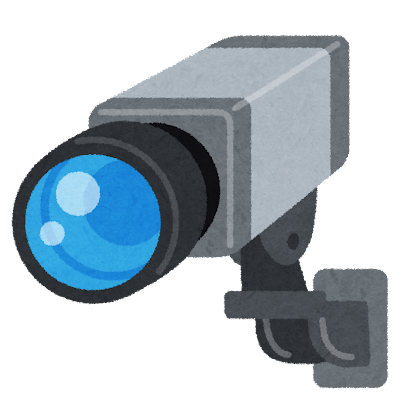
耳は代用が難しい
耳をDXで置き換えるにはマイクを使うことができるでしょう。
でも音の解析は非常に難しいです。
少なくとも費用対効果がでるまでにはまだまだ時間が掛かるでしょう。
特定の設備の特定の音だけを検知するということはできなくはないですが、数多くある設備のどの周波数の音をキャッチするか?という視点で進めていくのが精いっぱいでしょう。
測定機の導入・運用・メンテナンスに専門の人間が必要になります。
こういう技術を持つ人が今後の保全マンの歩むべき1つの道となりますが、主流になることはないでしょう。
鼻は代用が難しい
鼻のにおいに関する情報をDXで置き換えるのは難しいです。
測定装置の検出範囲が狭いからです。
ガス検知器や酸素濃度計などのガス検出器が鼻の代用となりますが、測定範囲の狭さが課題です。
人間の鼻はその意味で主流のまま残るでしょう。
パトロールしていない時間帯にも人間の代わりに監視をするという意味で検知器類は活用しますが、
DXによって人が行っている部分の大半を機械が行うという未来はまだまだ先だと思います。
味 → なし
化学プラントで人間が五感のうち唯一使わないのが味。
DXでも触れない部分ですね。
触る → 基本的になし
測定機器で設備を触って検出するというニーズもなかなか進まないでしょう。
振動計など原始的な機器を使うことは思いつきますが、音と同じで解析が難しいです。
特定の振動数だけを引っ張ってこないといけないけど、その範囲を決めることが難しいからです。
個々の設備の運転条件・プロセス内容量・建屋の強度などいくつもの情報が付加されます。
本当に重要な機器に限定して付けるという程度で、人間にとって代わることはそうそう無いでしょう。
メンテナンスフリー
日常点検でほぼメンテナンスフリーという機械はいくつかあります。
専任の保全員が巡回で月に1回程度回るだけで十分という機械です。
例を紹介しましょう。
誘導電動機
そもそも誘導電動機はかなりメンテナンスフリーに近いです。
- 100%負荷条件で使う機会が少ない
- 周囲環境はプロセス内より過酷な条件ではない
こんな条件が吹く案れているからです。
100%負荷で運転することは少ない
特にバッチ系化学プラントでは、100%条件で運転するのは商用運転の設備に限定され、ポンプやブロアーに限定されます。
攪拌機などはインバータを付けるため、100%の速度で運転することは少なく
最大負荷条件で使う機会は少なくなっています。
モーターの使用環境は空気とあまり変わりない
プラント内にある電動機は、雨風の影響を受けないわりに「屋外型」にしているとかなりの防御力があります。
ポンプや回転機の内容物は腐食性が高く、温度・圧力の影響も受けやすいですが、モーターは外気に露出していますので、影響は少ないです。
外部環境の悪影響というと、有機溶媒のガスとか粉体です。
それはプロセス内部の影響よりは遥かにマイルドな条件。
一般的な機械として確立している電動機であれば、化学プラント用の電動機であっても条件が大きく変わることなく、
メンテナンスフリーに近いと言えます。
軸受もメンテナンスフリーに近い
軸受でも特にすべり軸受はほぼ半永久的に使えます。
転がり軸受の場合は、グリース封入式ならほとんど日常点検は不要です。
周期を決めて定期的に修理する方が良いでしょう。
減速機
減速機は日常点検ではモーターと同じようにメンテナンスフリーに近いです。
これは油で満たされた環境であるからですね。
構造が相対的に複雑で起動停止時にダメージを受けやすいので、定期的なメンテナンスは必要です。
でも日常点検でチェックするかというと難しいところ。
月に1回程度の巡回点検では、その時に設備が運転していなかったというパターンが多いです。
油圧機器
油圧機器も日常点検ではメンテナンスフリーに使いです。
減速機と同じように油で満たされた構造だからです。
油圧シリンダーや油圧モーターを使った設備が底固い設備だからこそ、日常点検での重要度は相対的には低いです。
取扱説明書の位置づけ
メーカーの設備を購入したときに付属される取扱説明書。
これを日常点検に活かそうとしている企業はどれくらいあるでしょうか?
少なくとも化学プラントの機械設備は30年以上進歩がないのでありがた味を感じる人はいないでしょう。
実は使える取扱説明書です。
点検リスト
取扱説明書には点検リストのようなものがあります。
これが非常に見にくいです。
設備の部品名ごとに以下のようなモードが記載されているはずです。
- 損傷
- 汚染
- ゆるみ
- 動作
日常点検リストとは言葉通り日常使うことを目的としています。
日常とは「毎日」です。
取扱説明書を毎日見ながらパトロールする人なんていないし、チェックリストを付けてもその資料が膨大になるでしょう。
取扱説明書で書かれている内容からエッセンスだけを抽出して、保全カレンダーを作るという意味では有用です。
現実的にできる部分だけを抽出するという点に、保全マンとしての技能が関係して来るでしょう。
社内教育
取扱説明書は社内教育で使うことが一応は可能です。
教育者からすると「目からうろこ」の状態。
資料を水増しすることができ、受講者に情報を与えたという実績もでき、一見それっぽく見えるからです。
でも受講者が説明書を見てもすぐに理解できるはずがありません。
まさに形だけ。
運転方法
取扱説明書には運転方法が記載されています。
これが意外な落とし穴。
設備の劣化速度が速いのでいざ調べてみたら、設備構成が取扱説明書と違っていた。
なんてケースはまれにあります。
これは設計者の力量の問題。
日常的に使っている設備ほど落とし穴にはまる確率が高いです。
保全マンは設備の補修履歴を網羅的に把握することができるので、補修頻度が高いものについては取扱説明書を見なおしてみると新たな発見があるかも知れません。
ベテラン層ですでに暗記するほど見た!と思っている人もいるかもしれませんが日々勉強ですよ。
参考
設備保全は現場で学ぶものという風潮が強いです。
しかし、教えてもらえる先生が少なくなっている現在では、下のような書籍も活用して効率的な学習をしましょう。
関連記事
さらに知りたい方は、以下の記事をご覧ください。
最後に
日常点検はDXによるデジタル化が進む一方で、機械では検知できない現場の「5感」が依然として重要です。
経験ある作業者の観察力や感覚は、安全運転を支える最後の砦とも言えます。今後もDXと5感のバランスを考え、現場力を高める取り組みが求められます。
現場での点検は五感が全てです。特に目・耳・鼻が大事。
目はカメラでとってかわられますが、耳と鼻はまだまだ人間の活躍する分野です。
化学プラントの設計・保全・運転などの悩みや疑問・質問などご自由にコメント欄に投稿してください。(コメント欄はこの記事の最下部です。)
*いただいたコメント全て拝見し、真剣に回答させていただきます。
コメント