粉体を扱うラインでは詰まりは常に付きまとう問題です。
特に真空下で運転する場合には、真空ラインが粉体によりトラブルを起こしがちです。
その問題を解決するには、結構な装置が必要になります。
後で困らないように、導入段階から考えましょう。
粉は巻き上がる
当たり前の話ですが、粉は巻き上がります。
例えば粉体が容器の中に入っている状況を考えましょう。
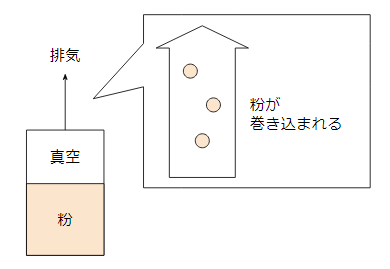
容器を真空にするために、気相部を排気していきます。
ここで、空気だけが外に排出されて粉は全く動かない、と勘違いしたプロセスが割とあります。
実際には粉は気体と一緒に巻き込まれます。
容器が真空ポンプと連結している状況を考えましょう。
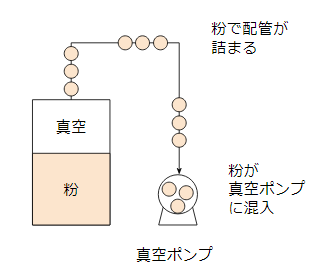
粉が気体と一緒に巻き上がるので、配管内に粉が付着して最終的に閉塞する可能性があります。
最終的には閉塞しますが、その手前には配管の流路面積が狭くなっていき、圧力損失が増えて、所定の真空度を得られないという形で表れてきます。
また、粉体は真空ポンプにまで移動してしまうと、真空ポンプを破損させる可能性が出てきます。
真空ポンプ能力が落ちたり、シール性が保たれずに運転できなくなるリスクがあります。
これらの理由から、粉体を真空ポンプに巻き込まないようにする仕組みが必要となります。
フィルターで除去
ライン中で粉を捕まえる方法の典型例が、フィルターです。
バグフィルターと呼ばれる大型のフィルターが一般的です。
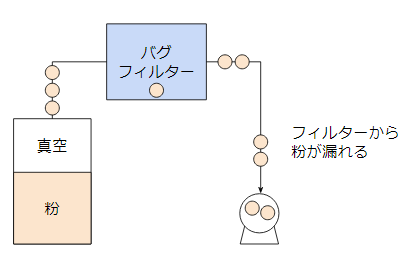
真空下では気体の体積が上がるので、小さなフィルターだと圧力損失が高くなります。
フィルターで粉を捕まえたとしても、運転を続けていくと粉が溜まり続けていき、圧力損失が高くなります。
定期的にフィルターを逆洗する装置が必要です。
それらの機能を持ったフィルターがバグフィルターと考えて良いでしょう。
フィルターでは完全に粉を取り除くことはできません。
100%ではなく一部の粉は抜けていきます。
フィルターの目開きがどの場所でも完全に同じでないことと、粉の径がすべて一律であるわけでないということが理由です。
バグフィルターで粉をできるだけキャッチしようとするなら、逆洗の回数は自ずと上がります。
水で落とす
フィルターでキャッチすることが難しければ、別の手段を考えましょう。
1つ目が水です。
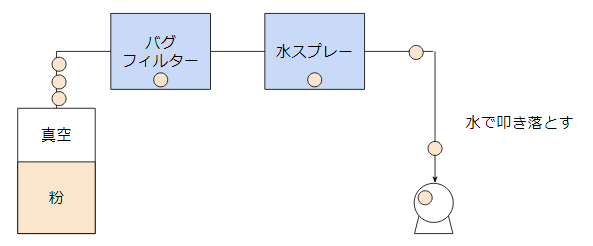
粉体の舞っている気体に、水をスプレーします。
水は重力で下方に流れ、気体は上方に流れます。
下方に流れる水に粉体がキャッチされ、気体と粉体を分離させるという仕組みです。
水スプレー以外にも、水シールでキャッチするという方法もあります。
いずれも、水はワンパスで使用するのがよく、循環させるなら定期的な入れ替えが必要です。
水スプレーの量や、水シールの深さが大きいと、圧力損失が大きくなるので、設計時に注意したいですね。
サイクロンで最終除去
水シールで粉体を除去したとしても、その水自体が気体と一緒に巻き込まれる可能性があります。
水をスプレーしても、ミストであったり液滴であったり、大きさが一律ではありません。
このうち細かな水は重力で下に落ちる前に、気体の流れに巻き込まれてしまいます。
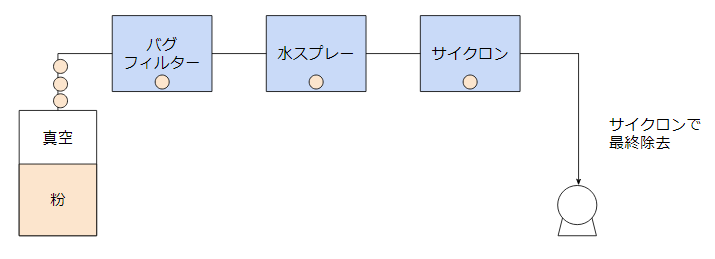
これを除去するために、サイクロンなどの気液分離装置が有効です。
サイクロンによって水と粉体を除去した後は、ほぼ気体だけの状態で真空ポンプに導かれます。
サイクロンで水(と粉体)を除去した後は、水の処理が必要です。水スプレーと合わせて処理するのが良いでしょう。
並列設置か水処理か
真空と粉体の問題を考えていくと、以下のどちらを優先するかという問題に直面します。
- 真空ポンプを複数台置いて、壊れる前に交換や洗浄する
- 真空ポンプを1台置いて、壊さないように粉体を除去する
今記事では下の例として紹介しましたが、真空ポンプを複数台置いて、状態監視するという方法も実は考えられます。
こういう組み合わせがいろいろ考えて実践できるのは、ユーザー側のエンジニアならではでしょう。
私はこの辺りの選択肢を考えるのが、かなり好きです。
参考
関連記事
最後に
真空ラインで粉体を詰まらせないための方法として、フィルター・水スプレー・サイクロンの方法を紹介しました。
粉が必ず巻き込まれるという前提で、対策を取りましょう。
真空ポンプを複数台置くという選択肢もあります。
どれがいいかはユーザーの状況によって変わります。
化学プラントの設計・保全・運転などの悩みや疑問・質問などご自由にコメント欄に投稿してください。(コメント欄はこの記事の最下部です。)
*いただいたコメント全て拝見し、真剣に回答させていただきます。
コメント