ステンレス配管(stainless pipe)の特殊仕様について紹介します。
ステンレス配管は鉄の配管と同じような感覚で配管設計をすることが多いでしょうが、実はオリジナルの設計要素をいくつか持っています。
マニアックな内容ですが、トピックス的に紹介していきましょう。
化学プラントで使用するステンレス配管はJIS G 3459「配管用ステンレス鋼鋼管」が一般的です。
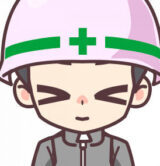
ステンレス配管のオプションって結構ありますよ
この記事は、SUS304シリーズの一部です。
SS400とSUS304|化学プラントの2大材質
SUS304・SUS316Lの比較|ステンレス2大材質
SUS304配管の設計が基本の化学プラント
なぜ304ではなく316Lを選ぶのか?化学プラントでのステンレス材選定のポイント
シームレス
化学プラントのステンレス配管はシームレス管を選択します。
ステンレス配管は製作方法の違いによってTP-A(電気抵抗溶接)、TP-S(シームレス)と区別して表記します。
SUS304ならSUS304 TP-Sという感じですね
化学プラントのエンジニアならTP-Sという表現すら意識せずに「SUS304」、「SUS316L]という名前だけを認識しているでしょう。
実際に購入した配管の仕様や実物に記載してある仕様を眺めてみてやっと「TP-S」ってなんだろうって疑問に思う程度です。
それくらい当然のものとして、シームレス管を使っています。
継ぎ目からの腐食がない
TP-Sのシームレス管には継目がないため、腐食の可能性が相対的に低いです。
TP-Aの溶接管は、溶接継ぎ目があります。
ここは完全には除去できません。少なくとも、熱影響部は残り続けます。
化学プラントでステンレス配管を使う場合、漏れたら危険であり腐食性が高い薬液を扱います。
絶対に漏らしたくないという安全性を高めるために、シームレス管を採用します。
特に応力腐食割れが腐食の形態として多い化学プラントでは、その原因となる溶接を極力少ないと考えます。
調達性が悪くない
TP-Sのシームレス管は調達性がそこまで悪いわけではありません。
TP-Aの溶接管のデメリットが無いTP-Sの方が加工が難しく調達しにくいと思う人もいるでしょう。
ところが、実際にはそこまで調達性が悪くはありません。
価格は若干高いですが、劇的に高いわけでもなし。
化学プラントではTP-Sには目立ったデメリットが無い、という良い方もできるでしょう。
漏れても良いので、コストを重視してTP-Aにする会社もあるでしょうが
そのコストに見合ったリスク管理ができる会社は少ないです。
結果、災害という大きなコストを支払うことになります。
配管精度は問わない
TP-Sのシームレス管はTP-Aの溶接管よりは配管の製作精度はよくありません。
SGPの熱間仕上げと冷間仕上げのような位置づけですね。
SGPでも製作精度を問わず、熱間仕上げを採用することが多い化学プラント。
ステンレス管も同じように製作精度はあまり問わないので、TP-Sで十分対応可能です。
スタブエンド
ステンレス配管をフランジ接続する場合、スタブエンド構造を取ることがあります。
スタブエンド構造を、最初に確認しましょう。
普通のフランジ構造と比較します。
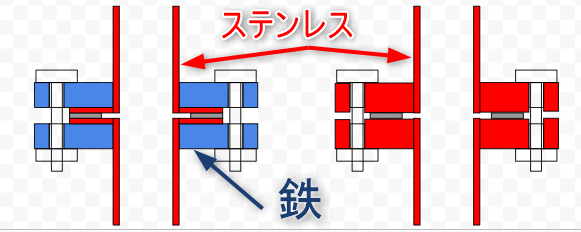
左側がスタブエンド構造、右側がフランジ構造です。
赤色の部分がステンレスで、青色の部分が鉄です。
配管内溶液と接触している部分はステンレスで、フランジの外側だけ鉄という構造ですね。
資材が安い
スタブエンド構造は、資材費が安いです。
これは当然のこと。
資材の費用は
ステンレス > 鉄
ですので、ステンレスの量が少ないスタブエンド構造の方が「お安い」ことは確かです。
溶接が少ない
スタブエンド構造の方が実は溶接数が少ないです。
下の図を見てみましょう。
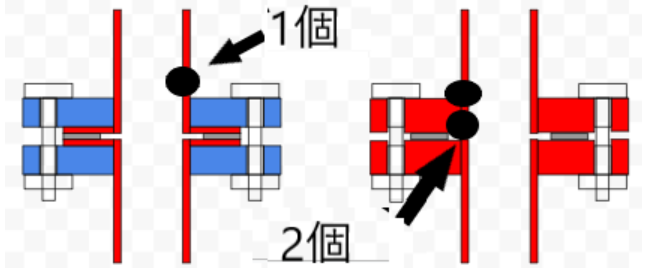
左側のスタブエンド構造は溶接数は1個です。
右側のフランジ構造は溶接数は2個です。
スタブエンドの方が溶接数が少ないですよね。
その分だけ作業費は安くなります。
厳密なDB(ダイヤインチ)で考えるとフランジのDBは2ではないので、純粋に1:2の関係ではなく1:1.5とする方が適切です。
それでも、スタブエンドの方が安いことは確かです。
腐食しにくい
スタブエンドの方が腐食はしにくいです。
どこの腐食でしょうか?
それはボルトとの接触部です。
下の図を見てください。
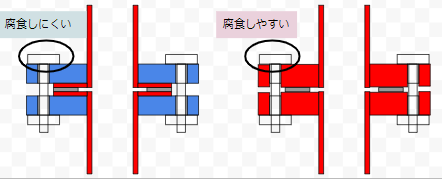
フランジとボルトの材質を整理します。
場所 | スタブエンド | フランジ |
フランジ | 鉄 | ステンレス |
ボルト | 鉄 | 鉄 |
スタブエンド構造だとフランジとボルトが同じ材質です。
フランジ構造だとボルトだけが鉄です。
どちらもボルトが腐食するのは確かです。
しかし、フランジ構造だとボルトの当たっているフランジ部の腐食も進みます。
こうなると、ステンレスフランジそのものを交換しないといけません。
それよりは鉄のフランジだけを腐食させる方が安心ですよね。
厳密には鉄のフランジとステンレスのスタブエンドが接触している部分でも腐食は起きます。
フランジの腐食が進んだ時にはスタブエンド構造でもフランジ構造でも、配管一体を作り変えます。
その意味では腐食についてはあまり差異がありません。
この辺は考え方の違いですね。
現地合わせがしやすい
スタブエンド構造の方が、現地作業がしやすいです。
これはフランジのボルト穴の問題です。
ボルト穴の位置は普通はある方向に統一します。
下の図は中心線で振り分けたパターンです。
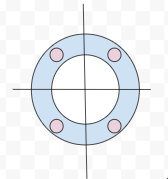
これを45度変えるパターンもあります。
いずれにしろ、フランジのボルト穴の位置はあるルールに則って施工します。
実際に現地で配管施工したときに、フランジ面の水平垂直が厳密にできあがるわけでなく、ズレは必ずできます。
スタブエンド構造だとこのズレを容易に現場で修正できます。
フランジを少し回すだけです。
フランジ構造だとフランジはあらかじめ溶接してしまっているので、
現場で強引に繋げないといけません。
これは配管に過度な力を加えて曲げる方向です。
応力腐食割れなどのリスクを高めますし、配管を曲げてしまって液たまりやガスたまりができるリスクもあります。
異径フランジ
鉄やステンレスの配管で異径フランジってそもそも聞いたことがない人もいるかもしれません。
考え方としては結構あっさりしたものですが、「おじいちゃんの知恵」のような扱いです。
構造や特徴を説明します。
構造
異径フランジの構造を下のイメージに示します。
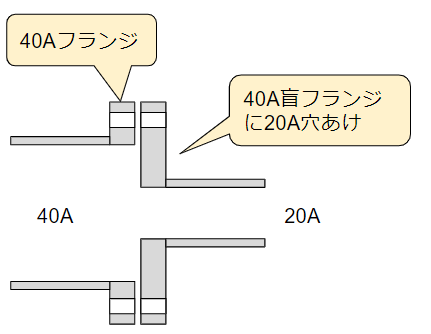
40Aの配管に20Aの配管を接続するための、異径フランジ例です。
レデューサや異径チーズと同じく「40A/20A」という書き方をします。
異径フランジは、盲フランジに穴を開けた構造をしています。
40A/20Aの異径フランジなら、40Aの盲フランジに20Aの穴あけをします。
簡単な構造でしょ?
「盲フランジを使う」というのが盲点でしょうかw
レデューサとの違い
異径フランジとレデューサの違いを見てみましょう。
レデューサは以下のようなイメージですよね。
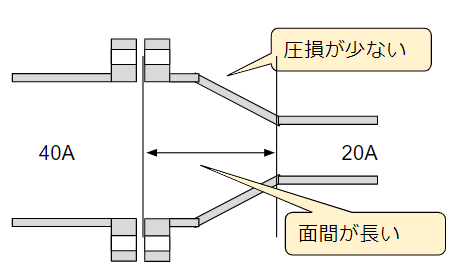
異径フランジに対してレデューサは以下の特徴を持ちます。
- 圧損が少ない
- 面間が長い
レデューサは口径の「絞り」が異径フランジよりも滑らかなので、圧損は当然少ないです。
圧損が高いことは運転上はできるだけ避けたいところ。
だからこそ、口径を絞る時は一般的にレデューサを使います。
滑らかに絞る分だけ、面間は長くなります。
既設改造時に大活躍
異径フランジはそもそもどんな場合に使うでしょうか?
「面間を小さくしたい」場合ですよね。
どんな場合に面間を小さくしたいでしょうか?
既設配管を改造する場合に面間を小さくしたいというニーズが出てきます。
今回の例では40Aの既設配管があって、ここから20Aに絞らないといけないという場合です。
特に高さの制約が厳しい場合として、設備間の構成位置が決まってしまっていたり、液たまりを極小化したい場合があります。
液たまりは化学プラントでは需要が大きいですよね。
ここで、レデューサしか思いつかないと「液たまり量はこれが限界!」って思考停止してしまいがちですが、
異径フランジを付けるとさらに削減することが可能です。
柔軟な発想をしたいですね。
直管厚みを下げる
配管の直管とフィッティングは同じ厚みにする方が良いという当たり前のことを説明します。
かなりマニアックですよね。
この状況を、言葉だけで理解できればかなりのベテランさんです。
これは配管の厚みを薄くするという選択肢があるからこそ、出てくる悩みです。]
以下のようなイメージを考えています。
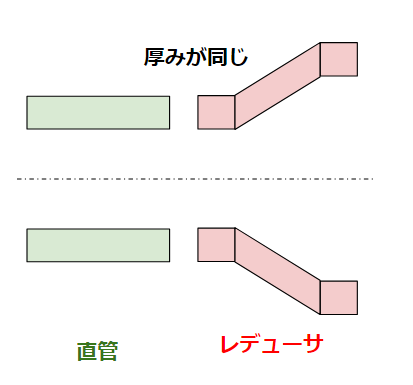
配管とレデューサを繋げているイメージです。
配管とレデューサが同じ厚みである方が良いよ!というのが今回の結論。
配管厚みは変更可能
配管厚みはJISで決まっている規格品と思うでしょう。
これっていくつかのパターンが存在します。
Sch(スケジュール)で区分します。
Schは配管の圧力に関して規定する式ですが、配管厚みの規格という理解でOKです。
SUS304のSch10sという規格なら2.8mmという厚みで指定できます。
これがSch5sなら1.65mmですね。
配管厚みは薄くしたい
配管厚みにはSchによる選択肢が存在します。
それなら配管厚みはできるだけ薄くしたいという思考はあってもおかしくありません。
板厚を薄くする方が、材料調達コストが安いです。
バッチ系化学プラントでは高圧の運転が存在しません。
Sch10sの配管でも使えますが、それよりも薄いSch5sでも十分に使用できます。
だから配管厚みはSch5s相当にしたいと思うでしょう。
フィッティング厚みは変更しにくい
フィッティング厚みは配管厚みに比べて選択肢が少ないです。
私はフィッティングのSch5sは見たことがありません。
この場合、フィッティングはSch10s相当を選ぶことになります。
配管厚みとフィッティング厚みを変えると手間がかかる
配管厚みを薄くしてもフィッティングの厚みは変わらないと、実は一手間必要となります。
この一手間が、調達コストの削減を圧迫してしまい、トータルコストはあまり変わりません。
この一手間とはなんでしょうか?
配管厚みを薄くした場合に配管とフィッティングを繋げる下イメージを想像しましょう。
この2つの部材を繋げる場合、一般に以下のように滑らかにするための処置をします。
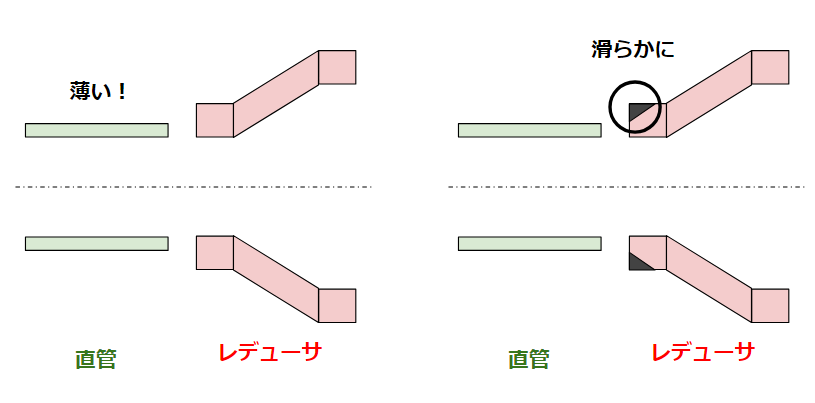
グラインダーなどでレデューサの端部を削り取ります。
こうしないと、溶接個所で不連続部分が出来上がります。
不連続部は応力集中が掛かりやすく、溶接割れが起こります。
グラインダーで削り取るという一手間に人件費が掛かります。
配管の厚みを下げることで、
- 得られる調達コストのメリット
- フィッティングの端部を削る人件費というデメリット
どちらが勝つかという勝負になります。
労務費が上がっている現在は、手間賃の方が影響が大きいでしょう。
フランジ厚みを下げる
フランジ厚みは実はJIS5kにするという選択肢もあります。
直管のSchと同じように、フランジ厚みも圧力に応じた規格があります。
JIS10kフランジなら1000kPaまで、JIS5kフランジなら500kPaまで耐えるというのが基本的な考え。
それ以上の圧力でも耐えることは耐えますが、そんな踏み込んだ議論をいきなりするのは止めた方がいいです。
フランジ厚みを下げると当然コストも下がります。
でも500kPaってバッチ系化学プラントでも結構微妙な世界。
気を許すと600kPa程度で使用する場合があります。
汎用的な使い方を想定する場合は例外がほとんど起きないような設計条件にするべきなので、1000kPaまで上げておく方が無難です。
JIS5kでもJIS10kでも調達性もコストも大きなインパクトはありませんからね^^
参考
最後に
ステンレス配管の特殊仕様について紹介しました。
シームレス・スタブエンド・異径フランジ・直管肉厚・フランジ厚み
設計思想を統一化させる方が良いですが裏技的に使える要素もありますので、関連知識として知っておきたいですね。
化学プラントの設計・保全・運転などの悩みや疑問・質問などご自由にコメント欄に投稿してください。(コメント欄はこの記事の最下部です。)
*いただいたコメント全て拝見し、真剣に回答させていただきます。
コメント