化学プラントにおけるプロセス制御では、「時間特性」の理解が非常に重要です。特にバッチプロセスでは、無駄時間や伝達遅れといった要素が制御の精度に大きく影響します。これらの特性は、温度・圧力・流量といった各変数ごとに異なり、設計や運転上の注意点も変わってきます。
本記事では、プロセス特性の基本である時間特性について、初心者にも分かりやすく解説します。
無駄時間
無駄時間というのは、ちょっと言葉がひどい気がします。
でも、確かに無駄な時間です。
水を流して、温度計が水の温度を検知している状態で、蒸気を入れたとしましょう。
その瞬間に、水と蒸気が混ざった部分の温度は上がります。
ですが、その温度の上がった水が温度計に到達するまでの間に、時間がかかります。
温度計に到達するまでの物理的な距離があるからです。
これは無駄時間に区分されます。
蒸気と水が混ざる、まさにその部分で温度が測れたら無駄時間はゼロになります。
下図のように、蒸気を入れてから、温度計の指示値が変わり始めるまでの時間として、表現できます。
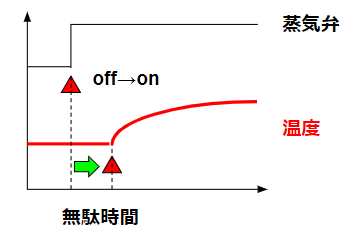
伝達遅れ
水に蒸気を入れた、混ざり合ったその部分の温度を、その瞬間に知る術はありません。
そもそも水と蒸気の温度の真値を知ることすらできません。
というのも、温度計はプロセス液と直接接触しているわけでなく、隔壁をはさむからです。
これは無視したとしても、温度計の顕熱分だけ、指示値の表示が遅れることは確かであり、これが伝達遅れと呼ばれます。
例えば、20℃の水に、100℃の蒸気を混ぜて、80℃の温水を作ろうとしましょう。
温度計の指示値は、蒸気を混ぜる前は20℃です。
蒸気を入れた瞬間に80℃の温水ができます。
これを温度計が検知したとしても、温度計の指示値はいきなり80℃になるわけではありません。
温度計自身が20℃から80℃にあがるために、熱量が必要だからです。
これを専門用語で顕熱と呼ぶこともあります。
温度計が80℃に上昇するまでにかかる時間は伝達遅れに区分されます。
厳密にいうと、温度計が20℃から80℃までに上がるまでの間は、20℃の水と100℃の蒸気で混ざった80℃の温水は、温度計の出口では80℃よりやや低い温度になります。
これは温度計に限らず、配管の顕熱も含んでいます。
今回の例での伝達遅れは、温度計・配管等の顕熱分による遅れ、という表現も可能です。
温度の伝達遅れは大きい
温度で伝達遅れが起こるのは、潜熱があるからです。
プロセスで温度変化が起きた時に、プロセスの顕熱が変わるだけでなく、周囲設備の顕熱も変わります。
伝達遅れの度合いは、温度変化量そのもので効いてきます。
圧力の伝達遅れは小さい
圧力で伝達遅れが起こるのは、測定器が物理的に動くからです。
ブルドン管式でも隔膜式でも、圧力という物理的な力を受けた検出部から、伝達部に伝搬して表示されるためには時間差があります。
とはいえ、この圧力の伝達遅れは温度の伝達遅れに比べれば微々たるもの。
圧力において伝達遅れを気にすることはほぼありません。
それよりは無駄時間に起因する要素の方がはるかに気になるでしょう。
液体ならポンプ、気体ならファンで、圧力が上がった流体が、別の場所に移送されるまでの間に、物理的な距離によって移動時間がかかります。
これはまさに無駄時間。
圧力損失、動圧、気体の圧縮性などの要因はプロセス特性として外乱の要因になりえますが、伝達遅れには該当しません。
この辺は、定義や物理特性などの本質を見る努力が大事でしょう。
流量の伝達遅れは小さい
流量も圧力とほぼ同じ無駄時間があります。
流量の伝達遅れも圧力の伝達遅れとほぼ同じ微々たるもの。
流量計で流量の変化を感じて物理的な変化が起こったら、すぐに伝達部に伝搬して、表示されます。
液面の伝達遅れは小さい
液面は流量や圧力と同じく微々たる伝達遅れがあります。
液面の伝達遅れを気にする人はいないと思います。
しかし、液面計は信頼度が低いため、伝達遅れがあるのでは?と疑問に持つ人がいます。
差圧式液面計なら原理は圧力計とほぼ同じ、電波式液面計なら電波・音波式液面計なら音波を使うため、伝達遅れはほぼありません。
信頼度が低い理由は、以下のようなものがあります。
- 液面揺動や撹拌の影響があるために測定位置の液面が真値か分からない
- 差圧式なら動圧の影響を受ける
- 電波式、音波式などでは系内の雰囲気の影響を受ける
流量制御
流量制御の例として、フローとプロセス特性を考えましょう。
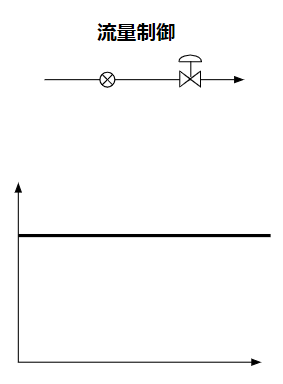
この流量制御は、以下の目的があります。
ポンプで液体を移送している時に、流量計の指示値を検知して、一定量を常時移送し続ける。
移送元がタンクであり、タンクの液面が下がってきたら、ポンプの送液量は若干ですが下がっていきます。
液面ヘッドが、ポンプ出口の圧力に影響を与えるため、ヘッドが高い方が流量が大きいからです。
バッチプロセスではポンプ送液以上に、自重落下の方がこのパターンの流量制御行うことが多いです。
ポンプがない方が、液面ヘッドによる影響が大きく出るからです。
それはいいとして、流量の指示値に応じて、調整弁を速やかに作動させて、流量を一定にします。
プロセス特性は時間に依らずほぼ一定です。
これは流量の伝達遅れが少なく、応答性が早いことが背景にあります。
特にポンプの場合は、流量が比較的早く、動機器を使っているという都合上、外乱が多いです。
したがって、プロセス特性も常に一定値を示すわけでなく、多少の振れがあります。
それでも一定範囲内に抑えやすい、制御しやすい系と言えます。
温度制御
バッチプロセスの温度制御の例を紹介します。
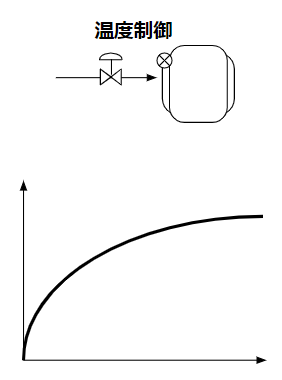
タンクにコイルというの伝熱装置を取り付け、タンク内に液体を入れ、コイルに蒸気を入れて、タンク内の温度を検知し、温度に応じて上記の量を調整する。
というプロセス制御になります。
このプロセスでは、温度による伝達遅れが顕著に表れます。
伝達遅れとして温度計の顕熱以上に、プロセス液の顕熱が顕著です。
フローには攪拌機が付いていませんが、少なくとも攪拌機は必須。
ところで、このプロセスはバッチ反応ではあまり多くはありません。
これは「一定温度に保つために、調整計を使う必要があるのか?」という問題です。
調整弁でなくて、
on-off弁を使って、タンク内の温度が一定値になるまで弁を開け、一定値になれば弁を閉める。
というon-off制御でも対応できる場合が多いです。
もしくは、蒸留等の場合には、温度制御を掛けずに、
一定の弁開度で蒸気を供給したり、一定流量の蒸気を供給するというような、流量制御側で対応することもあります。
液面制御
液面制御の例を紹介します。
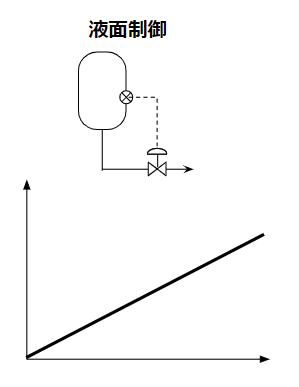
タンク内に液体が流入しながら、ポンプで払い出しをし続ける。
こういうプロセスは実はバッチ工場ではほとんどありません。
プロセス制御の教科書でよくあるような問題であり、流入ラインの調整弁の適切に制御できれば、制御できそうな気がします。
この例では、ポンプで一定量を払い出しているが、それ以上に受け入れをしていて、液面が常に一定量だけ増え続けるという使い方になります。
こういう使い方はバッチプロセスでは使いません。
受け入れは受け入れ単体で、払い出しは払い出し単体で、それぞれ分けて操作します。
それこそがバッチ運転です。
参考
最後に
化学プラントにおけるプロセス制御では、「時間特性」を理解することが不可欠です。無駄時間・伝達遅れは制御の遅延要因であり、変数ごとにその影響度は異なります。特に温度制御における遅れは大きく、設計・運転の際に注意が必要です。
機械エンジニアとしては、これらの基本的な知識を身につけておくことで、プロセス全体の安定運転に貢献できます。
化学プラントの設計・保全・運転などの悩みや疑問・質問などご自由にコメント欄に投稿してください。(コメント欄はこの記事の最下部です。)
*いただいたコメント全て拝見し、真剣に回答させていただきます。
コメント