プラント設計は、技術的に完璧を追求することが大切と思われがちですが、実は真面目すぎる設計が現場での運用や保守に支障をきたすこともあります。現場で役立つ設計とは、柔軟さと実務的な視点を持ち合わせたバランスの良い設計です。
本記事では、真面目なだけでは解決できないプラント設計の課題と、その解決策について解説します。
プラント設計(plant design)の仕事を15年以上経験してきた私は、自分の仕事の付加価値を常に疑問に思っています。付加価値といってもいろいろなベクトルがありますが、何に力を使うかはその組織やプラントに要求させる事項によって左右されるべきです。
ところが、これを明確に表現できる人は居ません。
製造現場や工事現場の人とコミュニケーションを取って、試行錯誤しながら自分のスタイルを確立していくことでしょう。
多くのことを即決即断しなければいけないプラントエンジニアの仕事で、設計に過度にこだわらなくても良い(適当に考えても意外となんとかなる)という考え方を解説します。
分からないことだらけで悩んでいる、プラントエンジニアの手助けになれば幸いです。
イニシャルコストを抑えたいって本当?
プラント設計の仕事でイニシャルコストを抑えることは、最大の付加価値だと一般に考えられます。
例えば概算50億円のプラント建設を計画して、40億円で完成したら嬉しいですよね。
このために、徹底して努力をしようとするプラントエンジニアはとても多いです。
例えば、以下のような感じです。
- 装置メーカーに発注を掛けるときに、1円でも安い会社に依頼する
- 工事会社に依頼するときに、見積のとても細かい部分を見て1円でも安くする
- 配管m数を1mでも短くしてコスト削減をする
- 1手でも作業性が楽になるような配管レイアウトを考える
私が新入社員のころは、こういう教育を確かに受けました。今では全否定しています。
これらの目線は一定のレベルまでは考慮が必要です。
ただし、1円でも1mでもという単位にまで絞り込んでいくと、キリがありません。
機電系エンジニアの仕事は、本人が意図していなくても、こういった細かいレベルでの検討になりがちで、悩めば悩むほど時間を浪費します。
かといって、こういう例はあまり好ましくありません。
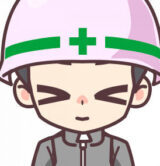
これ、他にもっと安い案ありませんか?
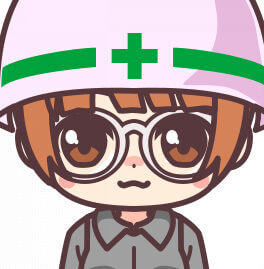
思いつきません。
考えるだけ時間の無駄です。
上司であるあなたが案を出してください。
言いたくなる気持ちは一応分かります。
こういう時に、素直に言わずに以下のような回答ができるとかなり印象が変わります。
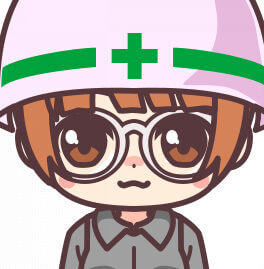
B案はたしかに数%程度安くなりますが、多分3年くらいで漏れが起こります。
C案は10年くらい安心感がありますが、50%くらい高くなると思います。
この数値は割と適当でも構いません。
与えられた環境でいくつかの案を考えて、絞り込んだという過程が大事です。
案自体は陳腐な物でもよく、何か1つの要素を変える程度でOK。
これを即興でできるようになるためには、構成される要素の分割と変更可能な要素の抽出が必要で、エンジニアの素質が試されます。
いくら時間を掛けても良いし、どんな手段を使っても良いから、イニシャルコストを徹底して押さえたいという会社は良くありませんね。
ランニングコストは評価しにくい
イニシャルコストと同じようにランニングコストに時間を掛けるエンジニアはとても多いです。
実は、これも時間を掛けすぎても意味があまりありません。
使い勝手は誰が評価する?
ランニングコストの代表例が使い勝手です。
使いやすいプラントは、運用コストが安いという表現ができなくもありません。
しかし適正に評価できる人は居ないでしょう。
- 手動操作や移動が楽になって、作業員が事故するか確率が減る
- 液溜まりやガス溜まりがちょっとでも少なくなり、配管の交換頻度が下がる
これらは、機電系エンジニアの絶対使命として言われているものの、数値化が難しいです。
数値化できないけど大事だから徹底するように!
否定することは許せないという流れで主張されがちです。
オペレータの立場からすると、そこまで考えてくれるエンジニアはありがたい存在です。
ところが、この検討に時間を掛けすぎたがゆえに、工期が遅れて生産開始が遅れたり、予算を超過したら元も子もありません。
同じことを繰り返しますが、全く考えなくて良いというものではありません。
考えるべきことを理解したうえで、その場その場で優先度や目標を人に合わせて変えていくことが望ましでしょう。
メンテナンス性はどうやって評価する?
プラント設計はその数年間は大変ですが、本当に大変なのはそのプラントを何十年を使う側の人。
製造や保全の人達です。
メンテナンス性はその意味で大事ですが、評価が難しいです。
Aランク・Bランク・Cランクの3段階くらいの評価はできるでしょう。
プラント設計者が実際の設計段階でメンテナンス性を悩んでいる時は、この3段階が変更するような大きなレベルではありません。
誰が考えてもBランクがAランクになることはなかったりします。
思いついても変更しようとしたら、とても多くの労力が必要になったり、時間切れになったりします。
いろいろな状況の中で、エンジニアができることは限られています。
機電系エンジニアの設計の質が良くなかったから、プラントのメンテナンス性が良くなかった。
こういう風に特定の人のせいにするような意見には、耳を貸さなくて良いでしょう。
プラントの寿命はどうやって評価する?
プラント設計が良くなかったとしても、数年オーダーで何かの問題が起きることはほとんどありません。
大抵は、10年20年と使ってしまいます。特に日本だと。
使いにくくても使ってしまうプラントだと、プラント設計の最終的な成果であるプラント寿命は評価がしにくくなります。
その組織にいる人なら誰が設計しても、どれだけ時間を使っても、結果は大差ない。
そう考えると、時間を掛けるだけ無駄だと思いませんか?
考えるべきことを理解して思いつくけど考えないということと、思いつきもしないということは全く別です。
拘りすぎては意味がない設計例
具体的にどういう部分にこだわってはいけないか、いくつか例を紹介しましょう。
配管のサブルート
プラント設計段階で、プラント形状や主要装置の配置と同じくらい、プラントメインルートは大事です。
問題はそこから後。
メインルートから枝分かれするサブルートを拘る人は、まれにいます。
確かにこれは運転段階や施工段階で一定の差が出ます。
理想的な取り方から、少しくらい失敗しても、大抵は運転できます。
液もガスもちゃんと流れます。
配管の寿命や、工事のちょっとした手間が変わる程度です。
問題になる数が少ないので、ランニングコストを評価してもほとんど影響がでないでしょう。
配管高さ
配管高さは、プラントの設計で確かに大事です。
標準化して、適切な運用をしてくことはエンジニアの基礎スキルでしょう。
しかし、長い間運転して改造していくと、そうも言っていられなくなります。
- 腰くらいの位置に配管があって、人が通るときに屈まないといけない
- タンクからポンプまでの間に液が溜まり、開放しないと液が抜けない
- バルブの操作位置が高い
こういったケースがどんどん出てきます。
プラント設計者としては、後々の改造も含めて新設時にある程度の余裕やしっかりした初期設計をしておきたいのですが、かなり難しいです。
プラント建設の頻度が少なく運用時の苦労を知るにも時間が掛かるため、現場の問題を言語化してプラント建設に反映できる人が極端に少ないからです。
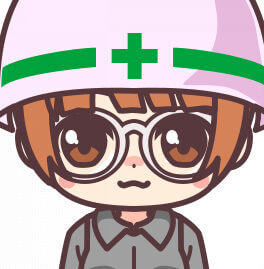
配管高さを少し上げたいので、今回の新設プラントでは高さを上げたいです。
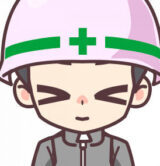
コストが上がるので嫌。他のプラントも今まで文句出てないでしょ?
何とかみんな頑張ってやっているから、そこは変えずに進めましょう。
こんな言い方をされるでしょう。
仮に、自分の思いが建設に反映できる機会があるかも知れませんが、運の世界です。
私は、おそらく一度もそういう機会に触れれないまま、日常業務での不満を抱えて仕事をしていくことになるでしょう。
フランジの個数
フランジの個数は、イニシャル・ランニングのいずれにおいても本来は大事です。
フランジが多いほどイニシャルコストはあがりますし、漏れのリスクがあがるのでランニングもあがります。
ところが、これを設計段階で見抜いて何とかするのは、結構な時間が掛かります。
配管図を書く段階で適切に支持し、配管図ができ終わるまでに何度もチェックしないと理想形には到達しないでしょう。
そこに労力を掛けるくらいなら、一度工事してしまって運転をして、劣化具合を見ながら修正を掛けていくという方が現実的です。
配管図で3次元をイメージして、長期的な運用をイメージすることは、エンジニアのスキルとしては大事ですが、誰もができるわけではありません。
割り切りは大事ですね。
配管ヘッダー
配管ヘッダーは、プラント配管設計の大きな要素です。
配管図を書く最初の段階で、決めるべきことです。
でも、ここに時間を掛けても得られる効果は年々少なくなっています。
自動化が進んでいるからですね。
バルブの開閉は現場で人が作業して、目視確認をしてヨシ!をする。
こういう光景はかなり少なくなりました。
自動弁で開閉して、DCSと現場で開閉状況を確認し合う。
ヘッダーは生産の最初と最後に扱うだけで、日常的には触らない。
こうなったら、設計の優先度は落ちていきます。
参考
関連記事
最後に
プラント設計は技術的に正確であることが求められますが、真面目すぎて融通が利かない設計はかえって現場の負担を増やしてしまいます。設計段階から現場の意見を取り入れ、柔軟でシンプルな設計を心がけることが、結果的に安全で効率的なプラント運営につながります。
プラント設計などの悩みや疑問・質問などご自由にコメント欄に投稿してください。(コメント欄はこの記事の最下部です。)
*いただいたコメント全て拝見し、真剣に回答させていただきます。
コメント