化学プラントで一度設置した設備は、かんたんには変更できません。わずかな変更にも1年かかるのが当たり前で、それだけに新しい設備を導入する際は、実績との比較や安全性の確保が極めて重要です。しかし、それでも「現場で試さなければ意味がない」というケースもあります。
本記事では、現場でのテストを安全に実施し、なおかつ有効な検証ができるようにするための実践的な配管設計や工夫について紹介します。
被害を最小限に止める配管構成
設備のお試しをするには、失敗に対する被害を最小限にする手段を考えましょう。
具体的には配管を上手いこと改造します。
例えば以下のような方法を取ります。
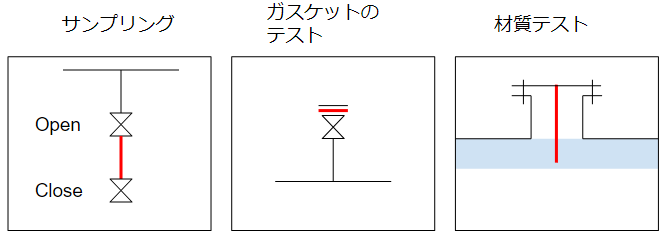
それぞれテストの目的によって変わりますので、個別に解説しましょう。
サンプリング
サンプリングは設備のテストの一面がありますが、運転のテストの一面もあります。例えば以下のような例があります。
プロセスの確認のように見えますが、設備の問題から対策を取ろうとしたときにも使う手法です。
サンプリングやモニタリングを安全にするために、二重バルブと貯めるだけの配管を設置します。
覗き窓を付ける例もあります。
二重バルブにしていると、真空下での運転でも安全にサンプルを取ることができます。
現場テストの基本形ですので、何か試そうとしたときには最初に考えましょう。
ガスケットのテスト
ガスケットのテストは、現場レベルではかなりニーズがあります。
漏れが起きたら困る割に、ガスケットは最適な物を見つけるのが難しい。
設備中の配管にセットしようにも、漏れてしまったらとても危険。
かといって、サンプル液に単に浸しているだけでは不十分。
この辺りの微妙な問題で、現場ラインにガスケットを安全にセットすることは、重要な課題です。
具体的にはバルブとブラインドフランジの間に、ガスケットを挟むようにしましょう。
漏れても被害を最小限にするために、上向きにします。
ガスケットから漏れが認められたら、バルブを閉じてガスケットを交換すれば終わり。
基本形ですので、悩むことなく提案できるようにしましょう。
材質のテスト
材質のテストをする場合は、液体と気体の界面がありそうな部分に、上向きのノズルを取り、試験片を挿入できるようにしましょう。
タンクの上ノズルを活用すると良いでしょう。
設置する前に重量を測っておき、一定期間過ぎた後で取外して再度重量を測ります。
実設備で危険なことをせずに、サンプル液に浸すだけでも結構な調査が可能です。
とはいえ、信頼性が一番高くなる方法は、現場で使うこと。
金属系などテストできる物が限られていますが、上手く使いましょう。
ガスケットのテストで紹介したような、ブラインドフランジを使うテストもあります。
ガラスライニングやフッ素樹脂ライニングのような特殊な材質向きです。
特徴比較と安全対策をしっかりと
現場でお試しをするというのは、かなり危険なことです。
できるだけ実験室で調べるのが良いのですが、現場で試さないと意味がないテストも存在します。
少しでも設備の寿命を延ばし、安全な運転をするためのテストなら、製造管理者も基本的には断らないでしょう。
試験の目的・比較すべき特徴の整理・安全対策をしっかりと説明すれば、製造も協力してくれるでしょう。
製造管理者にしっかりと説明して納得してもらう説得力は、生産技術以外でも使えるスキルになるでしょう。
上手くいかない場合には、生産技術者自身が現場を確認することになり、現場立ち入りの許可など安全対策を取らないといけなくなり面倒です。
参考
関連記事
最後に
化学プラントの設備は簡単に交換できないからこそ、現場での安全なテスト設計が求められます。
- サンプリングには二重バルブ+短管配管
- ガスケット試験にはバルブ+ブラインドフランジ構成
- 材質試験には上部ノズル+試験片の投入
これらはすべて、失敗時のリスクを最小限に抑える基本形です。安全と検証効果の両立を実現するために、事前準備と工夫を怠らないことが大切です。
化学プラントの設計・保全・運転などの悩みや疑問・質問などご自由にコメント欄に投稿してください。(コメント欄はこの記事の最下部です。)
*いただいたコメント全て拝見し、真剣に回答させていただきます。
コメント