ガス配管(ガスライン)は化学プラントにおいて、漏洩や圧力、爆発などの重大リスクをはらんでいます。一般的な呼び径の配管材(SGP)は水配管には十分でも、ガス用途には安全性が不足する場合があります。ガスラインには、材質(例:SGPW、STPG)をワンランク上げる判断が必要です。
本記事では、その理由と選定のポイントを、設計者視点でわかりやすく解説します。
ガスラインの材質選定の問題は、化学工場ではとても大きな問題になります。
いくつかの考え方がありますが、化学プラントであれば金属系の配管にすることが基本だと私は思っています。
ところが、私の身近なプラントでも必ずしもこの思想で設計されているわけではありません。
選定の背景や起こりうることをまとめました。
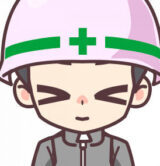
設計の重要度が下がりやすいのがガスライン。だけど問題はここで起きます。7
静電気着火のリスクが高い
化学プラントのガスラインの設計で最も気を付けるべきことは、静電気着火です。
ガスには有機溶媒が一部含まれているからです。
プラントの反応や運転で発生したガスをどこかに集めようとしているのだから、有機溶媒が含まれていても当たり前のはず。
ところがガスラインの設計をするときには、この当たり前の事実を意外と忘れ去ってしまいます。
ガスラインの中には圧力容器を回避するために、大気に一度開放することがあります(集気ラインと私は読んでいます)
この場合は、ガスラインに空気を追加することになるので、静電気着火のリスクを1つ上げてしまいます。
プラント内で静電気を回避するために空気の混入をいくら防いでも、ガスラインで空気を入れてしまうと怖いですね。
ガスの性質がいろいろある
化学プラントのガスラインでは、静電気着火にだけ気を付けたら良いというわけではありません。
ガスの性質がいっぱいあります。
例えば、腐食性の高いガス・毒性の高いガス。
こういういくつかの性質を持つガスですが、集気ラインの場合は空気で薄めているために、あたかも空気として取り扱えば良いという錯覚をしていまいます。
静電気着火のリスクすら忘れ去られてしまい、空気として取り扱ってしまいます。
これがガスラインで起こる悲劇のスタートラインでしょう。
樹脂系の材質は失敗しやすい
ガスラインの内容物を、ガスではなく空気として取り扱ってしまうと、材質選定を樹脂にしてしまいがちです。
塩化ビニルが典型例。
安くて軽くて溶接をしなくても施工できる手軽さが最大のメリット。
静電気着火のリスクがあるガスを通した場合、電気を通さない樹脂配管は静電気を溜め込んで着火する可能性があります。
ガスラインはガスを送り出すために流速も高めに設定して、口径はあまり大きくありません。
流速が高いから静電気が発生するリスクが高くなりますね。
樹脂配管を選ぶ場合には、有機溶媒が完全に存在しない酸系のガスに限定した方が無難です。
溶媒を含んで静電気着火というのも嫌ですが、溶媒がライン中に溜まってくると腐食をする確率が高くなります。
コスト重視で樹脂を選んだ結果、大きな事故に繋がるリスクを抱えることになります。
金属系を選ぶ時の注意
ガスラインでは樹脂配管だとリスクが高いので、金属配管を選ぶという選択肢があります。
例えばSUS304やSUS316L。
この場合は、静電気着火のリスクは1つ下げることができます。
ただし、腐食のリスクは少し上がります。
ここを許容できるかどうかはプロセス次第。
ガスラインは引き込み方式が多いので、配管に多少の穴が開いても外に漏れずに吸い込める可能性があります。
ガスが凝縮してミストになると、その穴から漏れるので危険ですけどね。
金属配管にするということは、このリスクをしっかり認識して日常パトロールで検査して定期的に交換するという作業が発生します。
認識をしていないと、結局は問題が起きます。
それでも静電気着火で新聞に報道されるような大事故に比べると、程度としては小さくなるので、金属配管にしている方がまだマシでしょう。
ライニング配管は高い
静電気着火と腐食性の問題の中間を狙う戦略として、ライニング配管があります。
ガラスライニングやフッ素樹脂ライニングですね。
ガラスやフッ素という電気を通さない材質と触れるので、静電気が発生しますが外側の金属部から静電気が逃げていきます。
耐食性はもちろん高くて安心です。
ただし、コストが高いことが難点。
フランジ接続なのでガスケットの漏れのリスクもあります。
樹脂・金属・ライニングどれを選ぶかは、設計思想による部分がありますが、しっかり選定しましょう。
それでも樹脂は止めておいた方が良いだろう、というのが個人的な意見ですね。
参考
関連記事
最後に
ガスラインでは、漏洩や爆発などのリスクが高いため、配管材質は液体用よりもワンランク上の材質(SGPW、STPGなど)を選ぶべきです。適切な材質の選定は、プラント設計における安全性、運用効率、メンテコスト低減に直結します。特にガス用途では、材質選定を重視することが設計者の責務です。
化学プラントの設計・保全・運転などの悩みや疑問・質問などご自由にコメント欄に投稿してください。(コメント欄はこの記事の最下部です。)
*いただいたコメント全て拝見し、真剣に回答させていただきます。
コメント