化学プラントや配管設備で欠かせない「フランジ接続」。その密閉を支えているのが、ガスケットとボルトナットのシステムです。
でも、「なぜガスケットが必要?」「ボルトはどう締める?」といった疑問も多いはず。
この記事では、フランジのガスケットやボルトナットの基本構造と役割を、初心者にもわかりやすく紹介します。
安全で漏れない配管接続を理解するために、ぜひご覧ください。
機械的な知識に詳しい方なら当たり前の内容ですが、化学プラントの機械屋のように「機械屋としては初心者+α」の方に知っておいてほしい内容をまとめています。
これを知るだけで、化学プラントの機械屋としてはかなり高いレベルになると思います。
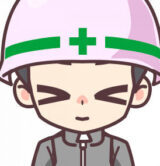
フランジをシステムとして考えよう!
この記事は、フランジ(設計)シリーズの一部です。
JIS10Kフランジに頼らない!化学プラントでの柔軟なフランジ選定ガイド
フランジとガスケットの接続寸法を比較
フランジとパイプの接続を寸法表でもっと確認
フランジ・ねじ込みとパイプの接続を寸法表で確認する方法【基礎】
フランジと溶接の接続方法の違い|プラント初心者向け
配管の接続方法をやさしく解説|フランジ・ねじ・溶接の使い分けと選び方
フランジが化学プラントの配管設計で大事な理由
【初心者向け】JISフランジの呼び圧力とは?意味・違い・使い分けをわかりやすく解説
【配管初心者向け】RFフランジとFFフランジの違いとは?特徴と使い分けをわかりやすく解説
フランジ(Flange)のシステム
配管フランジとボルトナットのシステムを下に示します。
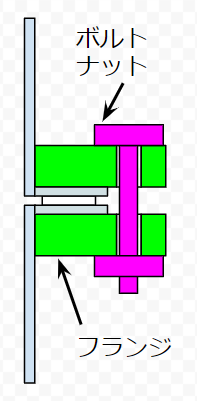
これは、配管・フランジ・ガスケット・ボルト・ナット(ワッシャ)という要素から構成された立派なシステムです。
材質・力を中心に化学プラントにとってのフランジシステムとして重要な箇所を解説します。
材質
化学プラントの配管用のボルトナットはフランジより1ランク材質を落とします。
ここで配管材質とフランジ/ボルトナットの材質が問題になります。
フランジ(Flange)と配管の関係
フランジ材質と配管材質の関係について、一般的な組み合わせを下に示します。
配管 | フランジ |
SGP | SS400 |
SUS304 | SS400 |
高級金属 | 高級金属 |
これは配管材質よりもフランジやボルトナットの材質を1ランク以上落とすことを意味しています。
SGPの配管
SGPの配管材質は、最低グレードです。
フランジは配管材質よりも落とすことはできないので、最低グレードのSS400とします。
SUS304の配管
SUS304の配管材質は、バッチ系化学プラントではかなりランクが高いです。
数量も非常に多いです。
配管材質に対して、フランジ材質はSS400とランクを落とします。
これはスタブエンドがあるから。
スタブエンドを使うと、フランジ材質にこだわる理由はありません。
最低グレードのSS400で大丈夫です。
高級金属の配管
高級金属は配管材質とフランジ材質を同じにします。
スタブエンドを使わないで、配管とフランジを直接溶接するからです。
ボルトナットとフランジ(Flange)の関係
ボルトナット材質とフランジ材質の関係を紹介します。
ボルトナットの材質はフランジ材質よりも低くする側で設定します。
下の表を見てください。
配管 | フランジ | ボルトナット |
SGP | SS400 | SS400 |
SUS304 | SS400 | SS400 |
高級金属 | 高級金属 | SUS316 |
配管とフランジの関係は上の項目そのものです。
ボルトナットの項目だけを右端に追加しています。
SGPの配管
SGPの配管はフランジ材質がSS400なので、ボルトナットシステムもSS400です。
最低グレードであるため、考え方がシンプルです。
SUS304の配管
SUS304の配管はフランジ材質がSS400なので、ボルトナットシステムもSS400です。
高級金属の配管
高級金属配管は、ボルトナットシステムはSUS316系にします。
SUS316は汎用的な耐食材質の中では、最高グレードです。
配管やフランジが高級なので、ボルトナット材質はランクを落としたとしても汎用材質の最高グレードに留めます。
ボルトナット材質を低くするのは、ボルトナットは交換ができるから。
グレードの違う材質を2つ接触させると、グレードの低い材質の方が早く腐食するのが普通です。
ここで交換のしやすいボルトナット側を材質を落とすことで、意図的に腐食する部位を選び出し、配管やフランジ側の腐食を守ります。
選択的な腐食対策です。
会社によってはSUS316系ではなくSUS304系にする場合もあります。
これはコストや調達性の関係があります。
ボルト材質とナット材質の関係
ボルト材質とナット材質の関係も紹介します。
下の図を見てください。
配管 | フランジ | ボルト | ナット |
SGP | SS400 | SS400 | SS400 |
SUS304 | SS400 | SS400 | SS400 |
高級金属 | 高級金属 | SUS316 | SUS316L |
SGPの配管
SGPの配管は、ボルトナットシステムの材質はSS400です。
ボルトとナットで材質を使い分けずに同じ材質にします。
SUS304の配管
SUS304の配管はルーズフランジを前提とすると、フランジはSS400となります。
フランジがSS400ならボルトナットもSS400ですね。
高級金属の配管
高級金属の配管なら、ナットはSUS316L・ボルトはSUS316とします。
ナットをボルトよりも若干ランクを上げます。
ステンレス系の場合はボルトとナットの材質を完全に同じにしてしまうと「かじり」が起きます。
これを防ぐために、ボルトとナットの材質は若干でも変えます。
ボルトとナットのどちらの材質を優先させるかというと、ナットの材質を若干上げます。
これはナットとボルトのどちらが安いか、という判断です。
ボルトとナットの組み合わせを考えるときナット側を腐食させて、ナットだけを交換する方が安く付きます。
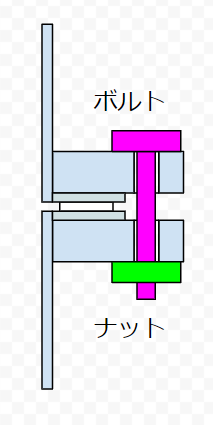
ワッシャーの材質
ワッシャーの材質は、ステンレスフランジなら、ワンサイズ落とした亜鉛めっきにするでしょう。
ナットは、さらに1サイズ落として普通の鉄のナットにすると思います。
そういう設計をします。
では現場ではどうでしょうか?
絶対に使い分けていません。
亜鉛メッキをしているかどうか、1枚1枚確認してフランジを取り付けることはしません。
全部亜鉛めっきにするか、全部鉄にするかで統一していると思います。
フランジ(Flange)に掛かる力
フランジをボルトで締め付けた時の挙動を考える時、フランジ側を先に考える方が分かりやすいです。
これはボルトで「フランジを締める」という本来の機能から直感的に考えることができるからです。
高校の物理で勉強したように、部品ごとに分割しましょう。
フランジ面だけに着目します。
内圧が加わらないとき
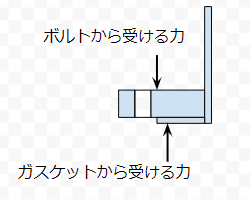
フランジ面をボルトで閉めると、フランジはボルトから締付力を得ます。
この力に反発するように、ガスケットは縮みガスケットの反力をフランジは受けます。
ボルトから受ける力 = ガスケットから受ける力
この関係が成立します。
内圧が加わるとき
ボルトを締め付けた状態で、運転した時を考えましょう。
配管内圧が加わります。
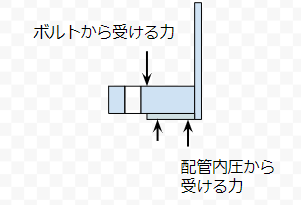
配管内圧を受けたフランジは、ボルト締付力に反抗する形で作用します。
ボルトから受ける力 = ガスケットから受ける力 + 配管内圧
ボルトから受ける力が変わらないと考えると、ガスケットから受ける力は、配管内圧分だけ小さくなります。
ガスケットから受ける力が低くなるということは、ガスケットに加える締付力が小さくなるということ。
ということは、ガスケットから漏れやすくなるということです。
ガスケット係数mや最小設計締付圧力yはこの辺りの世界の話をしています。
- ガスケット係数m 使用時のボルト荷重を決めるための、ガスケットに加える力
- 最小締付圧力y ガスケット締付時のボルト荷重を決めるための、ガスケットに加える力
この辺りは、参考程度の情報で十分です。
バッチ系化学プラントでは渦巻ガスケットを使う時に、最小締付圧力yが問題になる程度です。
ボルトに掛かる力
フランジ側に加わる力が分かれば、ボルト側は簡単です。
ボルトからフランジに加わる力の、「逆」です。
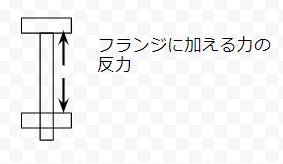
上の図のように、ボルトは伸びる力を受けます。
ボルトを締め付けすぎて、千切れるという問題がありますが、ボルトが伸びる力に耐えきれずに千切れる、という意味です。
人間の力でナットを締め付けていって、ボルトを締め付けているように見えますが、実際に締まっているのはフランジであり、ボルトは伸びている
この辺が、少し戸惑いがありつつ、面白い部分です。
SS400の引張強度
簡易的な物理計算をする時に、SS400は非常に使いやすいです。
極めて汎用的な材質です。
私もこれを使って検算することは多いです。
安全率
引張強度は、この値以上の応力が加われば、材料が壊れるという値と思っていいです。
要は限界値です。
設計をする時に、この値をそのまま使うことはありません。
色々な使用環境によってこの強度より高い・低い値でも破壊するからです。
汎用性を持たせるために余裕率を設けます。
これを私は4で計算しています。
SS400なら100N/mm2
分かりやすいのが一番。
なお、この記事でもSS400で100N/mm2を仮定して計算しています。(計算根拠は載せていませんが・・・)
熱応力と引張強度
熱応力の計算自体は色々なサイトにあります。
SS400のヤング率2.05*105 N/mm2、線膨張係数12.5*10-6(1/K)で常温から800度まで溶接で金属が温められたとします。
ここで金属が完全に固定されていた時に働く熱応力を計算しましょう。
2.05*105(N/mm2)*12.5*10-6(1/K)*800K=2,050 N/mm2 > 100N/mm2
SS400の安全率込みの許容応力を100N/mm2で考えるとその20倍の熱応力が加わります!
完全に割れます!
もちろん、溶接時に金属を完全に固定することはできず、ひずみとなって逃げていくのですが。
オーダーとして凄いものだという認識をしてもらいたいと思います。
800度まで上げるから熱応力が高いと思うかもしれませんが、例えば1/10の80℃上昇したとしても、205N/mm2なのでやはり許容応力100N/mm2を越えます。
80℃というと、設備を加温するときには起こりえます。
ボルトの締付力
ボルトで金属を締める場合、ボルトの締め付けトルクはボルトが壊れない範囲で決めます。
これが大前提
ボルトに加わる応力 = ボルトの締付力 / ボルトの断面積
であり、ボルトで締まる金属はボルトの断面積よりも大きいので、
ボルトで締まる金属に加わる応力 < ボルトに加わる応力
となります。
ボルトで締まる金属に加わる力 = ボルトに加わる力
ですが、
応力 = 力 / 断面積
で効いてくるというロジックです。
ボルトの材質もSS400と同じだと考えると、ボルトで締まった金属に加わる応力は、SS400の許容応力以下だという明確な回答が得られます。
ボルトナットの仕様
ボルトナットにはいくつもの仕様やオプションがあります。
バッチ系化学プラントで使う範囲で記載します。
マシンボルト(半ねじ)とスタッドボルト(全ねじ)
化学プラントではマシンボルトを多用します。
マシンボルトは「半ねじ」ボルトとも呼ばれます。
「半ねじ」の逆は「全ねじ」です。スタッドボルトとも言います。
「半ねじ」は「全ねじ」より強度は弱いですが、コストも安いです。
「半ねじ」はねじの軸に不連続部分があるから、強度が弱くなります。
「半ねじ」はねじ加工をする量が少ないので、コストは低いです。
使用圧力が低く、コスト重視のバッチ系化学プラントでは「半ねじ」マシンハッチ一択です。
逆に、圧力が高い所では、「全ねじ」スタッドボルトを選択肢に入れるべきですね。
メートル・インチと並目ねじ・細目ねじ
化学プラントではメートル並目ねじを多用します。
というのもこれが一般的だから。
「並目ねじ」とは違うオプションは「細目ねじ」
「細目ねじ」はねじのピッチが小さいものです。外観を見ると細かいピッチに見えますね。
「細目ねじ」は強度が弱く、製作コストも高く、焼き付きも起こしやすいです。
その代わりに、締付精度が細かく、小さなトルクで締めることができます。
こういう仕様は。バッチ系化学プラントレベルなら問われることはありません。
「並目ねじ」一択。
長さの単位で「メートル」と「インチ」の2つがありますが、日本では「メートル」を使うことが普通ですよね。
ということで、「メートル並目ねじ」一択です。
ねじ精度「ABC」・仕上げ程度「精中粗」
ねじは製作精度・仕上げ程度を規定しています。
これは「はめあい」のお話と関係があります。
精度の等級として、日本では過去に「1級」「2級」「3級」というランク分けがされています。
現在では「A級」「B級」「C級」という表現もします。
これが「はめあい精度」の区分と対応しています。
「2級」ではめねじが6H、おねじが6gという「はめあい」の精度にカテゴライズされます。
化学プラントでは「2級」「B級」を良く使います。
最も一般的だからですね。
化学プラントでは、少なくともボルトで、精度を気にするようなことはありません。
仕上げ程度も同じように「精」「中」「粗」という分類があります。
推測可能と思いますが、「中」仕上げをバッチ系化学プラントでは使います。
強度区分4.8
強度区分は3.6、4.6、4.8、5.6、5.8、6.8、8.8、9.8、10.9、12.9の10段階があります。
化学プラントでは「4.8」を使います。
というのも一般的だから。
ちなみに、「4.8」というのは呼び引張強さ4×100=400N/mm2,呼び降伏点が400×0.8=320N/mm2という意味です。
化学プラントのエンジニアレベルなら深く知る必要はありません。
ボルトだけでも強度を上げる選択肢があるということだけ知っていればOK。
仮に強度を上げる設計を仕様とした場合でも、強度を考えるより先に材質の指定で対応することが普通でしょうけどね。
8割ナットと10割ナット
ナットは8割ナットを使うのが普通です。
8割ナットとはナットの厚みがボルト径の「8割」という意味です。
8割ナットの別のオプションが10割ナット。
6割ナットという種類も存在します。
ナットが厚い方が、強度が強いですよね。
化学プラントでは強度を問わないので、8割ナットで十分です。
電気亜鉛メッキ(ユニクロメッキ)と溶融亜鉛メッキ(どぶつけ)
ボルトにはメッキをするかどうかというオプションがあります。
メッキは亜鉛を使います。
電気亜鉛メッキなのかか溶融亜鉛メッキなのかの違いがあります。
電気亜鉛メッキは亜鉛メッキ液にボルトを付けて、電気分解によってボルトに亜鉛を付けます。
電気亜鉛メッキは化学的な結合法なので精度が高く、膜厚が薄いので電気を通しやすいです。
化学プラントでは電気亜鉛メッキを好みます。
電気を通すからですよね。
ユニクロメッキという銀色の光沢があるタイプが一般的。
特殊なメッキをする場合は金色や黒色の色が付きます。
溶融亜鉛メッキは「どぶつけ」とも言います。
亜鉛メッキ液にボルトを付けて、物理的に付着させる方法です。
膜厚が厚く、腐食性に優れます。
とはいえ、化学プラントではボルトを犠牲腐食に使うのが一般的。
溶融亜鉛メッキのメリットが、逆にデメリットになってしまいます。
電気計装ダクトなど犠牲腐食を考えずに、ダクトそのものの耐食性を上げる場合には、溶融亜鉛メッキを使います。
ボルト長さ
ボルト長さは、ナットからネジ山が2~3個出るようにするのが基本です。
でも現場ではもっとネジ山が出ていたり、逆に不足している場合も見られます。
口径・フランジ厚み・スタブエンド厚み・ガスケット厚み・ワッシャの有無など化学プラントの配管フランジでは選択肢が多いため、統一したボルト長さを設定するのが難しいです。
取付現場で必要なボルト長さを準備できておらず、余ったボルトを使おうとするがゆえに起こる現象ですね。
事細かにボルト長さをチェックすることは簡単ですが、工事上はやむを得ない部分があることを理解しておきたいですね。
参考
フランジは化学プラントの配管を考える上でとても重要です。
フランジをシステムとして見ている人は意外と少なく、今回の記事を知っているだけでも運用面で色々役に立ちますよ。
もちろん、以下の書籍もとても役に立ちます。
関連記事

最後に
フランジ接続の安全・確実な密閉は、ガスケットとボルトナットの適切な組み合わせと管理にかかっています。
初心者はまず、それぞれの役割と相互作用、正しい締め付け方法を理解することが重要です。
この記事を参考にして、配管接続の基本をしっかり押さえ、安全なプラント運用に役立ててくださいね。
化学プラントの設計・保全・運転などの悩みや疑問・質問などご自由にコメント欄に投稿してください。(コメント欄はこの記事の最下部です。)
*いただいたコメント全て拝見し、真剣に回答させていただきます。
コメント