共通配管について解説します。
化学プラントでは多くの配管を扱います。
コスト削減を狙って配管数量を最小化するためにも、機能の最小化が大事です。
そのために配管のヘッダー化と共通化の仕分けが大事です。
プロセスエンジニアや運転管理者が真剣に考える設計箇所ですが、配管設計者や機電系エンジニアが意外と考えないのが実態です。
プラント設計思想にも関係します。
共通配管って?
今回のキーワードである配管の共通化。
どういうイメージを想像するでしょうか。
早速ですが私が考えるイメージを紹介します。
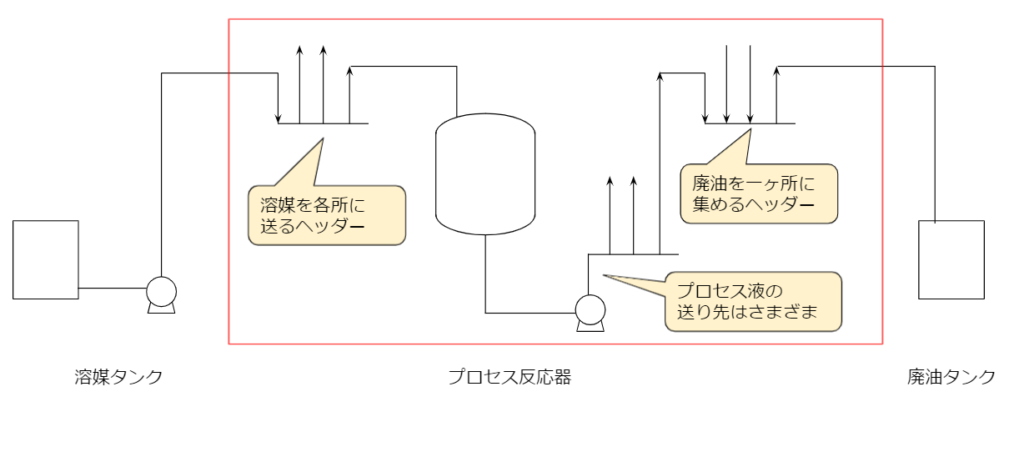
赤枠の部分がプラント内部で、赤枠の外が外部エリアです。
溶媒タンクや廃油タンクはプラント外部に置くのが一般的。
レイアウト的にもタンクサイズや外部とのやりとりなどの面からもごく普通の発想です。
ここで、プラント外部にある溶媒や廃油のタンクからプラント内部に送るための配管が共有化の対象です。
共通化は外面的にはヘッダー化している部分です。
1ライン1用途
配管は基本的に1ライン1用途で使います。
下の図のようにタンクAからタンクBに送るなら1本の配管ですね。
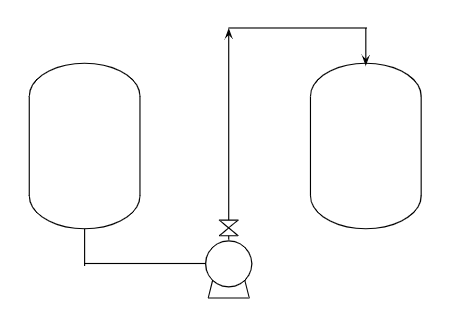
これはタンク数が少なければ問題ないでしょう。
例えば送り先のタンクが複数個あるとこんなフローになります。
逆に複数のタンクから1つのタンクに送る場合は、この絵と全く逆の図になりますね。
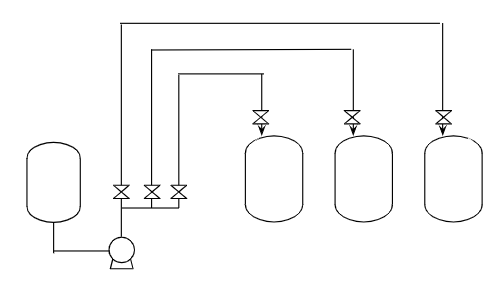
フローだけを眺めている機電系エンジニアはここに疑問を抱かないケースがあります。
しかし、実際にこの通りの配管を引こうと思うと、下のようなケースがありえます。
これは屋外タンクの溶媒をプラントの各装置に供給する例です。
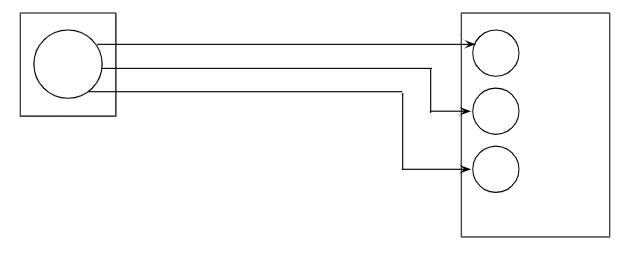
これだけでも3本の配管が必要ですよね。
実際に、屋外タンクにあるタンクはこれ1基ではありませんし、供給先も3基ではありません。
例えば屋外タンクのタンクが10基、供給先が20基あるとしたら、10×20=200本の配管が必要です。
これを配管スタンドでくみ上げるためには、単純に30m程度の幅が必要です。
1本のスタンド幅を2mで考えても15段。。。
非現実的なボリュームです。
共通配管(common pipe)のイメージ
1ライン1用途の原則を真面目に適用したら非現実的になることが分かりました。
そんな非現実的なことはせずに、下の図のようにまとめるのが共通配管のイメージです。
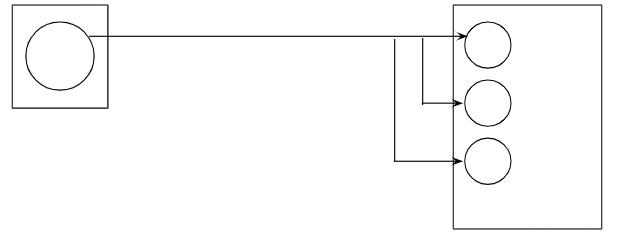
どんな用途に対して共通配管化をするかを具体的に紹介します。
以下の具体例を見て、タンクの数が意外と多いので共通化せざるを得ないということが実感できればOKでしょう。
溶媒配管
溶媒配管の共有化は無意識でも実現できていると思います。
- 溶媒タンクが増えることはめったにない
- タンク内の溶媒の種類が変わることはめったにない
- 溶媒の使用量が増えることはめったにない
溶媒の量も種類も使用量も変わる余地がめったにないので、いったん配管を敷設するとその後に増設する工事をすることはないでしょう。
だからこそ、エンジニアリングにおいて目立ちにくい部分です。
プラント建設時に送る予定が無かったタンクに配管を増やす場合にも、プラント内部でヘッダーを組んでいればヘッダーの増設で対応できます。
このように溶媒を各所に送るヘッダーは、工場の引き込み口でよく見かけます。
流量計とストレーナをヘッダーの前に組むことが多いです。
1か所のヘッダーではなく各階にメイン配管を作りそこから枝分かれする方式もあります。(水道管と同じ)
溶媒受入の流れ
溶媒をプラントに受け入れるまでの流れを少し見てみましょう。
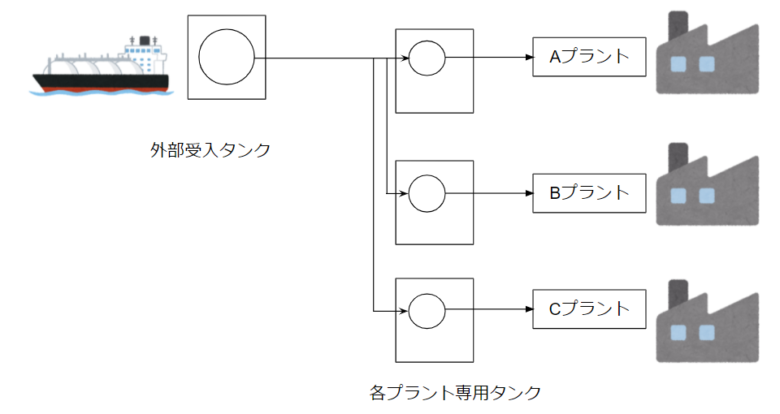
この溶媒を受入タンクという大型タンクに貯留します。
受入タンクが大きいほど、船やローリーの輸送頻度が下がり生産が安定する方向です。
受入タンクから各ユーザーのタンクに各ニーズに応じて溶媒を送ります。
ユーザーは専用タンクから自プラントの生産に使います。
こういう方式を取る工場が多いでしょう。
自プラントの溶媒タンク
自プラントに供給された溶媒は1タンクで完結するでしょうか?
実はちょっと違うことが多いです。
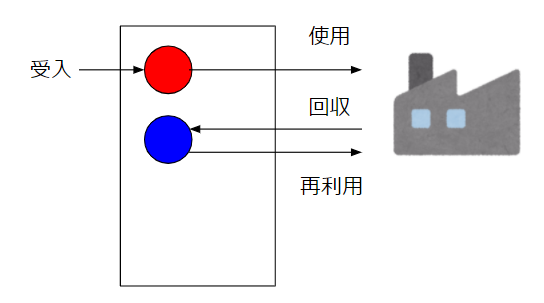
溶媒を受け入れるタンクが必要なのは明らかです。
このタンクからプラントに供給されるのも確か。
でもプラント内で溶媒を回収リサイクルするのは基本的な化学プロセスです。
回収されたタンクを受け入れるために別のタンクを持つでしょう。
こうしないとタンクの液量バランスを取るのが難しい局面が出てきます。
共通受入タンクは限定的
工場の入口で一括して溶媒を受け入れるタンクを付ける方式は実は限定的です。
これは1つの溶媒を大量に扱うという前提があるからです。
イソプロピルアルコールを大量に使うからイソプロピルアルコール受入タンクを持とう、アセトンを大量に使うからアセトン専用タンクを持とう。
こんな発想になります。
でもバッチプラントではそうとも言い切れないケースがあります。
ある製品ではイソプロピルアルコールを溶媒に使いたいけど、別の製品ではトルエンを溶媒に使いたい。
こんなケースです。
でも溶媒タンクの数が限られているので、現実的には実施できません。
自プラントの溶媒タンクはできるだけ専用化したいもの。
生産品目の入れ替えなど大幅な変更がある場合で、溶媒の入れ替えがあったととしてもタンク内の洗浄をする方向で動くでしょう。
タンク内の設備洗浄はとても大変なのできるだけ避けたいもの。
屋外タンクの数が増やせず溶媒の入れ替えができないから、生産品目が増やせなかったり生産スケジュールの変更が難しかったりするのがバッチプラントの悩みの1つです。
廃油排水配管
廃油配管の共有化の工事は頻繁に発生します。油だけでなく水も同じです。
これは社内での廃液処理の方法を見直したり、外部処理などの別の方法を採用するためです。
廃棄物処理の問題は根深い問題があると考えた方が良いです。
そのため、廃油配管を増設するということは「あ・・・、なんかあるのだな」って察した方が良いくらいのもの。
そういう察知のされ方を極力なくすためにも、廃油配管の増設は最小化したいものです。
バッチプラントの廃油配管はプラント内部でヘッダーによって1か所に集めて、プラント外の廃油タンクへ送るようにします。
ヘッダーに繋がる複数の配管から廃油タンクに同時に送ることがなければ、問題ありませんよね。
そういう運転がしやすいバッチプラントではヘッダーで集約するケースが多いです。
プロセス反応で使うポンプの出口にヘッダーを繋げることになるので、別のプロセスタンクから廃油が逆流してくる危険性には注意したいです。
ヘッダーの各所には最低でも逆止弁を付けておきたいですね。できれば自動弁で制御したいところ。
1か所のヘッダーではなくて各階にメイン配管を作りそこに集合させる方式もあります。(トイレと同じ)
廃油排水タンクの貯留
廃油排水タンクはプラント内で発生したものを一時貯留するためのタンクです。
このタンクがないとプラント内に廃油排水が溜まり続けます。
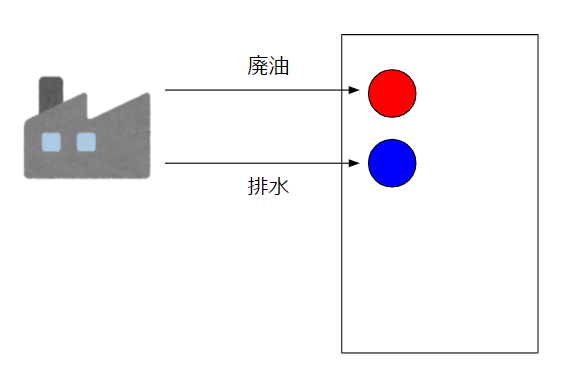
プラント内は液の貯留を許さないのが基本(反応など加工のための場がプラント)なので、貯めるためには専用のタンクが必要です。
このタンクも大きければ大きいほど安定操業に繋がります。
廃油と排水はタンクを絶対に分けます。これは当然。
廃油も排水もそれぞれ一括にまとめるだけでなく、含まれる成分によってタンクを分ける場合があります。
これは特定の廃油や排水が簡単に処理できないなどの都合があるからですね。
そのために廃油排水タンクは複数個確保するのが普通です。
異常時の対応がしやすい
廃油排水配管を供給化するのはなぜ必要なのでしょうか?
答えは異常時の対応です。
- 反応槽2で反応が失敗してドラム缶などに移し替えて処分しないといけない場合
- 反応槽3が故障して臨時的に反応槽3を開放しないといけない場合
- スタートアップやスローダウンで運転とは別のルートで洗浄したい場合
何かしらトラブルが起こる化学プラントでは、異常時に簡単に対応できる仕組みが特に求められます。
建設時には結構スルーされる問題です。
反応の失敗
まず最初に思いつく異常が反応の失敗です。
運転に対して目が行かない機電系エンジニアは、反応が失敗するということについて想像しないパターンが多いです。
ちょっとくらい失敗しても後で取り返しが付く、とでも思っていればまだ良いのですが・・・
生産を数日止めるだけでプロセス途中の物を廃棄するなんてありえない。
なんて思っている人も本当にいます。
実際には、工場の中に山積みになっているドラム缶が反応の失敗による廃棄品かも知れないのに。
反応の失敗として考えられる理由はいくつかありますが、オペミス・計器の指示不良などによる反応系の環境が異常であることが多いです。
バルブの内通やガスケットからの漏れも反応の失敗となりえます。
原料中の異物も反応の失敗となりえます。
こういう失敗が起きた時に、反応槽の中身を抜き出すだけではなく、設備の洗浄をしないといけません。
抜き出した中身が特殊扱いの廃油廃棄物となり、洗浄廃水が特殊扱いの排水廃棄物となります。
これらをどうやって処理するか決まるまでの間、マルチ的に保管できる廃油排水タンクに移送することを考えます。
どの設備で失敗が起きるか分からないので、どこの設備からでも廃油や排水の移送ができるようにしておきたいですね。
装置の故障
反応の失敗と同じように設備が故障した時も、廃油排水問題は起きます。
設備が故障して内部洗浄をして補修しようとする場合、洗浄で発生した廃油は排水は反応の失敗と同じように特殊な処置をしないといけません。
下手をすると、壊れた設備の手前の工程の設備も廃棄しないといけないかも知れませんね。
この辺は、後処理に時間が掛かって、反応が進み過ぎて不純物ができた場合などが該当します。
どの設備が故障するか分からないので、どこの設備からでも廃油や排水の移送ができるようにしておきたいですね。
洗浄ルート
ここでいう洗浄ルートとは、スタートアップやスローダウンで通常の反応ルートとは違うルートでの洗浄を行うことを想定しています。
これは実際にありえます。
通常ルートでは排水を送る予定のない反応槽から、スタートアップやスローダウンでは送る可能性がある。
こんな場合には、フレキシブルチューブなどで仮設配管を引くことが多いでしょう。
仮設配管自体がリスクがあったり手間が掛かったりします。
頻度は少ないですが定期的に発生するので、配管を常設化したいですね。
拡張余地は建設当初から考える
溶媒でも廃油でも、建設して立ち上げが終わった後に改造することが多いのです。
本来は、建設時にちゃんと考えて施工したいものです。
建設段階で共通配管化ができていることが理想。
すべてのタンクに共通配管が引き込まれていると後々楽です。
それがいろいろな理由で難しい場合にも、後で工事が楽になるように対策を取っておきたいですね。
具体的には以下のような対策です。
- ヘッダー方式なら余分なヘッダーを予め作っておいて、バルブで止めておく。
- 水道管やトイレのような枝分かれ方式なら、枝とバルブを予め多く取っておく。
マンションではこんな改造が起きないのは、ユーザーである部屋が最初からちゃんと決まっているから。
化学プラントでは溶媒(マンションの水・ガス)や廃油(洗面台・風呂・トイレ)がそれぞれの部屋についていたりいなかったりする変な環境だ。と認識した方が分かりやすいでしょう。
参考
最後に
化学プラントの共通配管の使い方について解説しました。
溶媒と廃油排水という2種類に分けています。
どちらも入口から出口までのルートを見ていくと、1ライン1用途の原則を守るには数が多すぎることに気が付くでしょう。
改造頻度が多い工場ほど、建設時から拡張余地を考えておきましょう。
化学プラントの設計・保全・運転などの悩みや疑問・質問などご自由にコメント欄に投稿してください。(コメント欄はこの記事の最下部です。)
*いただいたコメント全て拝見し、真剣に回答させていただきます。
コメント