化学プラントのエンジニアにとって、腐食は必須の知識です。
設備を導入しても時間とともに腐食はどんどん進んでいき、そのうち使えなくなります。
この寿命をできるだけ長くすることは、プラントのコスト競争力に効いてきます。
安全安定生産は、プラントの技術者にとって非常に大事なミッションです。
そのため、設備エンジニアは腐食に対する知識を一定量持っておかないといけません。
基本知識としての炭素鋼の腐食は押さえておくべきで、反応式など原則的な部分も知っておいた方が良いです。
実務では応用としての材質試験ばかりが目立ってしまうために、基礎知識が不要と思いがちですが、議論をするうえではやはり必要でしょう。
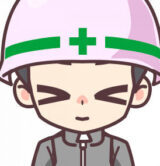
腐食は化学プラントの設備に欠かせない知識です。
腐食反応
金属にとって腐食は避けることができません。
鉄を例にすると、Fe2O3が地球上では安定な状態です。
工場でFeの形に還元して、所定の形に加工して、配管等に使用します。
そのためFeというのは地球上では不安定な状態と言えます。
これが安定なFe2O3の状態に戻ろうとすることは避けられません。
3Fe + 2O2 → Fe3O4
この化学反応式はあまり重要ではありません。
腐食の原理は鉄と水を使って説明することが多いです。
自然界で最もありふれた物どうしで起こる自然現象だからですね。
炭素鋼の淡水下での腐食というカテゴリーになります。
以下の記事が参考になるでしょう。
http://www.trc-center.imr.tohoku.ac.jp/_userdata/mono56_2.pdf
鉄の腐食(酸性)
鉄に限らず、金属の腐食は酸性下で起こりやすいです。
それは下記の反応が起こるからです。
- Fe → Fe2+ + 2e–
- 2H+ + 2e– → H2
この反応式は極めて重要です。
腐食反応は陽極・陰極とか電子の流れとかの要素があるため、ちょっと混乱しますよね。
陰極で鉄が鉄イオンになって、陽極で水素ができる。
なんて反応式を書いて思い出すような方法は私は合いません。
もっとシンプルに考えましょう。
腐食が起こると、鉄が削れる
この当たり前の現象から入ると良いです。
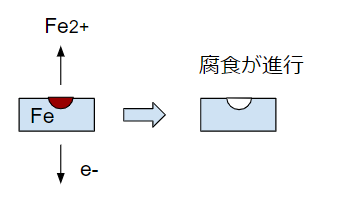
鉄は腐食が起こると鉄イオンになります。
鉄イオンになって水に溶けたり別の化合物になるために、鉄が削れていきます。
鉄はFe2+という陽イオンになります。
ここまで分かれば、Fe → Fe2+ + 2e–という化学式と関連付けることができます。
腐食という電池反応を起こすには、鉄から出た2e–を消費しないといけません。
このために、別の陽イオンが必要です。
酸性溶液下ではH+が過剰に存在しています。
そのH+の存在に釣られるようにして、鉄がイオン化して電子の移動が起こります。
イオン化すると、溶液中の不純物と鉄が反応して、純粋な鉄以外の物質に変化します。
そうして、元の母材である鉄が削られていきます。
こういうメカニズムで考えると、分かりやすくありませんか。
腐食で鉄が削られる量は、溶液中のH+の総量に比例するという当たり前のことが目立つようになります。
H+の量が腐食に影響するため、pHが低い強い酸であるほど、腐食は進行します。
鉄の腐食(中性)
中性の場合を考えましょう。
- Fe → Fe2+ + 2e–
- 1/2O2 + H2O + 2e– → 2OH–
この反応式も重要です。
H+は存在しませんが、O2がその代わりをします。
水中の酸素が腐食の役目を果たします。
水中の酸素は溶存酸素と言います。
水中の溶存酸素量が多い方が、腐食量が多いという事になります。
溶存酸素を意図的にコントロールする場合は、ファンなどでエアーを供給に吹き込みます。
一般の鉄配管で起こる腐食は、子の溶存酸素に起因するケースが多いです。
エアーを供給している訳でもなく、pHが低いわけでもないのに、各所で腐食が起きるのは、溶存酸素の問題です。
鉄の腐食(アルカリ性)
アルカリ性では腐食がほとんど起きません。
というのも、OH–が多いからです。
H+がほぼ存在しない環境で、酸性時と同じ反応は進みません。
中性時の反応でも、O2が電子を受け取って、OH–になる反応です。
溶存酸素がある程度あっても、OH–が多いために、OH–が増える方向の反応が起きずに、逆反応である酸素が増える方向に作用するからです。
だから、苛性ソーダなどでは一般に、鉄配管で使用できると考えられています。
溶存酸素の影響
溶存酸素が多い方が腐食が速く進みます。
溶存酸素はどれくらいの量でしょうか。
ppmという百万分の1のオーダーです。
この世界は機械屋にとってはなじみがないでしょう。
溶存酸素は温度と関係があります。
温度が高いほど溶存酸素量は少なくなります。
例えば25℃での溶存酸素は8.26ppm、0℃だと14ppmくらいです。
25℃の水にエアーを強制的に吹き込むと溶存酸素濃度は上がり、10~15ppmで腐食速度が最大となります。
低温の水で腐食速度が速くなるのは、溶存酸素が上がるからです。
0℃より低い水では鉄の腐食を疑いましょう。
溶存酸素と水に対する処置の相対的な関係を示しましょう。
- 空気を吹き込む:40
- 大気解放する : 9
- 窒素を吹き込む: 1
空気を吹き込むと溶存酸素が上がり、窒素を吹き込むと溶存酸素が下がるという関係性を示しています。
窒素を吹き込むことで腐食性を抑えることができますが、ランニングコストは上がります。
温度の影響
温度が高いほど腐食速度は上がっていきます。
反応速度があがるからですね。
開放系と密閉系と2つの系統を考えます。
開放系は空気が補給される系、密閉系は空気が補給されない系です。
タンクを窒素シールしていると密閉系ですね。大気開放をしていると開放系です。
開放系だと、80℃くらいがピークになり、それより高温になると腐食速度は下がります。
これは、100℃になると水が沸騰するためです。
密閉系では、100℃を越えても水の圧力が上がるだけで沸騰しません。
したがって、温度は高くなるにつれて腐食速度は上がり続けます。
具体的な酸と炭素鋼の腐食
硫酸環境中
炭素鋼の硫酸に対する腐食性について紹介します。
まずは常温について考えます。
濃硫酸
炭素鋼は60%以上くらいの濃硫酸に対しては、腐食速度が低いです。
流速が高い方が腐食速度が速いですが、1〜2m/s程度であれば、10年くらいは持つというデータがあります。
流速10m/sでは1〜2年しか持たないというデータとも読めますが、そんなに高い速度で硫酸を送るケースは、私は経験したことがありません。
希硫酸
硫酸濃度が50%より低いと、腐食速度はかなり高くなります。
濃硫酸の10倍くらい速い速度で腐食します。
高温ではステンレスやハステロイでも持たない
沸騰するくらいの高温硫酸では、 SUS316L やハステロイ系の高級材質でも腐食します。
高温の場合は、硫酸濃度が高い方が腐食しやすいです。
とはいえ、バッチ系では高温の硫酸を扱うケースがほとんどなく、私は扱ったことがありません。
塩酸環境中
私が持っているデータは、沸点近くの塩酸に対する耐食データです。
これもハステロイやチタン等の高級材質でも持たないことを示すだけのデータです。
バッチ系ではこの環境で使うことはほとんどありません。
硝酸環境中
炭素鋼の常温硝酸に対する耐食性はありません。
炭素鋼の常温硫酸に対する腐食速度の約100倍くらいの腐食速度があります。
常温の硫酸なら流速1〜2m/sで10年持つデータを紹介しましたので、常温の硝酸なら0.1年つまり1ヶ月持たないと推測できます。
それだけ腐食速度が高いといことがわかれば十分でしょう。
沸騰した硝酸については、ハステロイやチタン等でも持ちません。
バッチ系ではこの環境で使うことはほとんどありません。
塩濃度
炭素鋼と塩濃度の関係を整理したいと思います。
腐食速度はピークがある
塩濃度に比例して腐食速度は上がっていくイメージがあります。
ところが、一定値でピークを持ちます。
3g/l、つまり0.3wt%程度で腐食速度は最大になるようです。
NaClの水に対する溶解度は、温度にほぼ依存せず、30wt%程度です。
飽和溶解度の1/100くらいでピークを迎えます。
とはいえ、飽和溶解度での腐食速度とピーク時の腐食速度は、1:3程度の割合です。
10倍・100倍のオーダーで変わるわけではありません。
電気伝導度は増えていく
塩濃度が増えると、電気伝導度は当然増えます。
酸素溶解度は下がっていく
塩濃度が増えると、酸素溶解度は減っていきます。
酸素溶解度が減ると、腐食反応に寄与する酸素が減りますので、腐食速度は下がっていきます。
参考
腐食は化学プラントではとても大事です。
複雑な知識を求められそうに思いますが、本記事の内容が分かるだけでもかなり応用ができます。
さらに知識を深めたい場合には以下のような本で学習しましょう。
関連記事
最後に
炭素鋼の腐食についてバッチ系化学プラントで必要な知識を解説しました。
pHと腐食の関係・溶存酸素・温度などの情報と典型例としての硫酸の腐食性を紹介しています。
個別ケースに対する腐食データを取り扱うことが多いですが、基礎となる情報を関連付けができるようになりたいですね。
化学プラントの設計・保全・運転などの悩みや疑問・質問などご自由にコメント欄に投稿してください。(コメント欄はこの記事の最下部です。)
*いただいたコメント全て拝見し、真剣に回答させていただきます。
コメント