ボイラーは工場やプラントで蒸気を作り出す重要な設備です。しかし、その運転には安全性と効率性を確保するための基本的な知識と適切な操作が欠かせません。本記事では、ボイラー運転の基本的な流れや注意点を初心者でも理解しやすいように解説し、安全で安定した運転を目指すポイントをご紹介します。
ボイラー試験の範囲内で、ボイラーの運転取扱いに関する一般的な知識を紹介します。現場での運転管理という意味ではなく、その前後の部分に関する設備面での保護に関する知識です。実際の運転管理は現場ごとに変わりますが、準備立ち上げや片付け保全の部分は、設備に共通しているから試験で問いやすいです。
こういう発想はボイラーだけに限らず、いろいろな資格試験で同じでしょう。
ボイラー運転と取扱い
2級ボイラー技士の範囲内で、ボイラー運転や取扱いに関して解説します。
準備 → 点火 → 圧力上昇 → 運転中
という4段階に分けます。
準備
準備段階は、運転の実務では非常に大事です。
チェックリストを使って、各項目が漏れなく準備できているか点検します。
化学プラントでも、設備の運転開始前にチェックリストを仕上げます。
40人くらいの人間が、数日にわたり、交代しながら…
このチェックリストは設備によってまちまちです。
ボイラーでもチェックリストは大事ですが、試験で問いにくいです。
というのも「問題ないこと」「正常であること」を確認するというのが、準備だからです。
点火
点火時は非常に注意が必定です。
点火前と点火後で、ボイラーの状況が大きく変わります。
点火時に起こりえる大きなトラブルとして、「爆発」があります。
爆発に対して何をチェックするか、という目線で見てみましょう。
- 水がない
- 炉内に空気がない
- 燃料が多すぎる
点火時に注意する項目は色々ありますが、シンプルに「水」「空気」「燃料」という3要素で見ると分かりやすいです。
水
ボイラーに水がないと、空焚きになります。
点火前から水位計で確認することが可能であり、点火時に特に注意を払う部分ではありません。
空気
点火作業の最初は、ボイラーの炉内を空気で置換します。
空気で置換しなければ、前の運転で残っていた燃料や不純物が残っている可能性があります。
この状態で、急に火をつけると、間違ったら爆発するかも知れいません。
火をつける前に、ニュートラルの状態に戻す。
この意味で、空気置換をします。
空気ファンを起動 → ダンパをセット → 炉内通風圧を確認
空気系統が適正な状態に移行したことを確認します。
燃料
空気が適正であれば、次は燃料です。
燃料が適正にバーナーから噴出されないと、点火はされません。
燃料ポンプを起動 → 燃料配管の圧力を確認 → 燃料を予熱 → 火種を付ける→ 燃料弁を開く → 点火
燃料も空気と同じように燃料系統のチェックをします。
ボイラーに特有なのが、予熱でしょう。
燃料の予熱が適正でないと、燃料の粘度が高いので
バーナーから噴霧されません。
バーナーから噴霧が適正にされないと、安定した燃焼ができません。
点火火種を先に付けてから、燃料を投入します。
逆にすると、燃料が炉内に過剰にある状態で点火をしてしまうため、
爆発をする方向に作用します。
圧力上昇
点火ができても、圧力上昇中は注意が必要です。
ボイラーの状態が変化していくからです。
ボイラーの状態とは「圧力」「温度」という認識でOK。
- 燃焼量を急に増やさない
- 温度による膨張の影響をチェック
- 圧力の上昇による漏れの有無をチェック
熱・温度・圧力というファクターに着目すると分かりやすい。
熱を加え、温度が上がり膨張していき、圧力が増えて漏れが起こる
これが圧力上昇中に起こる大きな問題です。
圧力上昇時の取扱は以下のとおりです。
蒸気が発生 → 空気抜き弁を閉める → 増し締め → 圧力監視 → 燃焼量調整 → 水位の監視 → 蒸気吹出
点火をして蒸気が発生しだしたときは、水管内には過剰な空気が残っています。
これを蒸気とともにパージするという発想です。
蒸気が出てくれば、点火も水も適正であることが確認できます。
蒸気が無事に出てきて、空気抜き弁を閉めると、蒸気圧力は上がっていきます。
圧力が上がっていくと増し締め確認をします。
漏れが起こらないとそのまま圧力を監視します。
条件によっては、安定状態への移行のために、燃焼量の調整が必要でしょう。
蒸気を放出するために、水管の温度圧力が上昇していくと、
水も膨張していき、水位計が振れていきます。
落ち着いてきて、問題のない水位になるまで監視します。
ここまで来れば、蒸気をユーザーに放出し始めます。
運転中
運転中はボイラーの状態監視が中心です。
- 水
- 蒸気
- 空気
- 燃料
この4つが中心です。
これは連続プラントの安全安定運転状態と同じ。
- 水位が適正であるか(低すぎないか)
- 水の流量が適正であるか
- 給水ポンプの電流が適正であるか
- 蒸気の圧力が適正であるか
- ファンの電流が適正であるか
- ダンパの開度が適正であるか
- 燃料ポンプの電流が適正であるか
- 燃料流量が適正であるか
全部、「適正であるか」を監視するフェーズです。
水・蒸気・空気・燃料という各系統の計器が適正であることを監視します。
忘れてはいけないのが、スートブロー。
一定期間ごとに、伝熱面のすす掃除が必要です。
実務的には時間で縛って、定期掃除をします。
本当の意味で、実務的には燃料や水も、貯蔵タンクに定期的に供給しないといけません。
原料管理と同じように、廃棄物としての「すす」管理も大事です。
原料や廃棄物という見方ができれば、運転管理のイメージがしやすいでしょう。
ボイラーの異常
2級ボイラー技士のボイラー運転の異常について解説します。
ボイラー水位
ボイラー水位の異常は「低水位」側が多いです。
低水位の異常が出てくる理由は大きく3つです。
- 流入側の異常
- 流出側の異常
- 計器の異常
水位が低いのだから、流入側が少ないか流出側が多いかという発想は
ボイラーの運転やプラントの運転でごく当たり前に使う発想です。
機電系エンジニアは運転に関わることが少ないので、気が付きにくいかもしれませんね。
流入側が少ないということは、ポンプが弱くなっている・配管が詰まっているなどの原因が思いつくでしょう。
流出側が多いということは、燃焼量が高い・蒸気使用量が多すぎるなどの原因が思いつくでしょう。
流入側と流出側の系統を丁寧に見ていく作業になります。
低水位を判断するために計器を使う以上、計器側の異常も視野に入れていないといけません。
キャリーオーバー
キャリーオーバーは蒸気中に水が混入する現象です。
プライミング(水気立ち)やホーミング(泡立ち)などの分類があります。
蒸気中に水が含まれるのは、
- ボイラーの水位が多い
- 蒸気負荷が高いなど
の原因が挙げられます。
水が多いから蒸気に水が混入しますし、蒸気を多く生成するほど水が混じる可能性は高くなります。
蒸気発生量が多いほど、均一な蒸気生成ができなくなるので、局所的に水が残る可能性があるからです。
キャリーオーバーとして蒸気に水が含まれていると、ボイラーにとって以下の影響が出ます。
- 蒸気純度が下がる
- 安全弁・計器・配管などに水が入り詰まる
- 水位計が振れて、水位が異常に上がったor異常に下がったとして制御が掛かる
蒸気純度が下がることの影響
蒸気純度が下がるというのは、過熱度に影響を与えます。
過熱度が下がる方向なので、空気予熱や燃料予熱などに影響が出て、ボイラー燃焼量が下がる方向に動きます。
蒸気の負荷が高いことによるキャリーオーバーなら、過熱度が下がることによって、適正な方向に動こうとします。
高水位によるキャリーオーバーなら、水を減らそうという方向に動きはしないので、注意が必要です。
過剰な水が流入していないか確認しないと、水がどんどん増えていき、キャリーオーバーが進展し続けます。
詰まりによる影響
水が存在することで、安全弁・計器・配管などが詰まることがあります。
ボイラーの水には、純度の高い水を使いますが、不純物をゼロにすることはできません。
蒸気として放出される部分には、不純物が存在しません。
不純物が存在するのは、ボイラー内部の水が存在する部分。
ここで発生した不純物を定期的に清掃することで、運転管理をします。
その不純物が想定されていないエリアである、安全弁・計器・配管に侵入して包まってしまうと、大問題です。
計器の異常
キャリーオーバーによって水位が振れることで、計器の自動制御に異常を与えます。
自動制御が暴れます。
ボイラーを動かすべきなのに止まってしまったり、止めるべきなのに動き続けたり…。
怖いですね。
燃焼ガス漏れ・油漏れ
燃焼ガス漏れ・油漏れは、設備に明らかな破損が起きている以上です。
火災爆発やエネルギー損失・熱損失・設備の破損などの問題が起きます。
燃焼系統の問題
二次燃焼
二次燃焼は、燃料の不完全燃焼部分が、煙道内で燃えることです。
予想していない部分で燃焼するために、設備を破損する恐れがあります。
逆火(バックファイア)
逆火は火炎が炉外に吹き出る現象です。
運転中というよりは、点火の時に起こりやすいです。
- 炉内の圧力が高い
- 空気より先に燃料を入れた
- 点火時に着火遅れが起こった
炉内の圧力が高いことは、例えば煙道のダンパ開度が不足しているなどの原因が考えられます。
炭化物(カーボン)・火花
炭化物は燃料バーナーに付着する可能性があります。
これも分かりやすい異常ですね。
燃料が燃えないので、ボイラーの蒸気が出ません。
炭化物が生成する原因は以下のとおりです。
- 油噴射角度の異常
- 油圧・油温の異常
- バーナーチップの損傷
燃焼が適正に行われているかどうかを監視するために、
燃焼の光を監視したり、蒸気や水の各種計器を監視します。
火炎中に火花が生じることもあります。
これも炭化物と同じように、燃焼系統の問題です。
ボイラーの停止
2級ボイラー技士のボイラー運転の停止について解説します。
ボイラーの停止手順は一般に以下のとおりです。
燃料の停止 → 空気置換 → 給水停止 → 蒸気弁閉 → ダンパ閉
それぞれの工程について解説します。
燃料の停止
まずは燃料の停止工程です。
前提として、ユーザーが蒸気を使わないことを確認します。
ユーザーが蒸気を使わないことが分かったら、ボイラーから発生する蒸気を止めに入ります。
最初に燃料を止めます。
燃料を止めると、火が止まります。
当然ですよね。
ボイラーは「水」「燃料」「空気」の3つがありますが、このどれから順番に止めるかという視点で見るといいでしょう。
空気置換
燃料を止めた後、すぐに「水」「蒸気」を止めるわけではありません。
空気置換も立派な工程。
燃料を燃やす場所である火炉には、燃焼ガスが充満しています。
不完全燃焼の燃料も含まれています。
これを除去するために、一定期間の空気置換を行います。
燃料を止めて空気を送り続ける
やっていることはこれだけですが、その意味するところは重要です。
化学プラントでいうところの運転前の窒素置換や入槽前の空気置換と全く同じです。
給水停止
燃料を止めて、空気置換を行うと、燃料系統は安全な状態になりました。
次に止めるのが「水」です。
火炉は急に温度が下がるわけではありません。
燃料と空気を止めて熱源を取り除いても、顕熱としてレンガなど構造物自体が熱を持っています。
これを冷やす意味でも「水」があります。
運転時の水位よりも高い位置まで給水しておき、ボイラーの顕熱分を吸収する冷却源として使います。
張り止めと呼んだりします。
張り止めが終わると、給水を止めます。
ポンプを止めて、弁を閉めます。
蒸気弁閉
給水が終わると、蒸気弁を閉めます。
蒸気をユーザーに送らないようにします。
給水を止めて、ボイラーの顕熱も無くなり、蒸気が発生し無くなることを確認します。
蒸気が出なくなったことを確認して蒸気弁を占めます。
と同時にドレン弁を開きます。
蒸気が出なくなっても、蒸気配管中には蒸気は残っていて、蒸気配管自体も顕熱を持っています。
これが空気で冷やされてドレンができます。
このドレンを取り除くためにドレン弁を開けます。
これで蒸気系統も安全な状態になります。
ダンパ閉
「燃料」「蒸気」の系統が安全になって、「水」を止めているので、最後はそう。
「空気」です。
空気の系統を止めるために、ブロアーを止めてダンパを閉めます。
附属品の取り扱い
本体よりも附属品の方が取り扱いに注意する必要があります。
これはボイラーに限らず、化学プラントの設備でも同じ。
設備本体は安定状態に入れば、監視だけですむことが多いです。
一方で附属品は、監視以外にも操作や点検などの作業が入ります。
ということは、附属品については運転上の注意点が課題。
圧力計
圧力計は、意外と細かいルールがあります。
- レンジは最高使用圧力の1.5倍~3倍
- 最高使用圧力や常用圧力の範囲を色分けして表示
- 80℃以上ならサイフォン管を付ける
- 圧力計の予備を確保する
レンジや色分けは、各ユーザー会社のルールとして設定している場合もあるでしょう。
私が働く会社でも、レンジ設定はこのルールです。
バッチ系化学プラントでは色分けは独自に行っています。
圧力計手配時にメーカーに色を付けてもらうのでは?
と思うのは連続工場の発想。
バッチ系化学プラントでは、複数の用途に同じラインを使います。
物性が変わると同じポンプでも圧力が変わるので、常用圧力を固定することができません。
各ユーザーで運転時の常用圧力を現場で確認して、ペンでマーキングするのが現実的です。
サイフォン管はメーカーに使用条件を提示すると、付けてくれることが多いです。
圧力計の予備は、2つの意味があります。
「不具合時の点検交換用」「試験メンテ時の取替用」
いずれにしても、予備の圧力計を完備しておくことは、運転上大事なことです。
ボイラーだけに限りません。
水面計
水面計は以下のルールがあります。
- 水面計は2個1セット
- 機能試験を毎日行う
水面計はボイラーに限定したルールですが、興味深いルールがあります。
というのも、最近の化学プラントでは水面計はほとんど使わないので…。
水面計は2個セットで使うのは、1個では信頼性が無いから。
2個の水面計にズレが生じていないかを確認します。
ズレが起きていると、少なくともどちらかの水面計が故障しています。
故障というか、詰まりの方が正しいでしょう。
毎日機能試験をするのもそのためです。
ガラス管内の液をブロー → 水側のブロー → 蒸気側のブロー → ガラス管内に液満たし
この流れで行います。
水側を先にブローして蒸気側を後にブローするのは、系統分けやブロー効率などの意味があります。
どちらでも結果が同じだから、順番を気にしないで良いだろう
と安易に考えずに、どちらがbetterかということを考えましょう。
安全弁
安全弁は極めて重要な附属品なので、ルールも厳しめです。
- 性能検査時は分解整備をする
- 安全弁の吹出し圧力を、圧力計で確認する
安全弁の点検整備は専門的な技能が必要なので、自社で整備せずに専門業者に委託する場合も多いでしょう。
ルールとしては完結ですが、
重要なので怪しいと思ったらすぐに点検!
というスタンスで良いと思います。
安全弁は特にバネ式が多く、詰まりが避けられないので、蒸気漏れが起こる可能性は常に残っています。
安全弁だから安全であり故障しないというわけではありませんので、取り扱いが大事ですよ。
吹出し装置
吹出し装置のルールは以下のとおり。
- 1日に1回吹出し
- 水面計を見ながら吹出し
- 吹出し作業は専任で行う
吹出しをするのは、ボイラー中のスケールやスラッジを排出するため。
これがあるとボイラーの伝熱性能が低下するだけでなく、詰まってしまい機能不全に陥る可能性があるからです。
試験には教科書的なアナログな操作方法が載っていますが、現在では自動ブローが一般的です。
- 吹き出し弁が2重弁であること
- 急開弁を先に開けて、漸開弁を後で開ける(閉める場合はその逆)
この辺りの思考は、化学プラントの普通の配管ラインでも使える発送です。
給水装置
給水装置はボイラーに限らす、水系統の点検として一般的なものです。
- 給水タンク
- 給水ポンプ
- バルブ・圧力計
化学プラントでも同じ発想で取り扱いをしますね。
自動制御装置
自動制御装置として色々あります。
- 圧力調整器
- 温度調整器
- 燃料調整器
- 水位調整器
- 燃料安全装置
- 点火装置
この中で特徴的なのは、燃料調整器・燃料安全装置・点火装置でしょう。
これらの附属品は、機械設備というよりも電気制御設備です。
点検内容も制御回路が中心です。
運転員や機械エンジニアにはなじみがない、というか関われる部分が少ないでしょう。
安全弁と同じで専門の知識が必要です。
ボイラー(boiler)の洗浄
2級ボイラー技士のボイラー洗浄方法について解説します
機械的洗浄
機械的洗浄とはすべての基本です。
工具を使って手作業で行う洗浄方法です。
機械的洗浄は他の線場が終わった後の最終手段として行います。
- 手間が掛かる
- 装置の中に入るため危険
- 洗浄結果を分析できる
機械的洗浄はできれば避けたいところですが、普通は必ず行います。
手作業による洗浄は信頼感が抜群。
その代わり、作業が非常に大変です。
お風呂の掃除などを考えればイメージしやすいでしょう。
ボイラーではハンマー・やすり・ワイヤーブラシなどを使います。
管の洗浄のためにチューブクリーナーを使うこともあります。
電機が多いですが、水圧や空気圧も存在します。
また、化学プラントの設備では、洗剤とスポンジが多いでしょう。
酸洗浄
酸洗浄は、酸を薬液に使って洗浄する方法です。
酸を使うと、意図的に鉄を腐食をさせる方向です。
スケールのように腐食しきった鉄さびを、駄目押しで腐食させて
鉄管から浮かせて洗い落とすという方法です。
酸洗浄を行ったままだと、酸が系内に残るので、かえって腐食が進行します。
そこで腐食抑制剤(インヒビター)を追加します。
これはボイラーのメンテナンスマンにお任せするでしょう。
なお、化学プラントでは設備に対して酸洗浄をすることはあまりありません。
酸で腐食する設備が多いですからね^^
腐食をさせて寿命を縮めたくありません。
酸洗浄というと、ステンレスの設備や配管を製作したときに、溶接のひずみ除去として使用することが多いでしょう。
アルカリ洗浄
アルカリ洗浄は、アルカリを薬液に使って洗浄する方法です。
アルカリ洗浄は苛性ソーダを使います。
苛性ソーダに油を溶かすという狙い。
油は酸側に偏っている場合が多く、苛性ソーダで溶ける可能性があります。
油が残っているのは、ボイラー新作時。
製作時に使った油が系内に残っている可能性があります。
当然ながら異物としてボイラーの性能を悪化させる方向です。
これを苛性ソーダで除去するのがアルカリ洗浄。
苛性ソーダに対する油の溶解度で決まりますので、苛性ソーダは温めて使います。
化学プラントでもこの発想で洗浄するケースはあります。
グラスライニング設備では苛性の温度を上げることは、腐食を促進しますので注意が必要。
アルカリ洗浄をしないで別の方法で洗浄するケースもあります。
ボイラーの保存
2級ボイラー技士のボイラー保存方法について解説します。
乾燥保存と満水保存の2パターンがあります。
乾燥保存
乾燥保存は言葉どおりボイラー内を乾燥させます。
腐食が起こるのは水があるから
これはボイラーに限らず一般的に言えます。
ボイラーの停止期間が長い時は、水を徹底して取り除きます。
- 水をパージ
- 空気で置換
- (できれば)窒素で置換
- 遮断板で確実に閉止
- 吸湿剤を設置
- 吸湿剤を定期交換
ここまで徹底すればかなりの腐食は防げます。
水を抜いて蓋をして終わり!というわけではないことがポイントですね。
化学屋さんなら空気置換や窒素置換に目が行きますが、設備エンジニアはここに気が付かない人が多いです。
吸湿剤はボイラーに特有でしょう。
そう思っていたら、身近にあるじゃないですか。
お菓子
お菓子にも吸湿剤入っていますよね。あの感覚ですよ。
満水保存
満水保存は乾燥させずに、真逆に水で満たします。
停止期間が数か月程度の短い場合に使います。
乾燥保存は吸湿剤の点検交換が面倒ですからね…。
水が存在すると悪さをする環境で、水満たしをするのは若干奇妙に感じるでしょうか。
満水保存の手順は以下のとおりです。
- 腐食防止剤の入った水を生成する
- 腐食防止剤の入った水をボイラーに注入して満液にする。
- 水を定期的にサンプリング、分析をする。
- 薬剤濃度に異常があれば薬剤の追加注入。
- 鉄濃度に異常があれば、ブロー後に再水張
水に腐食防止剤を入れることがポイント。
こちらも定期点検は必要です。
薬剤の量が少なければ腐食が進行するはずです。
分析で気が付くくらいの初期段階では、薬剤を追加すればいいでしょう。
もっと後になって気が付く場合は、鉄濃度が増える形で露見します。
この場合は追加薬剤を投入せずにいったん全量パージします。
小手先の薬剤追加では対応できないという意味ですね。
ボイラー水に関する用語
ボイラー水の用語について整理します。
ボイラーの水を管理することは、ボイラーの運転管理でも非常に重要です。
このボイラー水の関してまずは用語から見ていきましょう。
pH
pHはボイラー水に限らず、水系で重要な指標です。
当然ながら化学プラントでも極めて大事。
硬度
硬度はカルシウムイオンやマグネシウムイオンの濃度を示します。
全硬度というカルシウムイオンとマグネシウムイオンの量を、炭酸カルシウムに換算したものが、一般的。
mg/lの単位で示すことが多いです。
ppmで表記されることもありますが、mg/lと同じ感覚で使えます。
mg/l → mg/1000g → 10-6 → ppm
この関係性は、化学プラントの機電系エンジニアにはなじみがないでしょう。
酸消費量
酸消費量は水中に含まれる、水酸化物・炭酸塩・炭酸水素塩などのアルカリ分を示します。
溶存気体
水には酸素や二酸化炭素が溶けています。
これを溶存気体として区分します。
蒸発残留物
気体以外に水に含まれているものというと、固体ですね。
水に溶けるものと溶けないものに分かれます。
溶解性蒸発残留物
溶解性蒸発残留物は言葉どおり、水に溶けるものです。
カルシウム・マグネシウム・ナトリウムなどの化合物です。
懸濁物
懸濁物は、水に溶けないものです。
泥、砂、有機微生物などです。
私はシリカなどもここに含んで解釈しています。
不純物の除去
ボイラーの運転にとって邪魔ものである不純物。
この除去方法を整理します。
溶存気体
溶存気体を取り除くことを脱気といいます。
主に3種類あります。
- 加熱脱気 … 水の温度が高い方が、気体の水に対する溶解度が低い
- 真空脱気 … 気体の圧力が低い方が、気体の水に対する溶解度が低い
- 膜脱気 … 高分子膜を境に真空引きをして、気体を強制除去する
気体の水に対する溶解度と、高分子膜という便利な設備の2パターンですね。
蒸発残留物
蒸発残留物の除去は、溶解性蒸発残留物と懸濁物に分けて考えます
溶解性蒸発残留物
水に溶けているものを強制的に取り除くには、イオン交換法がメジャーです。
イオン交換法でも、単純軟化・脱炭酸塩軟化・イオン交換水の3方法がありますが、
単純軟化がメジャーです。
軟化と呼んでいるのは硬水の硬度を下げるから。
化学工学的には吸着です。
吸着に適したイオン交換樹脂を充填した吸着塔にセットして、水をフィードするだけ。
こう考えると、化学プラントの機電系エンジニアは理解しやすいでしょう。
懸濁物
懸濁物の除去は自然沈降・凝集沈殿・ろ過があります。
これも化学プラントの機電系エンジニアにとってはメジャーですね。
自然沈降や凝集沈殿は排水処理で良く出てくる方法です。
ろ過は単体で行わずに、自然沈降や凝集沈殿で発生した沈殿物の捕集目的で使うことが多いでしょう。
ボイラー水の管理
ボイラー水管理上は、清缶剤・ブローがポイントとなります。
清缶剤
清缶剤は水に加えることで、色々な機能を果たします。
- pHの調整
- 硬度の低下
- 懸濁物分散
- 脱気
pH・硬度・懸濁物・脱気などこれまでに上げた項目に対して、器用に防止してくれます。
ボイラーに適した清缶剤を適宜投入するのが、運転管理上は大事です。
ブロー
清缶剤を添加しても、問題の先送りにしかなりません。
完全に除去できない不純物はボイラー内に溜まり続けます。
そのため、水を排出しないといけません。
完結ブローと連続ブローがあります。
ブローした水は別途排水処理をします。
化学プラントでは冷水塔も同じ発想。
連続プラントなら日常的にブローを行いますが、
バッチプラントだとブローという表現ははじみが薄いと思います。
連続稼働している設備として除害装置くらいしかありませんからね。
ボイラー燃料の特徴
ボイラー燃料の特徴をさっそく紹介しましょう。
燃料として3つに分けることができます。
固体・液体・気体です。
物質の三態そのもの。理科の授業を思い出しますね。
固体燃料
固体燃料は簡単に言うと「石炭」です。
木を燃やしたら熱が出るという古典的なお話と大差ありません。
石炭を燃やして熱を発生させ、その熱で蒸気を作ります。
原始的ですよね。
メリットは自然中に大量に保存されていること。
この石炭、炭素100%かと思いがちですが、実は不純物がいっぱい含まれています。
- 水分
- 揮発分
- 配分
- 硫黄分
これはボイラーにとってはデメリット。
不純物がボイラーの安定運転の阻害要因になります。
石炭発電が残り続けるのと同じ理由です。
液体燃料
液体燃料とは簡単にいうと「油」です。
油を使うメリットは以下のとおり
- 品質が安定
- 物流が楽
- 取扱いが楽
個別に解説します。
デメリットは産油国が限られているという点でしょう。
品質が安定
油の品質が安定しているのは、蒸留をしているからですよね。
液体だから均一に混ぜた状態で品質分析をでき、安定した品質が得られます。
石炭だとサンプリング箇所によって品質はずれそうですよね。
混ぜて均一条件にすることもできません。
油は石炭よりも変質が少ないです。
タンクに密閉できますからね。
石炭だと表面は空気中に晒されていて、時間が経つほど変質します。
安定した状態の原料は、安定したボイラー出力を得るときに大きなメリットです。
物流が楽
油は石炭に比べて、物流が楽です。
液体ですからポンプと配管で輸送できます。
タンクがあれば貯蔵も可能。計量も容易です。
物流面でメリットが非常に大きいです。
取扱いが楽
物流が楽というのと同じような意味ですね。
液体だと漏れても飛散しにくく、装置で詰まることも少なく、圧力が変動するわけでもなく、空気中に飛び散りもしません。
液体が固体や気体に比べて優れている点ですね。
気体燃料
気体燃料はメタン・水素・一酸化炭素などを混ぜたものです。
メリットとして以下が挙げられます。
クリーン
ほぼこれだけです。でもこれはボイラーの安定運転には非常に大きなメリット。
このメリットのために、最近のボイラーはガスを使うケースが増えています。
逆にデメリットの方が大きいですので、それを紹介します。
装置が大きい
気体を扱う装置は必ず大きくなります。
液体の方が気体よりも密度が高いですから、装置は普通は小さくなります。
この装置の大小が、コストにそのまま跳ね上がります。
火災爆発のリスクが高い
気体燃料は漏れると火災爆発につながりかねないです。
気体であるから漏れが検知しにくい。
空気と接触して爆発性雰囲気を形成しやすい。
液体に比べても火災爆発のリスクは高いです。
液体燃料の燃焼方式
ボイラーの液体燃料を使う場合の燃焼方式を説明します。
液体燃料の燃焼方式は、化学プラントの機電系エンジニアでも理解しやすいです。
液体を扱う以上は、油でも化学プラントの薬液でも同じですからね。
液体燃料のフロー
液体燃料のフローについて説明します。
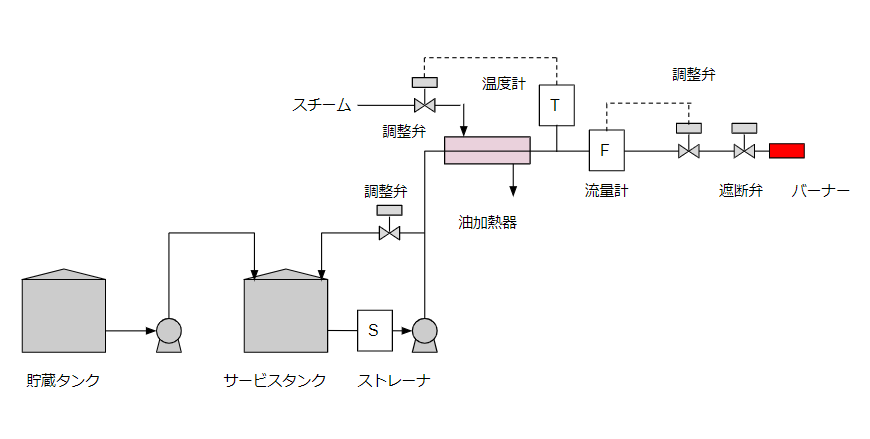
タンク
タンクは貯蔵タンクとサービスタンクに分けます。
貯蔵タンクはローリーなどで外部から運搬された油を貯める場所です。
ここがボイラーの油を溜め込む原料保管庫になります。
貯蔵タンクとは別にサービスタンクを持つことが普通です。
サービスタンクは使用バーナーの運転条件が変動したときに対応できるようにするためのタンクです。
貯蔵タンク1つあれば、バーナーに液が送れそうに見えますが、
バッファタンクがあると何かと便利です。
これは化学プラント内の原料貯蔵タンクと同じ発想です。
フィードライン
サービスタンクからバーナーまでのフィードラインを確認しましょう。
ポンプ
バーナーに油を送るためにはポンプを使います。
このポンプ保護のために、サクションラインにストレーナを付けます。
フロー上は1個しかストレーナを付けていませんが、普通は2個並列に付けます。
常時片側のみを使い、詰まりが大きくなってきたら切り替えるという方法です。
ポンプ出口にサービスタンクへの循環ラインを付けます。
ポンプの圧力調整用に循環ラインに調整弁を付けるケースがあります。
加熱器
加熱器は油の温度を上げて粘度を下げることで、バーナーで適切に噴霧させるために必要です。
装置型式としては熱交換器タイプが一般的。
加熱方式は蒸気や電機が考えられますが、起動時は電気で温めて、安定運転時は蒸気で温めることが多いです。
起動時は蒸気が発生していませんからね^^
フロー上は蒸気で温めるケースを考えています。
加熱器出口の油の温度を監視して、温度が一定になるように蒸気量を制御します。
流量調整
バーナーにフィードする油の量を調整する機能が必要です。
これはボイラーで発生させる蒸気量に連動します。
流量計と調整弁で組み合わせます。
流量計は加熱器の出口に付ける方が良いです。
加熱器で粘度が下がった油の方が、トラブルが少ないですからね。
調整弁の出口に遮断弁を付けます。
調整弁では漏れを完全に遮断できないので、緊急遮断目的で自動遮断弁を付けます。
バーナー
バーナーはボイラーでもかなり重要な部分です。
ボイラーの中でも非常に特殊な部分。
バーナーは大きく4つの方式に分かれます。
圧力噴霧
圧力噴霧はもっとも単純な方法です。
ポンプで昇圧した油をそのまま噴霧する方法です。
単純に油をそのまま放つだけシンプルな構造と
一部の油をサービスタンクに戻す構造の2パターンがあります。
循環させながら一部の油をバーナーから放出する方が、噴霧圧力を安定させやすいです。
これがバーナーの負荷調整範囲を広げることに繋がります。
これも化学プラントで一般的に取られる方法です。
蒸気噴射
蒸気噴射は、油と蒸気を同時にバーナーに噴霧する方法です。
油と蒸気を混ぜる部分が先にあって、混ざった燃料がバーナーから放出されます。
蒸気の力で油を微細化することで、均一に噴霧しやすくすることが狙い。
これでバーナーの火炎が安定します。
気流噴霧
気流噴霧は、油と空気と同時にバーナーに噴霧する方法です。
蒸気ではなく空気を使うのがポイント。
回転式
回転式は油をバーナーの遠心力で微細化する方法です。
バーナーの先端にカップを付けて、油をカップの内面に貼り付けます。
油膜が遠心力で徐々に微細化されます。
中小型ボイラー用です。
気体燃料の燃焼方式
ボイラーの気体燃料の燃焼方式について紹介します。
燃焼方法は2つ
気体燃料の燃焼方法は2つあります。
拡散燃焼方式と予混合燃焼方式です。
ガスと空気をどこで混合させるか、という違いですね。
拡散燃焼方式
拡散燃焼方式は空気とガスが別々にバーナーに投入されます。
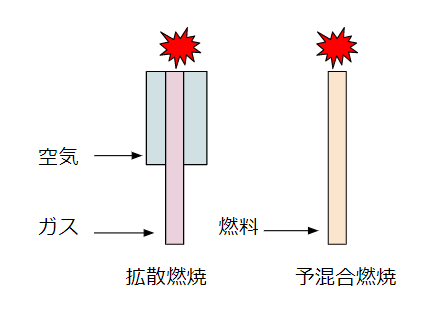
バーナー内で可燃性混合気が形成されないので、逆火の危険性がありません。
空気の流量・ガスの噴射角度などで火炎の広がり・長さ・温度分布をコントロール可能です。
安全で自由度が高いため、使用頻度は高いです。
ガスバーナーの形はいくつかの種類があります。
- センタータイプ ・・・ ガスパイプ1本から直射
- リングタイプ ・・・ ガスリングから円周上に放射
- マルチスパッド ・・・ ガスパイプ数本から直射
- ガンタイプ ・・・ 制御ユニットを組み込み
ガンタイプは制御ユニットを組み込んだ最新式です。
バーナー・ファン・点火装置・火炎検出器など、安全装置や制御装置を組み込んでいます。
残りのタイプは、ガスの吹込み方法を物理的に数パターンに分割しただけです。
予混合燃焼方式
予混合方式は言葉どおりあらかじめ混合した方式です。
空気とガスを混合した状態でバーナーに投入します。
あらかじめ混合した燃料を使うので、安定した火炎を作れます。
逆火の危険があるので大容量のバーナーには使わず、パイロットバーナーとして使うことがあります。
ガスは都市ガス・LPG
燃料の1つであるガスは、都市ガスとLPGがあります。
都市ガスは天然ガスのこと。
ガス会社が都市ガス配管を施工してくれます。
大容量のボイラーはほとんど都市ガスです。
LPGはボンベや貯蔵タンクに貯めておいて、配管でボイラーまで輸送します。
固体燃料の燃焼方式
ボイラーの固体燃料の燃焼方式について紹介します。
燃焼方法は3つ
固体の燃焼方法は3つあり、火格子・微粉炭バーナー・流動層があります。
固体燃料がどういうポジションにあるか、というのが違いです。
気体燃料の拡散・予混合というのと考え方は似ています。
火格子
火格子は固体燃料は床に設置されています。
固体燃料が燃焼室に置いてあり、空気を投入して、燃焼させます。
暖炉やキャンプで木を燃やすイメージで十分です。
木を燃やすのとは、燃料や装置がかなり専門的というだけです。
燃料が床に置いてある、という点がポイントです。
微粉炭バーナー
微粉炭バーナーは、微粉炭上にした石炭を空気ともにボイラーに送る方式です
微粉炭だから空気と一緒に同伴されます。
気体燃料の予混合燃焼方式と似た発想です。
メリットとしては
- 接触面積が高く燃焼効率が高い
- 使用可能な石炭の種類が多い
- 燃焼の負荷変動に対応しやすい
というように、運転における経済的なメリットが強いです。
逆にデメリットは
- 設備費、動力費が高い
- 爆発の恐れがある
というように、設備や保安面でのデメリットが強いです。
石炭を空気と一緒に送るための送気装置が大きくなったり、火格子よりも大きな燃焼室が必要だったりと、コストは掛かります。
予混合方式のように燃料が混合されているので、送気ライン中でも燃焼する可能性があります。
流動層
流動層は、火格子と微粉炭バーナーを重ね合わせたような方式です。
火格子内で燃料を浮かせる方式です。
火格子燃焼方式では燃焼室内の大量の固体燃料に対して、少量の空気を送ります。
流動層燃焼方式では燃焼室内の固体燃料が少ないため、空気の流れの力を受けて固体燃料が浮き上がります。
そもそも微粉炭も流動層も狙いは、接触面積を上げることにあります。
空気と固体である石炭を効率的に燃焼させるためには、空気と固体の接触面積が大きい方が良いです。
固体を積み上げた火格子燃焼方式では、積み上がった石炭のうち内部にある一部の燃料が燃えない可能性があります。
そのために、空気と石炭を混ぜ合わせた状態を作り上げることが大事。
これを送気ライン中で行うのが微粉炭バーナー燃焼方式、火格子内で行うのが流動層燃焼方式です。
ボイラー燃焼室
ボイラーの燃焼室・通風について紹介します。まずは燃焼室から
燃焼室の条件
燃焼室は言葉どおり、燃焼する部屋です。
この燃焼室に求められる条件を整理します。
- 燃焼室は高温を維持する
- 燃料が速やかに着火する
- 燃料と空気を効率よく混合させる
- 燃焼を完結させる
これらの条件を満足するt目に、燃焼室の構造を決めていきます。
燃焼室の構造
燃焼室の構造について主要部品を紹介します。
メインは炉壁です。
炉壁とは燃焼室の壁のこと。
部屋でも壁は大事ですよね。
レンガ壁
炉壁はレンガで作られることが多いです。
レンガは耐熱性が高いですからね。重宝します。
最近ではレンガの代わりに耐火材も開発されています。
水冷壁
水冷壁は水で壁を冷やす方式です。
こう書くと濡れ壁を想像する人もいるでしょう。
ボイラーの水冷壁は、水管を炉壁に配置します。
レンガが高温になり過ぎると、外気に熱が放出します。
水管を壁に配置すると、レンガが高温になるのを防げます。
かつ、水管で吸収した熱がそのまま蒸気発生の熱に使えます。
水管を壁に配置するだけのシンプルな発想ですが、効果は高いです。
ボイラー通風
ボイラーの通風について説明します。
燃焼室では燃料と空気を混ぜて燃やすことが基本です。
空気も大事な要素ですので、確認しましょう。
自然通風
自然通風とは煙突のドラフト力を利用したものです。
煙突は下から上に空気が流れていく方向です。
燃焼室で温まった空気は密度が軽くなります。
軽い空気は高い位置に上がろうとします。
高い位置ほど空気の密度は低いですからね。
温度の高い空気が密度の差が浮力となって、煙突を登っていきます。
ドラフト力は空気の密度差だけが駆動力なので、小さな力です。
原始的ですが、最近は使いません。
人工通風
自然でなければ人工的な力で通風させます。
簡単に言うと、ファンです。
押込通風
押込通風はファンが燃焼室の手前にあります。
ファンで圧力を上げた空気を、燃焼室に押し込みます。
メリットは以下のとおり
- 燃焼室に余分な外気が漏れこまない
- 燃焼効率が高い
燃焼室内に空気を押し込むため、燃焼室の圧力力は外気より高いです。
だからこそ、外気は漏れこんできません。
ファンで押し込んだ高い圧力で燃焼室に吹き込めるため、燃料と空気を効率よく混ぜることもできます。
誘引通風
誘引通風は押込通風の逆です。
ファンが燃焼室の出口にあります。
メリットは、燃焼ガスが外部に漏れこまないという1点。
化学プラントでは重宝します。
炎や高温ガスが外気に漏れると、外気に漏れた有機溶媒に着火する恐れがありますので。
ですがデメリットもあります。
- 高温で密度の低い(体積の大きい)空気を吸わせるので、ファン動力費が高い
- 燃焼ガスのすすやダストをファンが吸って、ファンが腐食する。
参考
関連記事
最後に
2級ボイラーの運転や取扱いについて知っておくべきことを解説しました。
ボイラー運転は、安全かつ効率的に蒸気を供給するために欠かせない基本的作業です。運転前の点検から運転中の管理、停止時の手順までしっかり理解し、トラブルを未然に防ぎましょう。初心者の方も今回のポイントを押さえて、安心してボイラー運転に臨んでください。
ボイラーが水・燃料・空気・蒸気という4つの要素から成り立っているという基礎を抑えながら、個々の部品について見ていくようにしましょう。
化学プラントの設計・保全・運転などの悩みや疑問・質問などご自由にコメント欄に投稿してください。(コメント欄はこの記事の最下部です。)
*いただいたコメント全て拝見し、真剣に回答させていただきます。
コメント