化学プラントの設計でも大事な防爆設計。
かなり大事な割に、設計がかなり雑なのが実態です。
設計方法が定性的で、危険場所の限定化が難しいことが背景にあります。
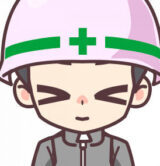
良く分からないから、一律で2種場所
こんな発想でガチガチの規制を作って、手も足も出なくなる化学工場は多いと思います。
近年はようやく緩和されていく方向ですが、急に変わるのは難しいでしょう。
仮に防爆範囲が変わったとしても、基本となる防爆思想が変わるわけではありません。
そういう背景を知ったうえで防爆機器の選定をすることは、機電系エンジニアリングで大事なことですね。
着火源・爆発性雰囲気の定義
防爆設計で非常に大事な発想が着火源と爆発性雰囲気です。
燃焼の三要素である着火源・可燃物・支燃物。
これを別の良い方をすると着火源・爆発性雰囲気となります。
具体的な定義をまずは確認しましょう。
着火源
着火源として以下のものがあります。
- 裸火
- 高温表面
- 電気火花
- 静電気火花
- 衝撃火花
今回は、電気についてですので、高温表面・電気火花・静電気火花が該当します。
爆発性雰囲気
燃焼の3要素のうち、可燃物と支燃物を合わせて爆発性雰囲気ということがあります。
危険物4類を例に挙げると、危険物そのものが可燃物、空気が支燃物です。
4類の場合、可燃物と支燃物が一定の割合でないと燃えません。
これを燃焼範囲と言います。
可燃物0%・支燃物100%の純粋な空気なら当然燃えませんが、可燃物100%・支燃物0%の純粋な危険物だけでも燃えません。
この燃焼範囲に入っている環境を爆発性雰囲気と言います。
爆発性雰囲気ができやすい工場
爆発性雰囲気ができやすい代表例は、化学プラントです。
化学プラントの中には、石油・医薬品・農薬なども含みます。
化学プラント以外には、半導体・ゴム・塗装・樹脂などの製造業も該当します。
いずれも危険物を扱っています。
半導体が少しイメージしにくいでしょうか。
ゴム・塗装・樹脂はまさに燃えやすい典型例です。
爆発性雰囲気ができやすい場所
危険物を取り扱う装置・配管が典型的な場所です。
適切に取り扱っている場合は、装置・配管内では爆発性雰囲気はできていません。
怖いのは、接続部。具体的にはフランジ。
フランジにカバーをつけたり、断熱材を付けると、逆に怖いことがあります。
フランジから漏れたガスが、空気中に拡散しにくく、滞留した状態で空機と混じり爆発性雰囲気を作る。
これは目に見えないだけに怖いことです。
着火源・爆発性雰囲気の対策
着火源や爆発性雰囲気を形成しないようにするためにできる対策を紹介します。
これを適切に実施できていなければ、危険物を取り扱うことはできません。
非常に大事です。
着火源の対策
まずは着火源に対してできる対策を紹介します。
火花を発生させない
火花を発生させないとは、例えば火花が発生するような工事を、運転時に禁止するということです。
静電気対策を適切にとって、運転時に静電気が発生しないようにするということも対策の1つ。
電流を極小化する
火花を発生させない努力をしても、電動機の端子部はそうはいきません。
ここは金属部が露出した状態なので、静電気が発生する恐れがあります。
しかし、電流が極めて小さい場合は、発生しません。
小さな電流でも作動するようにした構造を、本質安全防爆と言います。
小さな電流でも使えるものは計器くらいであり、
回転機などの動力設備では低い電流で動かすことはありません。
ここでは、単なる1つの手法として理解してください。
爆発性雰囲気の対策
爆発性雰囲気に対する対策も紹介しましょう。
窒素で遮断
火花が発生する部分について、火花が発生しないよう電流を落とすのが本質防爆でした。
火花が発生するくらいの電流を使っても、できる対策として
火花と爆発性雰囲気を遮断する
という思考があります。
静電気が発生する場所に、爆発性雰囲気があれば火災爆発しますので
火花が発生する恐れのある場所に、窒素や油などで封入するという方法が考えられます。
バッチ系化学プラントではほとんど行いません。
構造で物理的に遮断
耐圧防爆構造がこの1つに分類されます。
耐圧防爆構造は爆発しても、火炎が延焼しないようにする構造ですので、
爆発を物理的に遮断できているわけではありません。
それでも爆発後に、周囲への爆発を防げれば、それは遮断の1つとして分類しても良いでしょう。
というのも、耐圧防爆構造は電気設備のスタンダードな防爆構造だからです。
この他に、物理的な遮断をしようとすれば、電気設備をビニール袋で覆って測定するというようなアナログな方法になります。
立派な方法の1つで、簡易的な測定器には今でも使う方法です。
でも、これをメインの対策としたくないため、耐圧防爆を先に取り上げています。
ソフトで遮断
これは本質的な対策としては認められていません。
例えば、周囲のガス検知器が作動すれば、インターロックが掛かって設備の運転を止めるという発想です。
これは、ガス検知器が適切に作動するかどうかの信頼がおけないことが課題です。
ガス検知器が作動する場所が最もガス濃度が高いとは限らず、ガス検知器が作動する前に爆発性雰囲気が形成される部分があり、静電気着火により爆発する可能性はあります。
ガス検知器の設定に余裕を設けて、爆発下限界の25%以下に設定することが一般的ですが、しょせん気休めです。
爆発性雰囲気の指標
爆発性雰囲気に関連する指標として発火点・最大安全すきま・最小点火電流があります。
これらの定義も紹介しましょう。
発火点
発火点は引火点と関連のある、物理的な指標です。
最大安全隙間・最小点火電流のような設備に固有の指標ではなく、物に固有の指標です。
設備に固有の指標を特性値、物に固有の指標を物性値と使い分けることもありますよ。
引火点・爆発限界・相対密度も物性値です。
物性値は人間が変更することのできない値です。神が与えたパラメータ。
発火点は、「その温度になると自然と燃える温度」と考えればいいです。
引火点は、「その温度になって、着火源があると燃える温度」です。
着火源である生火や静電気等がなくても、発火点温度まで上がると、物体は燃えます。
ということから、 発火点 > 引火点 という関係になります。
電動機は運転をすると温度が上がります。
電流を流すと、電気のエネルギーのいくらかが熱として発散するためですね。
電動機の表面温度が高くなりすぎると、
外気に混じった可燃性ガスが高い表面温度の電動機に触れ、発火ということが起こりえます。
最大安全すきま
最大安全すきまは耐圧防爆の指標です。
耐圧防爆は、電動機内で爆発が起こっても外部ガスに引火しない構造という定義です。
電動機は完全に密閉されておらず、すきまがあります。
電動機内に爆発性雰囲気を形成することはあります。
- 火災爆発が起きても、火が外部に延焼しない構造
- 爆発が起きても電気設備が変形しない構造
これを決めるために、すきまが重要です。
すきまが大きいと、火は外部に延焼するが、爆発力を逃がすことができます。
すきまが小さいとその逆です。
このトレードオフの関係で、すきまと強度をどれだけ確保するかという設計を
耐圧防爆では求められます。
なお、火が延焼しないという意味で、火炎逸走限界という定義もあります。
また、フレームアレスタのような網も火炎逸走を防止することが狙いで、すきまが重要です。
最小点火電流
最小点火電流は本質安全防爆の指標です。
本質安全防爆は、最小点火電流以下の電流で使える設備と考えればいいでしょう。
最小点火電流は最大安全すきまと関連があるようです。
一方が分かれば他方が分かる。
そういう関係性にあるようです。
危険場所
化学プラントで危険場所というとき、以下の前提があります。
- 爆発性雰囲気を形成する
- 電気器具を使う
いわゆる治安や犯罪に関する「危険」ではありません。
火災爆発の方が、影響範囲が大きい可能性が高いので、はるかに危険ですよ。
この危険場所は、0種・1種・2種の3つに分かれます。
0種場所
0種場所とは以下の定義です。
爆発性雰囲気が連続して存在するか・長時間存在する場所
化学プラントの容器内・配管内は基本的に0種です。
バッチ系で例外的に0種に該当しない可能性がある場所として以下があります。
毎バッチの最終工程で水洗浄を行い、可燃性ガス検知器で検知しないレベルまで蒸気濃度が下がった場所
これは極めて限定的であり、普通はここだけ取り上げて0種場所から除外することはありません。
いわゆる抜け道として考えうる、という程度の位置づけです。
連続プラントであれば基本的にすべて0種場所になるでしょう。
1種場所
1種場所とは以下の定義です。
爆発性雰囲気が、正常状態で生成することがある場所
化学プラントでバッチ・連続関係なく該当する例として、これらが該当します。
溜めます・防油堤
そのほか、一般的に該当する場所として、これらが該当します。
ガスラインの大気開放口、サンプリング、原料投入、製品充填、廃油充填
これらは危険物が大気中に接する可能性がある場所です。
これらの作業は、日常的に行いますので、「正常状態」という定義になります。
2種場所
2種場所とは以下の定義です。
爆発性雰囲気が、正常状態で生成することなく、たとえ生成しても短時間しか存在しない場所
「正常状態で生成しない」という点がポイントです。
何をもって「正常状態で生成しない」とするか。
よくある例として、配管フランジがあります。
フランジのガスケットが劣化して、液が漏れるというケースはまれに存在するから、という考えです。
設備の劣化・異常操作などの特別な場合に、漏洩が起こりえる場所を2種場所と定義しています。
これは化学プラント内のありとあらゆる場所が2種場所になります。
ここを否定して、2種場所範囲を限定的にするためには、
- 装置や配管の位置情報から厳密に記録する
- 設備の増改築による情報をタイムリーに記録する
というプロセスを繰り返さないといけません。
これは特にバッチ系化学プラントではほぼ不可能です。
バッチ系化学プラントでは配管改造は日常的に行い、毎年配管が増えていきます。
放出源
放出源とは、言葉どおり可燃性物質の放出が起こる源を等級分けする仕組みです。
これは、危険場所とかなり考え方が近く、混同しがちです。
放出源は危険物が存在する場所そのものです。
危険場所は放出源の周囲を含む領域です。
広さという視点でいうと、以下の通りです。
放出源 < 危険場所
連続級放出源
連続級放出源とは言葉どおり、以下の定義です。
連続的に・長時間に可燃性物質を放出する源
もしくは短時間でも高濃度の放出も連続級放出源も該当します。
危険物の貯留している容器などは連続級放出源です。
ここは自動的に0種場所となります。
連続級放出源はシンプルな考えなので、危険場所とのリンクもしやすいです。
連続級放出源は0種場所と同じ!
1級放出源
1級放出源の定義は下記のとおり
正常状態で、定期的にまたはときどき放出することが予想される放出源
あいまいな「正常状態」という単語が入っています。
危険場所でも使われる表現である「正常状態」
具体的な例で確認していきましょう。
- 排水を大気中に開放して常時排出する場所で、可燃性物質が放出される場合
- 可燃性物質が大気中に放出されるサンプリング場所
サンプリングが特に混同しやすいです。
サンプリングは危険場所としては「1種場所」として定義されます。
放出源としては、「大気に放出される」という前提において「1級放出源」です。
例えば、サンプリングを可能な限り密閉化する装置を付ければ、「2級放出源」として定義できます。
ところが、サンプリングを密閉化しても2種場所とみなすのは少し無理があります。
1級放出源はほぼ1種場所!
2級放出源
2級放出源の定義は、以下のとおり。
正常状態では放出することが予測されず、放出してもまれで短期間の放出源
2級放出源の具体例としては以下のものがあります。
- シール部で、正常状態では放出が予測されない場所
- フランジ、継手、配管付属品
- 可燃性ガスや蒸気が大気中に放出されないベントライン
- 可燃性物質が大気中に放出されないサンプリング場所
シール部もフランジも同じ意味合いです。
どちらも劣化すれば漏れます。これは2種場所と同じ考えです。
ということで、2級放出源は2種場所と近いと予想されます。
ところが、ベントラインは少し違います。
タンクのベントラインに熱交換器を通して、大気に開放することはよくあります。
熱交換器でタンクのガスラインを冷やして、大気中に放出されるガス量を抑えるためです。
場合によっては、窒素を流しながらベントラインに放出することもあるでしょう。
これは、「2種場所ですが、1級放出源」と私は考えます。
「2種場所であり、2級放出源」と考えれるかもしれませんが、私はそう解釈していません。
というのも、危険場所は「爆発性雰囲気」、放出源は「可燃性ガス」という表現を使っているからです。
たとえ、熱交換器で冷却しているとはいえ、蒸気圧分の可燃性ガスは放出されます。
それが爆発下限界以下であれば、爆発性雰囲気を形成しないために、危険場所に該当しないというだけです。
その意味では、「危険場所に該当せず、2級放出源」と考える人もいるかもしれません。
2級放出源はほぼ2種場所!
換気
換気の種類として4つに分類して考えます。
- 自然換気
- 強制換気
- 局所換気
- 無換気
それぞれの換気方法とバッチ系化学プラントでの適用先を紹介します。
自然換気
自然換気とは、風による空気の移動で換気を狙ったものです。
温度勾配による空気の移動効果もありますが、風による移動効果の方が強く印象に残るでしょう。
プラント全体が基本的に開放された構造物なので、自然換気に該当します。
この理由のために、開放構造物としていると言っても良いでしょう。
開放構造物は自然換気を意図しているよ!
強制換気
強制換気とは、換気扇による換気です。
壁で囲われた部屋で、換気扇を使って換気します。
吸気・排気それぞれに換気扇を設置するかどうかが決まります。
排気側に換気扇
バッチ系化学プラントでは「吸気は換気扇なし・排気は換気扇あり」というパターンが多いでしょう。
換気扇あり・なしをそれぞれ自然・強制と呼ぶこともありますが、混乱する原因となりますので、ここでは使用しません。
換気扇なしとは、窓とかドアなどの隙間からの空気の流れを指します。
換気扇を吸気もしくは排気のどちらかに付ければ、その空気の流れができます。
- 排気側に換気扇を付ければ、窓やドアから空気が入ります。
- 吸気側に換気扇を付ければ、窓やドアから空気が出ていきます。
家のトイレやお風呂などは、バッチ系化学プラントと同じく、排気側に換気扇を付けます。
これは内圧室の真逆の発想です。
拡散場所のコントロール
排気側に換気扇を付けるということは、拡散場所を制御するということです。
内圧室にすると、部屋のあらゆる場所から外に向かって漏れようとします。
トイレなら臭気、お風呂なら湯気が漏れます。
これを特定の場所から放出させて拡散させることで、全体的に漏洩することを防いでいます。
化学プラントも同じです。
強制換気は、換気扇で空気を置換!
局所換気
局所換気とは、配管やホースの末端が開放されていて、除害装置に繋がっているような場所を指します。
簡単にいうと、局所換気は家庭の掃除機です。
掃除機では特定の場所を、人が装置を移動させて吸い込みします。
強制換気は換気扇そのものですね。
掃除機と同じで、特定の場所を吸気することを目的としています。
これは具体的には、サンプリング場所。
サンプリングは1級放出源となりえます。
ここに局所換気を付けることで、2級放出源を目指しています。
一般的には、サンプリング場所を箱で多い、その箱内を吸引させるでしょう。
そうしなければ、自然換気と称して、周囲の風によってサンプリング時に発生するプロセス内のガスが拡散され、作業者に暴露する恐れがあります。
自然換気が作業者の健康衛生面に問題が出てしまう。
そのために、局所換気を設置します。
サンプリング場所の局所換気は最近主流になっています。ここ10年くらいの話です。
ベントライン出口も局所換気をします。こちらはかなり昔から一般的でしょう。
40年以上前のプラントでは局所換気をしていない場所が結構あります。
この辺は、歴史を調べていけば気が付きます。
局所換気はサンプリング、ベントラインなど
無換気
無換気とは何も対策を取っていない部屋内などを指しています。
ところがこれは普通はあり得ません。
あえて言うと、地下ピット内に入って掃除をするなどの場合です。
これは限定的。
保護具を付けて、空気呼吸器をつけて作業することになります。
無換気状態での作業は厳禁!
危険場所の設計手順
危険場所の設計には下記の要素を使用します。
- 放出源
- 換気
放出源の等級と換気方法で、危険場所が決まります。
放出源による設定
放出源は、連続放出源>1級放出源>2級放出源という区分です。
- 連続放出源であるかどうかを設定
- 1級放出源であるかどうかを設定
- 2級放出源であるかどうかを設定
というように、フローチャートに従った判定を行います。
2級放出源ですらなければ、危険場所には該当しません。
距離による設定
放出源に対して距離で危険場所の分類をします。
距離以外に可燃性ガスの放出方式なども要素としてありますが、基本的に距離です。
- 連続放出源で、距離が短ければ0種場所、距離が遠くなると、1種場所・2種場所へ移行
- 1級放出源で、距離が近ければ1種場所、距離が遠くなると2種場所
- 2級放出源は、2種場所
という考えで設定を行います。
表で考えた方が分かりやすいので、下記に示します。
放出源と距離 | 近い | 中間 | 遠い | 最遠 |
連続放出源 | 0種場所 | 1種場所 | 2種場所 | 非危険場所 |
1級放出源 | 1種場所 | 2種場所 | 非危険場所 | 非危険場所 |
2級放出源 | 2種場所 | 非危険場所 | 非危険場所 | 非危険場所 |
ここで問題なのは放出源の種類と距離によって、危険場所の範囲が変わること。
換気方法によって変わる
換気方法が適切であれば2種場所であっても、不適切であれば1種場所になる場合があります。
これを換気による危険場所の緩和と呼ぶことにします。
危険場所の設定上は、換気扇の作動を担保するシステムがあるかどうかで決まります。
換気扇の作動が止まれば、プロセスの運転が止まるようなインターロックを組んでいる場合は、
換気扇による危険場所の緩和を適用できます。
ところが、そういうインターロックを組むことはほとんどありません。
ガス検知器による換気扇の作動を、インターロックで組むこともあまりありません。
2種放出源の場所が特定しにくい
2種放出源として、プラント内の配管やガスケットが該当します。
配管というと、プラント内の全域にいきわたっています。
- 特定の配管を放出源と設定して、
- その放出源から適切な距離を設定して、危険場所を決める。
というプロセスは、非常に時間がかかります。
それをするくらいなら、
- プラント全域を放出源と設定して、
- その放出源から適切な距離を設定して、危険場所を決める。
という方法の方が、確実で早いです。
距離の区分が多い
これは明確な指針が少ないことが1つの原因です。
危険物の量や、運転方法、プラント構造物の構造などによって
設定距離がいろいろ変わります。
ここをちゃんと設定できる専門家は、非常に少ないです。
危険場所の設計例
バッチ系化学プラントの危険場所の具体的な設計例を紹介します。
危険場所の設計は化学プラントの機械・電気エンジニアにとってとても大事。
この設計次第で、プラントの投資が大きく左右されます。
危険場所の設計は、0種・1種・2種という放出源と換気を元に実施することになっています。
そして危険場所には防爆機器を設置します。
ところが、ほとんどの工場では実態に応じて設計しているでしょう。
この具体例を紹介します。
なお、参考資料として産業安全研究所技術指針の工場電気防爆指針があります。
https://www.jniosh.johas.go.jp/publication/doc/tr/TR_No39.pdf
1種場所と2種場所の厳密な適用は無理
1種場所と2種場所をバッチ系化学プラントに厳密に適用するのは無理があります。
バッチ系化学プラントの危険場所の例を見てみましょう。
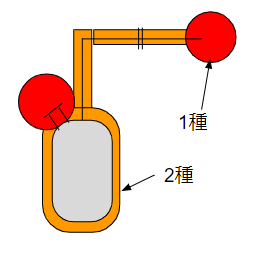
1種場所として考えられるのは、危険物を扱う設備周りで、サンプリング箇所であるマンホールや、漏えいが考えられる配管フランジ、ガスライン出口の放出部などです。
設備周りは全体的に2種場所に相当します。
バッチ系化学プラントだけでなく連続系の化学プラントも同じです。
こう考えると、1種場所も2種場所もかなり限定されています。
でも、これを現場でイメージすることはできますか?
危険物の配管がプラント中のどこを通っているか瞬時に明確に分かりますか?
これが、厳密な定義を当てはめるのが難しい理由です。
現実的な防爆設計
現実的な防爆設計を紹介します。
割と簡単で、「考えられる全範囲を2種場所に設定」するというものです。
下の図のようなイメージですね。
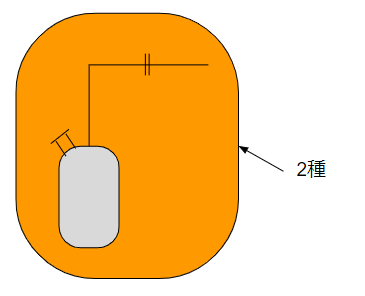
とにかく全体を危険場所として設定しておけば、間違いではないですね。
全体を1種場所として定めないのは、以下のような背景があります。
- 1種場所の範囲が限定化されていること
- 設備周りには1種場所に相当するような危険な状態にないこと
実際には2種場所はフランジ周りだけなので、フランジを除く配管直近は2種場所ですらありませんが。
危険場所を表示するためには、専用の配置図上に表記します。
全体を2種場所に設定した場合、以下のような危険場所区分になります。
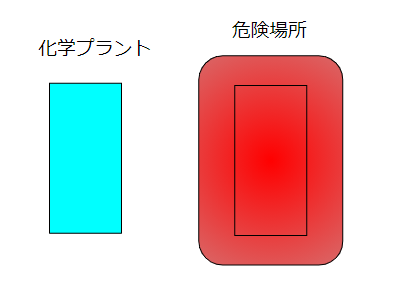
左が化学プラントとして、右が危険場所です。
これは化学プラント全体を危険場所として設定しているという例ですね。
化学プラントでは一般にこの思想での危険場所設計をしています。
特殊な防爆設計
特殊な防爆設計例を紹介します。
これは危険場所の一部を防爆範囲から外すというもの。
下のようなイメージです。
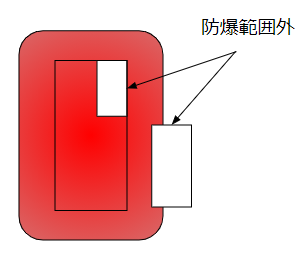
プラント内だと充填室など、プラント外の周辺施設だと計器室などは防爆設備を設置することができない場合があります。
こういう場合に、計器室の内圧室と同じ発想で対策を取ります。
計器室のようにプラントからやや離れた場所にある場合は、設計しやすいですね。
危険場所以外からの清浄な空気を計器室内に取り込み、計器室の圧力をやや高くして、空気は外に排出すればいいわけです。
一方で、プラント内は厳密にはかなり難しいです。
清浄な空気を取り込むためにダクトが必要だからですね。
ここまで真剣に考えて設計している会社はあまりないと思いますが・・・。
非危険場所の設計
危険場所近くで非危険場所を設ける場合にどんな対策をするかの一例を解説します。
古い計器室でこの考え方を採用している場合があるでしょう。
危険場所で非防爆エリアを設定する理由
そもそも危険場所で非防爆エリアを設定すること自体がおかしな話です。
防爆配置図などを見ると、昔のプラントでは以下のような「露骨なエリア設定」をしているケースはあるでしょう。
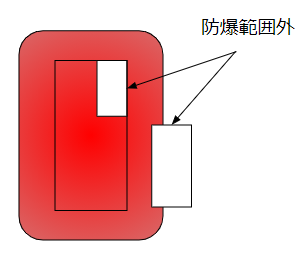
この設計には、「室内を陽圧に保つ」という明確な思想があります。
それを考えもせずに、たまたま非防爆に設定した場所だ。曲解する人はいます。
機械・電気・計装・土建どのエンジニアも均等な割合で存在します。
化学プラントでのエンジニアリングではなく、通常の建築物のエンジニアリングの感覚でいるとこの発想になります。
内圧室
危険場所で非防爆設備を使うためには、内圧室に対する考え方が必要です。
内圧室というと陽圧管理を厳密に行うことがイメージされます。
- 圧力計を設置して、一定値以下ならアラームを出す。
- 部屋の圧力が一定値になれば、ダンパが作動する。
こういった場所は、一定の陽圧が担保されます。
逆にそういう対応をしていない場合は、陽圧は維持できません。
何となくの感覚で、以下のような設備構成とすると、陽圧が管理できないという意味ですね。
- 換気扇を付けて部屋内の空気を外に出す
- 換気扇で追い出した分の空気は、ガラリから吸い込む
清浄な空気
陽圧管理ができない・するほどではないが、危険場所に非防爆設備を置きたいというケースは実際には存在します。
こんな場合は、少しでも正常な空気を取り込むことを考えないといけません。
- 風が通り抜ける場所から空気を取り込む
- 風向きに対抗する形で空気を取り込む
- 地面等の有機溶媒ガスが溜まる場所から空気を取り込まない
換気扇の能力が固定されていて換気回数自体を変えることができなくても、フレッシュな空気を取り込めるかどうかということ自体は容易に設計が可能です。
着目点はアナログですが、基本的な項目でありだからこそ効果的です。
テクニカルな「換気回数」というワードに拘っていると見落としがちですね。
計器室
計器室内で、電気を扱う設備を紹介しましょう。
DCS、パソコン、電話、分析機器、冷蔵庫、冷凍庫、スマホ、テレビ…
どう考えても家庭用の電気設備がありますね。
そうです。計器室内は非防爆設備の塊です。
計器室は内圧室
計器室内で非防爆設備を使っていい理由は、内圧室だからです。
計器室内は、外よりも若干圧力が高い状態を維持しています。
そうすると、計器室の扉を開けても、化学プラント周囲の爆発性雰囲気が計器室内に入ってきません。
計器室内は爆発性雰囲気でないきれいな空気で満ちています。
二重扉、外開き
計器室に出入りする扉は、二重扉にします。
一瞬でも二つの扉が開いた状態を確保しないようにすることが目的です。
これで計器室と外気を遮断する狙い。
ところが、これを守っているケースはあまり多くありません。
大体は二重扉の二枚の扉が近く、両方の扉が開いてしまう場合が多いです。
それ以外にも、様々な要因で扉を開けてしまいますね。
扉は外開きにします。
これは一般家庭や事務所でも同じ。避難目的です。
2か所の扉
化学プラントでも同じですが、扉は必ず2か所付けます。
1か所だけの扉は絶対にダメです、
火災。地震等があり、1か所の扉が動かなくなると、避難できなくなるからです。
網入りガラス
ガラスに強度を持たせるためです。
万が一、化学プラントで爆発が起こっても、その爆風で窓ガラスが割れて、飛散するリスクを減らすためです。
爆発が起これば、ガラスは割れます。
それが飛び散らないようにするのが狙いです。
ガラス窓は開放しない
内圧室の発想が分かれば、当然これは予想できます。
窓を開けると、内圧を確保できませんね。
ガラス窓は、「はめころし」の状態にします。
空気の取入れは、屋上等の新鮮な空気
内圧を確保するための、空気の取入れは、ファンで空気を押し込むという方法を取ります。
このファンの能力で、部屋内の換気回数が決まり、作業性がきまるので、極めて重要な設備です。
どこから空気を取り込むかという問題もあります。
普通は、計器室の屋上にするでしょう。
計器室が化学プラントのすぐ近くであっても、化学プラントから生成した爆発性雰囲気は地面に溜まる方向です。
屋上など高い位置には、爆発性雰囲気はたまりません。
屋上で、雨風が入ってこないような形でガードをして、ファンで空気を押し込むことが普通です。
参考
関連記事
さらに知りたい方は、以下の記事をご覧ください。
最後に
防爆設計で使用する考え方を解説しました。
着火源や爆発性雰囲気の定義と対策・爆発性雰囲気の仕様・危険場所・放出源・換気・危険場所の設計
一度設計してしまえばなかなか変えることができない危険場所。
実際に設計することがなくても、その考え方は知っておきたいですね。
化学プラントの設計・保全・運転などの悩みや疑問・質問などご自由にコメント欄に投稿してください。(コメント欄はこの記事の最下部です。)
*いただいたコメント全て拝見し、真剣に回答させていただきます。
コメント