化学プラントの機械設計では、機械的な力を正確に伝える部品の役割がとても重要です。力の伝達がうまくいかないと、設備の故障や事故につながることもあります。
この記事では、化学プラントで使われる機械的力の伝達部品について、初心者でもわかりやすく基本から解説します。
化学系のエンジニアから見たら、機械エンジニアはこういうギアのような機械的な勉強をしてきた人という目で見られます。実は知らなかったと思われることは、大学時代に勉強を疎かにしてきたとも思われかねないでしょう。
隙を作らないためにも、基本的な部分だけは学習した方がいいですよ。
軸継手
軸継手は機械装置の大事な部品の1つ。
モーターとインペラの接続など、化学プラントの設備も軸継手を使うのが基本です。
軸継手は機械装置があれば、かなりの確率で発生します。
その軸継手として、一般には下記の種類があります。
- フランジ型固定軸継手
- フランジ型たわみ軸継手
- オールダム軸継手
- 歯車型軸継手
- ローラーチェーン軸継手
- ゴム軸継手
- 金属ばね軸継手
- フック型自在軸継手
非常に多いですね。
化学プラントでは、フランジ型固定軸継手とゴム軸継手くらいしか使いません!
これで十分です。
固定軸継手(フランジ型固定軸継手)
固定軸継手は軸どうしをガッチリ固定させます。
構造としてはいたってシンプルです。
下の図を見てください。
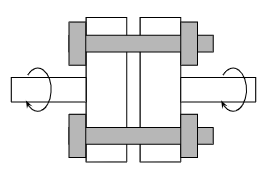
2つの軸の末端がフランジ構造になっています。
フランジをボルトで固定すれば終わりです。
ボルトを使わずに、キーで止める場合も発想は同じです。
2つの軸が完全に一致する場合に使います。
化学プラントの設備は基本的にこの固定軸継手が多いです。
モーターと回転羽根がずれている場合はどうするのだ?という意見もあるでしょう。
その問題よりも、位置調整をちゃんと行って、完全に固定させることを好みます。
というのも、効率ロスを極小化したいからですね。
特にバッチ系化学プラントでは設備が小さいから、継手前後のズレが大きな問題にならないということもポイント。
たわみ軸継手(ゴム軸継手)
たわみ軸継手は固定ではなく「たわみ」があります。
固定軸手のように、継手前後が完全に一致している必要はありません。
多少のズレを吸収するために、たわませます。
構造は以下のとおりです。

この例は、フランジ型たわみ軸継手と言います。
2つの軸にフランジを付けて、間をボルトで通します。
ここまでは固定軸継手と全く同じ。
違いは、ボルト固定部にゴムを付けていること。
ゴムでたわみを吸収させようという発想です。
この他にも、星形ゴム軸継手・タイヤ型ゴム軸継手・ギアカップリング・チェーン型軸継手などがあります。
いずれも、変形を吸収する部材を挟んでいるのがポイント。
バッチ系化学プラントでは遠心分離機に使います。
遠心分離機では高速回転をするため、わずかな軸のズレでも大きな影響がでます。
これを人力で固定軸継手で固定することは不可能。
多少のエネルギーロスは発生するし、ゴムなどの消耗品が出ることは仕方がありません。
それよりも高速回転の性能を優先しないといけないのが、遠心分離機です。
Vベルト
Vベルトについて化学プラントの設備で使う場合に知っておきたい情報をまとめます。
Vベルトは一般の機械装置に幅広く使われています。
断面がV型をしたベルトだからVベルトです。
化学プラントでは、ポンプ・送風機・減速機などに使います。
一般的な機械部品のであるVベルトは、仕様や要求事項も幅広くあります。
化学プラントで必要な仕様に絞って、Vベルトの解説をします。
Vベルトのメリット
Vベルトのメリットを整理します。
- メンテしやすい
- 振動や衝撃を吸収する
- 伝達効率が良い
- 機械寸法を小さくとれる
Vベルトはメンテが楽です。
安くて速く調達できますので、壊れても一瞬で取り替えできます。
減速機だとメンテンナンスに時間が掛かります。
機械寸法を小さくできるとは、例えば
- 反応器なら上下高さを抑える
- ポンプなら水平寸法を抑える
ということが可能です。
モーターと装置本体の位置を決めるための自由度が高いのがVベルト。
Vベルトでない直結の場合は、モーターの位置は装置本体の位置に強い制約を受けますよね。
この機械寸法が小さくできることは、配管設計や現場の運転において非常に助かります。
静電防止
Vベルトは静電防止にすることが化学プラントでは必須条件です。
ベルトはプーリーと激しくこすれ合います。
「これでもか」というくらい静電気の溜まる原因となります。
Vベルトは静電防止型にすることが、化学プラントでは当たり前です。
一般的な機械装置に使うVベルトでは要求されないオリジナリティのある要求事項ですね。
プーリー比
Vベルトはプーリー比の考え方を理解しておく必要があります。
これを知らない・考えない化学プラントの機械エンジニアは多いです。
プーリー比とは2つのプーリーの比のことです。
下の図を見てください。
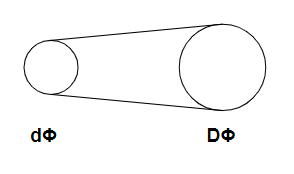
DΦとdΦという2つがプーリー径を指します。
Vベルトを挟んだ装置本体の回転速度は、DΦとdΦの比で決まります。
例えば、モーターが60Hz、4Pとすると1800rpmですよね。
モーターのプーリー径がDΦでDΦ:dΦ=2:1なら、装置本体の回転速度は1800*2 =3600rpmとなります。
これは1800*DΦ=3600×dΦ
という関係があるからです。一般化すると
プーリー径×回転速度 = 一定(Const.)
ですね。
Vベルトで2つのプーリーを挟んだとき、Vベルトは撓まず移動するので、2つのプーリーの移動量は等しいという関係があるからです。
歯車
化学プラントの機械設備で使用する歯車の種類を紹介します。
歯車自体は機械設備に非常に多く使われる、機械としては基本中の基本の部品です。
歯車の種類は非常に多いです。
ところが化学プラントの機械設備ではあまり登場しません。
ポイントを絞って解説しましょう。
ウォームギア
ウォームギアは化学プラントで使用する機会があります。
特にボールバルブやバタフライバルブで使用します。
ウォームギアは回転力を直角に伝達する機能があります。
下の図を見てください。
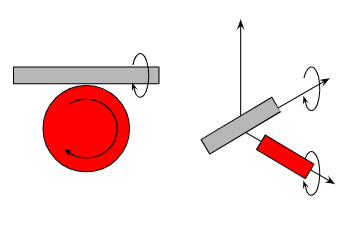
ウォームホイールとウォームはトルクが伝達されるので、トルク = 距離 × 力 の関係で、トルクが等しい時には距離が小さいと力が大きいという関係があります。
ボールバルブやバタフライ弁は手動で開閉する場合、ハンドル式が一般的です。
ところが一定の口径になると、人がハンドルで開閉することはできません。
ここでウォームギアの出番です。
ホイールを回す回数が増えますが、小さな力で大きな弁を開閉できます。
これと同じ発想にチェーンブロックがありますね。
かさ歯車
かさ歯車はウォームギアよりはレアですが、登場します。
かさ歯車もウォームギアと同じように、回転方向を変換させるときに使います。
これは特殊な設備の減速機なとに使います。
円錐状の歯車を直角に並べた構造で、円錐状の歯車が傘に見えるから「かさ歯車」と言います。
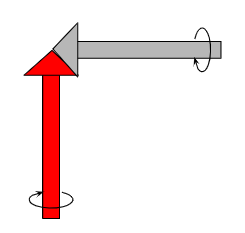
ベベルギアという良い方もします。
この絵は「すぐば」ですが、「はすば」という歯が斜めに傾いたパターンもあります。
バッチ系化学プラントで歯車を使わない理由
バッチ系化学プラントでは歯車はほとんど使いません。
歯車は機械に一般的に使いますが、化学プラントの機械設備ではなぜ使わないでしょうか?
そのキーワードはシンプル
シンプルにすることが化学プラントではとても大事。
歯車を使う機構は、やや複雑な機構です。
歯車は使い続けると、壊れます。
歯車を使わなくても機能するような設備の方がシンプル。
化学プラントの設備は、安定運転を行うためにトラブルを極小化したいです。
ただでさえ、「動機器の数が増えると故障が増える」と言われる世界です。
動機器を増やすことは仕方なくても、動機器の故障確率は下げたいものです。
イニシャルコストもランニングコストも低くする狙いもあります。
サイクロ減速機
サイクロ減速機について紹介します。
化学プラントで見かける減速機のほとんどすべてはサイクロ減速機です。
この特徴と化学プラントで重宝される理由について説明します。
サイクロ減速機は日本では住友重機械工業が有名です。
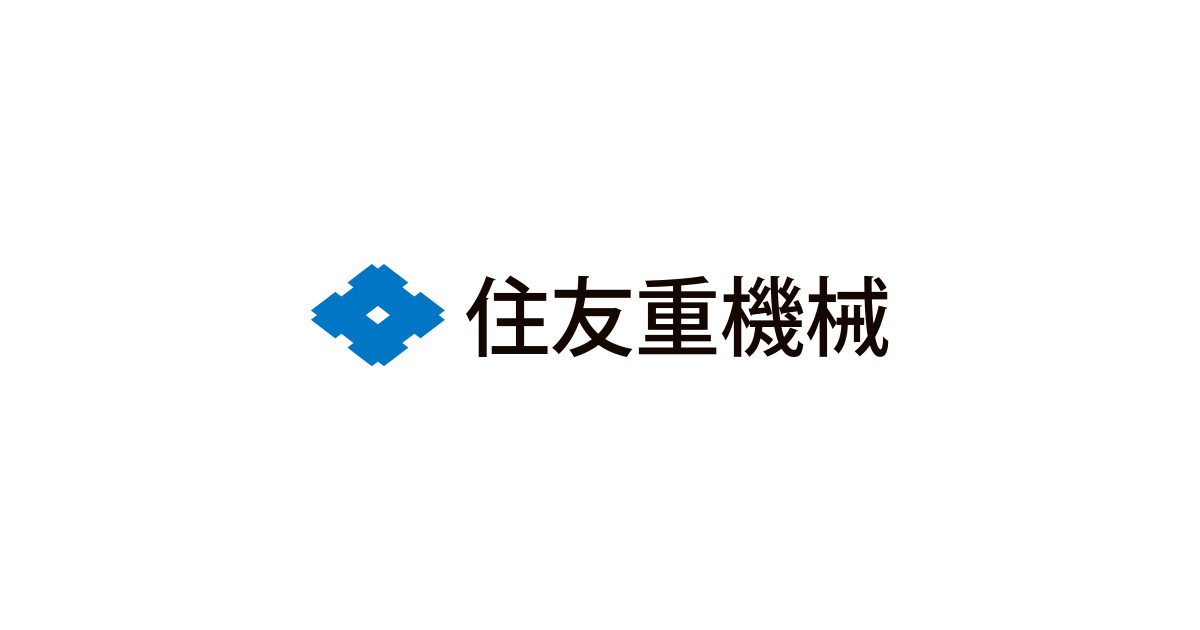
減速比が大きい
サイクロ減速機は減速比が大きいのが特徴です。
1/10~1/100程度です。
サイクロ減速機は歯車減速機の1種です。
通常の歯車減速機は1段で1/6程度です。
これより大きい減速比を出そうとすると2段・3段と段数を増やさないといけません。
化学プラントで減速機を使う主目的は、「反応」
反応のために撹拌槽で撹拌をしますが、必要な回転数は意外と少ないです。
100rpmでも高いくらいで、50rpm程度の場合も普通にあります。
60Hz・4Pモーターの回転数は1800rpm。
50~100rpmの回転数まで減速しようとすると、減速比は
50/1800~100/1800、つまり、1/36~1/18が必要です。
サイクロ減速機だと1段で対応可能ですね。
振動騒音が少ない
サイクロ減速機は振動騒音が少ないのが特徴です。
歯車減速機とはいえ、転がり接触にしているので、がたつきが少ないです。
下の図を見てください。
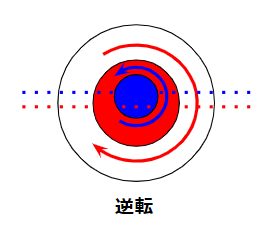
サイクロ減速機は滑らかそうな構造をしています。
実際に、転がり接触になっているサイクロ減速機はガタツキガすくなく、振動騒音が少ないです。
小型軽量
サイクロ減速機は小型軽量です。
これは減速比が大きいことと関連します。
1段で完結する小型のサイクロ減速機は、省スペースにした化学プラントに適しています。
長寿命
サイクロ減速機は寿命が長いです。
転がり接触であるため、部品に対するダメージが加わる確率が下がります。
これが長寿命に直結します。
摩耗がない・振動騒音が少ないという単語は、寿命が長いというワードに直結します。
分解組立がかんたん
サイクロ減速機は分解組立がかんたんです。
これは段数が少ない・部品点数が少ないということと関連します。
メンテナンスコストを抑えて連続運転をしたい化学プラントでは、
分解組立がかんたんというのは大きいメリットです。
バイエル減速機
バイエル減速機について解説します。
バイエル減速機は古式ゆかしい回転数変換方法です。
それでも現役で活躍していますので、特徴は理解しておきたいですね。
回転数を変える
バイエル減速機は回転数を変えることができます。
構造は下の図のとおり。
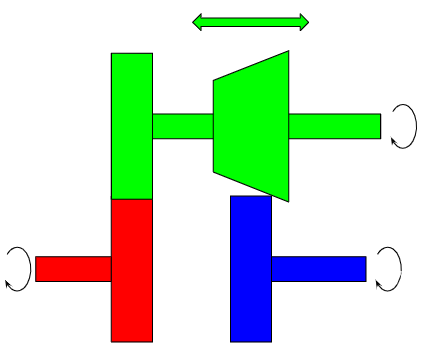
赤色の入力と青色の出力の間に、緑色のコーンディスクを挟んでいます。
コーンディスクの位置をハンドルを使って調整することで、出力に伝わる回転数を変化するという仕組みです。
低速の場合と高速の場合で、コーンディスクの位置を変えることで、フランジディスクに加わる回転数が変わります。
入力が例えば1800rpmのモーター回転数で出力が100rpmまで回転数を落としたい、という場合に使います。
これだけならサイクロ減速機も同じです。
バイエル減速機は回転数をある程度変換することができます。
運転条件に応じて100rpmや200rpmなどある程度の幅を持たせたいときに使います。
これが大きな特徴。
サイクロ減速機だと減速比が1つに決まってしまうので、例えば100rpmなど1つの回転数に固定されます。
運転時にしか調整できない
バイエル減速機の注意点を紹介します。
バイエル減速機の速度調整は運転時にしかできません。
バイエル減速機の運転を止めた状態で、コーンディスクの調整を変えようとすると故障する可能性があります。
古い設備だからこそ、使い方を知らないで壊す可能性がありますね。
街中の電話ボックスと同じです。
バイエル減速機は安い
バイエル減速機はコストが安いのが大きな特徴。
対抗馬であるインバータでの回転数調整と比較します。
- インバータが不要だから、制御盤が不要
- 耐圧防爆モーターが不要で、安全増防爆モーターが使える
- DCSなどとの信号接続が不要
バイエル減速機は減速機単体で見るとインバータモーターとの差があまりありませんが、
制御盤やDCSとの取り合いを考えると、トータルではバイエル減速機の方が安くなります。
バイエル減速機やインバータで速度調整がいつでもできる!
って言いながら、実際には一度調整すると回転数を変えることはあまりありません、
インバータで計器室で回転数を調整することは便利ですが、その便利さが本当にメリットに繋がるかどうかは疑問です。
こういう考え方の場合は、バイエル減速機を使用する方が良いケースもあります。
大きい
バイエル減速機はその寸法が非常に大きいです。
これはデメリット以外の何物でもありません。
竪型撹拌槽の頂点に座る大型のバイエル減速機。
日常メンテナンスでバイエル減速機にアクセスするだけでも面倒。
SDMでバイエル減速機を外すためにも大規模な工事になる可能性もあります。
コンパクトなサイクロ減速機の方がやりやすい面が多いでしょう。
参考
関連記事
さらに知りたい方は、以下の記事をご覧ください。
最後に
化学プラントの機械的力の伝達部品は、設備の安全性と効率を左右する重要な要素です。カップリングやギア、ベルト・チェーンなど、用途に応じた部品の特徴を理解し、適切に選ぶことが求められます。初心者でも基本を押さえることで、トラブルを未然に防ぎ、プラント運営を安定させることができます。
化学プラントの設計・保全・運転などの悩みや疑問・質問などご自由にコメント欄に投稿してください。(コメント欄はこの記事の最下部です。)
*いただいたコメント全て拝見し、真剣に回答させていただきます。
コメント