プラントの設計や保全で必ず登場する「計装用空気(インスツルメントエア)」。
一見するとただの圧縮空気ですが、実は求められる清浄度・乾燥度・安定供給などの仕様がかなり厳しく、通常のエアとは区別されています。
この記事では、現場で混同されやすい「圧縮空気」と「計装用空気」の違いをわかりやすく解説し、設備仕様のポイントや実務で注意すべき点を紹介します。
計装用空気ってどんなもの?と聞かれても
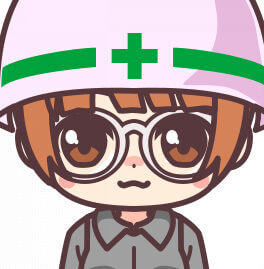
綺麗な空気でしょ
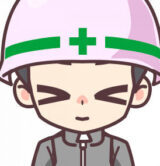
綺麗すぎる空気かな
くらいの情報だけというエンジニアも珍しくありません。それではもったいないので、今回は参考情報としての計装用空気の情報をまとめました。知っていると「できるエンジニア」と思われるかも知れません!
空気シリンダーの作動
計装用空気(インスツルメントエア)は、空気圧シリンダーの作動用に使用します。空気シリンダーは例えば自動弁や調整弁などの計装設備の駆動機構です。
自動弁に関する情報は以下の記事をご覧ください。
物を動かすという点だけに限ると電気でも使えますが、防爆の制約が強い化学プラントでは空気で物を動かすというのが一定の地位を占めています。
計装設備のように力があまり必要とされない設備なら空気でも十分という考え方ですね。
なお、力に関わるユーティリティとしては、空気の他に電気や油などもあります。ご参考まで。
計装用空気(インスツルメントエア)に求められる性質
空気圧シリンダーの機構は、密閉容器内に圧縮空気を注入して空気の力でしてシリンダーが動かすというものです。
この空気に異物やごみがあると、シリンダーが詰まって動かなくなります。万が一、自動弁の作動がしなくなると、プロセスの暴走爆発が起こる可能性があり、信頼性が非常に高い作動が求められます。
したがって、空気もきれいな空気が必要です。
ごみ取りフィルター
きれいな空気であるというためには、ごみを取らないといけません。
一般的にはフィルターを使います。
数μm以上のごみを取るフィルターが一般的です。
フィルターは適当に設置されがちですが、意外と奥が深いです。
興味がある方は以下の記事もご覧ください。
水分除去
空気中に水分を多量に含むと、シリンダー内で色々な誤作動を起こします。
- 水分により部品の鉄が錆びて、つまりのもとになる。
- 水が溜まって、空気の作動を妨げる。
大きく分けてこの2つの問題にが起こります。問題が大きくなると、どちらにしてもシリンダーを動かなくなります。
ところで露点という単語があります。露点とは水分を含む空気から、水が凝結し始める温度のことです。
計装用空気(インスツルメントエア)には、設置場所の最低気温より数度低い温度が露点となるようにすることが求められます。九州なら0℃くらいが最低気温なので、露点を-4℃くらいに設定するのでしょうか。空気圧力0.7MPaで露点を-4℃とするためには、大気圧下での露点-28.5℃となるようです。露点換算表を使って計算できます。
ここから、計装用空気(インスツルメントエア)中の実水分量が計算できて、約0.4g/m3となります。
これは、大気圧・10℃くらいの空気で考えると相対湿度3%程度というカラッカラの空気です。
油分除去
計装用空気(インスツルメントエア)では油も異物として考える場合があります。とはいえ、完全に油が無くてもダメ。どちらかというと、油が過剰にあっては駄目という感じです。
ここでいう油は作動油のこと。作動油は、シリンダーを動かすためにはあった方が好ましいです。今ではシリンダーの性能がよくなって、作動油が求められなくなっているかもしれませんが・・・。油としての有機溶媒は極力少ない方が良いです。
計装用空気(インスツルメントエア)の元となる空気は有機溶媒が滞留していない、綺麗な場所の空気を使う方が良いでしょう。計装用空気(インスツルメントエア)生成設備の場所や配管の取り口などが設計要素として考えます。
計装用空気(インスツルメントエア)を作るための設備
計装用空気(インスツルメントエア)を生成するフローの例を見ましょう。
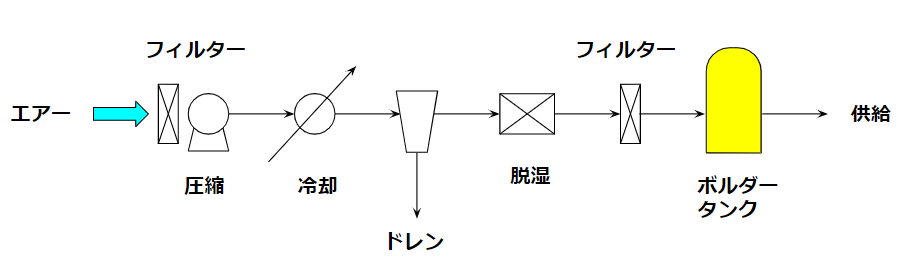
例によって、教科書ではこの記載程度で終わりです。
フローの説明を文字で行っているパターンはほぼありません。
ということで、言語化していきましょう!
①吸入フィルター
圧縮空気を作る原料は、大気中の空気です。
ゴミ・埃・有機溶媒などができるだけ含まれていない、清浄な空気の方が好ましいです。
その空気からゴミを取るためのフィルターが最初にあります。
物理的なフィルターが1番最初に来るのは、プロセス設備における基本です。
②圧縮機
①でゴミを粗方除去した空気を、圧縮機で圧縮します。
これで所定の圧力より若干高い所まで昇圧します。
③冷却器
②の圧縮機で空気を圧縮すると、空気の温度は急激に上がります。
いわゆる断熱圧縮という工程です。
一般論としては下記の説明でOKです。
大気圧の空気を、高圧の空気の状態にするために、圧縮機という動力を用いて、空気にエネルギーを加えます。
そうすると空気のエネルギーは高くなり、温度が上がります。
高温の空気では、プロセス設備に使用できないので、冷却しなければいけません。そこで冷却器を使います。
④ドレン分離器
③で冷却をすると、ドレンが生成します。
温度の高い空気ほど、水分を蓄えやすいです。
飽和水蒸気量は温度に比例します。
高圧の空気に含まれている水分は、空気の温度が下がることで、水として凝縮します。
水は、計装用空気として空気圧シリンダーに侵入すると誤作動を起こす原因となるので、除去しないといけませんね。
⑤脱湿器
④でドレンを取り除くというのは、気体と液体が入り混じった状態から、液体を取り除くだけの手法です。
これで取り除くべき液体のうち、大多数は除去できます。ところが、一部の液体は飽和分として空気中に残ります。少しでも温度が下がるだけで、またドレンが生成します。
例えば、圧縮空気を作った時間が昼間で、あまり使用しないで夜になったとしましょう。外気の影響で温度が下がった圧縮空気からドレンがまた発生します。もちろん、③で過冷却にできれば問題は起こりえません。
冷却水として冷却塔循環水を使っていれば、循環水が外気温度に左右されるため、過冷却に到達することはありません。
だからこそ、飽和水蒸気量より若干低い量まで水分を取り除くために、脱湿器を使うことがあります。
⑥フィルター
②圧縮機、⑤脱湿器では、空気は装置内を通過します。
この装置内にゴミや埃が付いていれば、それがプロセス計装に流入します。
そこで、この段階で最終的なごみ取り除去としてフィルターを通します。
フィルターが詰まっても、運転に支障が出ないように、並列設置することが普通です。
⑦容量タンク
バッファタンクともいわれます。
ここに圧縮空気を貯めます。
圧縮機が壊れたり、停電が起こったりして、圧縮空気を生成できなくなっても、
容量タンク内の空気で、最低限の処置をしようという発想です。
エアー3点セットはなぜ必要なのか
計装用空気(インスツルメントエア)には清浄性が求められます。
空気を目に見ることは少ないので、綺麗か汚いかを判断することは難しいでしょう。ですが、あなたが現在呼吸しているその空気も、汚れているかもしれませんよ!
化学反応を安定的に遂行するために、計装用空気は綺麗にしましょう。計装用空気を生成する段階で綺麗にできているものの、取扱設備の直前でさらに清浄性を担保するために設備を追加する場合があります。
それがエアー3点セットです。エアー3点セットはフィルター・レギュレーター・ルブリケーターです。
フィルター
フィルターは文字通り、異物除去です。
一般には、空気中のごみや埃などの固体を想定するでしょう。
ところが、エアー3点セットのフィルターでは、液体系も想定しています。一般的な水分や油分もこのフィルターで除去します。フィルターそのものよりも、水分や油分を除去して貯めるためのポットの方が大きいくらいです。
つまり、フィルター兼ドレンポット、という方が正しいでしょう。
このフィルターは、使用場所の空気と直接触れ合うため、フィルターの交換頻度は使用場所の空気の清浄度に左右されます。ということで、エアー3点セットの空気取り込み口はできるだけ、綺麗な空気が取り込める場所としましょう。
レギュレーター
レギュレータは、所定の圧力に減圧するための装置です。減圧弁と言った方が機械屋は分かりやすいでしょう。
例えば0.7MPaの空気をレギュレーターで0.4MPaに減圧して使用します。これは、使用先である自動弁の空気圧シリンダーの要求によります。安定運転をするためには、必要な圧力が存在します。それを実現するためにレギュレーターがあります。
一般に圧縮空気は、コンプレッサーで圧縮することで生成されます。コンプレッサーから供給された空気を、各プラントの各自動弁の各空気圧シリンダーで使用します。空気圧シリンダーはその数が非常に多いです。いつ作動するか分かりません。いきなり全ての自動弁が作動することはありませんが、一定量の自動弁は作動します。
そこで空気を大量消費すると、供給空気圧力が下がり、他の自動弁が作動しない可能性があります。そこで、コンプレッサーでは高めに圧縮して余裕を持たせたり、エアーホルダーを設けて対応します。高い圧力の圧縮空気を減圧するために、レギュレーターを付けます。
ルブリケーター
ルブリケーターは「オイルを散布する装置」です。
1次側の乾燥空気に、油をことばどおり噴霧します。
下の図のようなイメージです。
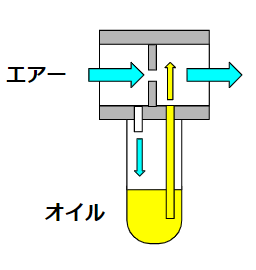
エアーの圧力で油を押し上げ、その油を自重落下させつつ、エアーの力で撹拌混合する。油とエアーの流れを形成するために、逆止弁を付けるケースも多いです。いずれにしろ、エアーの自力で噴霧する装置です。
油はタービン油でISO VG32くらいが一般的。油膜は数μmのオーダーです。
油の量の管理と逆止弁の管理がほぼすべてと言っていいでしょう。乾燥した空気にオイルを添付することで、空気圧シリンダーの作動を滑らかにする目的があります。オイルを散布するために、散布した全てが空気中に溶け込むわけではないので、オイルポットが必要です。
ところが、近年はこのオイルポットが不要となっているパターンが多いです。エアーシリンダー側が高性能になったからでしょうか?そのため、エアー3点セットはエアー2点セットと言われることもあるくらいです。
ノズルフラッパー(チャレンジ)
空気にまつわる知識としてノズルフラッパーを紹介します。
これは空気だけで制御をしていた昔の話で、電気制御が可能な今では知識として知らなくても良い話です。
古典的な知識なので、物理学の基本を知っていれば理解できる世界であり、
計装エンジニアよりも機械エンジニア向けの内容です。
昔の計装エンジニアが機械エンジニアから派生していっているため、同じ道を辿ると機械エンジニアが計装に興味を持ちやすいようにするために、記載しました。
完全に蛇足ですので読み飛ばしてもらっても構いません。
やや難しいので、チャレンジングな内容です。
原理
ノズルフラッパーとは以下のような装置です。
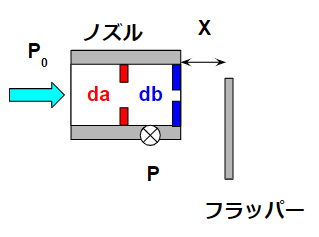
この原理を説明しましょう。
フラッパーとノズルの間隔Xを背圧Pに変換
これが最も大事な原理ですが、それを疎かにしている教科書。
フラッパーが検出器であり、例えば液面の情報そのものです。
フラッパーは左右に変形します。
左にフラッパーが動けば間隔Xが大きくなり、右に動けば小さくなります。
このXが変わると、Pが変わります。
Pの信号を、外部に伝搬すれば空気伝送器のでき上がり。
原理はシンプルです。
X=0ならP=P0
まずは、X=0、つまりフラッパーがノズルに接触している状態を考えましょう。
これはノズルが蓋をされている状態です。
P0として空気が供給されていますが、ノズルが蓋をされているので、背圧Pを検出する部分もP0の圧力になります。
これが第一。
X=∞なら絞りBの圧損分減圧
逆にX=∞、つまりフラッパーがない状態を考えましょう。
この場合、P0の圧力を持つ空気は、dbの径を持つ絞りBとdaの径を持つノズルから圧力損失分だけ減圧した状態で、外部に放出されます。
$$ P = P_0 – ΔP_b $$
背圧Pは絞りRでの減圧分だけ下がった圧力を検出します。
ここで db < daとして設計するので、ノズル部での圧損はゼロと考えます。
線形ではない
X=0とX=∞を考えれば、残りはそれをつなぐだけです。
シンプルに考えれば、直線関係になると思うかもしれません。
これが実際には線形ではなく、フラッパーが開けばすぐに圧力は下がります。
これはフラッパーとノズルの接触面積が小さいことが原因です。
接触面積が小さいため、フラッパーがノズルと近接しているX≒0の部分では、圧損が高く背圧Pは高いです。
ところが、接触面積が小さいためフラッパーが少し外れるだけで、圧損は極端に下がります。
解決策として、ノズルの形状を変えることは考えられるでしょう。
ノズル外径を変えると性能が変わることが期待できます。
力平衡式
力平衡式は下記の図で説明されます。
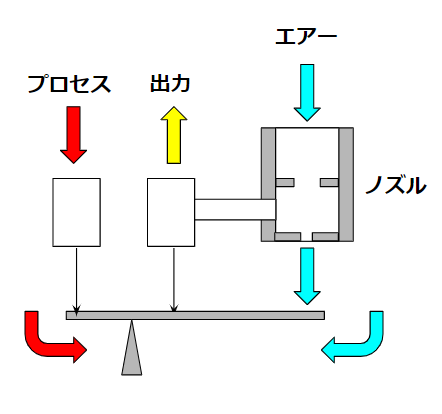
構成要素がいくつかありますが重要なのは、下記の二つです。
- フォースバーの固定点
- ノズルフラッパーの位置
力平衡式について作動原理を見ていきましょう。
- 入力として、プロセスの情報(液面・圧力・流量など)が加わる
- 入力部で圧力を受けるとバーの固定点から左側が下がる。
- バーの固定点から釣られて右側が上がる
- ノズルフラッパーの隙間が小さくなる
- ノズルフラッパーの背圧が高くなる
- 出力部に高い圧力の空気が生成され、外部に伝搬する。
フラッパー部でのフォースバーはスプリングによって常に平衡状態にあるため、力平衡式と私は解釈しています。
変位平衡式
変位平衡式は下の図のように説明できます。
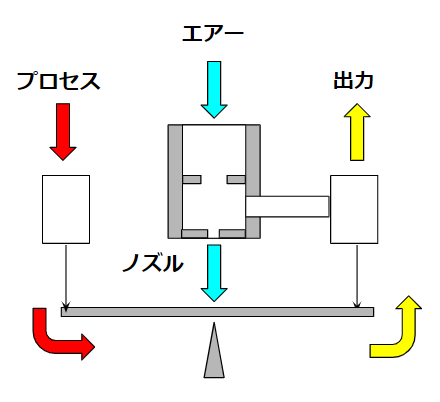
フラッパーの位置が固定されています。
フラッパーの背圧は固定されます。
入力部に圧力が加わるとバーが下がります。
釣られて出力側のバーが上がっていって、出力圧力タンク部を狭くします。
その結果、出力圧力が高くなります。
フラッパー部の変位が固定されているため、変位平衡式と私は解釈しています。
参考
空気圧に関する知識は、機械屋ではある程度知っていれば良いという程度で、計装屋に依頼することでしょう。
回路図からフローや制御方法がイメージできる程度で良いので、機械屋でも知っていると知識の幅が広がり応用ができるようになります。
最後に
化学プラントの計装用空気に関する情報をまとめました。
- 計装用空気は、圧縮空気とは別物で、より高い清浄度と乾燥度が求められます。
- 空気源の構成、機器ごとの必要流量、材質選定など、細かな設計配慮が必要です。
- 現場では、「共有しない」「定期点検する」「圧力監視する」の3つが重要です。
化学プラントの設計・保全・運転などの悩みや疑問・質問などご自由にコメント欄に投稿してください。(コメント欄はこの記事の最下部です。)
*いただいたコメント全て拝見し、真剣に回答させていただきます。
コメント